Okay, a lot has happened since the last episode. We installed the new CCE Dyna motor mounts. It was easy except for the placement of the jack. We needed to keep the jack clear so the old units would drop out easily. A chunk of 2 by 4 did the trick.
We had a discussion about Loctite. I use Loctite, stainless lock washers, and Nylock nuts whenever possible. I learned a lesson about red Loctite. That shit is mean and will cause serious problems, so the best bet for most applications is blue, except for engine and transmission mounting bolts, and as you will see transmission mainshaft splines.
When I wasn’t looking, Franky pulled the primary and started to take the clutch apart. This got tricky. The clutch hub nut is left-handed threads, whereas the engine compensator nut is right hand. Both of these bastards were tight, too tight. We fought the transmission nut for days with my impact driver.
When I feel lost, I reach out to Eric Bennett at Bennett’s Performance. He deals with this shit daily and knows the variations. “Is your compressor strong enough?” he asked. It was a good question and I’ve dealt with this issue before.
We have a shop compressor set at 150 pounds. The shop next door made a compressor connection for us out the side of their building. It takes more line to make the connection. But it did the trick. “The other issue can be too much Loctite on the threads, and you might need heat,” Eric said.
The stronger compressor did the trick for the transmission, but not the engine. Even the manual suggested too much Loctite and the use of heat. In the case of the engine, heat was the solution. We pulled everything apart.
Just to stay on the safe side, here are the Barnett Scorpion removal steps:
Note: A hydraulic press is required to remove OEM clutch hub and install the Barnett Scorpion clutch hub! We have one in the Bikernet Shop.
Barnett Tool and engineering recommends changing primary lubricant after the first 500 miles and every 5,000 miles thereafter.
Remove primary drain plug at bottom of primary.
Remove foot pegs (shifter lever) floorboard etc.
Remove five screws to remove the derby inspection cover from the primary chain cover.
Refer to your factory manual to remove the clutch basket and associated components using proper safety instructions, proper tools and pullers.
As it turned out, both major nuts were overloaded with Loctite and needed to have the threads wire-brushed clean, before installation.
Using a hydraulic press, remove the OEM clutch hub from the clutch basket. Watch for clip rings that might need removal.
Firmly support the OEM basket as shown during this operation. After pressing the hub out, check the bearing for smoothness. If the bearing feels rough or binds, it must be replaced.
Using the press is better accomplished with another set of eyes and hands to make sure everything is aligned. I have lots of chunks of bar stock of different diameters, and a wide selection of sockets help, too.
Barnett Warning: Always wear proper eye protection when removing or installing snap rings. Slippage may propel the ring with enough force to cause an eye injury. Verify the tips of the pliers are not excessively worn or damaged. That’s a tough one…
Barnett Installation Guidelines for a Scorpion Clutch
Install snap ring into rear of Barnett Scorpion hub; make sure the snap ring is correctly embedded into the snap ring groove. There are two grooves. The inner groove is for the 2011 and up models, and the outer groove is for all other models.
Reinstall the clutch basket into the primary case (don’t forget the chain, chain adjuster and the compensating sprocket). Using red Loctite on the transmission main shaft before installing the clutch hub nut. Tighten the hub nut to 50-60 ft-lbs.
Start by installing the “B” fiber plate (B plate has larger I.D.). Next, install the damper spring seat (flat steel band), and then install the damper spring (curved steel band) with the white dot facing out. Follow with a steel plate, then fiber, steel, fiber, ending with a steel plate installed last.
Install the pressure plate using six MT-95 springs, six spring cups, and six 6mm SHCS bolts.
The Barnett Scorpion comes with three varieties of spring pressure for your riding style and clutch handling. If you have a hot rod and ride hard, you may want stronger springs. If you need a lighter touch clutch, you may want to go with lighter springs.
Torque the 6mm Allens to 5 ft-lb.
Adjust clutch and cable per factory instructions.
Don’t forget the starter components if you removed the starter.
Finally, we straightened his stock shifter lever, buffed the road rash and installed it. A new Brass Balls Cycles shift lever is headed our way, but we did install the wild billet pegs.
