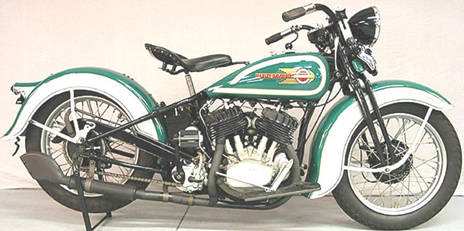
Stuffing a big twin into a VL frame dates back to the days when the Knucklehead was a brand new, modern OHV engine, 1936.
There were a lot of advantages to a conversion like this. VL frames were good for a 25 pound frame-weight reduction, versus its Knuck counterpart. The shallower VL rake made for a quicker handling bike. In addition, the physical look of a big twin in that compact, single downtube frame layout, was not to be denied. It's still the stylish case today.
While not extremely difficult to accomplish, installing any of the pre-EVO big twins into VL frames is definitely not a drop-in affair. How much frame surgery required depends on which version of the Harley V-twin you're considering.
A few notes before we begin. First, the newest VL frame you're likely to come across is now approaching 68 years old. These frames were manufactured by combining forged frame junctions, virgin steel rails, and furnace brazing. Herein lies two important things to watch for.
A lot of VL frames around today have rotted from the inside out. What looks like pristine frame rails, may look like Swiss cheese after sand blasting. Look for these symptoms where the frame tubes enter, or run through the forgings.
Next, VL frames were assembled using the furnace braze method. This entailed heating the assembled forgings/rails until brass rod would melt, and flow into the unions, similar to “sweating” copper plumbing tubing together. When modifying a VL frame, EXTREME CARE must be exercised in making sure that ALL TRACES OF BRASS are removed from modified areas. Electric welding over brass will result in, DANGEROUS CRACKS FORMING in both your frame, and your weld beads. No good for you at 80MPH!
Additionally, over its production run, the VL forgings changed from year to year. While, at first glance, they will all look the same, you may experience varied forgings. You may need to adjust your mods to suit the shape and size of your particular frame forgings.

Also you are liable to run across already modified VL frames. Some are well done, others (more likely) are out and out butcher jobs (pictures #1&2, This one was butchered so poorly, that the engine snapped the seatpost tube.) While this is not an all encompassing frame repair article, a lot of what you'll see here, can be used as a guideline to double check, or correct frame mods.
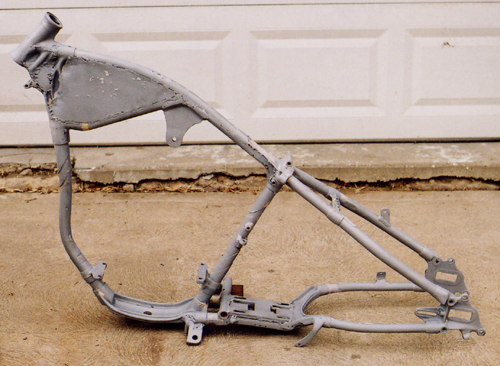
One last comment. The rake on these VL frames is right in the area of 25 to 26 degrees, in stock form. Consider this, the rake on a FXR frame is 28 degrees, and the rake of a VL frame is approximately 4-5 degrees LESS than a later big twin rigid frame. Raking is definitely in your future if you plan on running at high speeds with your finished cycle.
Don't say I didn't warn you!
