A friend, the notorious Deadwood John, called recently about his 1960 Panhead roller project, sort of a basket case on wheels. The engine still remained in the frame and a glide front end was in place, but not much else.
He wrote to Ron the shop owner in Alaska and said, “What about the transmission?” Ron who ran this shop for 40 years was an old friend. Semi-retired he was willing to help with all aspects of the build, so he sent John a box of transmission parts.
John tried to hand it to his engine rebuilder who rightfully turned him down. I’ve been around 4-speed transmissions for 50 years and rebuilt one in 1971. Kinda fucked it up but made it right.
“I’ll give it a shot,” I said to John and went to work with a manual, a parts manual from the era, a Lowbrow, Frank Kaisler video and any other resource I could find. I worked with Frank for years at Easyriders and he was a Hamster until his passing a few years back. I also dug out every 4-speed transmission part I could find, which took serious sorting from all the 5-speed stuff.
So, if you’re in the mood to rebuild an early, greasy 4-speed transmission I’m going to share my notes and suggestions from the bros. I will also share product warnings, tools, etc.
Watching Frank’s video with the Lowbrow crew covers the entire process, but I find videos cumbersome. I want to turn the page and see what I need. Can’t do that with videos without getting grease all over the screen.
Still, if you watched the entire video before you started the process, you would know what you’re up against and what you need.
My notes here will help with the sloppy effort and inform you of the blunders I encountered.
First, I inspected all the shit in the box. Much of it was junk and needed to be replaced. I soaked the trans case and the partially completed kicker cover. I studied all the threaded holes and the stud threads.
Ron sent a case which was approximately a 1965 electric-start version with the wings cut off. The corner of the case was also damaged where the mounting stud rested. It had been welded and later in the game the stud came loose. I re-installed it with red Loctite. I also coated the inside of the case where you can see the studs, with Permatex to prevent leaking.
Otherwise, the case seemed fine, but then I noticed the counter-shaft steel sleeves were missing and we ordered some. Here’s a major point. There are good parts out there and there are shit parts. You can go to a distributor and find good shit and shit, so it’s on you to determine what’s good quality, and stick with it. I won’t mention names.
We ordered a new set of counter-shaft mounting sleeves, and I heated the case using a portable room heater. You can use an oven, which might stink up the house. I coated the sleeves with never-cease and found some appropriate punches to do the job, including one JIMS tool. In the process I annihilated my right thumb with my JIMS brass hammer, but after a few tender weeks survived. Regarding these sleeves be careful. One is specifically designed for the kicker side and one for the sprocket side.
Before I started final assembly. I heated the case and tapped them a few more times. Under ideal conditions you can feel when the sleeve bottoms.
With the sleeves in place, I studied the case for other missing elements. We didn’t have a drain plug or the fifth mounting stud. I checked the threads and took care of those from the tranny stash.
The next move included securing all the pieces for the main-shaft and John reached out to Ron, who sent us another box of goodies. The shaft he sent was over-heated and damaged. I had a shaft with a slight ding to some of the mounting threads, otherwise it was golden. I also had other shafts. They were longer, so I researched early 4-speed shafts. There are three or four leading from about 1962 to 1971. They started to get longer as soon as the first electric-start was introduced and a ring-gear added to the clutch basket.
1936-1965 Knuckle and Pan era. Kicker only: 11.750 inches
1965-1969 Pan to kidney Shovelhead with electric start: 12 inches
1970-1984 Cone motor Shovelhead to Evo with alternators and electric start: 12.5 inches
1985- Belt rear drive Evos: 13.750 inches
Some of Ron’s gears were dinged and I discovered I had some good replacements. My mainshaft could not be corrected, so I reached out to Lee Clemens, who operated Departure Bike Works for over 40 years. He scored me another mainshaft and started to coach me on the rebuild. Lee is also a Hamster. Neither of them were rich guys, but they were a part of the industry since the beginning.
