
Click here for ad info.

Five days ago I was looking at a frame, two tires, and what seemed like a million different parts sitting around my bike project. I stood there in Lucky Devil’s shop, mouth agape, hopelessly wondering if there was any way we would finish in time. Kent Weeks, head wrench and mastermind at Lucky Devil Metalworks, just smiled and gathered parts while humming a tune from one of the seasonal Christmas programs.

We had less than a week before Sucker Punch Sally’s crew was supposed to drive through town and pick up the bike. Thankfully, between Sucker Punch Sally’s, Bikernet.com, Custom Chrome, Hot Bike Magazine, Westbury Hot Rods, Fabricator Kevin, the Lucky Devil, Kent Weeks, Glenn Priddle, BDL, and J&P Cycles, we were able to obtain everything we needed to complete the build and deliver a bad-assed ride to my brother. Watch for features in Hot Bike after Biketoberfest.
Kent, knowing we were in a time crunch, switched gears and stepped up like no other.
He single-handedly assembled the ride from the ground up in 4 days. I stood by his side much of the time snapping pics and asking questions, all the while he quietly kept at the task at hand. I think the more time I spent with him, the more certain he grew with the conviction my brother might have been hurt if I’d have built the entire bike on my own. While I am not a complete idiot, when it comes to mechanical knowledge, I would definitely be riding the short bus.
We started by buffing the frame after Kent laid down a beautiful coat of silver paint accented by black airbrush shading.
The look was almost like raw steel which went along with the build perfectly.


We decided to spin balance the tires before starting final assembly. Kent used on of the machines he has at the shop. I was surprised to find out how self sufficient his shop is, containing everything one would need to build a motorcycle from start to finish.

Next, we went in and started to assemble the front-end we received from Bikernet.com. We had stripped down the chrome and decided to paint the legs the same color as the frame. We slipped the triple trees into the freshly cupped neck and carefully placed the legs into the cradle. It became immediately apparent the legs were a little too long. SHIT! Being as it was already 10 pm on Wednesday night, I shot back to my house and stole a BURLY lowering kit my buddy was planning on putting on his Fatboy. (Thanks Ronnie, I owe you one!)

By the time I returned to the shop, it was after 11 pm. After watching Kent disassemble the forks and install the lowering kit, I was once again visually reminded how much skill it takes to work on these things. Building bikes is definitely harder in real life than it looks on T.V.




Once we lined the front end back up, we installed the engine, followed by the transmission, and finally the primary plate.






We started installing the coil and top motor mount, but was surprised we had a space between the bracket and the frame. Kent made a spacer on the mill. Once again proving this stuff was better handled by a professional.



We put in the oil bag, but had to remove it to install the starter. Once the starter was in place, we could install the bag again, but the lead off the starter was dangerously close to the oilbag. Kent patiently kept arranging it, but eventually modified the lead off the starter and mounted a piece of rubber on the oil bag to prevent the occasional rubbing that could occur.



The main thing I learned the first night was the skill and patience required to build a bike is built upon over years of trial and error. I was privileged to watch a master at work who moved effortlessly through each task with the magnificence of a maestro directing his orchestra. Every movement, every selection of tool or task, was the result of a master plan in which there would be no wasted time on the build. He was awesome!

At 4:30 am, I headed out to my day job. Kent worked until a little past 7 before crashing until noon. He never even told me it was his birthday, so Happy Birthday my friend! I went to work and seemed to blaze through my daily routine. Although I was sleepy, I was still too excited to stop. After work I was able to sleep for two hours before heading back to the shop. Kent had already been back at it for several hours.

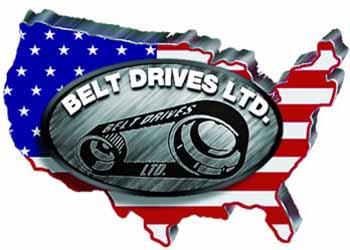
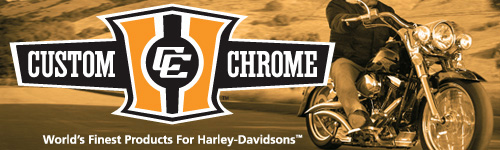

He had installed the coil, intake, spark plug wires, and belt drive. Holy Shit!! This bike would be running in no time…or so I thought. It seems wiring a motorcycle, no matter how simple you make it, takes a lot longer than I had anticipated. While Kent worked out the bugs with the wiring, I installed the handlebar grommets and handlebars. Now at least it was starting to resemble a motorcycle. I left early that night because my body seemed to be shutting down. I had to get some much needed rest, and besides, it was still his birthday, right?





Friday afternoon, day 3, and I can not believe what I see when I walk into the shop. There sitting on the lift, is a beautiful bike, almost complete. The tank is perched atop the frame like a king on the throne. The crown gas cap may have articulated that simile. The rear fender was affixed to it’s proper place, covering just enough tire too block the rooster tail of mud and rain the would follow a fender-less tire. The bike looked great!

Kent still needed to assemble the headlight assembly and taillight assembly, but it was coming together. He ended up kicking me out of the shop so he could finish with the final wiring schematics. The attention to detail he thrives upon is next to remarkable. I once again was thankful to have him in my corner.