With these warnings out of the way, let's get to it. We're going to modify four areas of the frame:
1. The lower tank frame rail (picture #3)
2. The upper seatpost/backbone forging (picture #4)
3. The front , and rear lower engine mount pads (picture #5, and #6 respectively)
4. The brake mounting area of the left rear frame rails (picture #7)
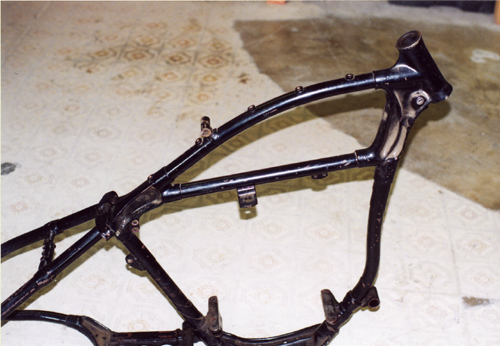
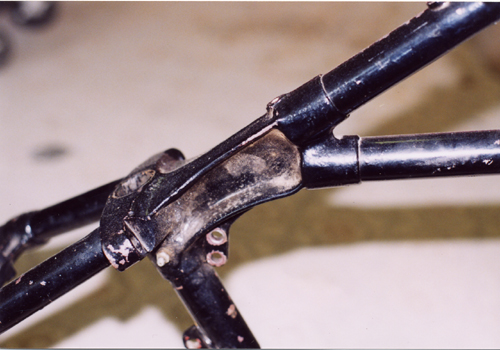
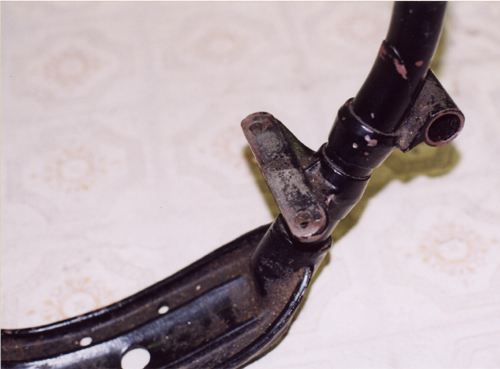
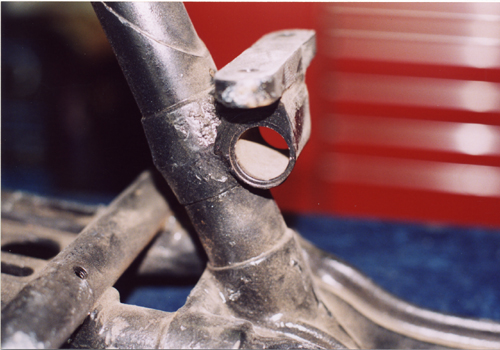
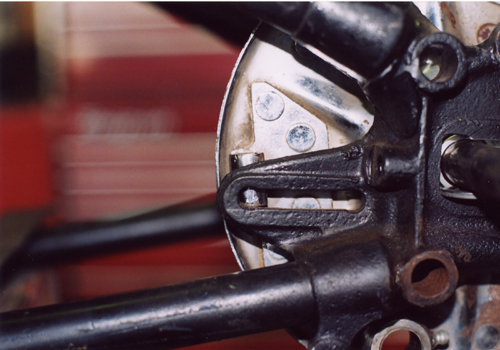
Let's start our modifications at the rear seatpost/backbone area (picture #3 again), to fit a Panhead, or early/late Shovelhead. You are going to make a cut that starts between the upper and lower tank tube lugs, through the forging web, just short of the upper lug for the seatpost.
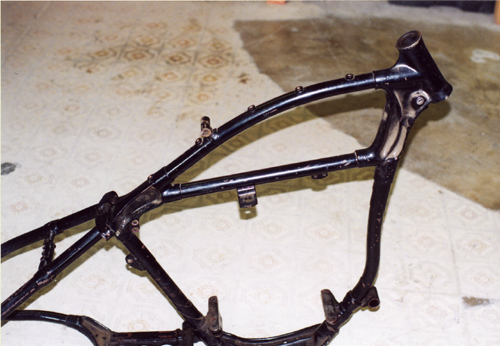
Next, make a cut along the upper seatpost lug, intersecting your previous cut*. (picture #8)
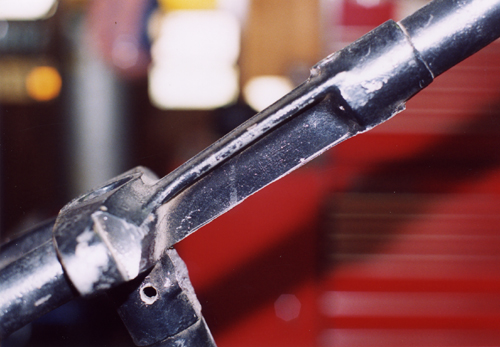
*NOTE: If your intended engine is a Knuckle, or a UL-series Flattie, your surgery here is not as extensive. Both engines will fit (if they aren't strokers), by cutting just between the tank tube lugs and stopping. Mark a cut line approximately from the seatpost tube gusset (with the two holes) on the lower I-beam section, to the upper tank tube lug. A simple 1/8-inch thick gusset is cut and shaped from cold rolled plate, to restore the I-beam structure. The lower I beam webbing