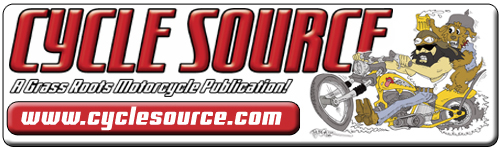
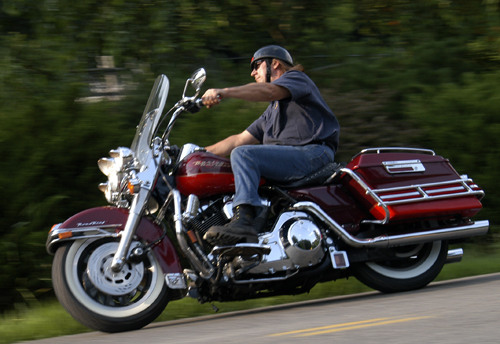
Editor’s note:We’re working with Chris, the editor of Cycle Source to bring you even more current tech material. Let us know what you think. This is a semi-automatic clutch system. In some respects they are very helpful, especially for jockey-shift bikes, but they have their dangerous drawbacks. I know Mike Phillips of Grandeur makes a clutch that’s nearly automatic. Just be careful with these puppies. Let’s get to work.–Bandit
In our formidable years we were frequently called upon, or more or less designated by the graybeards, to chip in and lend a hand. We didn’t know back then, but they were teaching us valuable lessons for the future; work hard, pitch in, trust in one another, and you shall live a full life. We here at the Source still hold those values close, so when we heard that a friend of ours, Denise Gasper, was having some difficulty operating the clutch on her '95 Road King, we agreed to put our heads together to help her find a solution. (Ol' Man Dave would dispute this by saying “All your heads put together still wouldn’t make one good head.”) Denise has severe arthritic pain in her left elbow from young accidents. Time goes on and Denise's tolerance for pain fades, but the motorcycling spirit remains strong, and we want to help keep that spirit alive!
Denise reached out and found some wonderful folks with extremely large hearts and was blessed with the Rekluse ProStart Clutch, a high-performance, semiautomatic, centrifugal clutch. Trying out cool new products is always hip, so we eagerly agreed to perform the installation. It was off to the operating table at Pappy's shack.
First thing, open up the package and inspect the instructions, read them over thoroughly, then we inventoried the parts. Then we obtained the rest of the necessary items to complete the task, such as primary side gaskets, tranny gasket and enough of the specified lubricants to refill the primary chain case and transmission.
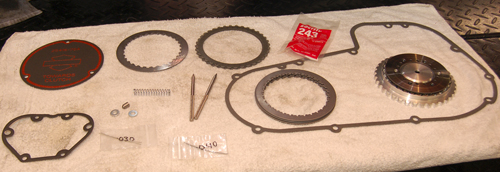
Two quarts of Genuine H-D formula tranny and primary lubricant would be plenty for the '95 Road King. It’s always handy to have a service manual for the specific model. We followed the Code of the West and disconnected the battery first before starting any primary drive work, to prevent any fingers from being torn off.
As per the H-D service manual, remove the drain plug from the bottom of the primary cover, let it empty out, inspect the drain plug magnet for metal shavings, (a small amount is normal) and clean the debris from the drain plug.
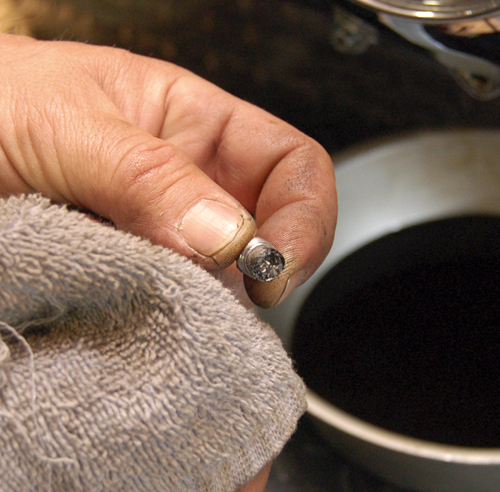
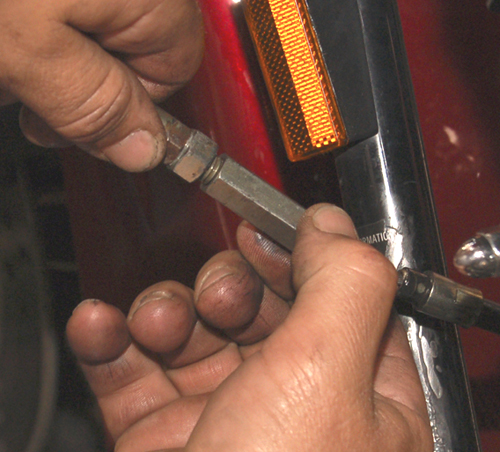
Next, loosen the in-line clutch cable adjuster and wind it together to achieve maximum cable slop.
