
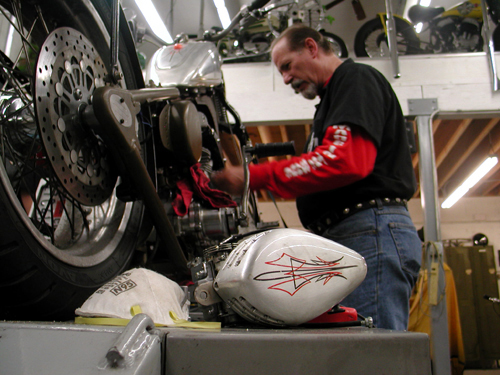
Just before rolling out and leaving for Sturgis I check my plugs in the only stock item left on the 93-inch House of Horsepower/S&S hot rod Shovelhead—the early heads. Unfortunately every time I attempted to unscrew the short reach plugs the threads and heli-coil came with them. I rode to Sturgis without ever checking the plugs again.
I reinserted the helicoils with the infamous green bearing race Loctite and didn’t touch them again. The bike ran like a champ fortunately, but every time it hiccupped, I gulped with the notion that the plug might need removing. Phil’s Speed Shop rebuilt the heads with all the best components and Phil offered to fix them, but I was on my way to the Badlands. No time. Plan B was to replace the old stock heads with S&S Performance updated heads upon return to the coast. Sounded good to me and I started a Shovelhead improvement list:
1. Replace the heads.
2. Remove the front barrel and ream the oil return hole. (it leaked from where the factory drill intersected holes for the oil return passage from the top and the bottom of the barrel. We plugged it with a brass wedge and JP Weld. It always bothered me.)
3. Realign the Mikuni Carb for a better, more secure fit. There’s a critical trick to this.
4. Replace the copper/hard oil lines with plain old rubber lines. Sure, there not as sexy, but I was running a rubbermounted oil bag and solid mounted lines. Something was going to give. One line cracked in Sturgis. It was time for a change.
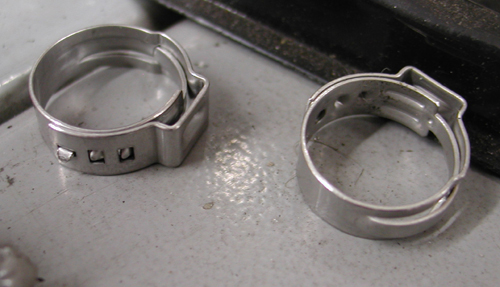
5.Take the pipes off, have them bead blasted and treat them with flat black heat paint.
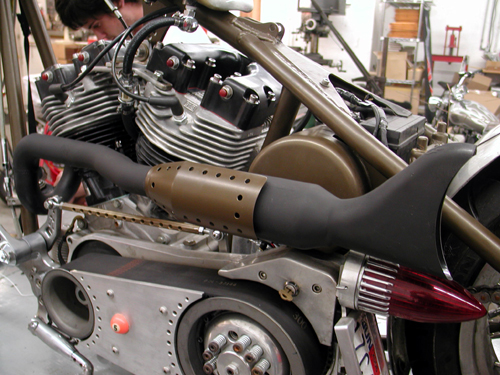
6. Have the replacement heat shield powder coated. One snapped off in Denver after a cannonball sized pothole kicked my ass.
I think that was the extent of it. Of course one fix often leads to another. The first prep aspect was to hit Larry Settle’s shop for Rocker gaskets, head gaskets and barrel gaskets. I needed one barrel gasket to replace the front barrel gasket after we removed it.
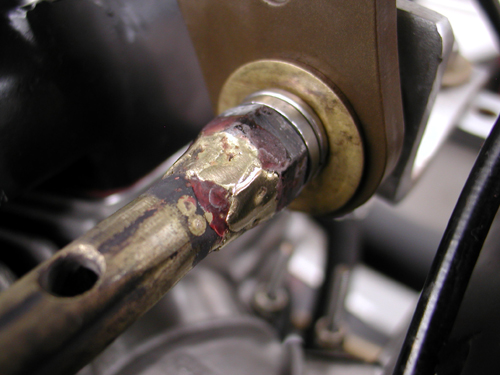
We disassembled the top motormount first and removed the carb, releasing it from the throttle cable and gas line and set it aside. I discovered that my brass carb mount was cracked where it met with the frame. I added a thick layer of braze.