with the two holes is removed, and the forging is slightly shaped to flow nicely. This is all the clearancing you need for these two engines. If you own a stroker, you need to make the full relief cut, as done for the Pan/Shovel.(see drawing)
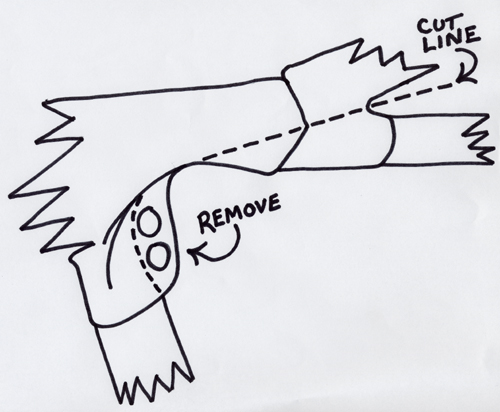
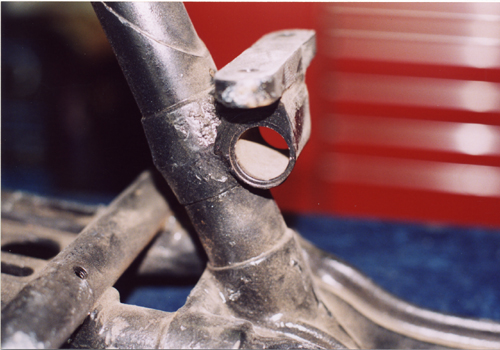
Before mounting your engine, to check your rear rockerbox clearance, remove the lug under the rear lower engine mount, that held the rear footboard crossbrace. The engine will not slide into place with this intact. It'll hit the back engine casebolt tunnel. (picture #6)
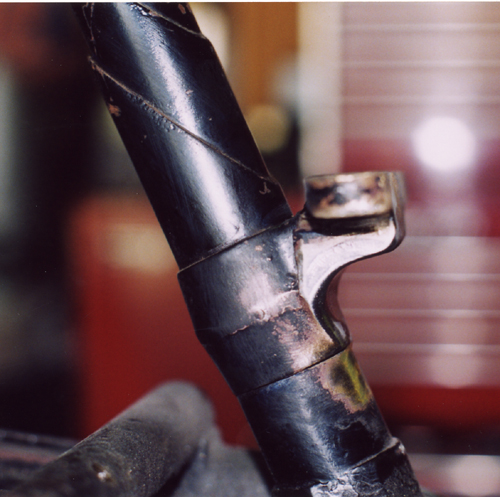
Cut the loop right at it's upper arc, and right in front of the lower seatpost casting. Remove no more of the loop than is absolutely necessary, to preserve the integrity of the mount. (picture # 9)
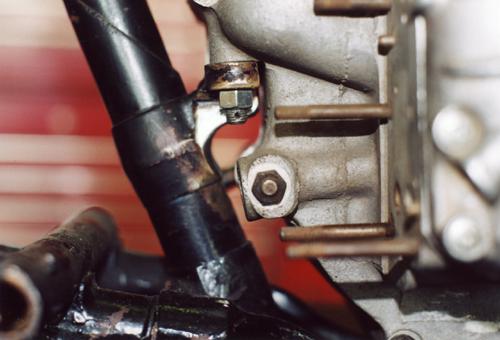

Install your engine of choice (in this case, a Panhead), using just the rear mounting bolts (torqued to 35 lbs./ft.), and check your clearances. (pictures #10 and #11)

As you can see, even with the forging reduced to half it's original thickness, is still a tight fit! Your gap here, over the rear rockerbox, will be approximately 3/16-1/4-inch, if you made a nice straight cut. Remove no more material than absolutely needed to adjust the gap! (picture #12)
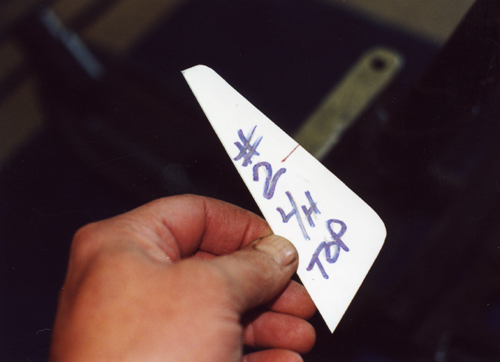
We need to restore the structural integrity of the forging next. A posterboard template is made to fit the contours. (picture #13)
