This valve is what controls the oil pressure to your engine, and protects the engine from too much pressure. Over a period of time it is known to either leak and or pop off at lower than the desired pressures. This is easily checked and repaired while the Camplate is off the engine. Feuling recommends testing the relief valve anytime the cam plate is out of the engine, and always testing the valve before it’s removed from the plate. The Feuling tool is an ideal workstation for servicing camplates.
The Feuling Cam Plate Tester comes unassembled but is easy to put together using the included instructions. Basically you insert a nipple in the tester and then screw the regulator to it and finish off with an air hose nipple.
Install the Camplate to the tester and clamp the tool in a vise. Add the air hose and open the regulator to test for leaks and pop off pressure. According to the Feuling staff: We like to see the camplate pressure relief valve seated and sealed from 0 to 30 psi with a full pop off pressure of 50 to 60 psi. It’s also important that the valve again seals at 30 psi after having opened. These recommended settings will ensure the engine is protected and receives the most oil pressure available which is especially important on those hot days, which can generate extremely high oil temperatures and low oil pressure.
If adjustments are needed use the Feuling tool #9000 to hold the spring down to remove the roll pin, spring and plunger.
Depending on what you found, you can clean the seat of the original valve or replace it with one that has a better contact surface. There are springs with more tension available and also shims that can be added to the original spring to increase the pop off pressure. Inspect and clean the camplate bore and plunger valve. Use very fine 400-600 wet-and-dry sand paper or an abrasive pad to remove any debris or burrs, then clean and reassemble the plunger valve using a spray lubricant on the bore and valve.
To re-seat the plunger valve, hold it down with a punch, turn up the air on the tool regulator while holding down and centering the plunger with the punch, then give it a goo whack with a hammer. This process will create a new seat and may need to be performed multiple times in order to obtain the desired results.
Next re-install the spring, inspect for leakage and check the pop off pressure. You may want to use a 1/8-inch pin punch to hold the spring in place for ease of testing and spring adjustments, thus eliminating the need to re-install and remove the roll pin each time.
If your existing spring is not reaching the desired pop off pressure of 50-60 psi, Feuling recommends replacing the spring (see Feuling part #8018). You can also adjust the existing spring, but if you stretch the factory spring, it may collapse and lose pressure after multiple cycles. Feuling recommends cycling the completed assembly numerous times to ensure proper operation.
When you have reached your desired pop-off pressure re-install the roll pin and proceed to install the camshafts.
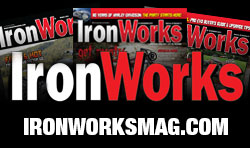