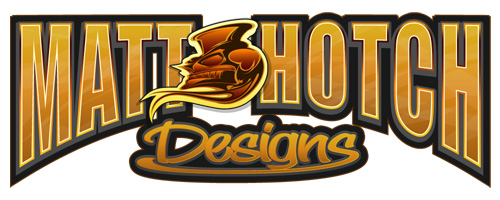
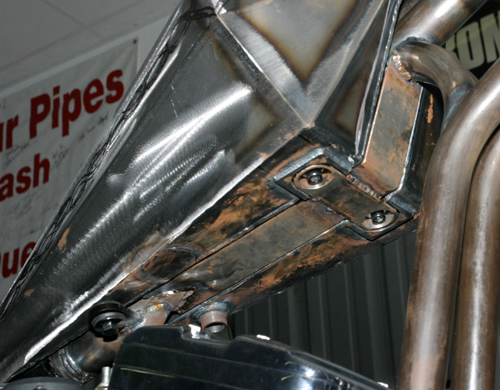
I have been using gas caps and kickstands from Mat Hotch Designs for quite some time, even before Lucky Devil was up and running so when the news came around about their new flush crossovers I was already interested to see them and give them a try. I always jump at the chance to chop up a tank and whip out the welding machine so there was no time wasted and a set was ordered, along with a pop up gas cap for a sporty chop in the shop at the time.
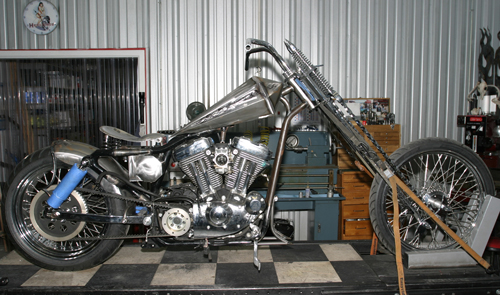
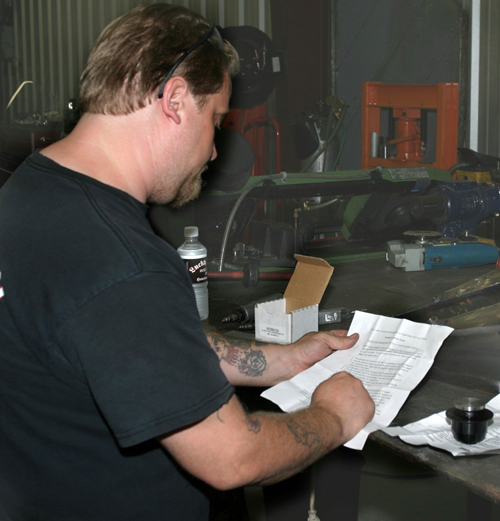
Once the gear came in the box was butchered and contents tossed out on the table for inspection. Every time I install a new product I check out the instructions, not that I always follow them, but I look them over just the same. After I got the tank set up and finished welding out the tank mounts and found a good location to install the insert. Before the tank was cut it was mocked up on the tank mounts to make sure the selected location allowed me to miss the backbone.
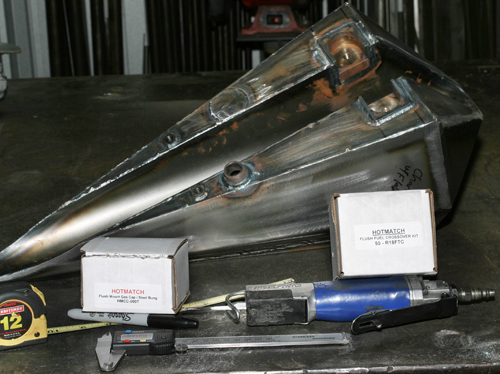
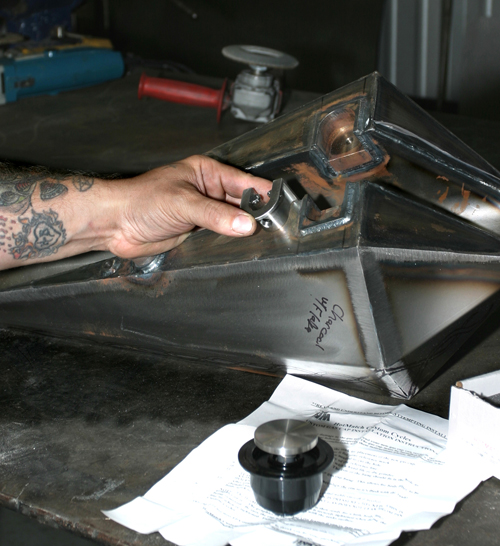
To get things started I used a square off the tank tunnel, along with a steel rule and scribe, to make a mark from one side of the tank to the other to be sure the two sides lined up properly. From there I used the Matt Hotch component to mark the hole location by placing it in position on the surface of the tank and tracing around the part with a marker.