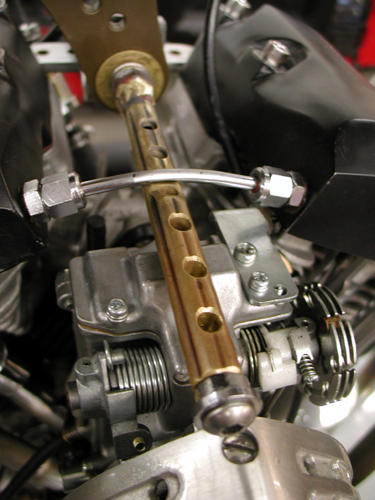
We watched out for spilled gas. We removed the push rods and kept them in order, because they were all different lengths. We removed the pipes and tried to organize the fasteners so we wouldn’t lose the bastards.
The above operations gave us space and accessibility to reach the barrel nuts and head bolts. We discovered that both fasteners had their quirks and why. Since this is a big bore engine (3 5/8), the head bolts were a narrow 12-point stainless steel jobs that were removed with 12-point 7/16 box end wrenches. All my cool head bolt wrenches were too large for the job. I discovered that it took every 7/16 box end wrench, in the tool box, to reach all those 12-point heads. Ultimately I altered a broken head-bolt wrench to reach in and find a secure connection. We welded two Craftsman short 7/16, 12-point sockets to the Snap-On head bolt wrench. Is that against the code of the West, or what?
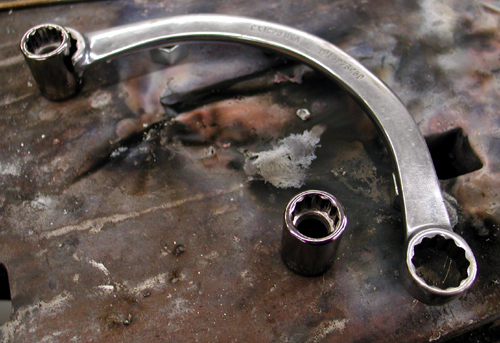
After MIG welding the sockets, grinding the welds, smoothing the surfaces and polishing the edges, it worked like a champ.

There’s another trick. The barrel bolts are also trimmed and small, reachable with a ½-inch open-end wrench. In addition they’re tall, so to remove them, the barrel must be lifted before they will come completely off the case studs. Tricky.
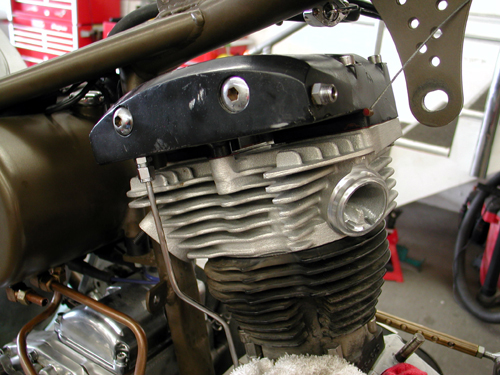
There’s a trick about the oil lines that run to the rear head and between the heads. I loosened up the pipe fittings, but then let them sit. When the heads came loose so did the lines. We had to watch this procedure when we slipped the heads back together. I didn’t need to arch or bend the lines.
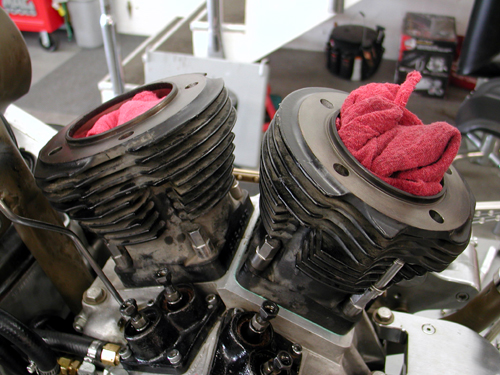
Once everything came apart we cleaned the gasket surfaces thoroughly. We discovered that the blue tephlon gasket material comes off with electrical contact cleaner better than trying to scrap it, which I avoid. The catch with big cylinders is the slim barrel gasket material and edges. Not much to work with considering the additional power. Be extremely careful.
