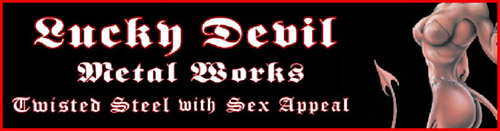
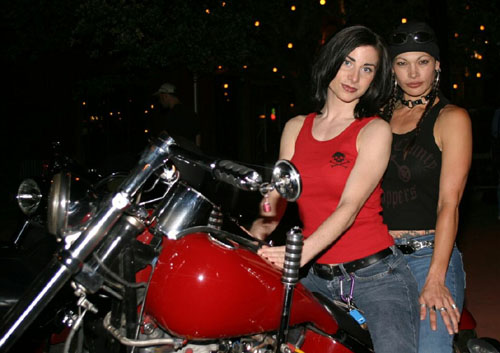
I returned, this time, from my hometown of Houston. Kent at Lucky Devil Metal Works informed me earlier in the week that Bradley Da Polisher & Darryl the Photographer from Dallas were planning on making a run to Lucky Devil's to see about having some work done. Sounded like as good a reason to pay a visit, and of course there was your e-mail, “Oh yeah, She's hot. Keep me posted. If you see the lucky Devil guys, do a tech with their stuff.”
Here's the tech: Don't try this at home. How's that boss?
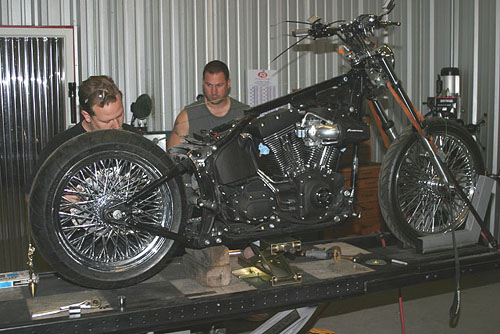
My brother & I arrived that morning and were concerned, only Frank's Springer was up on the lift, the one from the Dallas weekend shoot and a 2002 Night Train. Hell I should have known when I saw a stock bike sitting on the frame table that it would be feeling the cold steel teeth of a Lucky Devil rip saw in the near future. I wasn't disappointed. Kent started by manufacturing his own rear wheel axle spacers to ensure the rear wheel was centered, “You can't trust that factory shit,” he said firing up his lathe.
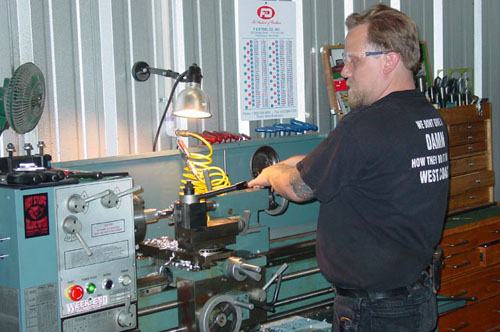
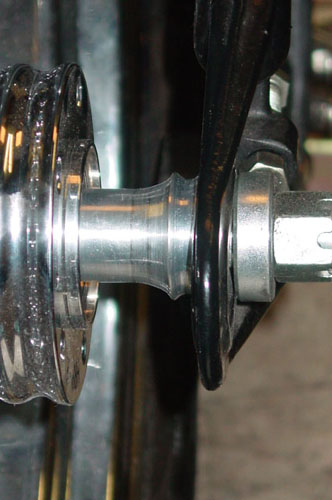
Once spacers were handled the front end was removed. The bike was secured and then it happened! While it appears fairly painless, it takes most folks a while before they're convinced and confident enought toallow the Devil to carve at their pride and joy with a high speed cut-off saws. After the removal of the obscene stock limbs from the frame, the front end was secured to the remaining neck (to retain stock numbers) and clamp and extended tubes were carefully installed. The Night Train would receive new 14-over centerless ground fork tubes.