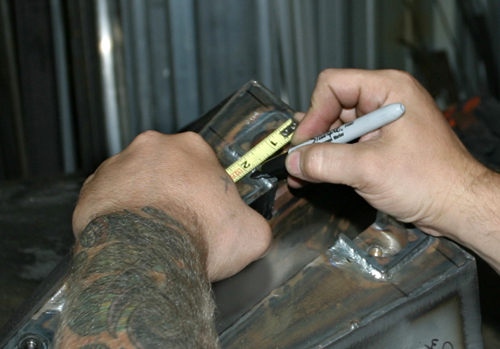
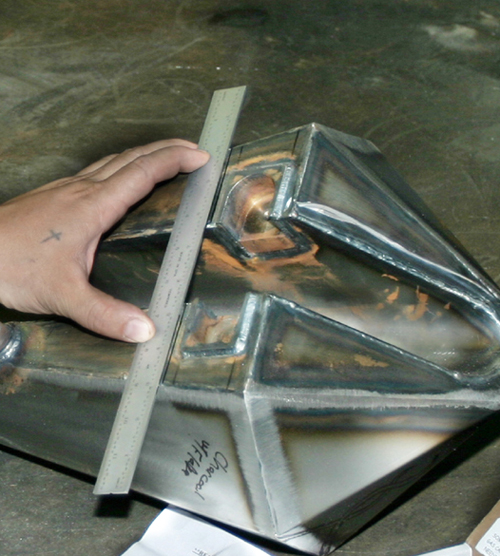
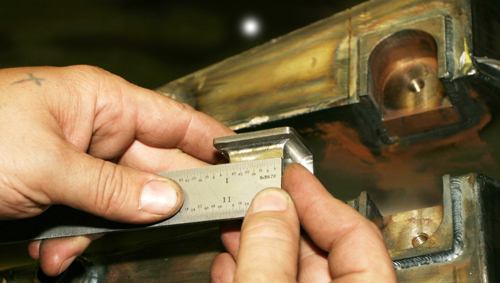
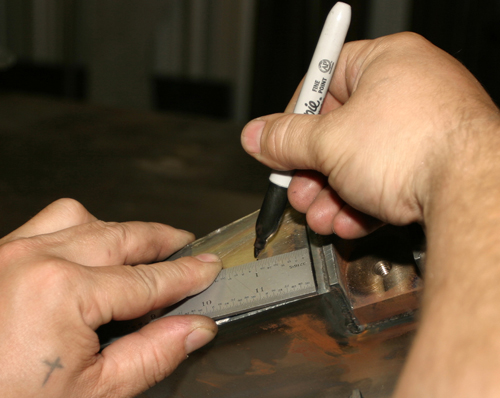
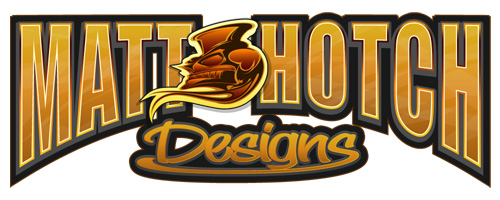
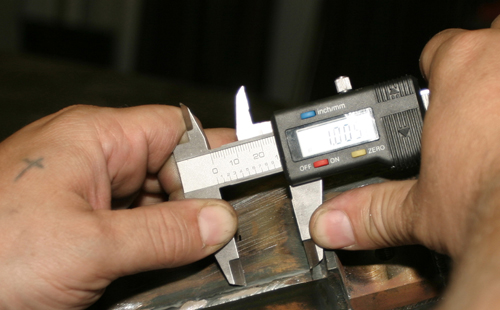
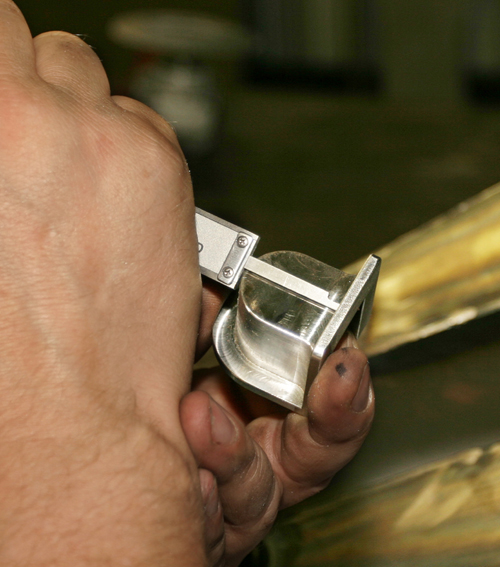
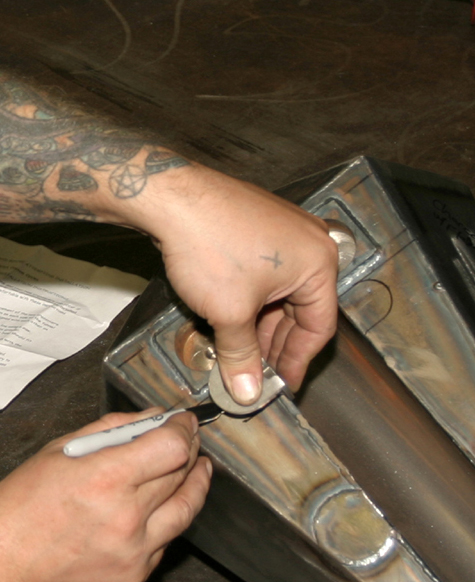
To get the hole started I used a die grinder with a cut off wheel to cut the straight part of the cut outs and an air saw to cut out the rest. The