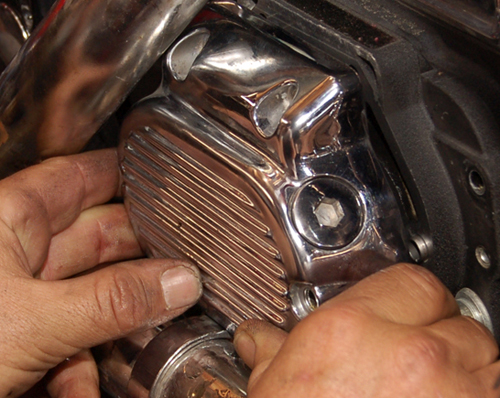
Again following the service manual, remove the clutch release cover and gasket leaving the clutch cable attached.
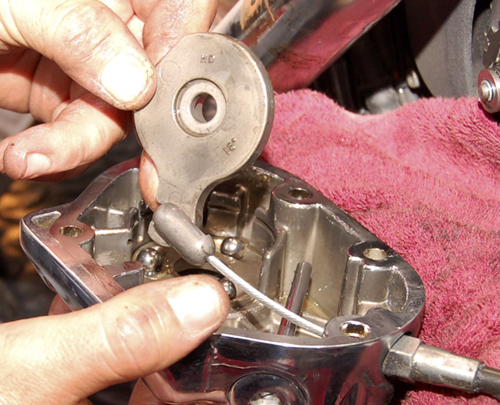
Then remove the snap ring and the components from the clutch release cover.
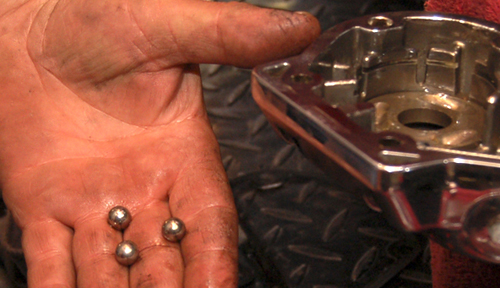
Place one washer over the end of the clutch cable followed by the spring and other washer. And finally, add the ramp coupling to the end of the clutch cable.

Apply a small amount of grease to the inner ramp then install the three balls into their detents.
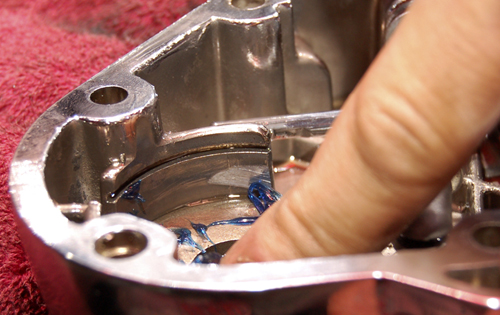
Connect the outer ramp to the ramp coupling, place it over the three balls and secure it in place with the snap ring. You are now ready to re-install the clutch release cover along with a new gasket, refer to the service manual for proper installation and torque specs of the cover.