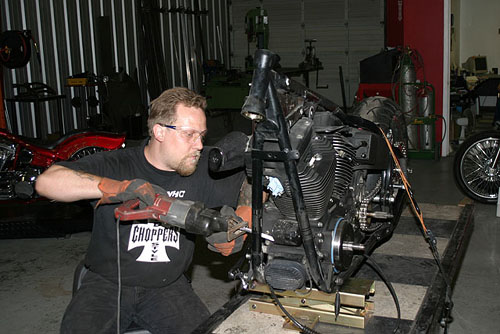
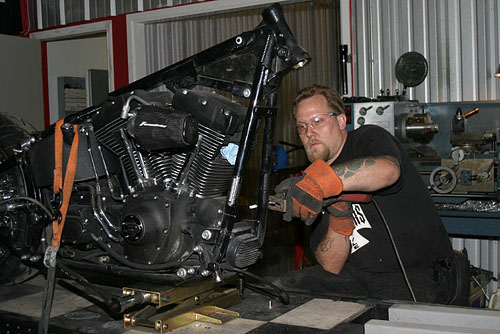
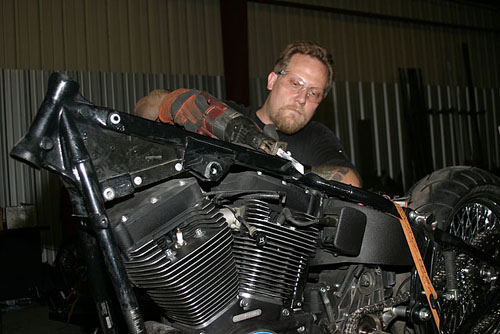

Still additional complex and highly mathematical formulas were evaluated to decide the correct amount of metal needed to manufacture the new single tube front frame section. Along with new stretched square tubing backbone (to match the stock Softail backbone) and the single downtube, precision ergonomic testing took place. (Really Ol' One Eye just slid the chassis back until he experienced the rake and trail that fit the 14-over tubes based on years of experience, ground clearance and handling priorities). In the final welded analysis it ended with 38 degrees of rake, but I'm not sure of the final stretch configuration. Between siering cut-off saws, weld splatter and the whirling lathe, the crew didn't have time to answer my query. I tried to grab a tape measure and collect my own data, but a grinding wheel spun maliciously near my sweating temple. I backed off.
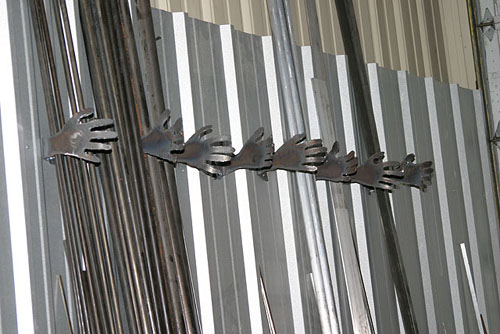
Then Bradley arrived with another project bike, which will fill a future Lucky Devil segment. It will be worth the wait, though.
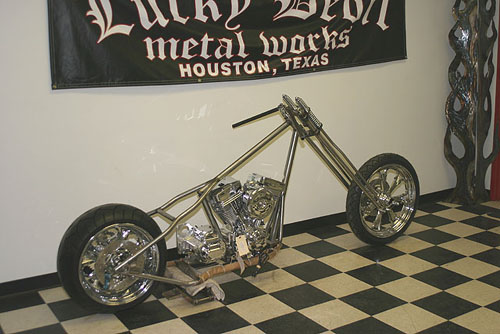
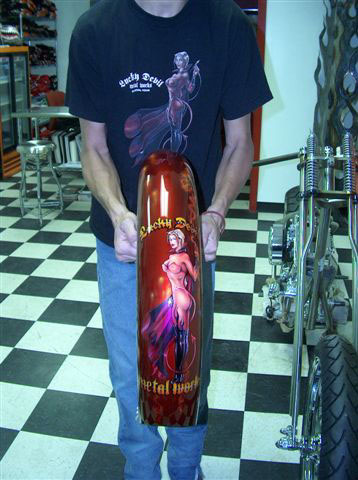
I was also invited by Bradley, Da Polisher's, to write a story on his shop, Hands Off Polishing and Chrome. Watch for it in the future too, as soon as we can schedule some time. By the way the prefix for Bradley's shop is 972 not 214.
