
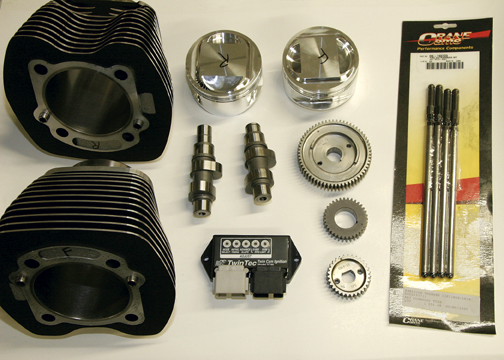
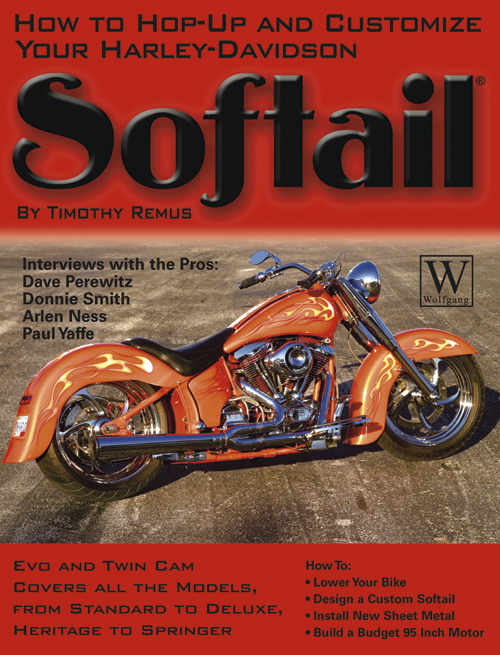
The title of the Wolfgang book is Hop Up & Customize, and the easiest way to get significantly more power from a Twin Cam engine is to install a 95 inch kit. In this case, the Wolfgang Softail book, we decided to try a relatively mild kit from Kuryakyn (click on any Wolfgang Banner in this article to order one of these books or more). The kit is based on the idea that by using carefully chosen parts a 95-inch Twin Cam with stock heads and mild cams can produce very nearly as much power and torque as the same engine with ported heads and much more radical camshafts. The difference between the two engines, besides some measure of power, is money. The Kuryakyn kit does not require ported heads. And because the cams are mild, and based on a stock baseline circle, the stock valve springs are more than adequate, even the stock pushrods can be reused (through an oversight, we did use adjustable pushrods).
Disassembly
Ken Misna, the bike builder on this project, starts by draining the tank and removing the cross-over tube. Two bolts hold the gas tank on, one at the back and one through-bolt at the front. Don’t forget the two-wire connector for the fuel gauge on the bottom of the tank.
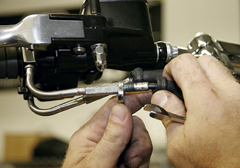
Ken removes the exhaust next, the flange nuts are first, then the nuts on the support bracket at the back of the frame on the right side. The air cleaner is removed next, then it’s time to move to the left side. First there’s the choke cable to take off the bracket, done by loosening the nut from behind, followed by the throttle cables. Before disconnecting the throttle cables, though, Ken puts slack in the cables with the adjusters near the throttle grip. Then he pulls the carburetor off the intake manifold, and while holding it, unhooks the two cables, explaining as he does, “having slack in the cables makes this job much easier.”
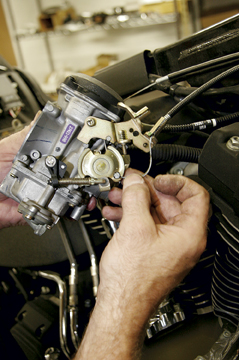
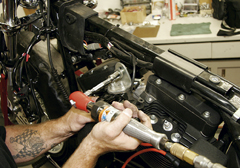
Now Ken removes the motor mount bracket and horn, then he takes out the spark plugs, because, “with the plugs out it’s easier to turn over the engine later in the process.” The intake manifold is next. The map sensor is disconnected, then a special ball-end Allen wrench makes it easier to loosen the four Allen bolts.