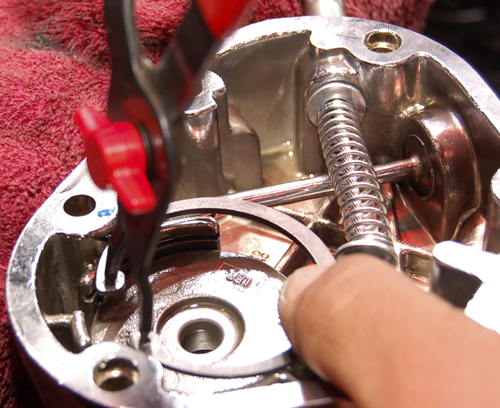
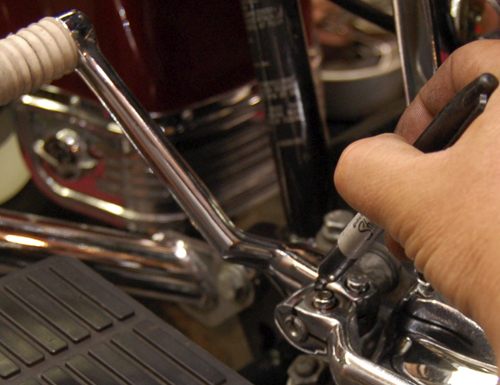
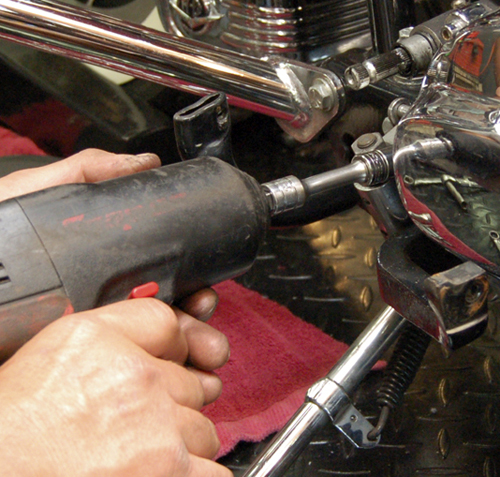
With the primary drained, remove the outer primary cover bolts of the clutch and chain inspection covers and remove them along with the gaskets.
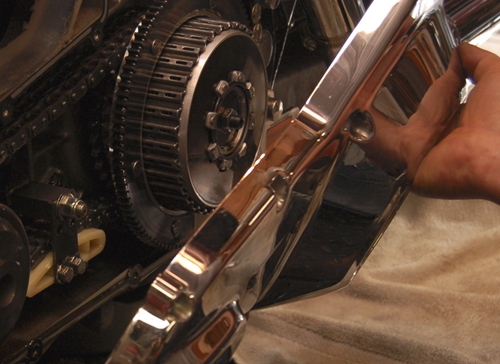
Remove the bolts from the primary cover itself and remove it along with the gasket.
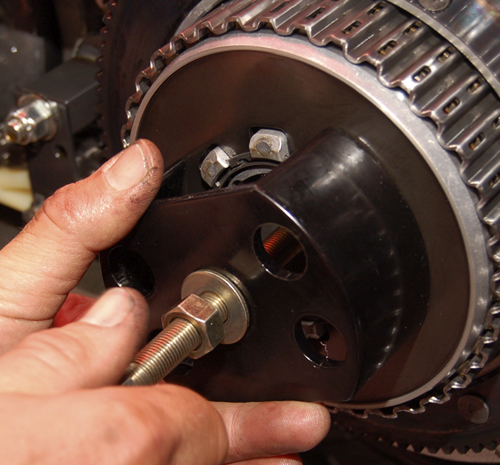
Loosen the lock nut and remove the throw-out adjuster from the pressure plate, set aside it will be re-installed. Obtain a JIMS clutch spring compressor tool to relieve the clutch spring tension, remove the inner snap-ring holding the clutch spring to the clutch basket and remove the pressure plate.
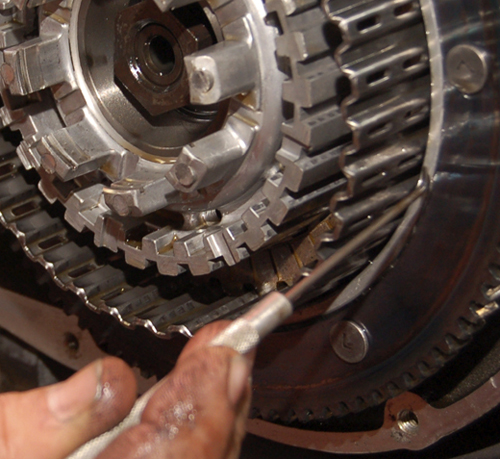
Remove the clutch pack of friction discs and drive plates from the clutch basket.
