It’s May 23, 2011, about two months before we roll out to the Badlands. Every year takes on a different character. It’s sorta like the new kid on the block. We never know exactly the direction this kid it going to take. Sometimes we can guide him, and sometimes he takes the lead, good or bad. So this year, we seem to be facing a kid who has a pocket full of delaying tactics, and a waiting year seems to be unfolding before me.
I’m still waiting for the Harbor Department to build the park across the street. The ground breaking has been delayed from June until November. Damn. We are still waiting for the city to finish widening Harry Bridges Boulevard. It runs along the south side of the building. The completion date was recently pushed back from January 2012 to April 2012. And I’m finally wrapping up my Motorbooks Terry the Tramp book project. It was supposed to be released in June, now it’s November, but it’s already for sale on Amazon. And I’m still waiting on our City Council person to decide on my building grant.
My son asked the other day, “Have you made arrangements for lodging in Sturgis?” How can I make arrangements? I don’t have frames, front ends, handlebars, controls, you name it. If I was a tad closer on these bikes, I’d step up. But I can’t just yet. Ya never know. There has been progress, though. Hell, I’m still waiting for Frank to come up with his Mudflap girl mascot illustration.
Last week, I picked up my H-D Evo engine from Bennett’s performance. Let me take you through the process we put this bone stock puppy through to pump up the performance without messing with reliability.
I discovered two prime safety sources for keeping Evo engines alive. First, proper warm-up is essential for Evolution engines, because all the major components are aluminum and move around a lot during warm-up. That’s why the barrel gaskets tend to leak. Let ’em warm up slow and they love it. Number 2 relates to the warm-up period, new gaskets. Use only the finest H-D or Cometic gaskets on your Evo engine and it will save tons of headaches in the future.
We took the heads to Branch O’Keefe. Jerry Branch was recently inducted into the Trailblazers Hall of Fame for his performance technology over 40 years in the motorcycle business. He is currently working with Dan Gurney on very fast cars.
Jerry sold his shop to long-time former employee John O’Keefe, and John has made a living keeping the Branch intake performance technology alive. They strip the heads completely, weld in and reshape the combustion chamber to allow for better flow, new larger valves, a slightly higher compression ratio (from 8.5:1 to 8.9.1), and 78cc flow from 84 stock. They also shave .050 off the head gasket surface.
They reshaped the heads through years of trial and error to allow for larger, better flowing valves, in the optimum position, since the stock heads didn’t burn all the fuel, impeding efficiency in the factory engines. The area around the valves became smaller, but they were able to speed up the velocity of the air passing through. In a smaller area, they were able to add more space around the valve.
John squeezed in a 1.94-inch intake into the combustion chamber, compared to the 1.85-inch stock valve. They were able to design in a larger valve with more functioning space around it. The crest in each port allows for more valve guide support and still enhances the port flow.
The exhaust valves are enlarged slightly from 1.608 to 1.612. The Branch team rebuilds heads in three performance levels, from mild for stock displacement engines to ultra wild with higher compression pistons.
John O’Keefe replaced the valve guides with bronze magnesium components. “I like these work hardened valves and guides because I can run a much tighter valve stem-to-guide tolerance,” John said. The tighter tolerance affords heat dissipation from the valve through the guide. The enhanced grain structure in the guides acts as a heat sync pulling blistering temps off the valves. All these elements make for a longer lasting valve train.
These amazing aerodynamic guides come with Vito seals built into the structure of the guides. They also run a thicker, more robust exhaust guide for additional heat dissipation.
For my heads, the Branch team installed one-piece stainless valves with chromed stems and stellite tops where the valve meets the rocker for additional hardened strength.
For twin cams and dressers, John recommends black nitrate valves with a Teflon coating.
“I use the stainless valves in Evos because the guys don’t lug them,” John said.