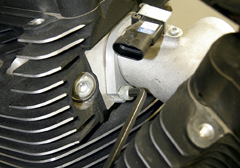
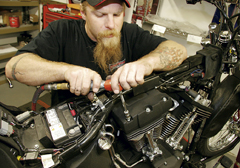
Rocker boxes
As shown, Ken removes the top of the front cylinder box first, being careful to keep all the parts organized: with the front cylinder parts in one group and rear in another so they all go back together in the same group. It’s time now to put a jack under the bike and turn the engine over until the intake closes. This leaves the front cylinder on the compression stroke and both lobes on the cam’s base circle, which minimizes tension on the valve train during disassembly. Ken likes to put the eraser end of a pencil in the plug hole and roll the engine back and forth so he knows it’s at TDC.
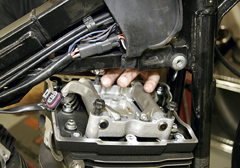
The breather covers come off now. Ken does the front cylinder first.The bolts for the lower rocker box are next. Ken rolls it over again so the rear cylinder has both cams on the base circle (compression or firing). The lower rocker box bolts for the rear cylinder come out now. Head bolts come out in a criss-cross sequence, as noted in the service manual, and then the heads are off. With the heads off the cylinders are next, followed by the lifter covers and the anti-rotation pins.
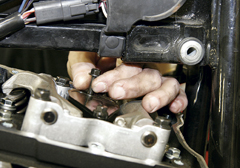
“I always put the lifters on the bench in such a way that I can reinstall them the way they came out, not turned 180 degrees,” explains Ken.
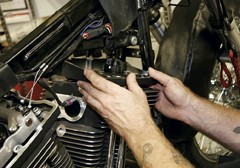
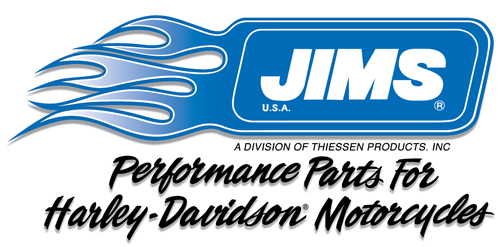
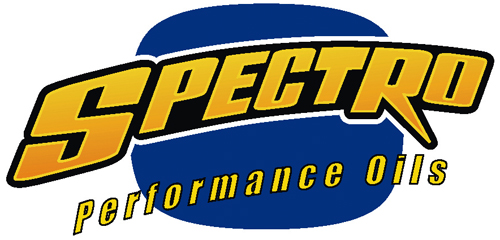
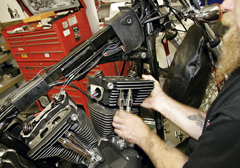
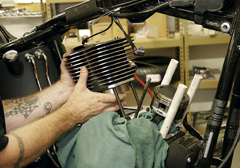
At this point Ken pulls the cam cover and then uses a JIMS tool to crank back the tensioner and put the pin in place to hold it off. (Tool #1283-1 with 2 pins, note the nearby photos.) “Because I did the front first then the rear cylinder, and left rear at TDC, the timing marks are lined up, which is nice if a chain drive cam set up is going back in.”
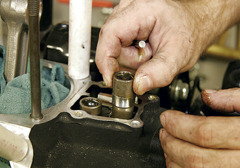
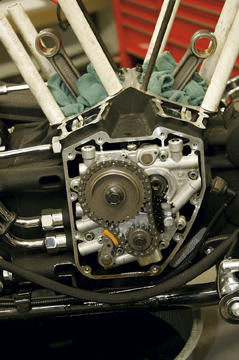
Once the retention pin is installed Ken can take off the primary drive chain and gears. Next he removes the six small machine screws positioned on the perimeter of the cam support plate. There are four more machines screws, the four that screw into the oil pump, that must be removed before the plate itself can be pulled out of the engine case.