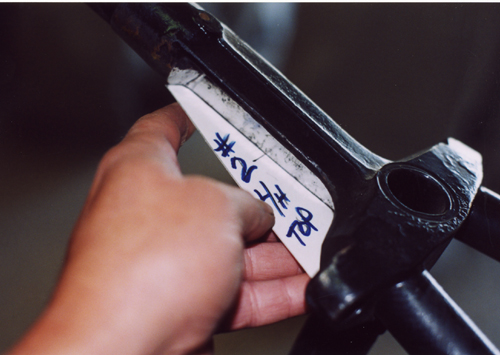
Most times, it is necessary to make a different pattern for each side. (picture #14)
The patterns are transferred to cold rolled plate, cut to shape, and a slight bevel is ground on the edge of the plates, to improve weld penetration. Then the plates are tacked in place.(picture #15 and #16)
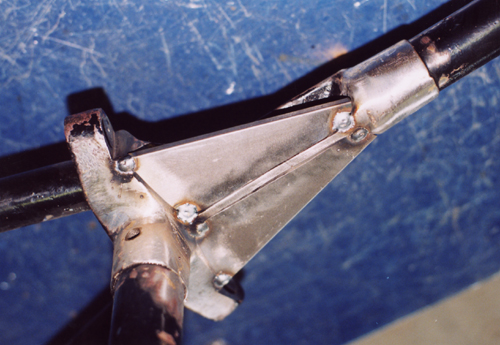
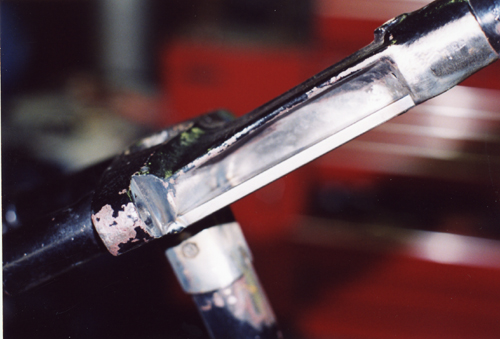
The engine is mounted once more as a final check, removed, and the plates are final-welded in place. Here's a tip: When welding on any forgings, take an oxy/acetylene torch with a “rosebud” tip and preheat the forging before welding. This will improve weld penetration immensely. After you finish your welding passes, cover the welded area with a fireproof covering (such as a welding blanket – shown here), and allow the forging to cool at a slower rate. Harley forgings have a tendency to crack, if they are exposed to cold air during cooling. NEVER accelerate the cooling-off process. It will surely crack as a result. Let welded forgings take up to an hour to cool to the touch. Take your time! (picture #17)
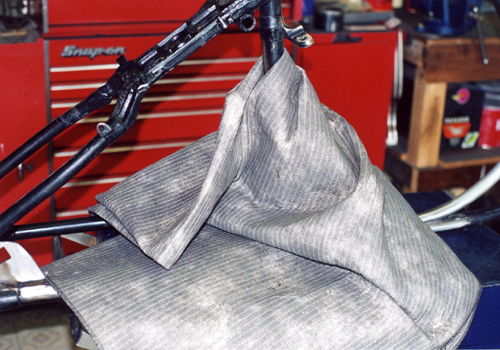
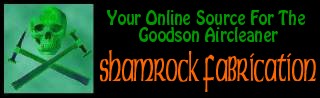
Your modified seat post forging, fully gusseted, should look something like this when you're finished. (picture #18, and #19 respectively)

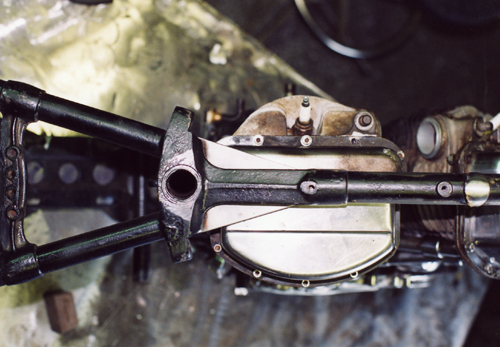
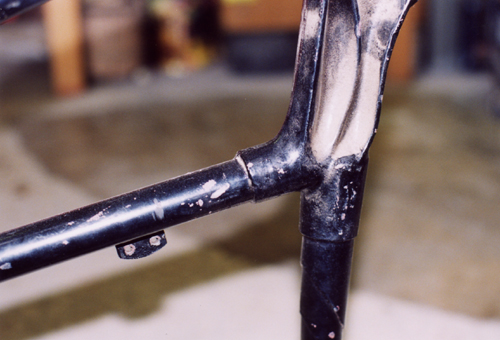