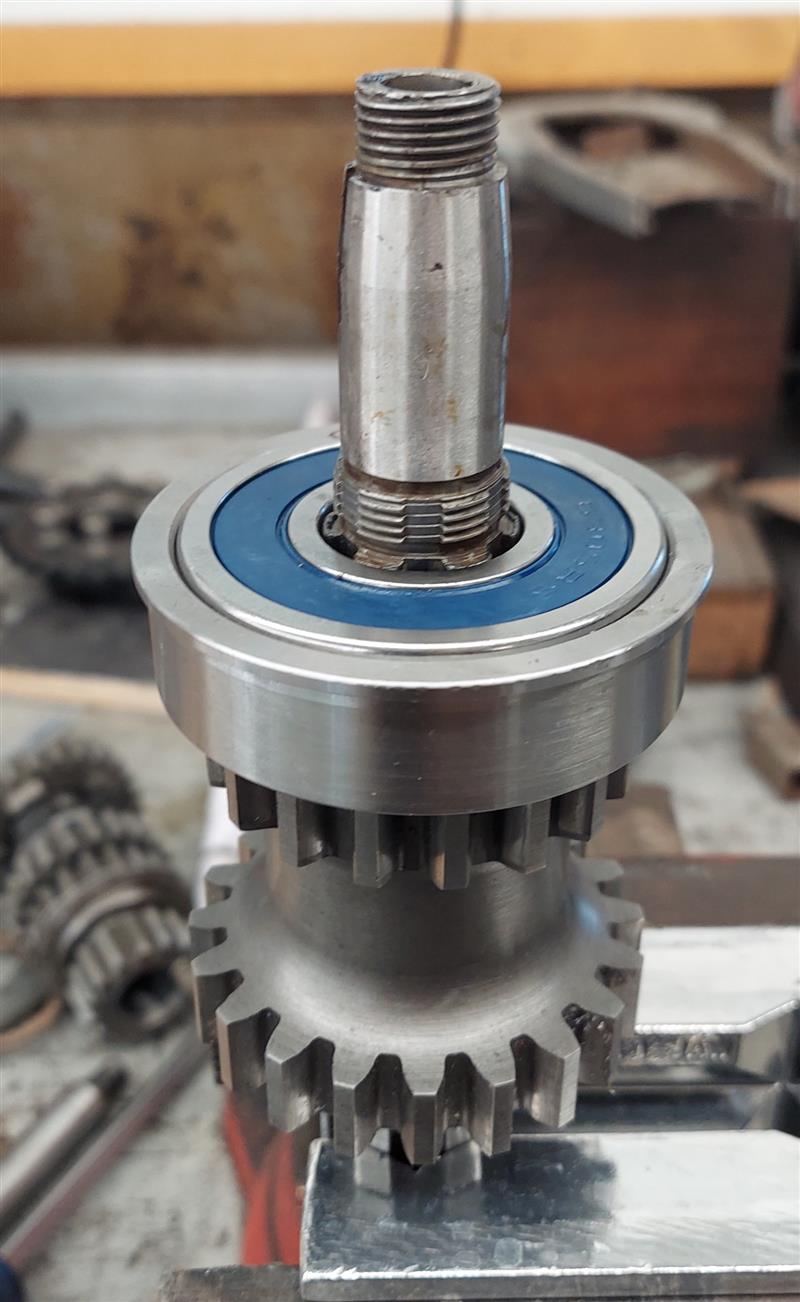
Ron sent us used main bearings, but not the sleeve. We ordered one and Frank recommended ordering a new main bearing, since they are cheap. It came as a sealed bearing, which I question.
We also ordered a new set of thin, long roller bearings. There are 88 bearings in total and the batch came with extras. Here’s where the quality issue came into play. Just because one distributor sells the bastards for half the price of another, doesn’t mean you want them.
Out of all the 4th gear choices we had, we picked the best one, cleaned it, cleaned and checked the case race, checked the thrust washer that goes on the inside, greased the bearings and stuck 44 around the gear race.
Frank slipped the gear, bearings and thrust washer up from the inside of the case through the case race and added the sleeve and the massive left-handed nut to hold everything in place and then he moved on.
