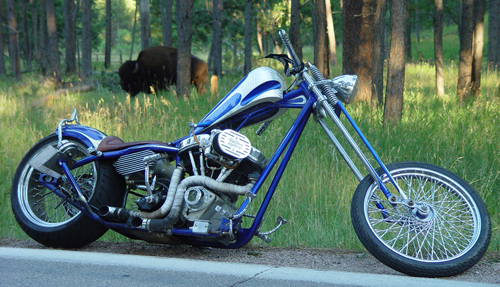
I started building a bike for two reasons: I needed something new to ride, and I didn't want bike payments. I had an idea of what I wanted. I liked the looks of the bare bone choppers, with no gimmicks. I like long springer front ends, and I like fat back tires (to an extent). The first thing I had to do was figure out what I really wanted.
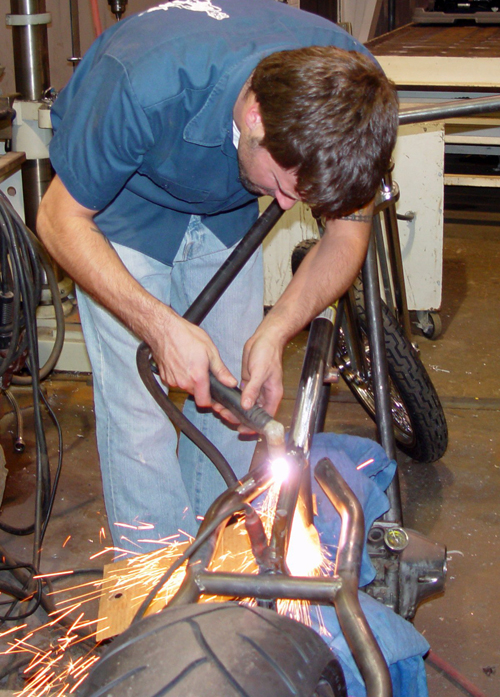
I am a big fan of Billy Lane's bikes, and I really liked his “Whole Lotta' Rosie” bike. I decide these were the dimensions I wanted my bike to have. I did a little homework and learned Billy's frame was a 6 up, 4 out Santee frame with a 42-degree rake and a 250 tire. It had a high mounted gas tank, straight and low split handlebars, plus a long springer front end. I remembered reading in his first book that he said if you can't afford what you want to buy, pick up a book and learn how to make it, so that's what I was going to do.
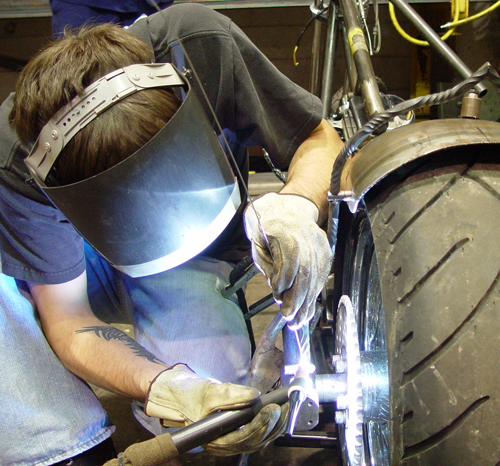
I only had basic hand tools and a flux core wire feed welder, but I figured I could tack all my parts with it and pay someone else to TIG everything. The parts I couldn't make I thought I would just pick up at a swap meet, and once it was finished I was going to rattle can everything flat black. Nice and simple.
I got an old springer front end, which was made in the early ‘70s from my dad. It came with an old Panhead chopper he bought. It was just extra parts, so he didn't need ‘em. It was missing a lot of pieces, but I figured I could make it work, and it was free.
Next I started shopping around for a good frame, I looked high and low for a good deal on a quality frame and finally came across Chopperhead Road's ad in The Horse Backstreet Choppers. Through them I got a frame with the exact dimensions for $999, and it turned out to be a great frame. Next I started shopping around for the rest of the parts for a rolling chassis. I started to look at local swap meets, but couldn't find anything that was worth anywhere close to what people wanted for it. Soon after this I met a good friend of mine named Andy Schupbach, who introduced me to eBay. It wouldn't be long before the good deals started rolling in.
I started shopping around on eBay and in no time I had wheels and tires. Around this time Andy introduced me to a guy named Bob Archambeau, who used to be a tool and die machinist for General Motors, but is now retired. It turns out he has a 3 phase lathe and mill all hooked up in his garage, and he likes to work for cheap! Bob made me some of the front end parts I was missing, and at the same time I continued to shop around for the rest of the parts on eBay. I now had a rolling chassis and would enjoy riding it whenever I could find someone to push.