The later model swingarm became a major issue. I couldn’t find anyone who had switched out an early model swingarm for a late heavier, stronger model.
I took on the final assembly by myself. I had to bore out the transmission case from 5/8-inch to ¾ inch for the new axle. Fortunately, the case width is exactly the same. I pressed in all the sleeves and bearings using my handmade press with all-thread. Once the parts were in place and the case bored, the swingarm fit like a dream, except…
I couldn’t get the axle nut on the left to start. I was concerned that some machining would be required, but I was patient. When Franky showed up, I backed off the axle and had him hold the nut in place on the other side. He did, and it slipped together like a dream and we applied the proper torque.
We are waiting on our MetalSport wheels, tires, rotors and pulley, and then we need to bore the old brake anchor for the new 1-inch axle.
While I worked on my Panhead, Franky installed the Brass Balls grips and Aeromach levers. His clutch perch was damaged from the accident and he had to chase one down. The Brass Balls grip confused him since it doesn’t slip under the switch housing like a stock grip would.
He cleaned up the ends of the bars, also damaged from the accident. Then he slid on the Brass Balls grips. I suggested some silicone on the bar to dampen vibration and secure the grip. Brass Balls supplies stainless setscrews to hold the billet grip in place.
He replaced the perch and we installed the Aeromach lever. It came with the old style axle and not the Teflon bar, but we greased it and oiled the cable, so finally we could adjust the clutch and install the derby. I’m sure I have a Teflon bar to replace the steel unit.
On the throttle side, he grappled with the puzzle of positioning the brake master cylinder, the lever perch, the switch housing, the throttle and the throttle cables. We carefully oiled the throttle cables from the top, greased the Brass Balls throttle cable grooves and made sure there were no kinks in the cables.
Next, we need to replace the wiring and install the Zipper’s Thundermax EFI system. Then with the MetalSport Wheels and new paint, we can replace the front end and finish the build. Hang on!
Aeromach
www.aeromachmfg.com/Motorcycle
Twin Power
BDI Exhaust
Call (530) 274-0800
Email Ramsay@bub-design.com
110 Springhill Drive, Suite 14 Grass Valley, California 95945
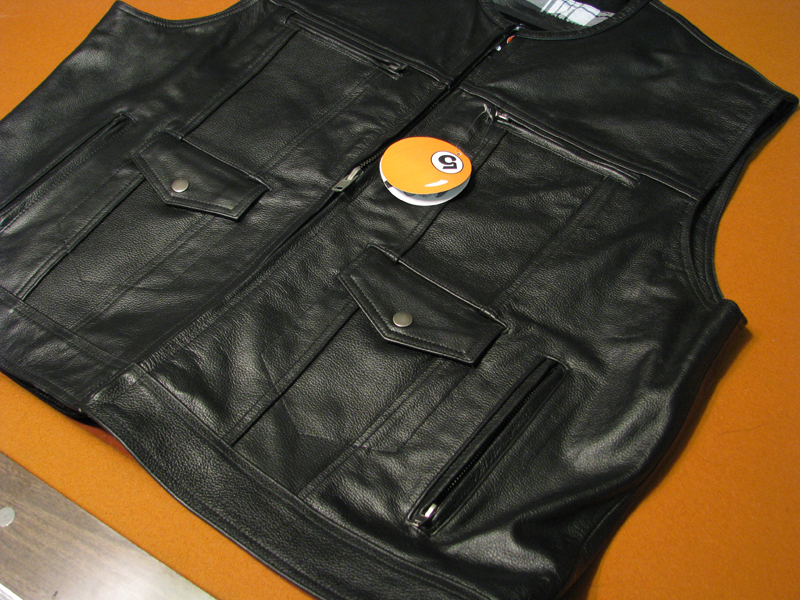
Larry Settles
Address: 1436 259th St, Harbor City, CA 90710
Phone:(310) 326-3466
Yvonne Mecalis
https://www.yvonnedesigns.com/
Chris Morrison Paint
Ronnie’s Harley-Davidson