Sportster Performance Solutions
By Bandit |
Many of us madmen started with Sportsters. Not long ago, there wasn’t much a guy could do with his Sportster to make it sing, but now there is. So we went after a complete list of parts and recommendations for a strong, better handling Sportster. We started with Bartels’ Harley-Davidson. Bartels’ is a family organization of performance-minded folk who believe and live by performance and speed. The Bartels family has been competing in 883 and Buell Lightening racing series, for nigh on 75 years, not really, but they’ve been at it for a couple of decades. Bill, the father and owner of the Marina Del Rey dealership, still races stock cars every weekend. Scott and Bill’s wife, Merle, run Bartels’ Performance Products. Ron Bartels is the head of the service department where we recently watched the transformation of an 883 Sportster belonging to Brenda Fox, a hard-riding woman. Using her bike as a base, we spoke to Ron first then to his brother Scott. We’re talking street performance here. No stroker kits or tearing into the bottom end. Keep in mind the kind of riding you like to do. Stoplight drag racing, in the hills flying, or all-out high speed freeway endurance runs. I’ll touch on them all. Check it out: | ||
![]() | Heads: You have a couple of choices here. You can have your heads flowed and shaved for higher compression or you can replace them with Buell heads and barrels. If you have an 883 don’t hesitate to go with a Factory 1200 kit, but you’ll feel real potential if you have the heads messed with. For an 883 you need to have the valves replaced with 1200 valves and the heads shaved for higher compression. | |
Cylinders: The way to go without big bore situations is with the Factory 1200 kit, or Buell heads and cylinders. In this case Buell cylinders and pistons were added to shaved and ported heads to create a 10;1 compression situation. | ![]() ![]() | |
![]() | Cams: Brenda’s bike was goosed with Bartels’ Performance 140 cams. | |
Intake Manifold: Bartels makes a flowed performance manifold that is something to consider if you’re upgrading your heads and carb. | ![]() | |
Carburation: Mikuni carbs were the ticket until the Factory developed the CV carb for stock bikes. With the installation of Thunder slides and Dyna jets, the CV carb can keep up with a big bore Mikuni. | ||
![]() | ![]() | |
Front ends: Scott recommends the Sportster Sport front end with Race Tech Gold Valves to adjust the ride. You can also add a White Bros steering dampner. | ||
Front Brakes: Pre-2000, the only way to go was dual 4-piston Performance Machine brakes. You could also replace the stock rotors with Harley or Performance Machine floating rotors. Now stock Harleys come equipped with 4-piston brakes, which are comparable to the P.M. units. | ||
![]() ![]() | ||
Clutch: The Factory clutch is good to 110 horsepower. Transmission: The stock transmission hangs together under any load, but if you need to shift fast, you could consider Zippers back-cut gears. | ![]() | |
Exhaust: Exhaust is as critical as carburation, but more difficult to tune. Scott recommends Bartels’ Performance two into one exhaust. But depending on your configuration you may want to research an adjustable system such as Supertrapp or Hooker. Gearing: This is an area of choice. Depends on what you want to do. Buells are designed to top out at 110 mph. They’ll do wheelies all day long. They’ll blast through the canyons, but the top end ends at 110. Scott likes that style, but if you want to ride the freeways and hit 130 mph from time to time you may want to look into Daytona gearing and go to chains and sprockets. You may need to slip the clutch in first and second, but you’ll ultimately get to 130 mph. | ||
![]() | Ignition: Scott Bartels recommends the Screamin’ Eagle performance model. | |
Branching Out: | ||
In our effort to bring you a complete list of performance products for Sportsters we’ve broadened our scope and found a couple of other items to consider: Vortex Heads R&R mega Flow Vortex Heads are now available for Sportsters. OEM castings are carefully welded to add material in the intake and exhaust port to allow precision CNC machining. They say the intake port “vortex fin,” plus the raised exhaust port floor generate amazing horsepower. An otherwise basically stock 1200 Sportster with Vortex Heads produced 97 horsepower on a chassis dyno. For more information contact Hyperformance at (515) 266-6381, or e-mail hyperformance2dwx.com. | ||