Their valve seats are nickel chromium and capable of running valves up to 2 inches. The biggest valve you can put on a stock seat is 1.90. The Branch O’Keefe seats are machined with an interference fit of .007-inch so they will never rattle in the heads or even fall out. Factory seats are only .0025-.003 larger than the hole in the head. He heats the heads to 300 degrees, and freezes the seats before assembly. The nickel chromium seat material will take any unleaded fuel and won’t pit.
Each valve seat is cut at 45-60-30 degrees, three angles. With porting, it is the equivalent to a 5-6-angle valve job. Each valve is ground to 45 degrees, and John uses a special carbide-honing bit to ream the guides. It is designed with a reverse spiral so it runs clockwise and it is set to slip fully into the guide before it begins cutting, for an absolute straight ream. Each bit costs over $200.
John and the Branch team hand-lap each head. “We can modify heads for any performance application,” John said. “It is no longer a one-size-fits-all world.”
The master in the clean room is Paul, a former Honda race tuner. “He’s great at tech support,” John said and I could tell he wanted to talk to the milling machine more than me.
“We like to find out what a guy rides, and how he rides,” Paul said. “It helps to find out what they have in their engine, what kind of intake, and carb.” Sometimes, they polish intakes and Paul can make recommendations on carbs and carb tuning.
Even their valve springs are top of the line. “We have a five-year track record,” John said, “of no failures or pressure drop.” They are shot-peened, stress-relieved and they test at 180 on the seat. “Some springs drop 20-30 pounds of pressure in a race bike after just 50 dyno pulls.” Their springs are refined and capable of .675 cam lift. He uses only chrome moly collars and retainers.
What the Branch O’Keefe crew does with heads is truly amazing. Their shop handles all the final assembly for STD heads. It’s the best bang for the buck for reliable performance. With the heads refined and completed, I headed back to Bennett’s to button up my engine.
We ordered a Cometic top end gasket kit from Biker’s Choice, the Andrews cam and adjustable pushrods from Branch O’Keefe, and a JIMS replacement breather gear with enhanced breather slot.
Eric’s first move was to discuss his Signal Hillbillies band’s gig at the Roland Sand’s grand opening gig Friday night. When Roland asked for a CD, Eric said, “We don’t have one.”
“How will I know you’re any good?” Roland asked.
“Am I going to step into the center stage in a room fulla my peers and make an ass of myself?” Eric retorted.
I was there and the Hillbillies rocked the joint. If we have a Pre-Love Ride party this year, they will be the headliners.
Then Eric grabbed his micrometers and measured the length of the cams. The stock cam was 3.080 inches to the Andrews cam at 3.020. So Eric dug out a .065 shim. He also had an S&S breather shim kit to use for spacing. He put assembly lube on all the bearing surfaces and slipped all the components into place in the cam case. Assembly lube is critical in any engine that hasn’t run. The time between first turning over and fully lubricated is critical to bearing surfaces.
“The manuals are whacky,” said Eric. “The H-D Evo manual calls for .010-.050 cam end play tolerance.” In comparison, the Shovelhead manual requires .004-.008 endplay.
Eric generally sets endplay from .006 to .012. He shoots for .010 endplay for the breather gear, then uses blue Loctite on the cam chest fasteners and snugs them to 120 inch-pounds of torque.
The Cometic head gaskets are MLS, or multi-layered with steel. Eric applied anti-seize under the headbolt head lip, and lightly on the threads to prevent galling and rust, since some cylinders allow breathing around the head bolts. This can lead to condensation collecting around bare metal and cause corrosion. The anti-seize affords the mechanic a more accurate torque setting. “A little goes a long way,” Eric said. “Always use anti-seize on sparkplugs.”
Eric tightened the headbolts in a different pattern than stock manuals call for, but one recommended by S&S. He started with a square/crossing pattern. If you’re facing the cone of the engine, Eric started with the close in, right headbolt and tightened it to 20 foot-pounds of torque, followed by the left fastener, then crossed to the right fastener in the back, and then the left. At 8 foot-pound intervals he worked up to 42 foot-pounds of torque. “Ya gotta bring them down gradually,” Eric said.