instructions suggested you start by making the holes too small and open them up to fit the part. This is a key building philosophy for the future.
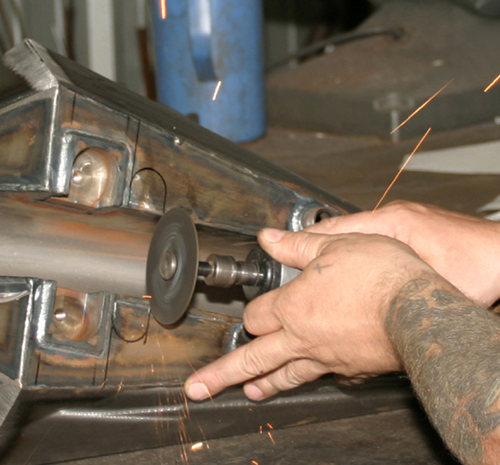
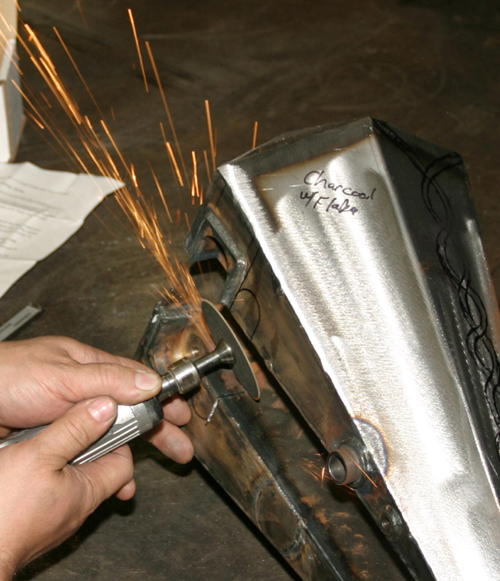
A rotary file mounted in a die grinder works great to slice in, nice and tight, and get ready for the rod, welding rod that is. It’s a good idea to make sure the two inserts stayed lined up on both sides before you get the welding machine cranked up.
