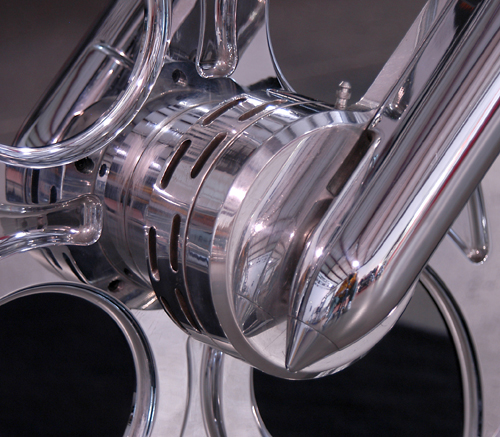
This could be the product of the year, a braking system within the wheel of a hub. At last we could see those bitchin’ wheels. But as our Bikernet investigation continued the benefits of this new system expanded.
“It’s called the “360 Brake” and it is revolutionizing the braking industry,” said Chet Burozski, of Baldwin Wilson Development Corporation out of Brownsburg, Indiana. “The design is actually quite simple. Take a clutch – make it work backwards – then stick it in the hub spacer between the wheel and the swing arm or lower fork leg.”
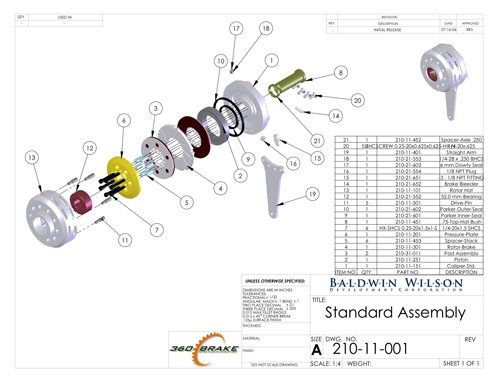
The “360 Brake” is a hydraulically activated brake that applies pressure to a piston that runs 360 degrees around the axle. The piston movement causes two brake pads, also 360 degrees around the axle to clamp on the rotor. The pads and rotor float across five drive pins that are attached to the rotor hat.
The “360 Brake” uses two square, O-ring type, hydraulic seals in grooves to seal the piston and pull it back (after pressure is applied) allowing the brake to release as quickly as it was applied, resulting in decreased drag, less wear and less noise from the pads. My first question revolved around the heat produced by constant 360 degree pad friction, without any cooling area from the rotor. I spoke to Tim Wilson the manufacturing arm of the team.
“We spent 1.5 million investigating and testing rotor and pad materials,” Tim said. “In the process we discovered that larger rotors spin the rotor metal twice as fast as our small rotor, generating more heat.” Under testing their current iron rotors and semi-metallic pads generate 260 degrees of heat and up to 500 degrees during repeated panic stops, which isn’t bad.

The basis for the design is not unique. It has a history of airplane use, except for one startling aspect, the 360-degree piston. Airplanes use a hub braking system with three pistons staged around the rotor area. Fred Baldwin came up with the initial design less than a year ago on a drink napkin and applied it to his design concepts for a twin-engine jet. He approached Tim to have some of his components manufactured, but Tim keyed on the braking system. “I knew it had considerable potential, so I pushed Fred to actively test, manufacture and market. We are quickly discovering additional applications outside the motorcycle or airplane markets.” First they covered their asses through the patent process and didn’t step into the market until they were secure.
Results from this design have been staggering. It looks like you have no brakes at all, when in actuality you have on average 60% more brake pad touching the rotor than conventional brakes. “The stopping is smoother because you don’t have the pull of a caliper 6 to 8 inches away from the axle,” said Chet. The brakes encompass the axle and keep the bike straight during hard stops. Think about what he said. Under load, common disc brakes pull front ends down and attempt to launch the motorcycle and rider over the front axle, like Stoppies. That virtually removes weight off the rear wheels in addition to removing stopping power. Standard disc brakes deliver 80 percent of stopping effectiveness to the front wheel and 20 percent to the rear. Under extreme conditions this level depreciates to 90/10 until rear brakes are nearly useless. There’s also a gyro-scopic effect of normal disc brakes pulling bikes out of alignment.