Before we can continue on with the full engine mounting, the lower tank bar needs to be fabricated, and welded into place. In the old days, most guys cut the original lower tank bar, shortened it , heated it at the front forging, and bent it straight up till it hit the upper tank tube, and called it good. It worked, but it looked like hell! Watch how we handle it.(picture #20)
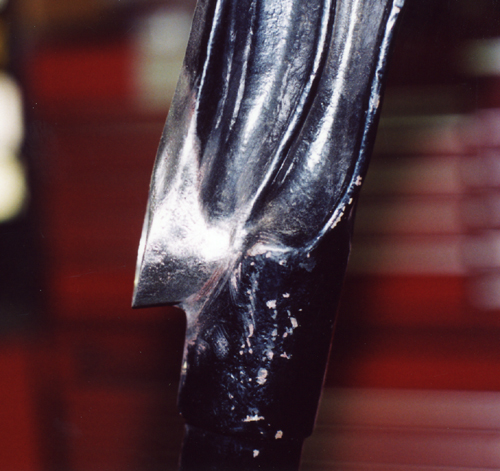
The lug for the lower tank tube is cut off flush, along the back angle of the neck forging. (picture #21)
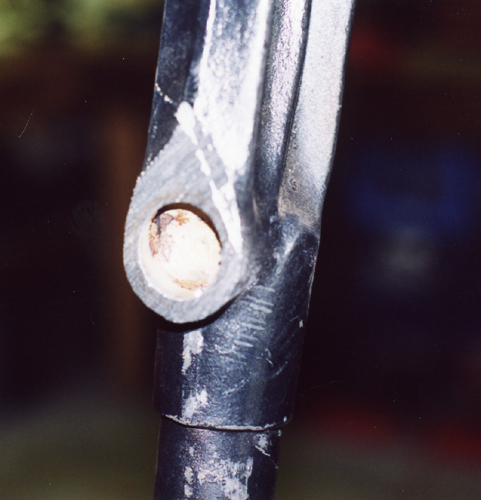
With the lower tube cut off, you will see what remains of the tubing, and you will also see the line of brass that held the tubing in the lug. (picture #22)
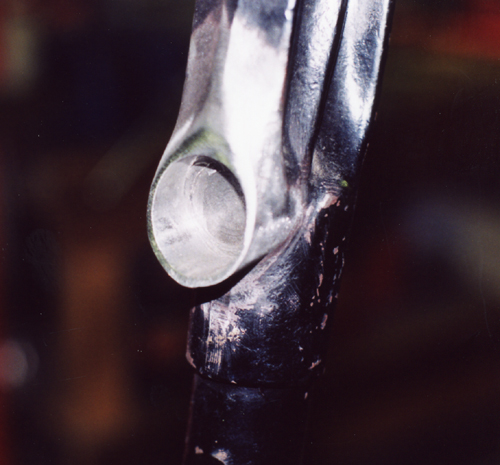
The remaining tubing, along with all the brass, in this area, needs to be completely removed and the area contoured to blend with the lines of the casting. (picture #23)
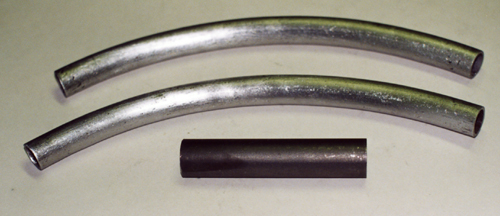
A piece of 1-inch diameter, 1/8-inch wall, DOM tubing needs to be bent in an arch that will allow it to meet the upper tank tube approximately in the area that is directly over the front of the rear rockerbox. In addition, a section of 1 1/8-inch wall tubing is needed to form a lug for the front of the lower tank tube in the forging. (picture # 24)
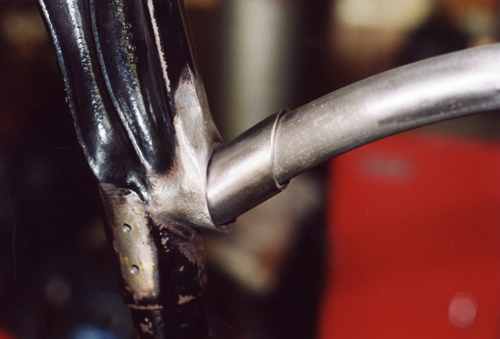
The socket is cut approximately 3-inches long, and a 30-degree cut is made on one end. The angle cut is purely for esthetic reasons. The lug is seam welded to the end of the tubing, and a plug weld is used on each side of the lug to secure it in place. (picture #25)