I started looking for a motor and tranny, I didn't really have a preference other than the fact that I wanted a kick-start only bike. I preferred a Shovelhead motor but I was open to anything because of my budget. Sometime around June of 2005 I got a good deal on a ‘79 four-speed tranny, which was, “freshly rebuilt with Andrews gears.” I bought it, took the guys word it’s condition and started to figure out my offset distance for the tranny plate, so I could get around that big ass back tire.
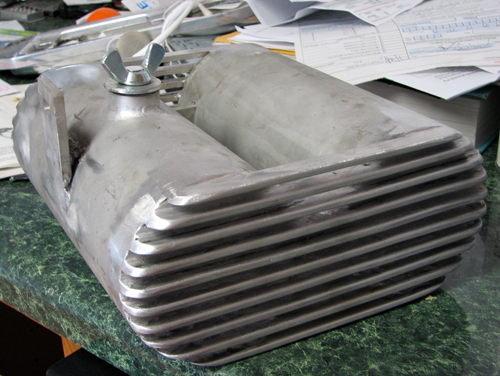
Andy showed me how to use the Bridgeport vertical mill at work, so I messed with it a little and in no time I was hacking parts out with the best of them. I made my tranny plate out of a chunk of 1/2 inch thick aluminum, and on the third or fourth try I got it right. I was still shopping for a motor and belt drive, but at the same time I was learning a little about fabrication while building the handlebars, oil tank mounts and rear fender. Sometime around August I came across a guy selling a bunch of leftover Shovelhead parts on eBay. For about $700 I scored just about everything, except pistons, cases, rockers and boxes, push rods and tubes, lifters, electrical, and so on. In other words I bought a bunch of junk that was nowhere near a complete motor. My plan at this time was to rebuild the motor with aftermarket cases, and shop around for everything else.
I kept shopping and came up with some rocker boxes which I was splitting, rounding off and re-polishing. I found a dual throat dell'orto carb set up with the manifold, which was supposed to be in good working order. I also found a belt drive: a 1 ½-inch wide Primo, which I wanted to use to be different, I just needed the clutch parts. I started piecing the clutch together at my local parts store. I also came up with the crazy idea of using old 1950s aluminum malt cups for velocity stacks. I machined a single flange from 1/2 inch aluminum and welded the cups to it. Then I smoothed out the welds and polished everything. The finished product was a dual throat, 6-inch velocity stack, which shared a single flange. By about this time I was starting to get quite a parts collection. My house was starting to look like a salvage yard, because that's where I kept everything, due to a leaky garage roof.
Everything was rolling along up to this point, so it was about time for disaster to strike. In November some punk kids kicked in my door, in the middle of the afternoon, while I was gone. They grabbed all my electronics, some tools, and apparently anything that was shiny. From what I could tell these idiots didn't know a fucking thing about cycle parts. They grabbed my brake caliper but not the rotor, one reworked rocker box but not the other, the stock Shovel heads, but without taking the valves and springs that were right next to them, and finally the carbs and velocity stacks, which I worked so hard on.
I'm sure that once these “thugs” figured out that they couldn't get a dime for the parts they stole, they got tossed to the curb. Meanwhile I was left with so few engine parts that I was better off to start looking for a whole motor than replace everything and continue to shop for what I still needed.
Within another month I received a hefty check from the insurance company, so I started looking for a complete motor. I found a few Evo's going for reasonable prices, but I really grew to like the old Shovelhead motor that I once dreamed of. I watched eBay like a hawk and it paid off, because before long I came across the deal of a lifetime. For $2,400 I bought a complete motor, which only had about 1,500 miles on it. It turns out that the guy built it to show it and rarely rode it further than down the road and back. It was titled as a ‘78 Shovelhead motor but that's hardly what it was. When it was rebuilt it was based on STD cases, with all Crane Cams valve-train components, Keith Black pistons, an S&S HVHP oil pump, and STD Panhead, dual plug heads to top it off. The only thing stock about this motor was the fly wheels and the jugs. Needless to say I got a pretty good deal, but it gets even better. The owner threw in a Daytona Twin Tech single fire ignition, and a complete charging system. Like I said, “deal of a lifetime'.
Those crooks did me one hell of a favor because if it weren't for them I'd still be piecing together a rattly old stock Shovelhead, built out of everyone else's left over parts. I could also start selling some of the old Shovelhead parts on eBay to help finance the rest of the project.
The next couple of months went by fast. I was learning a lot about metal fabrication. I learned to TIG weld from Andy, and I was taking a Machining class at the local community college. Andy drastically changed my original plans, definitely for the better. He helped me fabricate a lot of my parts at work, and he gave me the idea of making all the pegs and other bolt on parts out of twisted steel. Of course this was all inspired by Indian Larry, whom I am a great fan of.