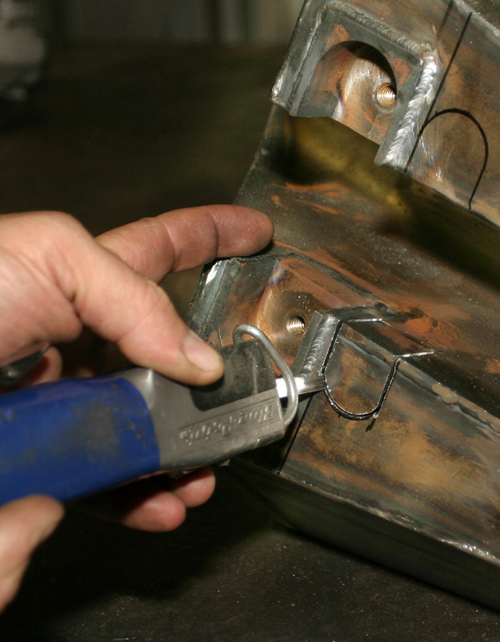
Before you just start going to town you may want to tack the inserts in place in a few spots to keep the part from moving during the welding process. I also recommend that you take the time to mock up the tank back on the bike and test fit the line to be sure you are happy with it’s placement before welding it in permanently.
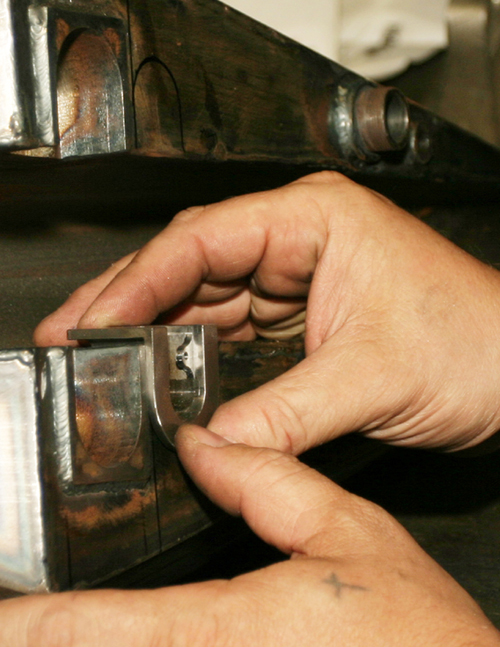
For this kind of project my first choice is a TIG machine but if a guy is good enough with a MIG welder, it can be handled that way. I will say that TIG welding is my preferred process for just about everything! If you are stuck with a MIG machine using anti-spatter spray might be a good idea with a project like this. If you don’t already know this spray keeps the little weld bb’s from sticking to the tank, or whatever part you are working on. The broke dick version is non-stick cooking spray, and if you rob it from your sweetie’s kitchen, I hope you are smart enough to put it back!