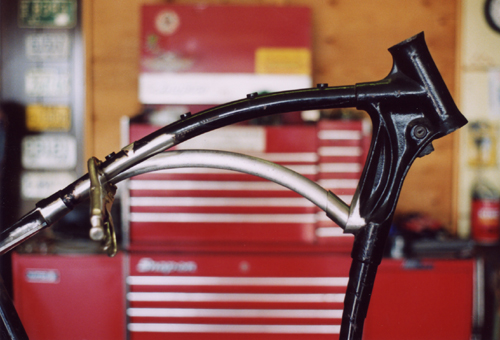
Then, the assembly is placed in the neck forging, and the curve of the upper tank tube is marked and cupped in the tube. The lower tank tube is ready to weld in place. (picture #26)
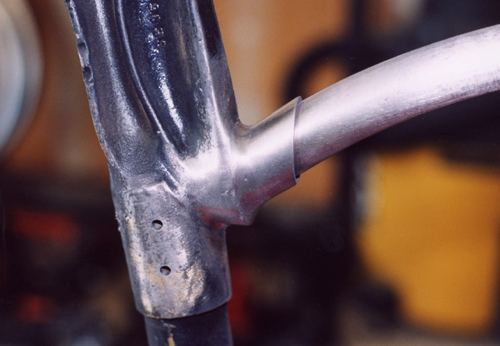
After welding, the beads are blended into the surrounding areas. (picture #27 and #28 respectively)
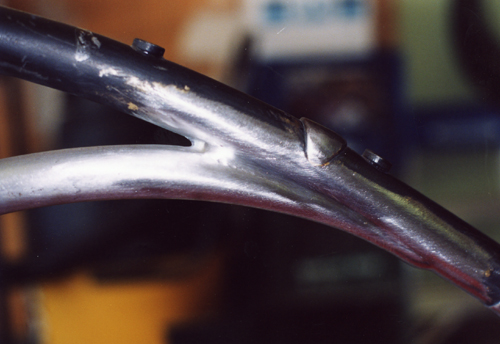
If you've done this right, it's hard to tell that the lower tank tube wasn't original! (photo #29, and #30 respectively)
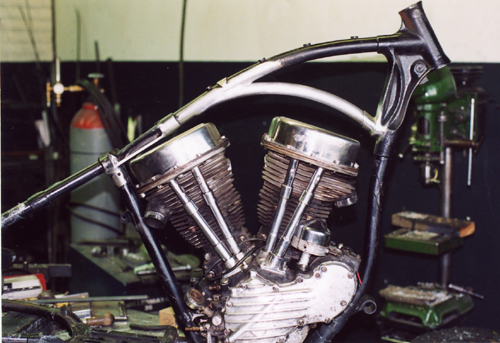

We're almost there, only two modifications remain.
With our lower tank tube in place, we can bolt the engine back in the frame. Again, mount the engine with the back engine case bolts only, torquing them to 35 lbs./ft. Looking at the profile of the engine/frame, you'll notice that the engine tilts to the front of the frame, and doesn't sit square on the front lower engine mount pad. (picture #31)
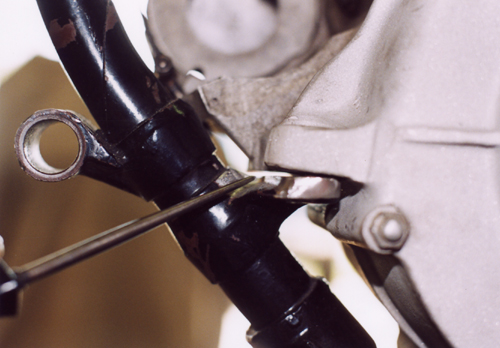
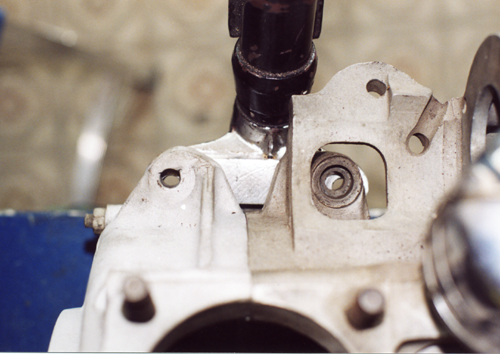
In addition, if you look from above, in the area of the front case mounting ears, that the holes in your mount pad and your case ears will not align. (picture #32)
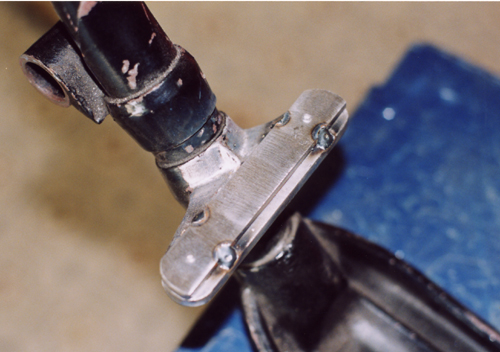
To correct this, we need to add a 1/8-inch thick, cold rolled plate to the frame mount pad and relocate the mounting holes.