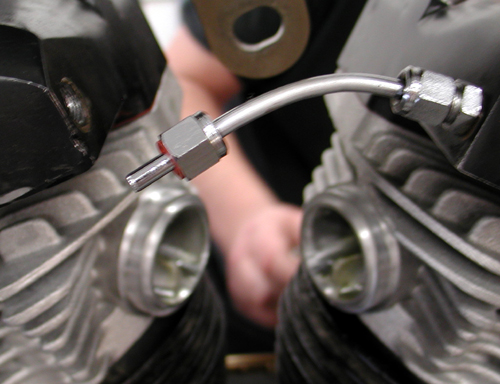
Before we go into the assembly process here’s the base material from S&S about their heads and assorted equipment:
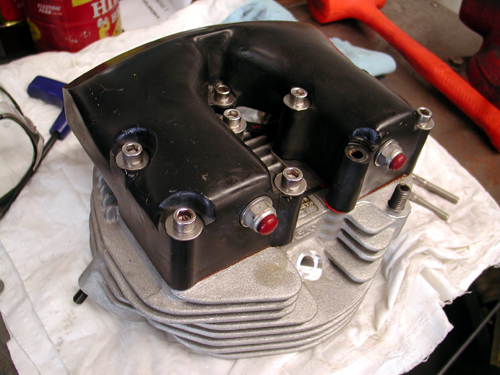
S&S SUPER STOCK® CYLINDER HEADSFOR 1966-'84 SHOVELHEAD ENGINES
Super Stock replacement heads for 1966 to 1984 shovelheadengines maintain a stock appearance for restoration purposesbut offer improved port shapes for riders interested in moreperformance.
As with other S&S heads, our CNC machining maintainsdimensional accuracy and reduces cost. This allows us tooffer the finest possible parts at a reasonable price.While stock heads use studs to attach the rocker boxassemblies, S&S heads utilize 5/16″-18 hex-head bolts.
Rocker cover bolts are included with each completeShovel-style head kit. Otherwise, S&S heads accept allstock-style components.
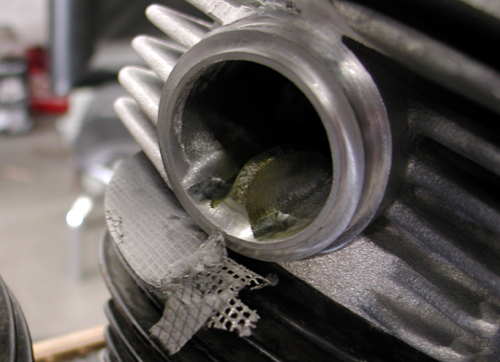
PORTS AND COMBUSTION CHAMBERIntake and exhaust ports are in the stock locations and are thesame size as stock. Stock intake manifolds and exhaust pipesare easily installed with no modification required. Heads areavailable for both the 1966-'78 o-ring and 1979-'84 rubberband-type manifolds.
Since S&S heads are compatible withstock manifolds, special manifolds are not required except forengines with taller than stock cylinders.S&S intake ports feature a directional vane to route theincoming fuel-air mixture around the valve guide and valvestem for improved performance. At 1.940-inch, intake valves arethe same diameter as stock, but exhaust valve diameter(1.720-inch) has been reduced by .030-inch to improve valve to valveclearance for cams with high TDC lifts and to improve flow. Astock-like hemispherical combustion chamber is compatiblewith all standard Shovelhead style pistons.
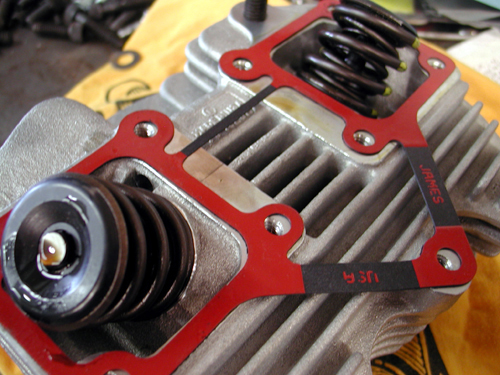
VALVE TRAIN COMPONENTS
Valve train components used in S&S cylinder heads forShovelhead engines are specifically selected for durabilityunder contemporary, real-life conditions. They are compatiblewith present unleaded fuels. Valve springs can handle .590-inchtotal lift. Heads are machined to accept cams with TDC lifts of.210-inch on both valves.
SIMPLE INSTALLATIONBecause S&S cylinder heads for Shovelhead engineshave stock dimensions, they readily bolt on with astock-like fit with no clearance problems with framesand standard Shovelhead exhausts. Complete kitsinclude all gaskets required for installation exceptintake manifold seals.
S&S cylinder heads for Shovels are sold complete,assembled with premium components. Installed partsinclude valve seats, guides, seals, valves, valve springs,collars, and keepers. Complete kits also include rockercover gaskets, head and base gaskets, all requiredhardware, and instructions.