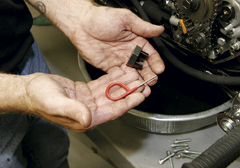
“Try not to let the oil pump come out with the cam plate,” warns Ken, “and try not to get oil on the clutch cable housing, it’s fiber and will soak up the oil and drip on the ground later making it look like you’ve got an oil leak.“
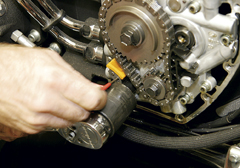
Before proceeding farther Ken installs the second retention pin, as shown on the facing page. Next he takes out the snap ring, then the retaining plate on the support plate’s back side.
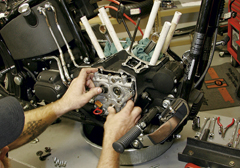
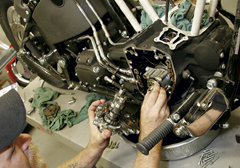
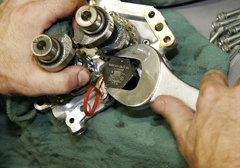

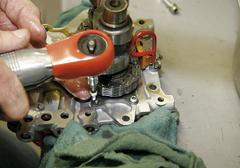
Press out Cams, Install New Bearings & Cams
Once the cams are pressed out(note the photos) it’s time to pull the inner cam bearings, with JIMS tool #1279, “if this were getting a high lift cam I would pull the oil pump and clearance the case,” adds Ken, “but these are just mild cams so we will just check the lobe-to-case clearance but shouldn’t have to do anything except clearance the outer cover (later). Now we drive in the new inner cam bearings with JIMS tool # 1278, as shown in the nearby photos.
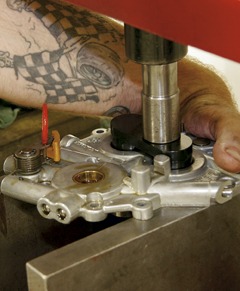
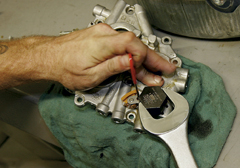

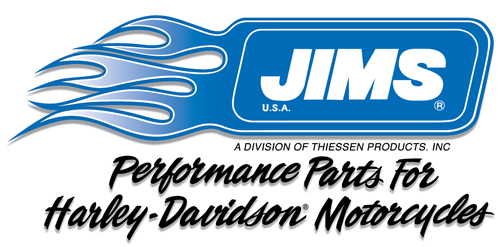
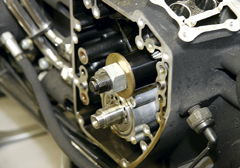
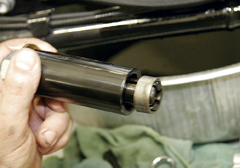
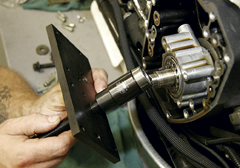
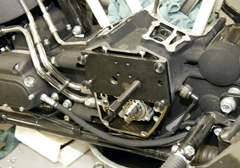
Next the new cam bearings are pressed into the support plate with the installer tool as shown. Even though these are mild cams, Ken checks the clearance between the lobes and the case, and in this case there is plenty of clearance. Ken installs the retaining plate, applying a little blue Loctite to the small machine screws, each of which is tightened to 20 to 30 in. lbs.
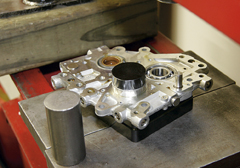
The gears need to be installed on the camshafts, but first the keys must be installed in the cams as shown. The cams are not the same, the rear cam has a longer shaft because it connects to the outer gear.
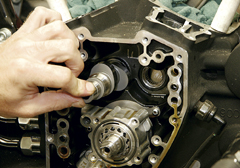
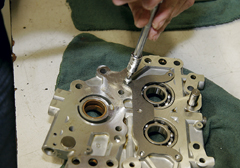
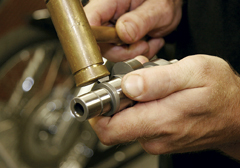
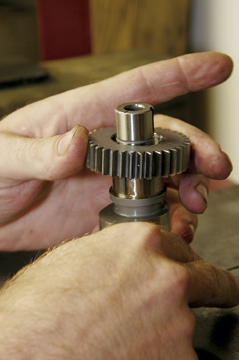
With the gears on the cams, the cams themselves are pressed into the plate. This can be done two at a time, but Ken presses them in one at a time. It’s important that they be timed correctly, as shown in the directions and the nearby photos. At this point we have a fully assembled cam support plate ready to be reinstalled into the engine case.