I watched another film about tranny rebuilds and they installed the fourth gear, the sleeve, the cork washer and the seal. They checked for a .003 to .013-inch end play, and then they started to install the other gears and main-shaft.
I watched both films a couple of times and moved along with Frank’s process. He slipped his 4th gear with the thrust washer and bearings stuck with grease right into place, bada bing.
I wasn’t so lucky. They wouldn’t go. I could get them started from the outside of the case, but not from the inside. I struggled with it a few times and then took three bearings out and was able to install it. I added the three back in from the outside, no sweat. Then I added the sleeve, a couple of Shovelhead intake manifold O-rings and the left-handed nut to hold everything in place as Frank did.
Installing the mainshaft is a puzzle. Just slip the shaft through from the kicker side. About 2/3s the way in, you will add the third gear, thrust washer, keeper snap-ring, which needs to be worked up over the shaft teeth carefully and then the shift dog. The shift dog will have “High” stamped on one side. It goes towards the 4-speed gear. The dog will also help in pushing the snap ring into place evenly once you get it started.
When I first started this process, I had a snap-ring, but once in place, it seemed loose so we ordered a new one. I’m glad, but the new one was a chore to slide up over the teeth on the shaft and it’s critical not to stretch it. I joke that being a good mechanic is similar to being a surgeon. Sure, we’re grubby and covered in grease, but the operations are just as critical and delicate as surgery. I think sharp mechanics deserve way more respect.
With the snap-ring in place, you want to spin the shaft and with a punch, tap the snap-ring to insure it’s properly seated. Oh, and make sure you grease all the pieces as they slip together. I used assembly lube.
The shaft slipped into place. This is the stage where we needed a main-shaft bearing housing. We had a new one, but it was larger, most likely for a 5-speed. We ordered another one quick. We also considered Frank’s recommendation and purchased a new main-shaft sealed bearing. Ron sent a retaining plate. But it was dinged. I had another one in my stash.
Between Ron and I, we had enough pieces to finish off the main-shaft assembly after the ordered pieces arrived. Throughout this process, I checked every pressed in bushing for fitment.
I shifted to the countershaft and started to research all the parts. Once all the parts were located and sourced, some from Ron and some from my stash, we ordered a set of various sized thrust washers. I sensed an issue. That’s why I heated the case and punched the sleeves again using the JIMS tool.
I took care with checking this assembly several times without the new bearings in place, 22 in each end of the countershaft gear. Once I had all the pieces, I took it apart and added the grease to help the roller bearings remain in place during assembly.
This was an early case, but not super early, still it didn’t hold an electric start countershaft, or the oil cap on the end. All the necessary pieces came in the James gaskets seal kit. So, with the countershaft assembled with the roller bearings, lock rings, thrust washers, second gear and low gear in place with bushings, the entire assembly slipped into place, but there didn’t seem to be room for even the smallest thrust washer. With the additional sleeve taping I was able to install a small thrust washer and check for end-play .008 to .012 inch.
When I slipped the countershaft into place, I had to take notice of the slotted end on the kicker side. It had to line up with the thick steel washer shape.
Throughout the video Frank struggled with the transmission on a bench. Part of his problem included filming and access to what he did. I didn’t have that issue, so I took a long chunk of angle Iron, drilled a couple of holes and bada-bing, I had a transmission rebuild tool. It was long enough to allow several mounting positions in a vice.
With the shafts in place, I moved onto the mainshaft retaining plate. It’s a trick like a puzzle to fit with an oil guide tin piece. I cleaned and wire brushed the retaining screws. The plate goes into place against the bearing housing. I used blue Loctite and tightened the screws several times carefully. Then I installed the large coil spring and the mainshaft kicker gears.
There’s a ball bearing in one gear. I made sure it was free. Most of the shafts are held in place with flat washers with tabs to bend up to prevent the nuts from loosening. I bent the tabs slightly to make picking a tab and punching it into place easier. I torqued all the nuts before bending the shafts.
I found a clean kicker shaft and I had a good kicker gear with the plate riveted to it. Keep in mind that over the years there were different kick gear ratios. Make sure you have the right shit. You’ll know as soon as you try to install the kicker cover.