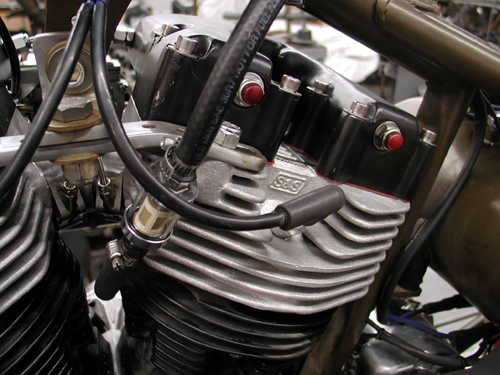
OPTIONS FOR SPECIAL ORDER
Cylinder heads for Shovelhead engines are available from S&S inblack powdercoat as well as natural cast aluminum finish.
Machining for dual spark plugs and/or external oil return lines isavailable at an extremely reasonable cost. Both of these options arenormally associated with large-displacement, high-performance,competition engines. However, dual spark plugs are often used instreet engines to control detonation or knock, and external oilreturns are not uncommon on high performance Shovelhead streetengines. External oil returns are used to redirect return oil from thecylinder heads so that it does not drain into the flywheel cavity inthe stock manner. This is intended to reduce drag on the flywheelsat high rpm. These options are available by special order only.
SPECIAL REPLACEMENT CYLINDER HEADSFOR S&S 93-Inch HC SHOVELHEAD STYLE ENGINE
O-ring style 35/8″ dual plugged – internal oil return
Set ……………………………………………………………90-1491
Set without valves and springs …………………..90-1489
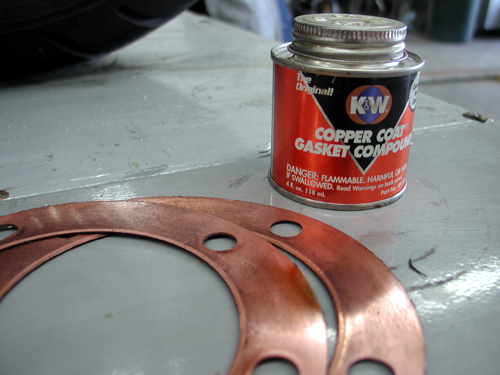
It was easy to clean the heads ‘cause Phil used thick brass gaskets and they were unharmed, like a big brass washer. Here’s where the quirky aspect jumped at us like a frightened cat. I had my three grandkids hanging out over the weekend, and they constantly asked me what they could do, so we positioned them around the lift with little wrenches to tighten head bolts, a boring job.
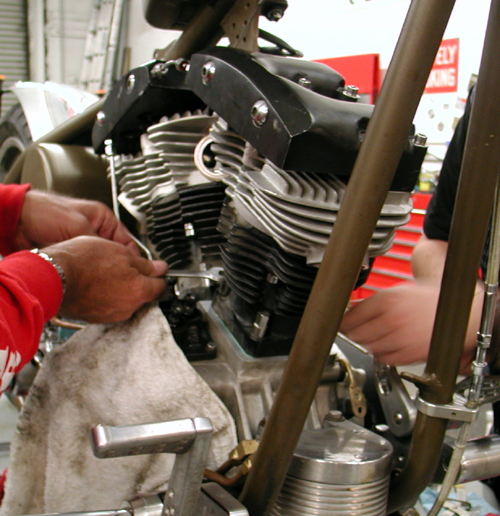
Fortunately it was recommended not to use any gasket sealer or glue with the Rev Tech tephlon coated gaskets. We didn’t. The second tip was to align the O-ring heads with the intake manifold before tightening. We also fed the oil lines into place as we aligned the intake manifold and started the fittings, but didn’t tighten them. Then the kids went to work. Then highly educated Bikernet employees, like Snake, checked the head bolts.