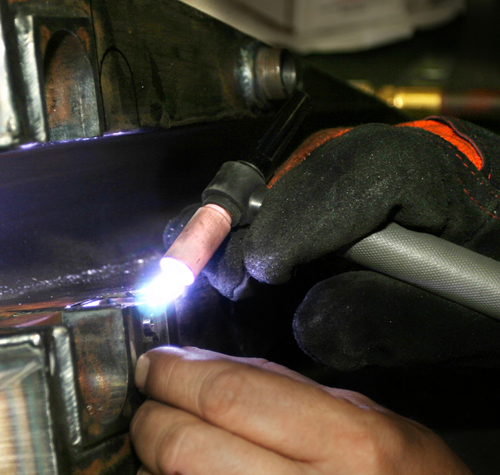
Editor’s note: I just experienced the difference between MIG and TIG welding on tanks. TIG is a much more controlled welding procedure. I MIG welded on my Bonneville tank and it leaks where I welded it. The welds weren’t bad and you can’t see the pinholes, but the bastards leak under pressure and fixing them is a problem because of imperfections in the welds.–Bandit
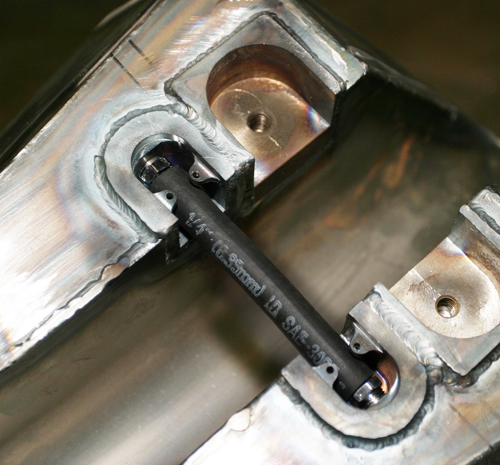
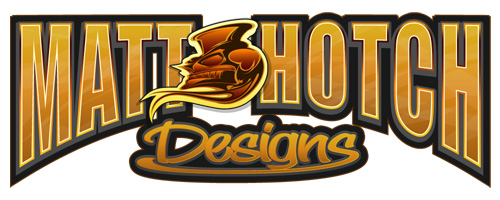
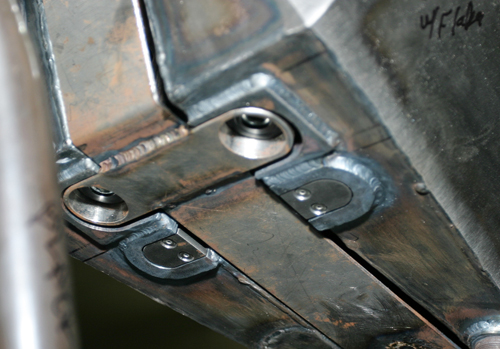
Once you have welded the inserts into the tank you need to pressure test the tank to make sure there are no leaks before you start pissing paint on it. For this job it is a good idea to use a regulator to reduce the amount of pressure to an acceptable level.
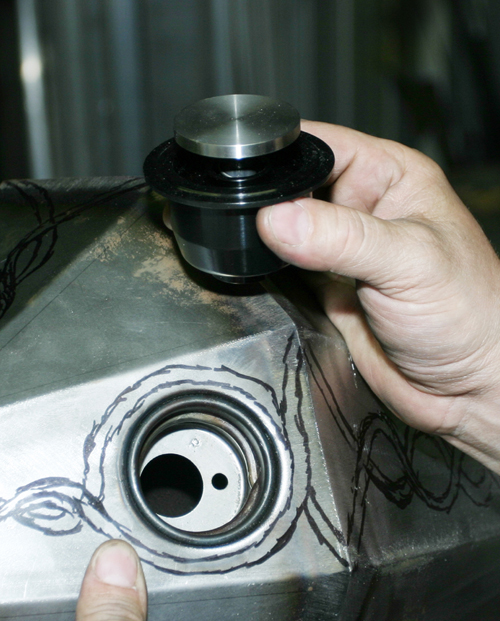
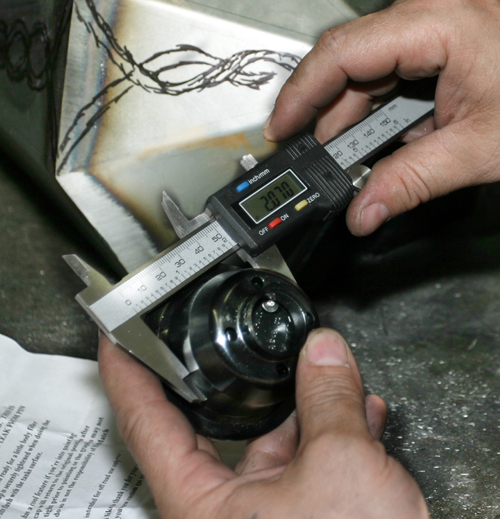
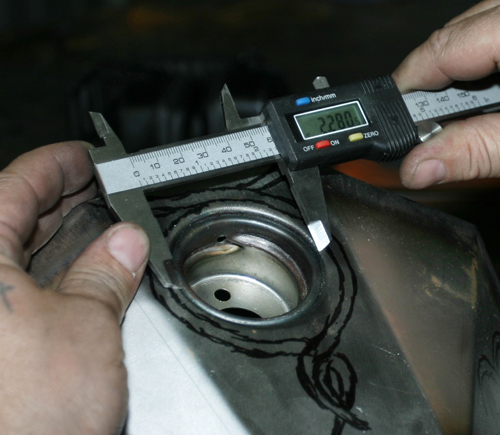