I thought of tapering the steel square stock before it was twisted, which put a new “twist” on it. I still haven't seen anybody else do it quite like that. I also tapered and twisted some hex stock, and decided it would look great as a sissy bar, foot controls, and some other small parts. The hex stock really keeps a nice round shape when it is twisted and it also stays straight.
The tranny I bought the previous summer didn't quite look right next to the motor due to some black powder coating on the motor. I decided to tear down the tranny and polish the case, and send the covers off to be powder coated gloss black. It was when I did this that I realized something didn't quite look right about this picture. This tranny was rebuilt, yet it had globs of sealant on the outside of the case around the counter shaft seal.
I didn't want it leaking all over my back wheel so I bought a manual and decided to tear it apart and change all the seals. When I got it all apart, I figured I might as well add some style to it, so I TIG welded some flames I already had hand-sculpted out of aluminum. When I was done with this I smoothed out the welds (remember at this point I'm still learning to weld. so my beads looked like shit) and polished the whole case. Now, when you look at the tranny, the flames appear to be melting right out of the back of the case, and it looks awesome. I didn't want to have any regrets later so I decided to change all the bearings because some of them didn't look too “rebuilt.” I was certain that this tranny was a huge piece-of-shit and I bought someone else's headaches. The counter shaft leaked due to extreme heat coming off of the bearings. This heat was happening because some asshole pounded the bearings in despite the fact that the hole was about .010-inch smaller than the outside of the bearing. I had my machinist friend bore the hole in the counter shaft to accept the new bearings and before long I had it all going together smoothly. At this point I also learned that all the gears were stock Harley-Davidson parts and that the year this tranny was made Harley was producing some real garbage. Oh well, it was too late to turn back now.
This tranny was definitely a lesson, but I am glad that I can now say I know how to rebuild a tranny, while the asshole that sold it to me never learned.
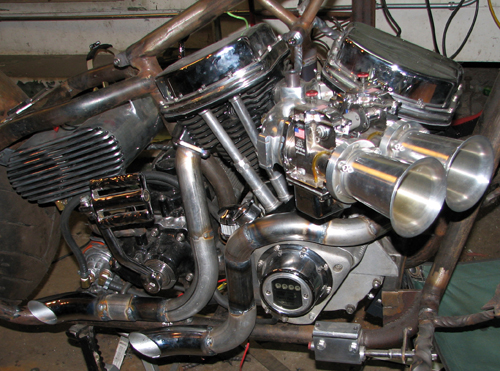
I didn't have a welder so a lot of the fabrication was going on at work, after the shift. The general foreman didn't like it, so finally it got to the point where he was threatening to fire me. My union reps confirmed that he could, if I got caught using their company equipment again. I needed to buy a TIG welder, so back to eBay I went. I found a barely used Miller syncrowave 180 for under $800, so I drove down to Indianapolis to get it.

The next couple of months sailed by. I fabricated my gas tank, my oil tank, all my controls including the handlebars, and I was getting sharp on a mill and lathe. I made my own license plate frame/taillight using a ‘64 impala lens. I used a lathe in my machining class so I turned all my own brackets and mounts out of round stock. I bought some exhaust flanges from Fab Kevin and tubing out of Jeg's and welded up my pipes with some help from my Dad. I didn't want to spend $400-600 dollars on a brake caliper to go with my sprotor set-up, so I decided to try a Wilwood caliper for a car, also out of Jeg's.
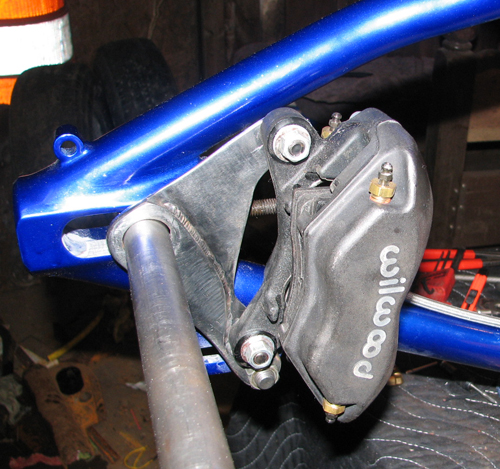
I found a dual Edelbrock carb set-up, mounted on an early weber manifold with S&S velocity stacks on eBay. I also found a good deal on a 3-inch BDL belt drive. which I decided to use to hold up the extra power of my new motor. By early May I had a complete bike, minus paint.