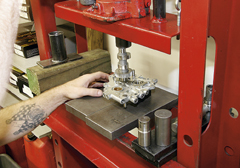
There are three O-rings used between the cam plate and engine case, one for the oil pump and two for transfer ports between the case and the cam support plate. It’s important to replace all the O-rings. Be sure to inspect the screen as shown on the facing page and clean as necessary. Only one camshaft, the front one, get’s a snap ring to hold it in place.
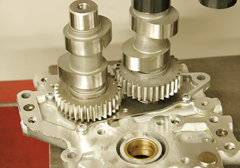
Ken recommends cleaning the cam support plate bolts, and installing them with a little blue Loctite on the threads. He also puts prelube on cam lobes and some on the gears as well.There are six outer screws that hold the cam support plate to the case, and four more that screw into the oil pump. Ken installs the outer fasteners first.
“There’s a tightening sequence for these bolts,” explains Ken. “The factory lists the torque range as 90 to 120 in. lbs., but S&S recommends 95 in. lbs. because some of the holes, those with dowels, can be stripped at 120 in. lbs.
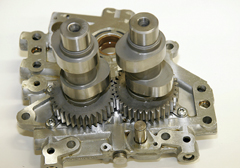
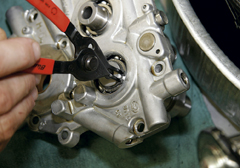
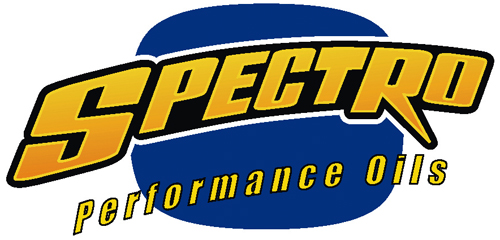
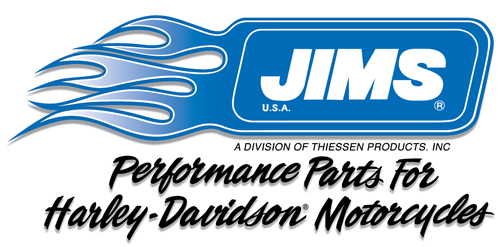
Oil Pump Alignment
There is a specific alignment procedure for the four bolts in the center of the plate, the ones that screw into the oil pump. Though there’s more than one way to do this, Ken uses a tapered tappet tool (used to align lifter blocks on Evos) in # 1 and #2 holes as shown, snugs them down, then snugs down the other two, then installs the other two machine screws, where the tapered pins were installed, and torques all four in the sequence shown in the service manual to 95 in. lbs.
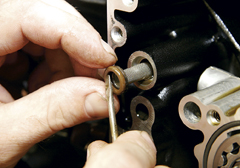
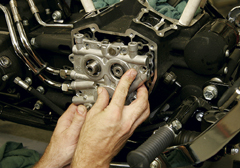
Primary Cam Gears
To pull the lower gear onto the crankshaft, Ken uses a bolt and washer. Once the gear is in place, red Loctite is used on the correct bolt, which is tightened to 25 ft. lbs. By putting the bike in gear, and holding the rear brake, Ken is able to prevent the shaft from turning. What’s left is to line up the timing marks and install the upper gear. Once again the gear is pulled onto the shaft. The bolt is the one supplied with the kit. When the real upper bolt is installed, it is first treated to red Loctite then tightened to 34 ft lbs.
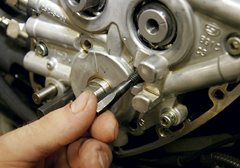

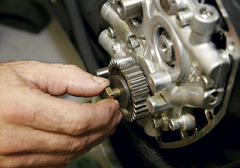
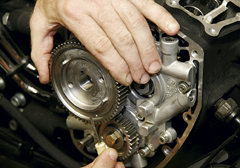
The one place where there’s nearly always a clearance problem when converting to gear-drive cams is the outer cover. As shown, the one rib needs to be ground away. The clearance can be double checked with a little clay and adjusted as necessary.The cover itself is installed with more of the small machine screws, tightened to 90 to 120 in. lbs.