If you have MIG welded the parts in and find a leak, you will most likely need to grind out the area around the leak and re weld that spot and test again. With a TIG process you will be able to re-weld the spot without grinding.
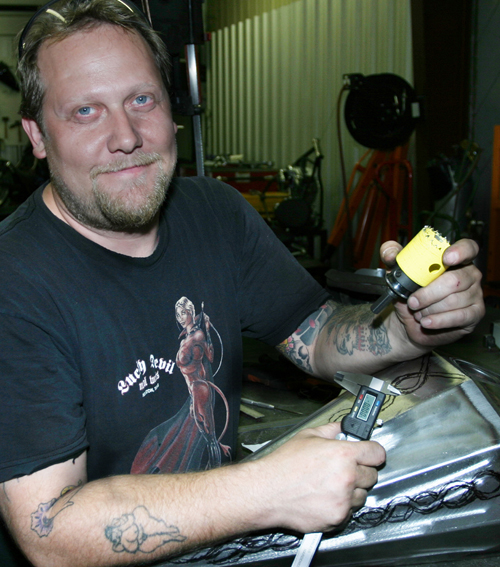
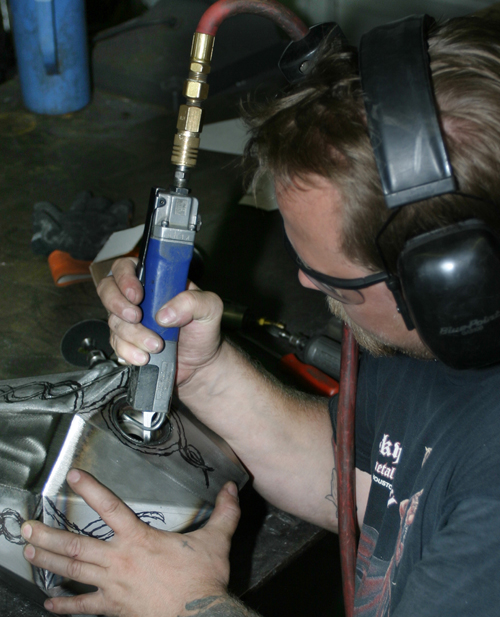
For the gas cap install I went right to work. It has been a long time since I read the instructions for this product. If you are working with a tank that doesn’t have a gas cap fitting, you can mount it just about anywhere on the highest part of the tank. Once a location is marked you can just grab a hole saw and go to work. Just like with the crossovers it is a good idea to start out with a little smaller hole than you need and open it up with a rotary file. If there is a gas cap fitting in the tank already, I start with a drill bit and cut around the edge of the fitting using an air saw.