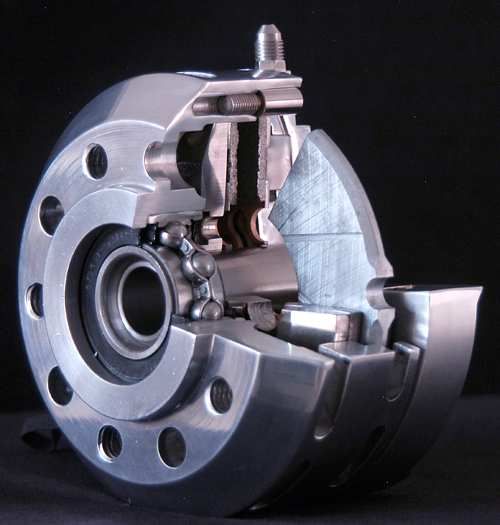
”The 360-brake causes a bike to squat,” Tim explained, “and the percentage of effectiveness runs from 60/40 to a consistent 50/50. Plus the bike won’t veer out of alignment, but stay true to the steering track.” They also noticed that wheels without heavy rotors track better in windy conditions. Motorcycle front ends can act and respond more effectively without the weight and mass.
The “360 Brake” also deadens the lever affect caused by a standard rotor and caliper. That’s to say when you stop the old way someone on the back would feel as if they were being launched over the handle bars. With the “360 Brake” the feeling is a gentle slide forward and down into the rider in front of you instead of being slammed into them. The “360 Brake” also applies downward pressure to the back tire increasing contact with the road and allowing harder braking without loosing traction.
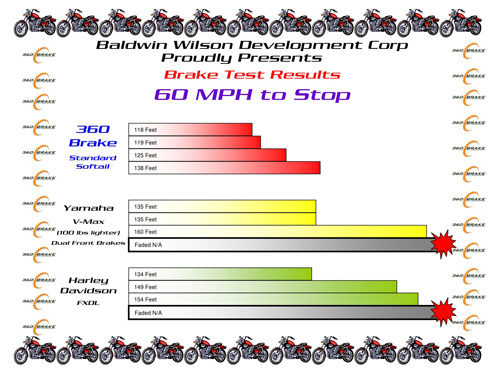
Testing showed that the 360-degree brake would stop similar motorcycles up to two car lengths faster than standard brakes in 0-60 mph tests. Under repeated testing the 360-brake showed substantially less heat deterioration than standard discs.

That’s not all. Initially Tim was convinced that larger mastercylinders were required. It’s not the case. Smaller, less-volume mastercylinders work the best.
Installing a 360-brake requires that as much as 2 5/8s of an inch of material be removed from the wheel hub to set the brake against the hub. It generally removes one wheel bearing which is replaced with the 360-degree brake hub. They are also being manufactured to fit ¾-inch, 1-inch, 20 mm and 18 mm axles. Currently Renegade, RC, Ego-Tripp and PM wheels are working with the 360-Brake for hub spacers. In most cases the hub spacer can be removed from any wheel, machined and replaced. Or the guys at Baldwin Wilson will supply you with the proper spacer and you're good to go.