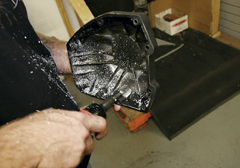
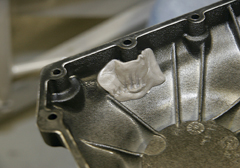
Install Lifters, Pistons and Cylinders
The lower case is fully assembled, it’s time now to start on the cylinders and top end. Ken starts by installing the lifters and the anti-rotation pins, everything in exactly the same position as before.
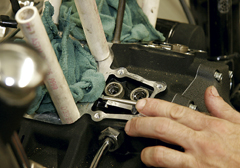
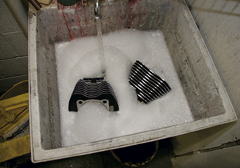
Before installing any of the top-end parts, Ken washes the cylinders thoroughly with soapy water, then takes clean engine oil and a clean paper towel (no lint), and wipes and wipes them out until the towels come away clean.This leaves a light film of oil at the same time which is good because it will prevent flash rust if the cylinders are going to sit on the shelf for a little while before assembly.

Before installing the rings on the pistons we have to check ring end gap. The instructions that come with the kit list the minimum clearance as .003 inch per inch of cylinder diameter, or just under .012 inches for a 3.75 inch cylinder.

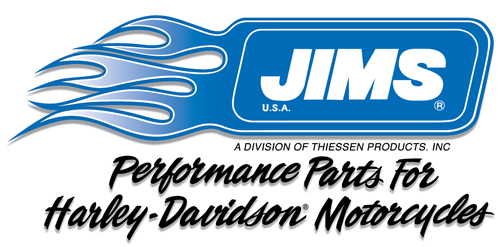
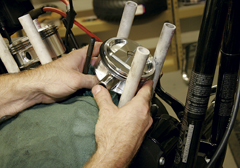
Ken warms that, “you have to be sure to follow the directions on installation of the rings as there is a top and bottom to the first and second ring. And the cutout on the top of the piston is bigger for the intake valve, so the pistons have to be oriented correctly. I always put assembly lube on the piston pins before I install them.”
Now the cylinders are installed down over the pistons and rings.
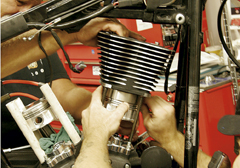
Cylinders
The front cylinder is set down first, then the rear, as shown nearby. Cylinder heads are next, followed by the pushrods tubes. Torque the head bolts, first to 120 – 144 in. lbs., then to 15 to 17 ft. lbs., following the sequence in the service manual. The final step is to turn each bolt an additional quarter turn. The lower rocker boxes are installed next, note the caption regarding the gasket position. The fasteners are tightened to 156 inch pounds. Be careful to put the longer bolts on the left side, and tighten per the sequence in the manual.
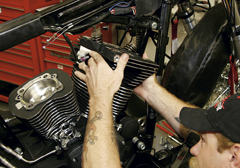
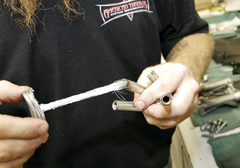
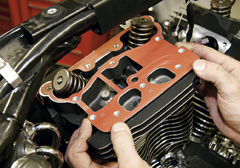
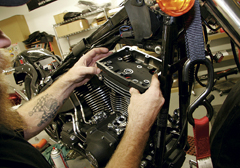
The pushrods are installed now, the longer ones are for the exhaust, (there are only 2 lengths), be sure to put pre-lube on the ends. There are three O-rings on the pushrod tubes, be sure to replace them. In the HD kits, the top is yellow, the middle is black, bottom is black too but “they are different enough that they’re easily identifiable.”