Here’s a sidebar of interest. You can imagine the pressure that builds up in the bottom end as the pistons slam toward bottom dead center. In the past, that pressure pushed air and oil into the gear case and vent cavity. That cavity below the breather gear was removed in 1996 and venting was handled through the top end, breathing into the air cleaner. Imagine if your engine sat for a while and oil sumped into the bottom end. It would fill your air cleaner with oil.
“S&S builds their cases with the cavity,” Eric said, “so the engine can breathe out the top or the bottom. You can modify the rocker boxes, and bore out the vent holes to ½ inch and replace the rocker boxes with later model units. I like the notion of more venting for a smoother running, less stressed engine.”
Eric used the stock rocker-arm rubberized-coated steel gasket and tightened the 5/16-inch fasteners down to 18-22 foot-pounds of torque, and the ¼-20 fasteners to 120 inch-pounds.
The Andrews adjustable lifters were installed with long units in the exhaust with the covers, and the short ones with the intake. Eric installed the intake pushrods first and just took up the lash. With the rear intake at its top position, he adjusted the front out 3.5 turns or 21 flats. He counted them out loud, so he didn’t lose his count. Then he let the engine bleed down and handled the rear intake adjustment.
“Solids are great for high performance, where you need the maximum out of each cam lobe,” Eric said.
Hydraulics have a cushion built in for easy running, less adjustment and less noise, but you lose some cam capacity. Eric noted that you need to be aware of the thread size on adjustable pushrods. Make sure to read the instruction, so you don’t over adjust your valves because of coarse threads.
We buttoned up the new stock Evo engine, but I will pull the ignition module and replace it with a Compu-Fire one-piece ignition module, and I’ll be good to go.
I have a Trock-modified CV carb for my bike and a 42 mm Mikuni for Frank’s with a Roger Goldhammer shapely air cleaner.
Okay, I made a mad run out to Spitfire with two Custom Chrome gas tanks. Both had too-narrow tunnels, but Paul’s associate told me that replacing the tunnels was not a problem. With my optimistic approach, I was sorta hoping to have my frames by the end of this week, but I believe it will take another week.
My 3-inch open primary arrived yesterday from BDL, and my risers arrived from Custom Cycle Engineering, along with their FXR swingarm axle and bearings. I still need to find the rubbermounts and diamond plates for the frame.
I also ordered Wire Plus wiring systems for both bikes. I’m the outlaw so I won’t run turn signals, but Frank will. And I need two stock Evo intake manifolds.
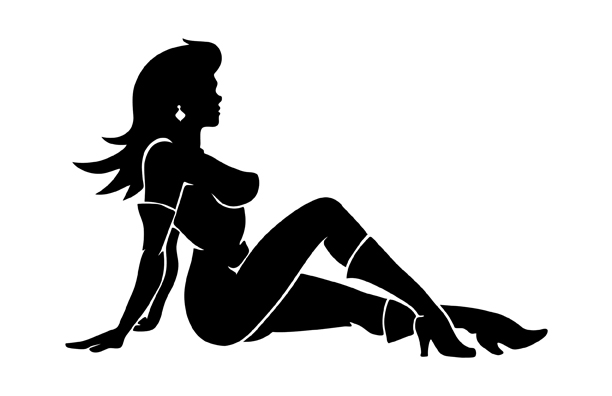
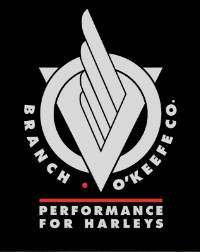
Biker’s Choice
JIMS
Spitfire
D&D
Bubs
Harley-Davidson
Rivera Primo Inc.
Belt Drive Unlimited
Metal Sport Wheels