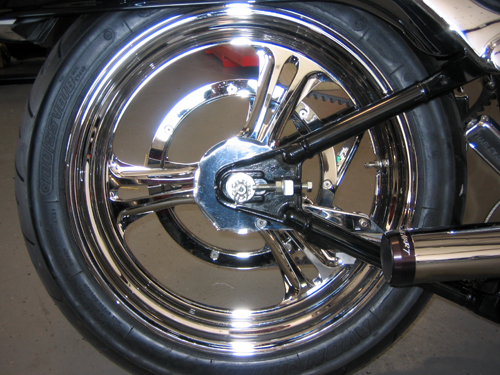
I was still curious about the donut piston. Would it cock under load? Would it hold the fluids under constant vibration? How difficult would it be to install or bleed? What about heat to the hub or wheel bearings? My concerns were unwarranted. It’s probably the easiest brake to mount and bleed today. You can unbolt the mounting arm and spin the brake if a bubble is stuck. Since the rotor floats, heat will not transfer to the hub or wheel bearings. Since the piston is one large unit, there’s reduced wear, with increase pad surface and efficiency.
Recently Chet, who in the marketing director and a lifelong rider worked with Kimmy Chapman from the Phoenix Biker Information Guide. She offered to introduce Chet to the custom motorcycle industry in Phoenix.
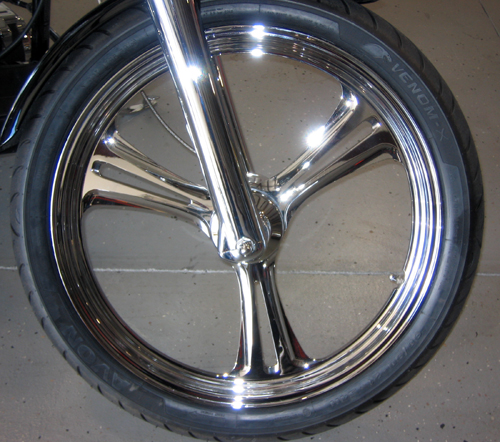
”The builders got a demonstration of how our brake works and then got to test ride the bikes we had fitted with the brakes,” Chet said. “I have to thank all of the guys who took time out of their busy days to see us. The guys at Highway Choppers, Care Free Customs, Street Walker Exhaust, Titan, AMP Customs, Ram Jet, Hacienda HD and Hacienda Customs, Larry with Jail Break, Boss Hoss, Rick with FLX, Bikers Bay, Fang with the Arizona Rattlers, Knockout Motorcycle Co., Chandler Customs, Iron Horse Corral, Evolution, AZ Thunder Cycle, Hot Rod City, Bourgets, Jim Nasi and our favorite watering hole The Hideaway Bar, thanks Mark. They were all blown away.”
Just in their first year of production Cycle Source Magazine awarded them the Product of the Year in the January ’07 Issue. It’s also been nominated for a similar award by Iron Works Magazine. This is an amazing product. Let’s see what ’07 brings for Baldwin Wilson and Chet. It’s obviously bringing the cleanest choppers to the market since spool wheels and no brakes.
–Wrench
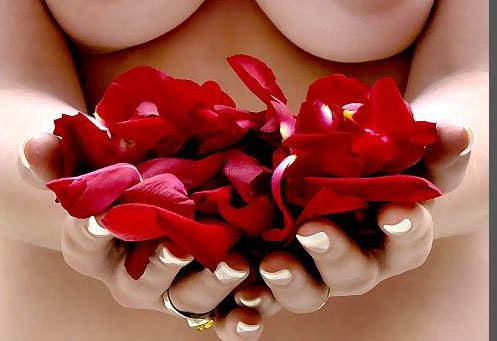
Check out The Baldwin Wilson website www.360brakecom.
Chet Burozski
Sales and Marketing Director
Baldwin Wilson Development Corp.
1531 E. Northfield Dr.
Brownsburg, IN 46112
W. (317)852-7867
C. (317)370-0920
F. (317)858-9287
www.360Brake.com
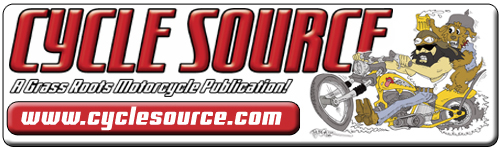