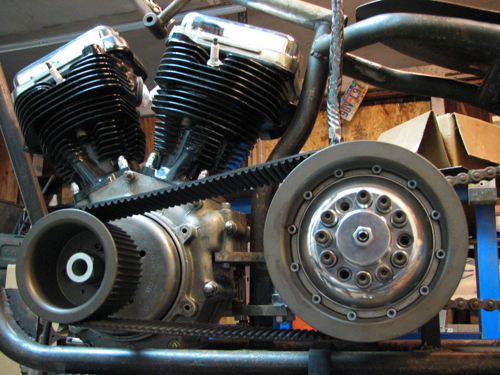
This was my first build and I was figuring out most of it as it progressed. Needless to say I didn't want to have to change anything after it was all painted. I wired everything up while it was all in raw steel, and with about 8 kicks the beast was alive. It was leaking a little oil, but it ran, and that was all that mattered to me at that point.
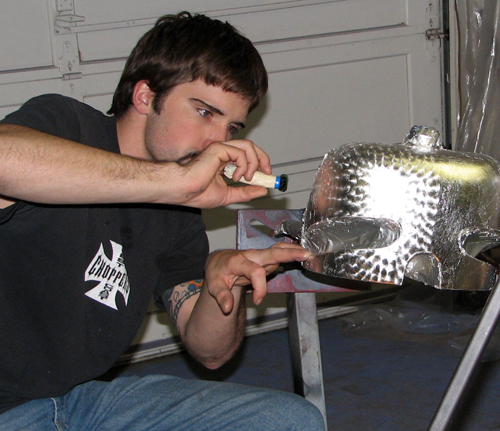
Within about a week I had it all torn apart, and my good friend Andy was going to paint it for me in his garage, with his paint, and he wasn't charging me a dime, except that I had to repay him for the paint. He volunteered to mold the gas tank, and he did all the work that took any know-how. I just helped as much as I could, molding the frame and sanding where he said to sand.
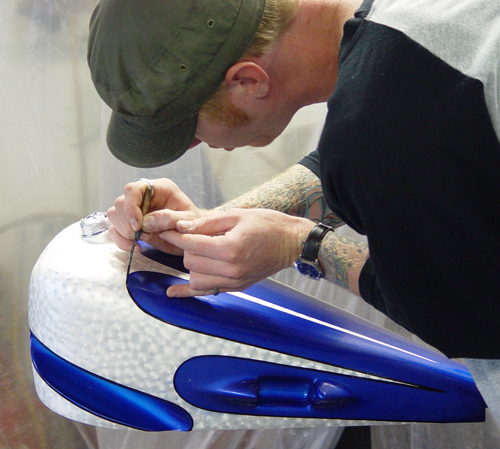
By about early June I had all the parts back from the chromer, the paint work was done. I had some awesome pinstripes thanks to Chris Hornus of Flint Michigan, and it was time to bolt it all back together and get her running. Reassembly was a breeze, probably because I took it so far in the mock up stage. I put together everything in four days, and it only took about five kicks to start it the second time.
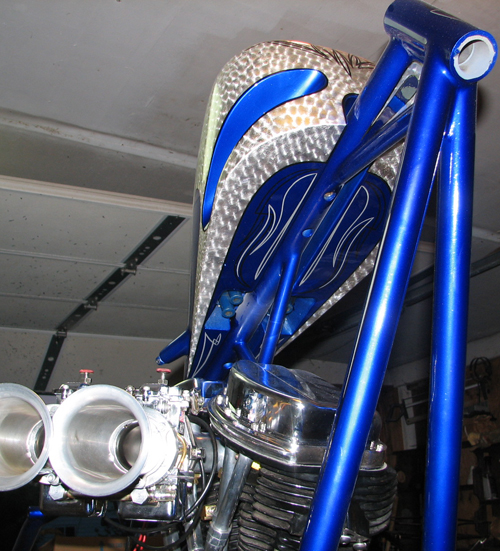
I had a couple small bugs to work out. I couldn't run velocity stacks on the Edelbrock carbs, and I was constantly blowing oil out of my breather line. These were all minor problems and were nothing to overcome. I had to install the stock air cleaner on temporarily, but eventually I put two flathead ford air cleaners on it, they look wild. I also fabricated a bracket out of aluminum to hold a half pint Jack Daniel's bottle, which acts as a catch can for the breather.
As soon as it ran, it was my only transportation, because my truck's rear-end went out in late April. I could only do one project at a time and I made gettin' the bike done my priority. Who wants to drive a truck in June anyway, right? Within a month I had all the bugs worked out, so my trusting girlfriend and I took the blue bomb on it's first long trip, from Flint to Manitowish Waters, Wisconsin, and back, which was about 1,200 miles. I am happy to say it went beautifully with only one minor set back on the way back when my alternator loosened up. luckily I was only about 2 miles into the trip home, so I was able to push it back to the cabin and get it fixed soon enough to catch the second ferry ride across Lake Michigan.