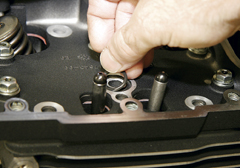
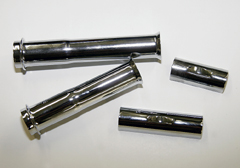
The H-D tubes for adjustable push rods come with a shorter lower tube, which allows you to slide the tube up farther which provides more room to get at the adjusters. (H-D part #s: Lower Tube 17938-83. Upper chrome cover, 17634-9. Upper tube and the rest of the hardware stays the same. The complete kit is part # 17997-99A.)
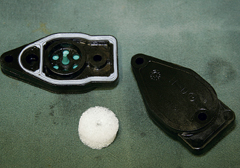
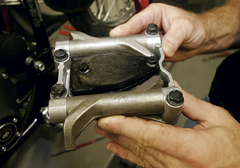
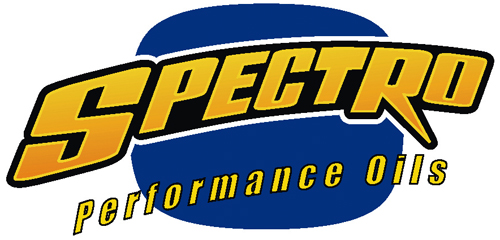

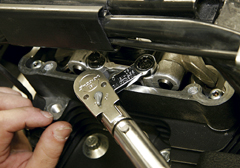
Breather assemblies come in two styles, this is the one-piece design, which means the sponges (called a filter element) can be replaced, but not the rubber umbrella valves. With the new filter element in place the breathers can be dropped down onto rocker shaft assembly.
Ken adds that “because these are adjustable pushrods, and they’re collapsed all the way we aren’t going to run the pistons up to TDC and get the cams on the base circle before tightening the bolts for the rocker shaft assemblies.” The four bolts are tightened to 18 to 22 ft. lbs. in sequence and the breather bolts to 90 to 120 in. lbs.
Rear cylinder
Now it is necessary to run the first cylinder to be adjusted up onto the top of compression stroke (so the cams are on the base circle). The basic procedure is to adjust the pushrod to zero lash, then a certain number of turns after that. How many turns depends on the pitch of the threads, so each brand of pushrod is different. With the Crane adjustable push rods it’s 2-1/2 turns after zero lash, which happens to be the same as H-D pushrods.
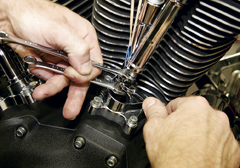
Once Ken has one cylinder adjusted he lets those lifters bleed down (evidenced by the fact that you can rotate the pushrod with your fingers) before turning the engine over and going through the same procedure for the other cylinder.
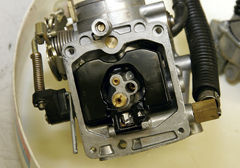
Carburetor set-up
To help the carburetor better meet the needs of the new hopped up engine, Ken gives it a quick tune up as follows:Take off float bowl. Take out the slow-speed jet, Stock is 45 for all T-Cs. Start by going to a new slow jet, a number 48. Remove the cap for the idle mixture screw (ours was already removed). Ken starts with the screw 2-1/4 turns out from seated (stock is usually 1-1/2). The main jet is a 190, which Ken thinks is bigger than stock so he decides to leave it alone for now. Take off top cover and install a new needle.
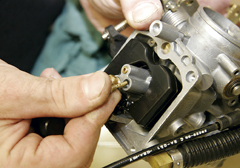
Be very careful that the diaphragm stays seated on the carb body, along the edge. The new needle is #27094 88, a 1200 Sporty needle.

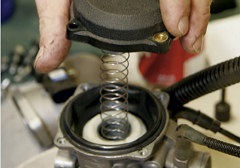
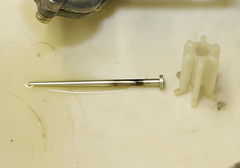
Ken installs the intake manifold next, with the help of a fixture that will ensure the carburetor is sitting at the right angle before he does the final tightening of the intake manifold bolts. With the fixture in place the bolts are tightened almost all the way (they’re still a little hard to get at). Then after the fixture is removed and the carburetor is popped out of the way, the bolts are double-checked to be sure they are tight.