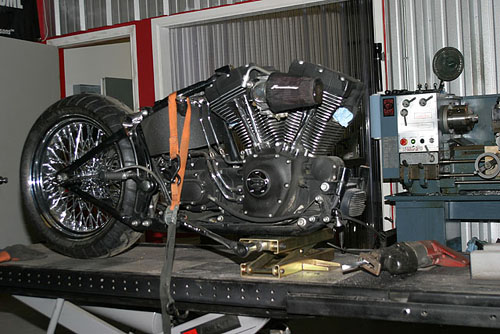
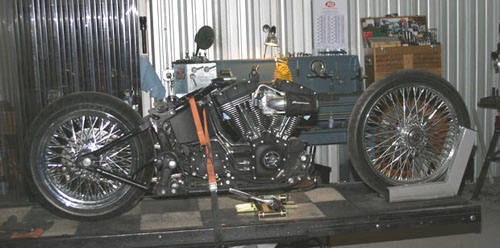
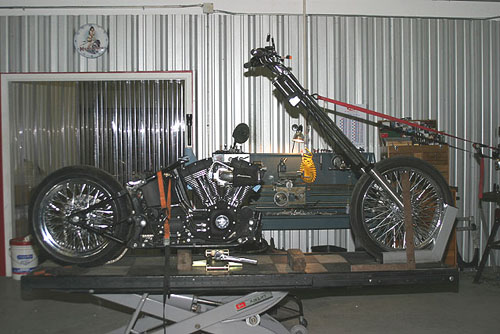
Kent uses 1 1/4-inch Seamless Mechanical Tubing. He Tig welds the tubing to the stock frame. Kent uses hollow plugs the same wall thickness as the tubing instead of a solid plugs like some builders use. This allows for the two pieces to break down at the same temperature as they are welded, whereas solid plugs require more heat. The hollow plug also allows for wiring to run through these areas for concealment. “I'm not want saying solid plugs are wrong,” Kent said. “This is just the process I'm comfortable with.”
The rake is 38 degrees, trail is 6.5 inches, the backbone is 7-inches over stock, with 10-inch over on the front single tube for a 14-inch over front end.
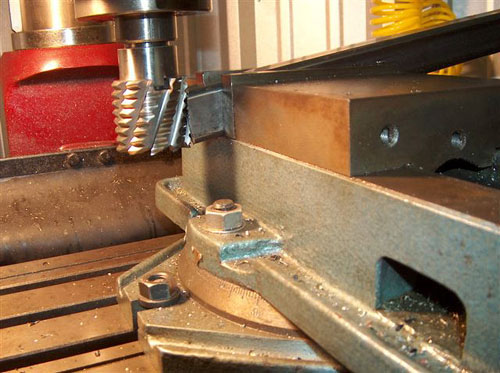
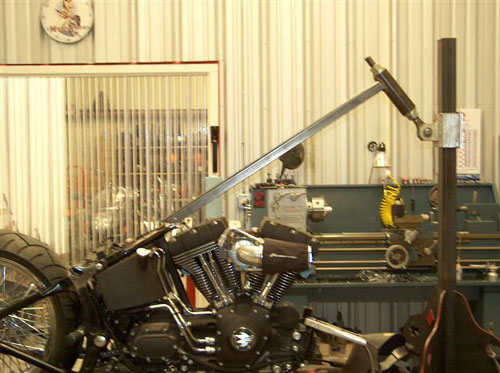
No Kent didn't actually eyeball the fit. This arm holds the neck precisely in place while the frame members are cut then welded.