For three months this was my only transportation, I used it to travel 30 miles a day to work and back, and I still beat the hell out of it every weekend. I am proud to say that everything is holding up great. To top it all off I won best of show for the 2006 bike night season at a local bar, Scooter's Bar and Grill. (
This whole experience was great for me, and I can't wait to do it all over again this winter. I decided to make some subtle changes to this bike, and I am also building a Buell based chopper, which I will most likely sell to finance a ‘54 Panhead project. I'll send some pics of those when I can.
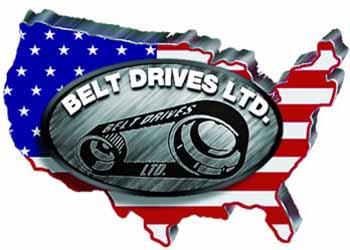
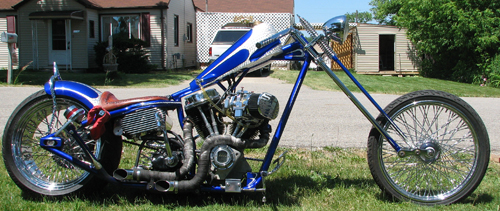
Eric’s Blue Bomb Spec Sheet
Owner: Eric Barnett
City/State: Flint Michigan
Builder: Eric Barnett
City/state ( or company contact info):
Fabrication: Eric Barnett and friends
Manufacturing: Eric Barnett
Welding: Eric Barnett and Andy Schupbach
Machining: Eric Barnett and Bob Archambeau
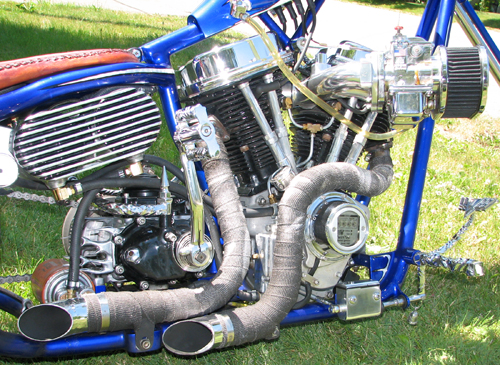
Engine
Year: 1978
Make: 1340 cc Shovelhead
Model: Big Twin
Displacement: 1340 cc
Builder or Rebuilder: Richard Zubli, of Zubli Engineering
Cases: STD cases and STD Panhead heads
Case finish: Cast
Barrels: Stock Harley
Bore: .010″ over stock
Pistons: Keith Black 10:1
Barrel finish: Powder coated gloss black
Lower end: Stock Harley
Stroke: Stock
Rods: Stock
Heads: STD dual plug pan heads
Head finish: Powder coated gloss black
Valves and springs: Crane cam, stock size
Pushrods: Crane cams
Cams: Crane Cams, roughly .570″ lift, duration unknown.
Lifters: Crane cams, solid
Carburetion: Dual 38mm Edelbrock mounted on an old Dellorto manifold, with flathead Ford aircleaners
Other:
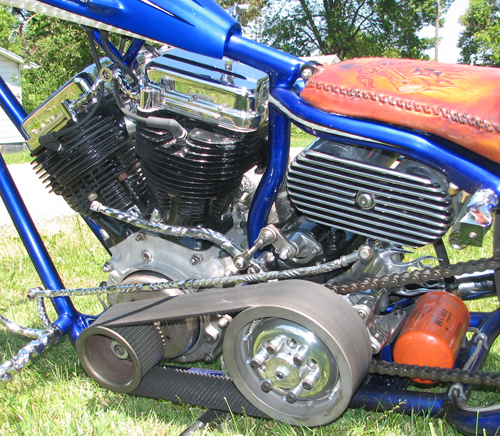
Transmission
I bought it on eBay and got royally fucked on it.