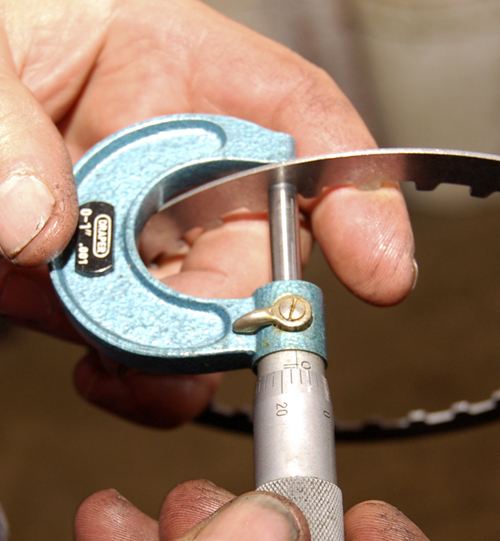
Remove the spring plate from the pack and the six other stock steel drive plates, put them aside, only one plate will be reused. A micrometer or calipers should be used to measure thickness of the Rekluse steel drive plates.
Load the clutch basket, start by inserting a stock friction disc followed by a Rekluse 0.047-inch steel drive plate into the clutch basket, continue this procedure until all eight stock friction discs are installed. The kit contains two friction discs along with different thicknesses of steel drive plates, so pay close attention while putting them in, measure then install!
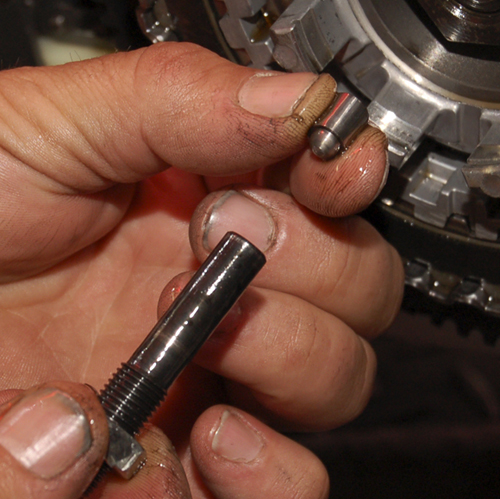
Next, place in a Rekluse 0.040 steel drive plate followed by a friction disc, then a stock 0.062 steel drive plate and finally the last friction disc. You are now ready to install the Pro Start pressure plate. A throw-out spacer is provided; it is placed into the main shaft hole with the dome end out.
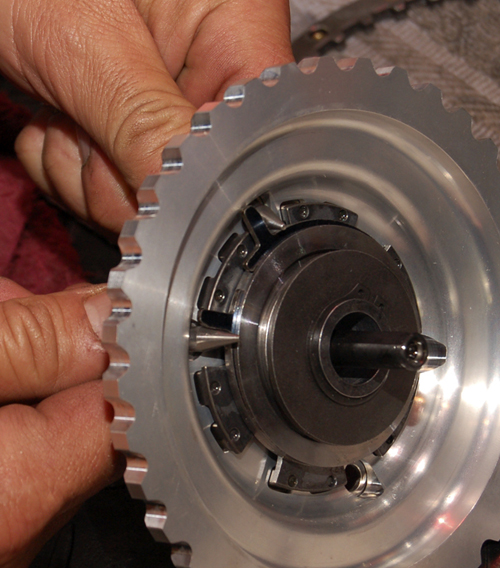
Screw the stock throw-out clutch pushrod adjuster into the Pro Start pressure plate leaving approx.1/2-inch of thread showing, insert the Rekluse retaining ring tools through the access holes to catch the outer edge of the retaining ring tabs, compress the retaining ring by prying outward on the tools.
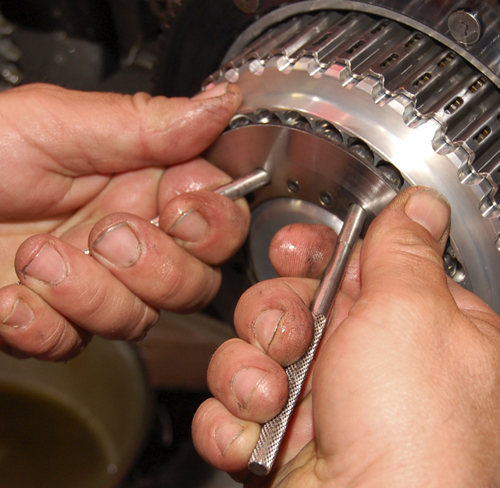
Slip the clutch pushrod into the main shaft; this will help line things up. Center the gap of the retaining ring over one of the eight center clutch posts and push the pressure plate into place. Insure that the retaining ring is fully seated into the groove of the center clutch posts by pushing in and pulling out on the throw-out to make certain it is locked in place!