Spanky, a good friend of Lucky Devils, wandered in and out of the shop sharing new Lucky Devil rotor designs with Kent. He showed me pictures of the one he's developing for Kent's chopper, and it kicks ass!
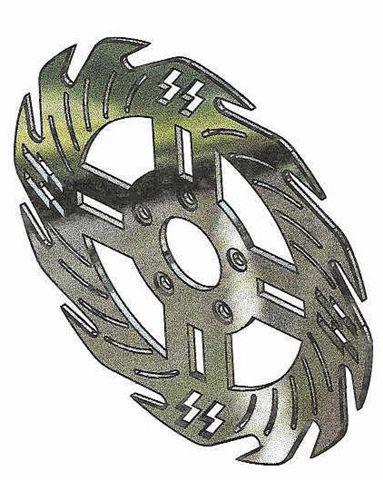
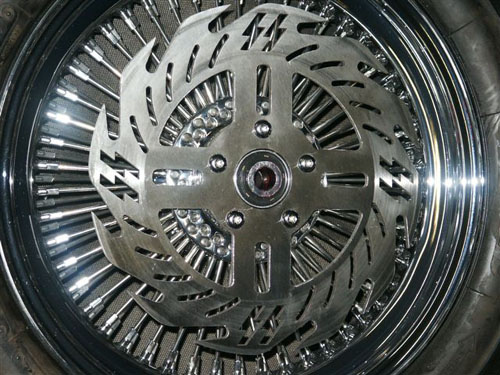
“The rotor machining process was a learning experience, Kent said, “I guess being a mechanical engineer comes in handy.” I witnessed Spanky's computer CAD drawing for the shop rotor, impressive. He's the engineer.
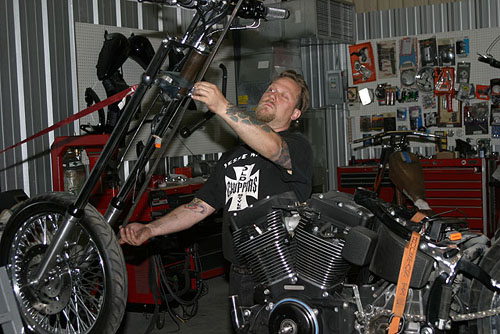
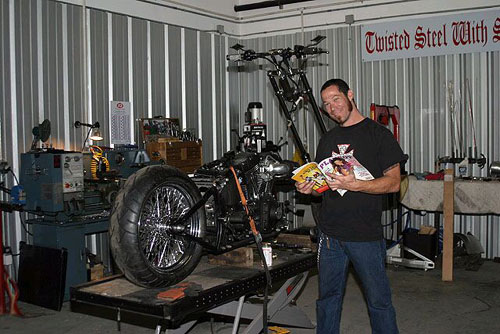
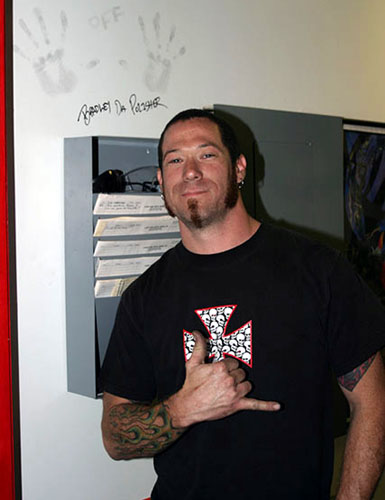
After Kent mocked up the Night Train for Monday morning final welding and assembly. It was time for happy hour and our favorite charity work, clothing poor girls. Kent, Spanky, Bradley and I hauled ass into the humid Houston night. The first place we tested didn't cut it. The hot young ladies were merely beverage runners. As you know waitresses don't lack threads. So we decided to try a different establishment with much better results.