Year: 1979
Make: 4-speed,
Gear configuration: as far as I know it's all stock gear ratios
Final drive: Stock
Primary: BDL 3-inch open belt, no backing plate
Clutch: BDL
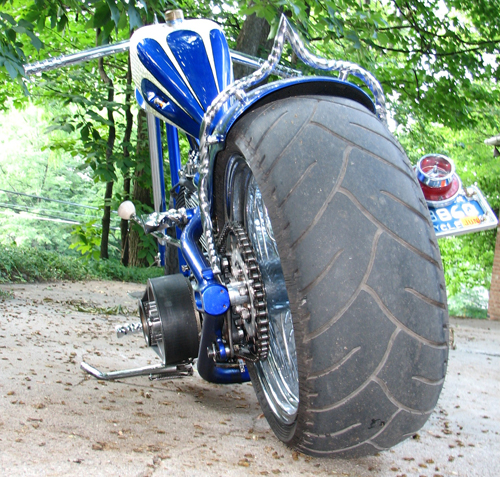
Frame
Year: 2005
Make: Chopperhead Road
Style or Model: Double down tube rigid
Stretch: 6 up and 4 out
Rake: 42 degrees
Modifications: I cut the tubes around the seat area away from the back bone, shortened them and bent them in, then welded them to the seat post tube. I also used one frame tube as an air tank to fill the airbags, under the seat.
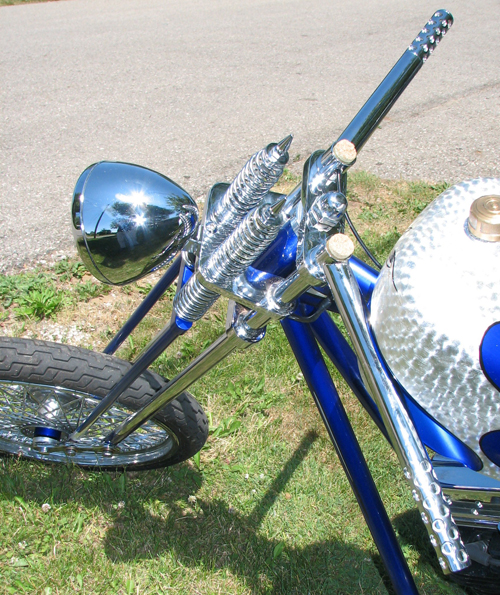
Front End
Make: Very long and narrow springer which was originally built in the '70s. This was actually the first piece I had for this project.
Year: '70s
Length: a mile
Mods: I had to shorten it by about 14 inches, make new rockers, come up with some shoulder bolts for the rockers to pivot on. I had a custom pin and top plate made for the triple trees by Bob Archambeau.
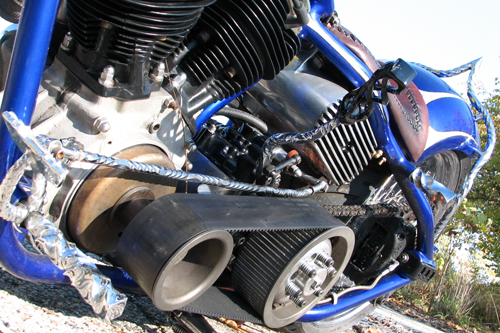
Sheet metal
Tanks: Eric Barnett
Fenders: West Coast Chopper cut in half, (they were having a sale).
Oil tank: I made the oil tank from a really long air cylinder, cut in half. The tank has two chambers, the return oil fills one chamber, then flows to and through the second chamber before being fed to the motor. The two chambers are held together by about 12 fins made of 3/16 by 1/2 inch flat stock, which I welded on individually and them rounded off with a grinder and polished. I had in between the fins powder coated gloss black so I didn't have to polish there. I'd say I have about 80 hours in it, but it turned out pretty cool.
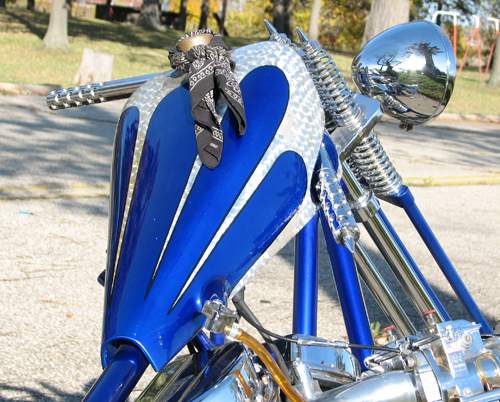
Paint
Molding: Eric Barnet and Andy Schupbach