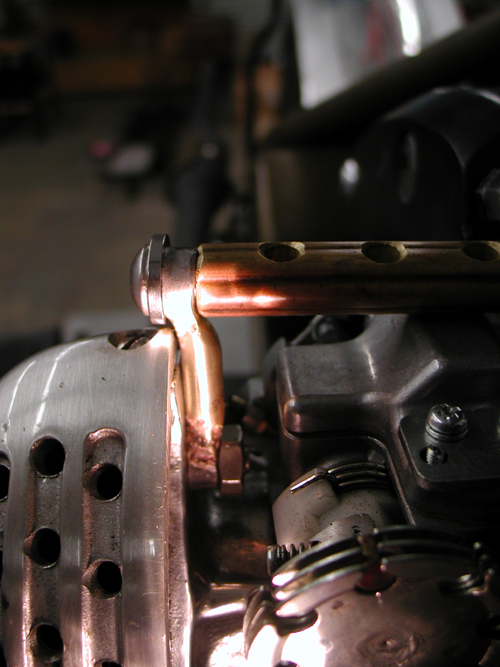
The next morning I asked Black Market John if the headbolts were tight and received a positive response—I thought. That afternoon, we blew both the head gaskets during our first road test.
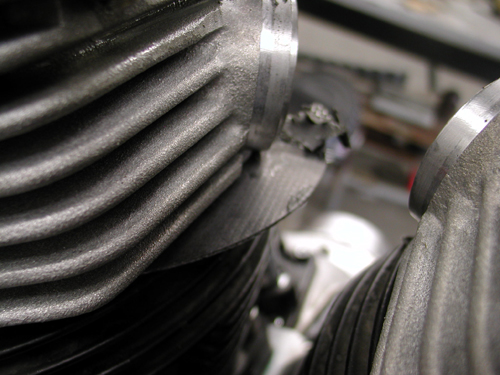
That night we drank whiskey and I tore into the top end once more. Fortunately we still had Phil’s copper gaskets and they were good to go, as if they put a hex on the project.
The next day we hit the lift like hungry dogs determined to remove and replace the heads pronto. All the other repairs were made, so it was just a matter of stripping her down, replacing the gaskets, bolting her back together and adjusting the valves.
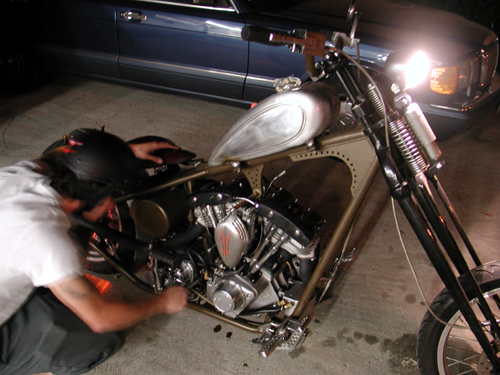
I discovered that adjusting the valves had it’s own tricks. After we ran it a few miles I adjusted the solids by finding the lowest spot in the cam travel and taking out all the play (one at a time), but allowing me to spin the pushrods slightly. But then I tightened the rocker boxes and had to adjust the valves again.
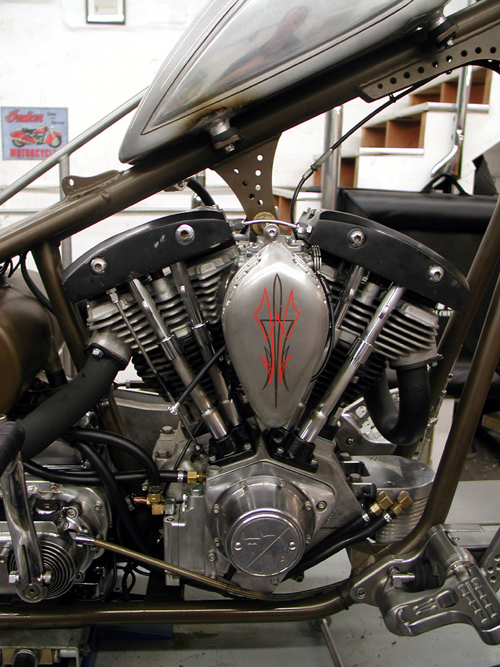
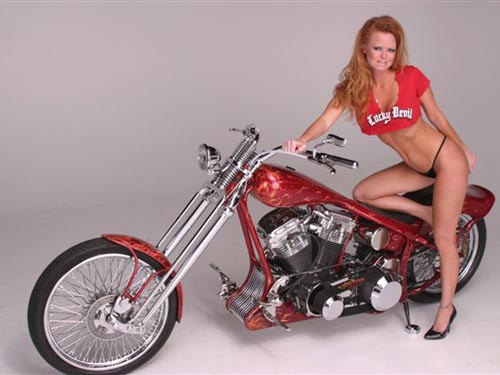
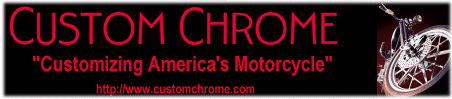