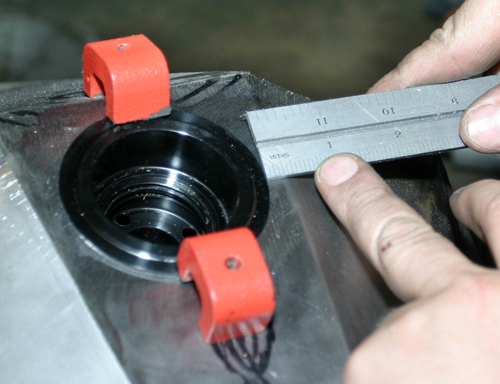
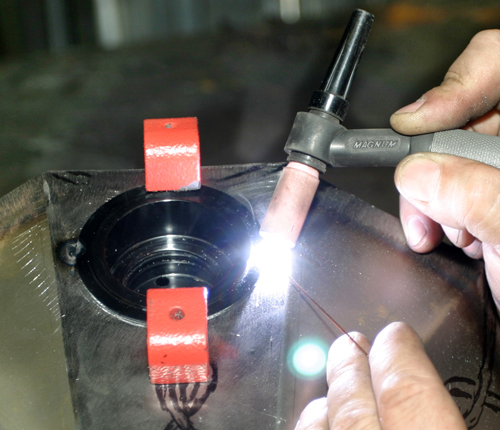
Once you have a comfortable fit and you make sure you are in the desired location, you are ready to tack the new fitting in place. With this tank I used a steel ruler to make sure it was in the center of the tank before I kicked the TIG welder on. After the cap fitting was tacked in and welded out I started to pressure test the tank again. I always like to test the tank at each stage of the job, so I don’t find myself chasing too many leaks at once.
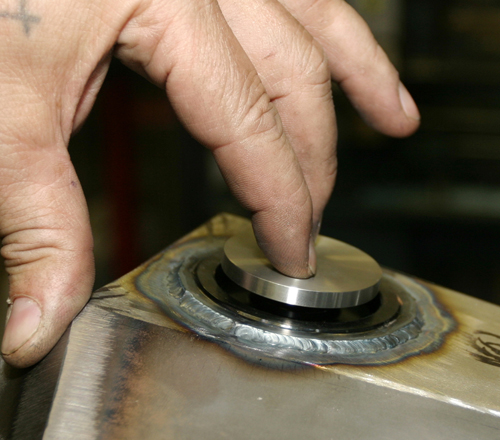
With the cap on the top side of the tank it is easy to feel like it’s not that big of a deal, but if there is even just a tiny little pinhole the vapor from the gas will cause the paint to lift and bubble away from the tank. Needless to say pressure testing is a very important part of the installation process! Wasting a $3000 paint job is a shame.
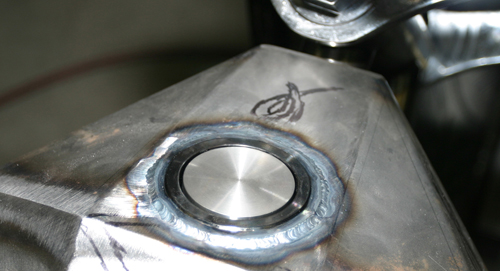
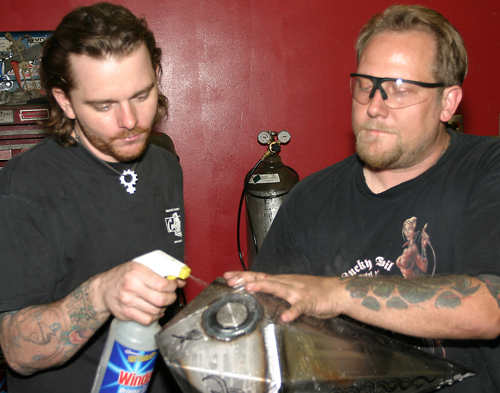
–The Devil
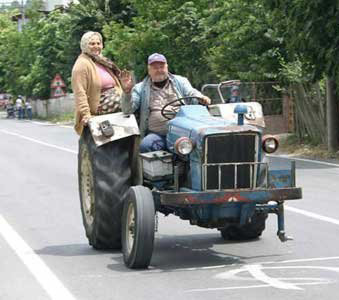