Paint: Andy Schupbach
Graphics: engine turnded silver leaf scallops by Eric Barnett and Andy Schupbach
Pinstriping: Chris Hornus of flint Michigan
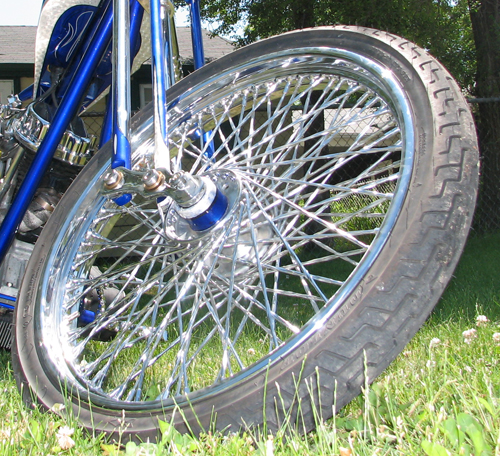
Wheels
Front
Size: 21 by 2.15 80 spoke with twisted spokes
Brake calipers: No front brake
Brake rotor(s): Nope
Tire: 80/90 21 Dunlop
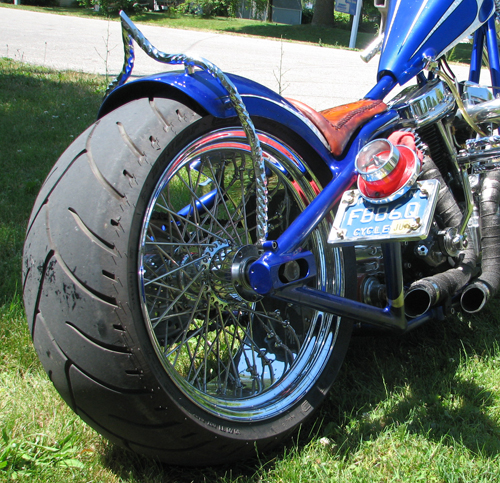
Rear
Make: DNA
Size: 18 by 8.5 40 spoke
Brake calipers: Wilwood Dynalite caliper for a car
Brake rotor: Sprotor style made by a machine shop in Lansing Michigan
Pulley: Sprotor
Tire: Dunlop 250/45R18
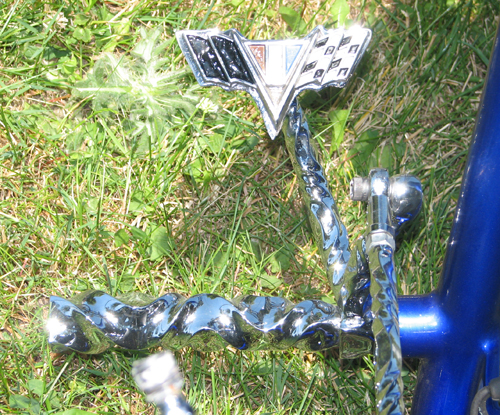
Controls
Foot controls: Hand made by me, tapered and twisted hex stock, with '60s Chevy emblems for pedals.
Finish: Chrome
Master cylinder: I believe it's for a newer Indian, eBay item.
Brake lines: Braided
Handlebar controls: None
Clutch Cable: No cable, foot clutch with twisted hexagon likage.
Brake Lines
Shifting: Jockey shift, tapered and twisted hex stock, with custom handle made by me.
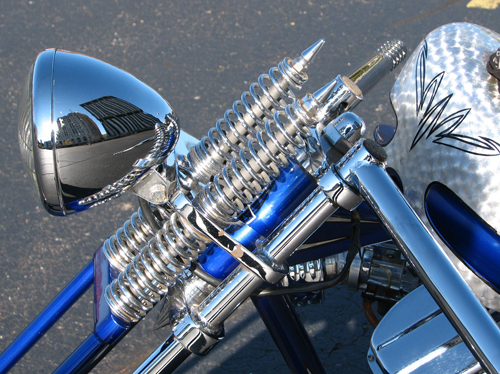
Electrical
Ignition: Daytona twin tech Dual plug, single fire with multispark.
Ignition switch: toggle
Coils: Another eBay item, dual coils from Big Dog, mounted in Gas Tank.
Regulator: Stock Harley
Charging: Stock Harley
Wiring: 4 wires, nice and simple.
Headlight: Harley 5.75″
Taillight: '64 Impala taillight mounted in a plate frame made by me.
Accessory lights: None
Electrical accessories: nada
Switches: none
Battery: Odyssey dry cell
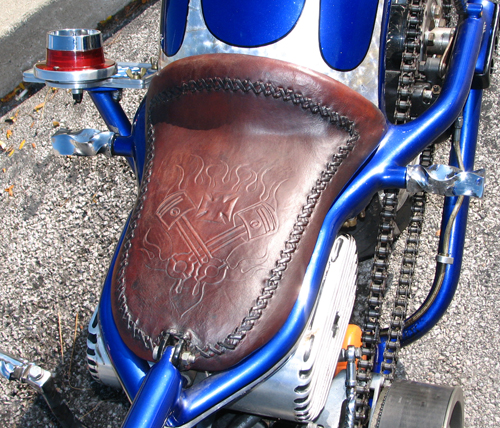
What's Left
Seat: I made the pan and did the foam, Leatherman of Flint Michigan did the leather work, also has two goodyear air bags hidden under it for a little comfort on them long rides.