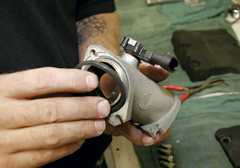
The throttle cables are installed now, with the cable adjusters still in the slack position (they are adjusted later). And then Ken can install the air cleaner, with some thread sealer on the breather bolts. The top motor-mount is next, then the plug wires are connected to the new plugs.
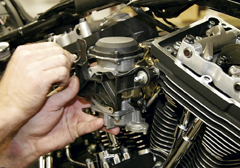
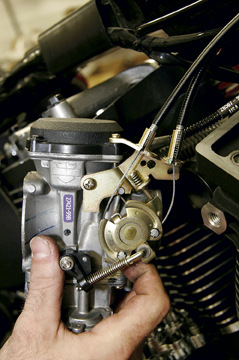
To hang the exhaust, Ken gets the bracket on the studs first, then attaches the header flanges and tightens those, then tightens the nuts on the frame studs. Installing the exhaust is one of those things that needs to be done with a little finesse to make sure the parts are seated and positioned correctly. Our budget exhaust option is shown on the right, what might be called the high-tech hole-saw option.
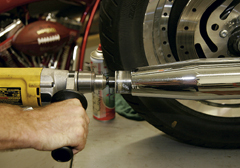
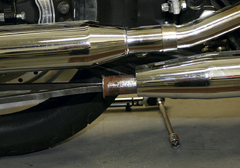
What’s left is to adjust the throttle cables, reinstall the tank, put in gas and oil and crank ‘er up. To see just how much power our combination of parts actually makes, and ensure the carb is jetted correctly, we took the bike to the local dyno facility and that reports follows on the next page.
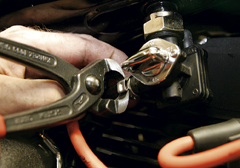
SPECTRO OIL BREAK-IN RECOMMENDATIONS–For break in on a Twin Cam I would recommend a straight petroleum like SpectroHD20/50 for the first 500 to 750 miles, then switch to Spectro platinum20/50 full synthetic. The straight petroleum will help the rings seatfaster, and our high zinc formula will reduce piston scuffing during thecritical break in period.
–Rollin Karoll
Vice President of Sales
Spectro Oils
993 Federal Rd
Brookfield, CT 06804
800-243-8645
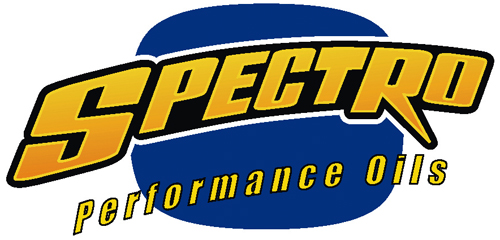
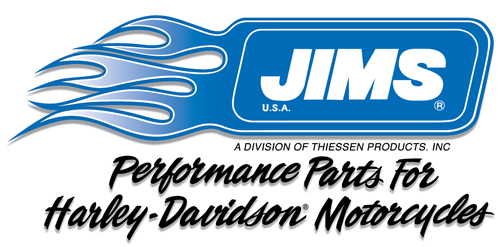

DYNO SIDE BARS:
To determine just how much horsepower and torque we obtained by installing the Kuryakyn 95 inch kit with their cams, and to ensure the air-fuel ratio and the timing are set at their optimum value, we took the Night Train to Doug Lofgren at World Class Tuning, in Watertown, Minnesota.
Doug starts out by positioning the bike on the dyno, attaching the dyno’s computer to the bike’s CPU with the data link, and attaching an inductive pickup on one plug wire. Next, it’s a matter of running the bike through the gears repeatedly to get it thoroughly warmed up.