Remove the engine, cut your plate, and tack weld this to your frame mount. Note the plate is not quite as wide as the pad itself. This allows us to run a good, solid bead. Reinstall the engine, torquing it to spec again. Using the case ears for a template, a layout punch (or, a long 3/8-inch grade-5 bolt, with a point ground on it) is dropped through each ear, and the bolt hole locations are punched into the plate. Do this as accurately as you can. It will pay off when you bolt the engine back into place.(picture #33)
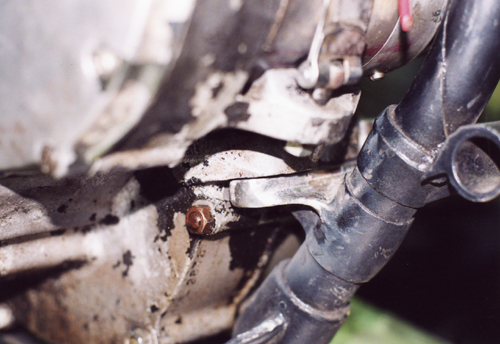
Remove the engine, and weld the plate in place. Flip your frame over, and plug weld the original front mounting holes shut. When cool drill your center-punched marks with an 1/8-inch pilot bit, followed by a 3/16-inch bit, followed by a 3/8-inch bit. Doing the drilling for the mounting holes in these steps will assure you of very accurate hole alignment. When finished, your mounting pad, and your case ears, should align. Additional thin shims may also be necessary here for a perfect bolt down.(picture # 34)
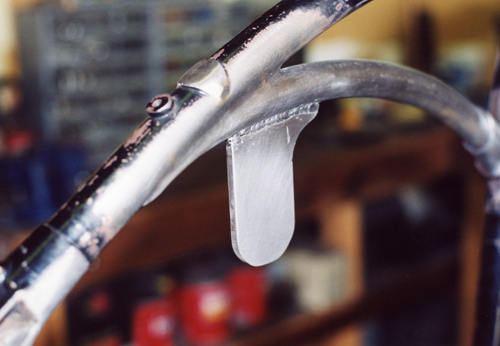
A simple upper engine mount was fabricated out of 1/4-inch thick cold rolled plate, cut to shape. Using the top motor mount, bolted to the cylinders, the upper mount location is marked and welded to the lower tank tube. After the welds cool use the motor mount, bolted to the cylinder heads, as a jig to drill the mounting bolt hole in the frame mounting tab. (picture #35)