Pipes: Fab Kevin did the Stainless steel flanges, I welded the pipes up.
Mufflers: No way,
Exhaust finish: The first bend and the flange is stainless, most of the pipe is steel, and the tips are autozone chrome. I wrapped most of the pipe in black header wrap so all you see is a little stainless at the beginning and a little chrome at the end.
Gas caps: Brass pipe cap, I turned it on a lathe to put a little style on it. (and because it used to say CHINA on the top)
Handlebars: 1.25 o.d. d.o.m. tubing,
Grips: bars are drilled on the end and I stuck another tube inside, I then welded the end up and smoothed it out for a seamless look. No padding, lots of grip.
Pegs: Tapered and twisted 1″ square stock
Oil filter: Fram racing filter, holds almost a quart.
Oil cooler: Tank doubles as a cooler
Oil lines: black rubber lines
Fuel filter: no, probably should get one I guess
Fuel Lines: clear plastic
Throttle: Cheap internal throttle I got off of eBay, has a bronze bushing instead of a bearing, I don't suggest buying one because mine is looking very rough after only 6 months, this is one thing I wish I wasn't trying to save money on because now It's welded to the handle bar.
Throttle cables: Barnett internal throttle cable.
Fasteners: A mixture of Stainless Steel, Chrome and Black, mostly Socket Head.
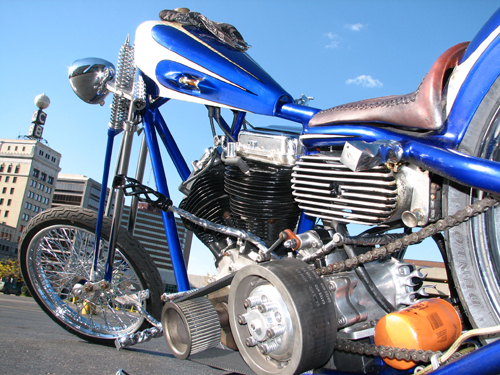
Specialty items: Everything is pretty special to me. You asked about the flames on the back of the tranny case, I made those. I started with a 4 inch square piece of 1/2 inch thick aluminum, and sketchted some flames on it. I then started sawing out the rough shape, but had trouble getting in then tight spots. I then started using a vertical mill to rough out the shape. Once this was done I started using a combination of grinders, files and emery cloth to shape and sculpt the flames. I then polished them with sandpaper and a buffing wheel. When they were finally done they looked great, but I had no idea of what I was going to do with them. A couple months later I decided they would look great on the tranny, so I welded them on and slightly molded them in when I was polishing the tranny case.
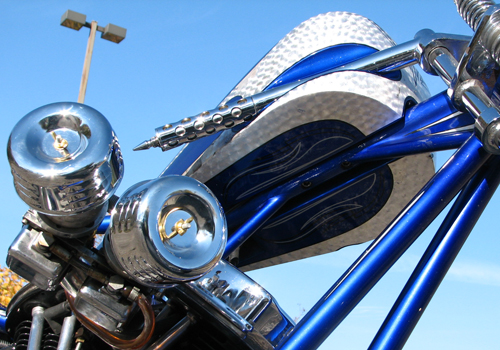
Credits: I definately want to give thanks to Andy Schupbach, he helped me through this bike practically from day one, and never charged me a dime, what he wasn't helping me on he helped make possible by teaching me new skills.
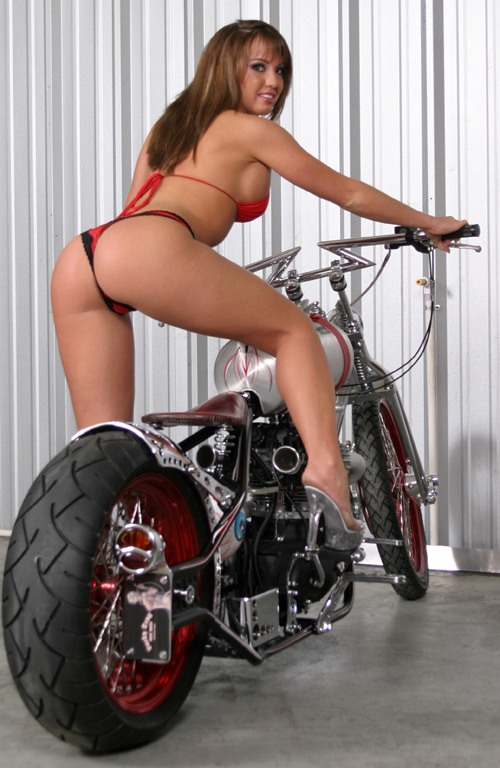