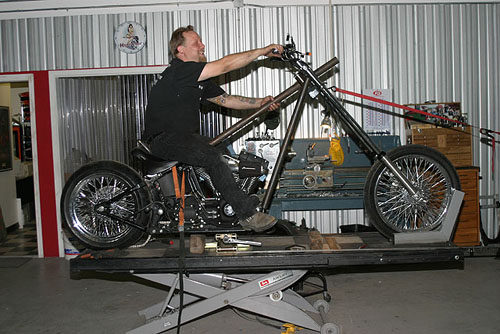
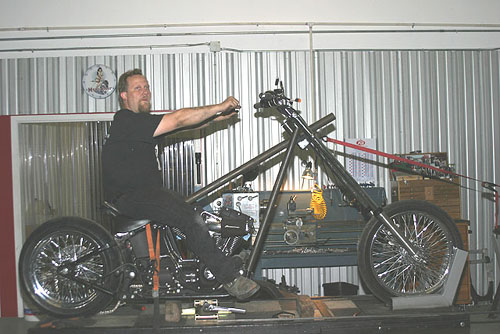
During the evening, at one of the many corporate meetings with our lovely assistants, we decided to form a “Not For Profit” organization to help in our quest to aid these young women, in their search for apparel. Donations are currently being accepted.
I'm hoping the Lovely Ms. Nicci (above) calls me this morning. She's off today, can we say “Sick Time!”
Till the next adventure,
Rigid Frame Richard
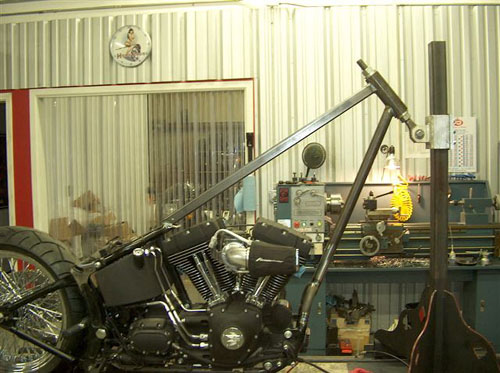
Just received these shots of the Night Train coming together,
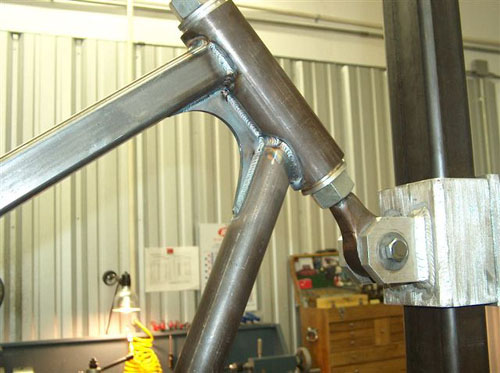
Here's a close-up of the neck after Kent TIG welded this puppy carefully into place.
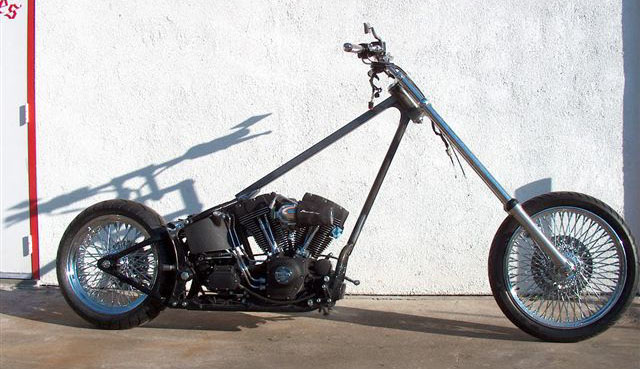
Ah, up on its wheels. This sucker has a new life as a monster chopper. Can't wait to see it put together.
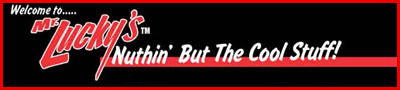