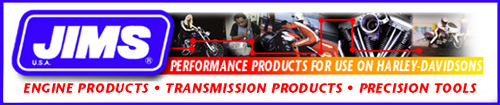
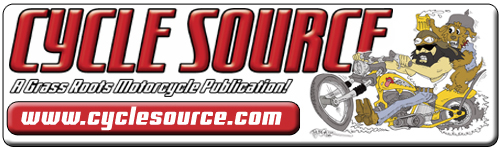
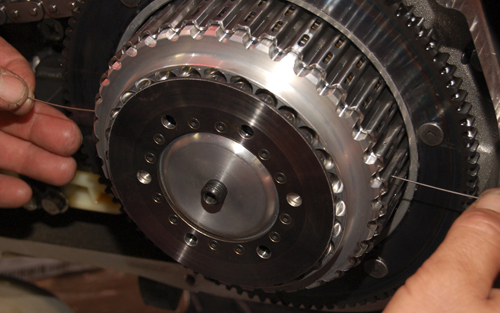
Measuring the installed gap of the Pro Start Clutch is done with wire gauges supplied with the kit. The gap should be 0.030 to 0.040-inch between the steel drive plates and the friction discs, this is the distance of travel required to properly clamp the clutch pack. Start by sliding the 0.030 wires into the gap between a friction disc and drive plate at 180 degrees apart.
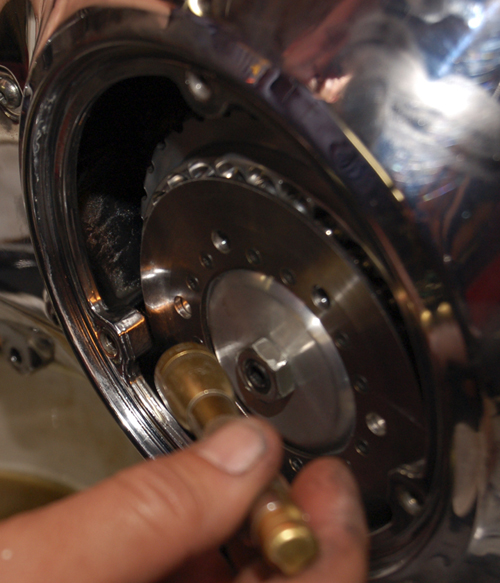
If a slight drag is felt on the 0.030 wires and the 0.040 wires will not slip in, you're are in good shape. Should the gap be too tight or too loose, follow the calculations in the Pro Start Clutch installation guide for configuration of the steel drive plates to obtain the proper installed gap. Adjust the clutch throw-out slack by turning it clockwise until it seats against the throw-out spacer and rod. Back out the throw-out adjuster by turning it counter clockwise 1-1/2 to 1-3/4 turns. While holding the throw-out in place with a 7/32-inch hex key, tighten the locking nut with a 11/16 end wrench. Before installing the primary cover, an inspection must be made of the two lower bosses that the derby cover attaches to. If any contact is made with the outside of the clutch, a bit of relieving must be done.
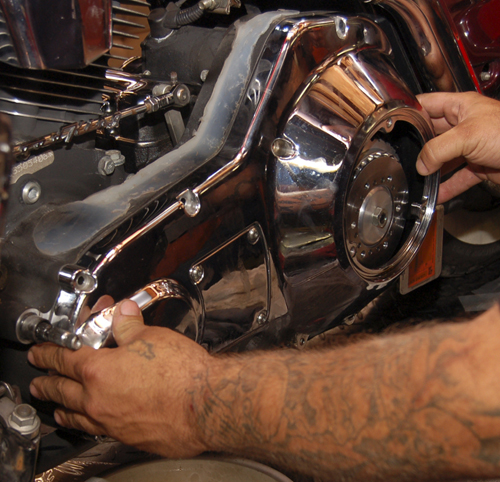
Grinding can be performed with a Dremel tool, by chamfering the inner edges of the bosses; there should be at least 0.010-inch clearance between the primary and the Pro Start Clutch. Clean any shavings and chips from the cover before final installation. Follow the H-D service manual for proper re-installation of the outter primary covers and gasket.