I checked the kicker shaft through the kicker cover for fitment. Ron sent a new set of brass bushings, but I only replaced the O-ring seal in the center. Keep in mind the large generally chromed return spring on the outside of the kicker cover must be positioned properly. Some of the shafts come with one notch for the kicker arm bolt. This shaft had four notches. At first, I thought I was golden, but not-so Kemosabe.
With everything in place, the spring wound way too tight. I needed to take it apart and shift the gear on the shaft 90 degrees.
Next, I installed the shifter forks after hunting down the dinky shaft retaining screw. The forks only go into the shift dogs one way, when shift drum pins and sleeves face the same direction toward the front of the motorcycle. With everything in place, I dropped the ratchet top, which was in Neutral into place and carefully removed it, several times. The shift forks should be in the center between gears.
I removed the shaft and carefully straightened the tabs and shifted the shims until both shift forks were close to center. Lee Clemens said, “It’s okay to set the tranny up so that the forks lean one thin shim to 2nd and 4th gears.”
With the shift forks adjusted and the kicker cover in place, I could lock the shafts from moving with both shift folks in gear. I went digging for the JIMS tool to replace the mainshaft seal. I couldn’t find it and called Kit Maira a longtime Easyriders staff member. At one time he borrowed some of my JIMS tools, and I couldn’t find the puller/installer.
I looked in my special tools drawer, but not the puller drawer. There it was. Here’s the issue. While trying to find the proper tool I attempted to install the mainshaft seal with another JIMS tool and it worked, but I looked up from my successful operation and discovered I had not installed the cork under it.
At the time, I was consulting with Lee Clemens and he recommended I Permatex the area before installing the cork and then the seal. In order to remove the seal, I had to knock holes in it and use sheet metal screws to pull it out. Frank also recommended wiping the outside of the seal with Permatex to prevent leaking around the seal.
I found the JIMS tool, installed the screws, pulled the old seal, Permatexed the inside of the area around the sleeve, installed the cork, which was also coated with Permatex and used the JIMS tool to install the seal after I added a coat of Permatex coating the outside.
That left the ratchet top. I didn’t completely disassemble it. I took out the spring-loaded shifter paul, checked it, regreased it and replaced it. I took the cover off the ratchet case and inspected the springs, which are generally the issue with shifting. If a spring breaks, shifting goes to hell. I checked the alignment and greased everything.
I noticed a stud bolted into the ratchet top and wondered WTF? It must have been a neutral indicator for cop bikes at one time or electric-start bikes. I tried like hell to find another alternative but could not find a matching fine thread, short bolt.
I cleaned the gasket surface, found a set of fasteners. Note, that one is a vent hole. Make sure it aligns with a threaded hole through the case to the interior for proper venting.
I installed a greased gasket and the ratchet top. It shifted like a dream. I dug around for a kicker arm and found one offset and one straight, John went for the offset one, but we might reconsider. Also, I noticed the sleeve for the clutch arm, which was cast into the case was loose.
I tested green Loctite in this situation. I was told green was for studs and permanent stuff. John researched and discovered green is for situations when you can’t reach the threads. You can drip this around the opening and It will seep into the threads tighten and seal. Ya got me.
During final assembly I studied his clutch actuating system. This was a mousetrap bike with the clutch rod that extends past the trans. I knew we would incorporate and clutch eliminator bracket, which would eliminate the use of at mousetrap. We needed a shorter clutch rod and it had to be short for clearance under the oil tank. I had one.
One final note, the chain sprocket. John wanted to go with a stock 22-tooth configuration. I had a bunch of them. Some were offset for wider tires. Some were flat and seemed to rub against the case and some were just slightly dished on the inside to clear the case but run the sprocket tight to the transmission. I had a 24-tooth and discovered I also had and 22.
The trans was rebuilt and complete when I returned it to John’s Deadwood Garage. Bada-bing
–Bandit
Sources:
JIMS Machine
Ron Harvey’s Classic Motorcycles
Alaska
Lowbrow
5-Ball Racing
Baker