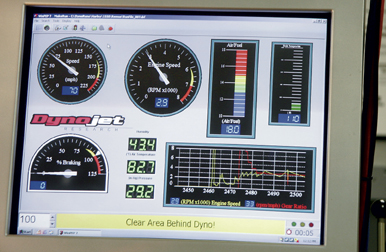
As Doug explains, “what’s really important are the numbers. People get intimidated by the machinery and the computer, but it’s the numbers that matter. What you need for good dyno work is consistency, repeatability. Once you get good consistent results then you can make changes based on small increments in power.”Dyno runs are done in 4th gear. Doug starts below 2000 rpm and rolls it open very quickly. The revs build fast and smooth all the way to 5500, when the engine starts to break up. The numbers we get from the first few runs are 94 ft. lbs. of torque and nearly 86 horsepower. So even without any further tuning we’re well up on a stock Twin Cam with about 65 horsepower.
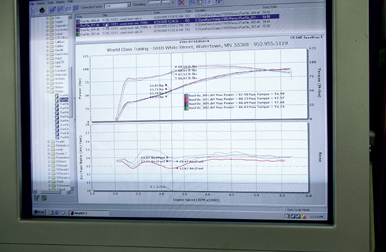
At the bottom of the typical dyno chart is another graph, the air-fuel graph. An ideal air fuel ratio under full power is 13.1 to 1. In our case the numbers are more like 14.5 to 1, or way too lean. Doug decides to add a bigger main jet, “to richen the mixture all the way through the rpm range.” To make a long story short, we go from a 190 to a 200, then start drilling the 200 until we’re at a number 230 jet and have achieved a fairly flat, 13.1 to 1, fuel curve all the way to redline.
Speaking of redline, the reason the bike wouldn’t run past 5500 is because the Twin Tech ignition module came with the rev limiter (and the ignition timing) set at a very conservative level. Near the end of the jetting sequence Doug begins to add timing as well.
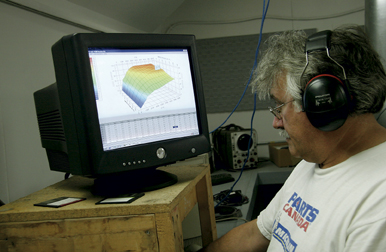
The first thing he did is set the rear cylinder to fire three degrees later than the front. The Twin Tech can be adjusted either by turning the small radial switches built into the unit, or by making much more sophisticated choices with the computer. Doug opts for option number two, which allows him to add or subtract timing, in very small increments, at any point in the rpm/speed/load map.If you add too much timing the bike will ping or detonate, which can be heard even over the horrendous noise levels in the dyno room. But before reaching that level the additional timing will cause the power to drop off.
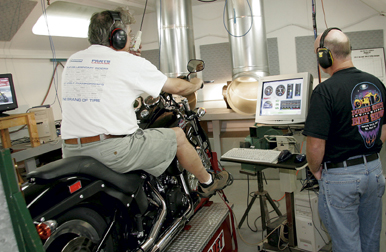
As Doug explained near the end of our dyno run, “I gave it more timing throughout the rpm range and it didn’t increase the max torque but the power came up a little. So I backed everything off two degrees and then added timing at the upper RPM range. The particular map we’ve loaded into this bike has the timing backed off at low rpm/low vacuum (high load) conditions so it won’t ping when you roll it open on the street without downshifting.”
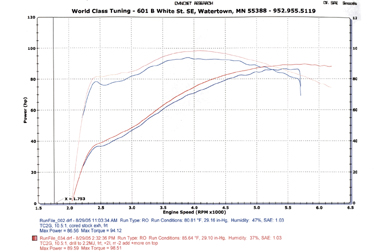
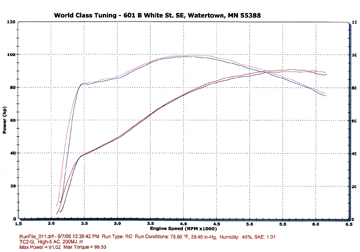
All Doug’s patient massaging of this particular V-twin nets us 98 ft. lbs. of torque and 89 horsepower. Again, not bad for what is essentially a budget hop up. As an aside, we came back another day and tried one of the new Kuryakyn Hi-Five air cleaners which gave us an additional two horsepower for a total of 91. We should note that even the simple change from one high-flow air filter to another required re-jetting because, as Doug explained, “the air filter design affects how the airflow travels over the vent for the float bowl, which in turn affects the float level.” So, as always, nothing is simple and the best results go to those who pay attention along the way.