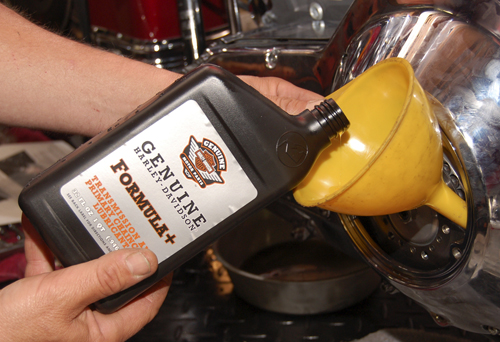
Be sure to inspect the drain plug o-rings. If they are nicked, replace them! Re-install all removed accessories. Remove the motorcycle from the lift and insure the transmission is in neutral. Start the bike and let it warm up to operating temperature. With the bike in NEUTRAL rev the engine to a minimum of 2500 rpms then adjust the clutch cable slack. Turn the in-line adjuster until there is 1/4-inch of clutch lever movement before any resistance is felt. Doing this will ensure proper cable slack set-up. Engine idle should be between 900 and 1050 rpms. If needed adjust idle speed according to the H-D service manual. We adjusted Denise’s idle speed of her Road King to 950rpm.
The bike was well warmed up. It was time for the test ride. Rekluse suggests a thorough reading of the owner’s manual provided, prior to riding the bike for total understanding of how the Rekluse Pro-Start Clutch operates. When you pull the clutch lever in at idle it feels as if the clutch cable is not attached to anything, there is almost no resistance. I dropped the shifter into first gear and slowly let the clutch lever out, the bike just sat there idling in gear. No drag was felt. It was kinda’ freaky. I gently rolled on the throttle and was amazed at how smoothly the bike pulled out. I got rolling to about 20 mph and applied the brakes without pulling in the clutch. The bike came to a complete stop in gear with a very slight drag felt in the clutch; this is normal. To eliminate the drag, simply pull the clutch lever in and release it and the drag was no longer felt.
Rekluse recommends a break-in of stop and go for approximately one hour, this should be sufficient. After I felt comfortable with the operation I headed for the highway. The clutch seemed to hook up well and there was no slipping. I ran up and down through the gears and it was smooth. This is a semi-automatic unit and Rekluse suggests always using the clutch lever when shifting gears, and to pull the clutch in while stopped in traffic. Making a habit of holding the clutch lever in while stopped will prevent unexpected movement forward if you rev the engine. I rode for an hour or so and was becoming quite in tune with the operation of the Pro-Start Clutch.
After putting the clutch through its paces, I was very happy with the way it was working. It was performing just as was claimed in the owners manual and I believe the operation was a success!! I give this product a big thumbs-up and will review it at regular maintenance intervals. We would like to thank all those involved who gave freely of their time to lend a helping hand to keep the spirit alive, your generosity is heart felt, and thanks again Al for the helpful phone tech info. I think all is well.
Well, I have to call Denise now and give her the good news, she will be more than ready to throw on her boots and meet me at the park for a briefing and a test ride. Once again thanks to all, hope to see you out there!!
RESOURCES:
Rekluse Motor Sports,inc
110 E. 43rd Street
Boise,Idaho 83714
Ph. 208-426-0659
support@rekluse.com
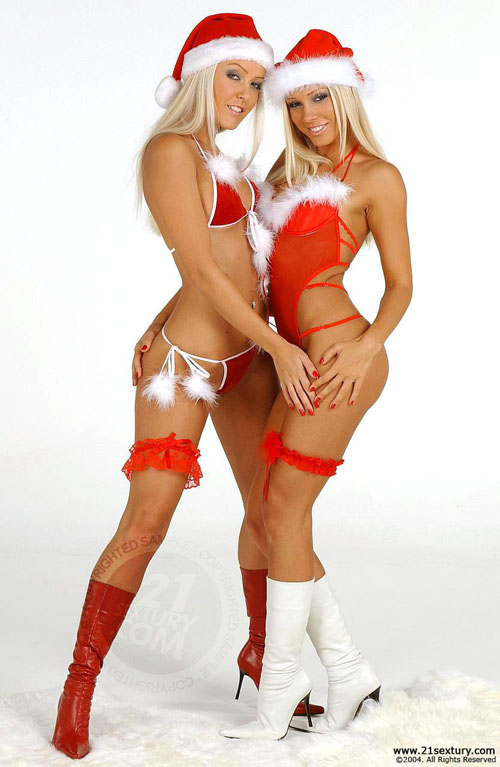