All we have left is fabricating the anchor plate for the rear brake. This client opted for a '36-up OEM mechanical brake. As you can see, the original VL slot for the backing plate locating tab isn't even close. (picture #7 again)
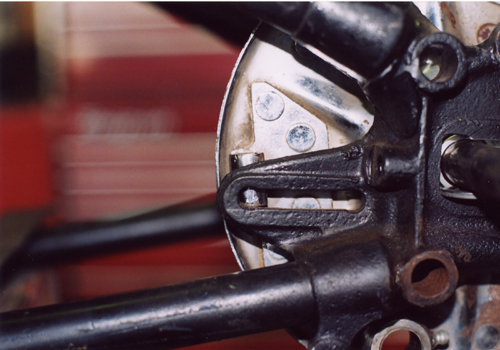
First, the upper part of the brake tab was removed and the base was draw-filed flat. (picture #36)
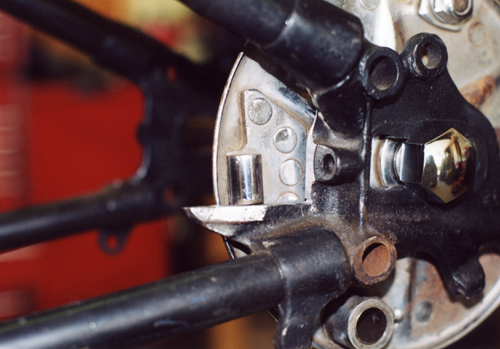
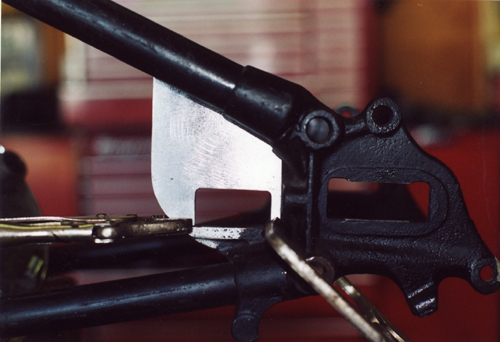
Next, a 1/4-inch thick plate was cut from cold rolled steel, with a relief that would allow the backing plate locating tab to slide back and forth during chain adjustments. (picture #37)
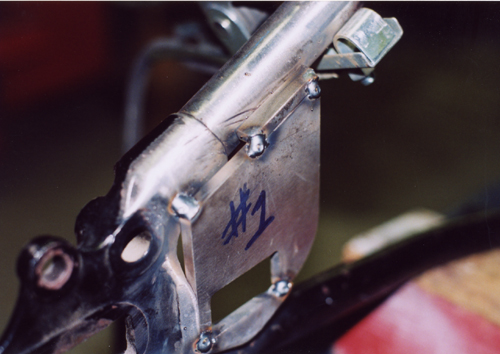
After the plate was squarely tacked in place, a small spacer was required to fill the gap between the upper plate and the upper frame rail.(picture #38)
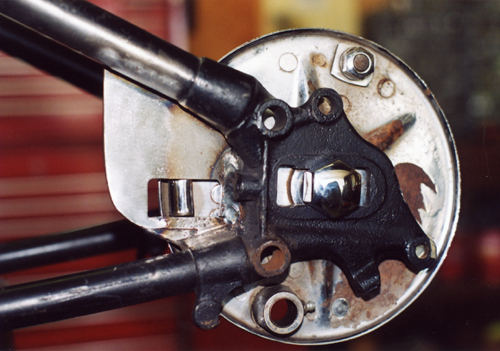
One final check, and the plate was welded into place. (picture #39)
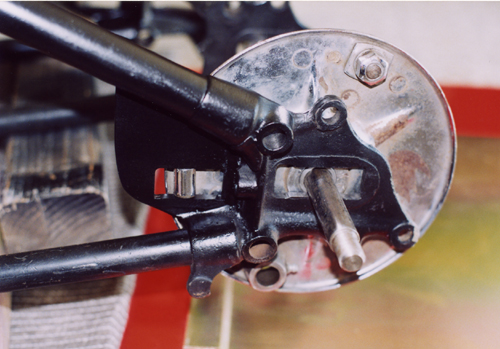
The finished plate. (picture #40)
And here's two VL frames headed back home to Cleveland. (picture #41)
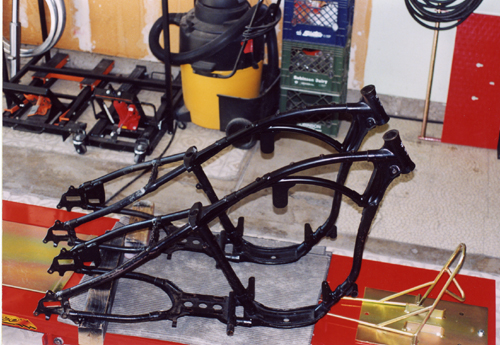
I hope this gives you a good working knowledge of what actually goes into fitting a big twin engine into a classic VL frames. It's not a difficult modification to do. But, it does involve making your patterns and replacement pieces accurately. It involves a lot of measuring, cutting, measuring, cutting, assembling, disassembling, welding, assembling, checking and double checking. Take your time, goddamnit. It saves screaming later.
Later,
Irish Rich / Shamrock Fabrication –
www.shamrockfabrication.com
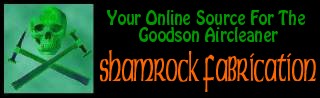