Ride Forever, –Bandit |
S&S Monster Build
By Bandit |
I was sitting at my desk the other day pondering the woes of the world and, at the same time, wondering just how much crap I could stuff into my garbage can before the trash company would refuse to empty it when the phone rang. It was George Smith from S&S Cycle calling in the loan of his 40th Anniversary Engine. I had been running this beast for a couple of years and tried to convince him that he’d given it to me. “Notta chance, Oz,” he said. “You know the drill, run it for a couple of years and then we get it back to see just how much damage you were able to do to it.” S&S and Hubba-Hubba Racing (George’s Drag Racing Operation) had asked me to punish the 40th motor for a while and I’d readily agreed. I whined for a while about how used I’d become to all the power and torque, and said that I didn’t know how I’d be able to ride anything else. I threw in a couple of tears along the way. George finally got tired of listing and said they’d cut me a fine deal on a new 113 inch ground pounder, with one catch. I’d have to assemble it. Knowing what a fine motor man I wasn’t, I jumped at the deal, and as soon as I’d hung up the phone I called my pal Fuzzy, owner of Shakedown Street, in Ventura, California. “Fuz, I need your tender touch on some S&S parts I got coming!” Fuzzy said no problem and I eagerly awaited the promised packages from Wisconsin. The stuff arrived in short order, and into the truck it went on it’s way to Shakedown Street, arguably one of Southern California’s premier shops. Fuzzy and his crew specialize in everything form radical customs, such as the one seen here,
![]() to this soon to be finished drag racer…..
![]() If Fuzzy’s name sounds familiar, he’s well known in H-D drag racing circles, and most recently handled much of the precision stuff for Jim’s Machine. Shakedown also offers all the service any street rider could require. The first thing you gotta do, before any assembly, is to thoroughly check everything out for the proper clearance and alignment. We started with the flywheels. We jigged them up in the truing stand and found them to well under the 0.002 inch runout.
![]() In fact, the gauges didn’t seem to move at all.
![]() The pinion shaft bearing race (above) and shaft (below) were both damned near as perfect as you could get.
![]() Next we needed to check the sprocket shaft bearing fit. To accomplish this Fuzzy uses a slightly turned down sprocket shaft with two thousandths taken off.
![]() The new bearing is then slid on the dummy shaft, dry, and the fixture mounted in a vise (photo below).
![]()
![]()
![]()
![]() The assembly is torqued down and the dial indicator set up (above).
![]() It was necessary for us to use a slightly thicker spacer to get the precise endplay required. The specifications call for endplay between 0.001-0.005 inches. We then cleaned the cases and blew out all the oil passages. Any new case should also have the oil pump mounting surface checked for burrs or other irregularities.
![]() The oil pump is also inspected and lightly oiled.
![]() Next the breather gear is fitted into the case and checked for rotation.
![]() It’s now time to install the flywheels and mate the case halves together.
![]() Fuzzy recommends Three Bond Liquid Gasket #1104 for trouble free and leak free assembly. The cases are torqued (below) and the pinion gears, oil pump and breather are installed.
![]()
![]()
![]() The lifters and lifter blocks finish off the cases and it’s on to the cylinders. We cleaned and checked the cylinders for any irregularities and then made sure the ring end gap was within specs.
![]() Next Fuzzy installed the rings on the pistons….
![]() ….and then, after lubing the rod bushing….
![]() ……installed the pistons on the rods.
![]() The inner skirts of each piston are cut….
![]() ….to make sure they don’t collide as they pass each other. The rings are compressed and the cylinders slid into place. Head bolt can be used to secure the first cylinder as you install the second.
![]() The cylinder heads are bolted on and torqued….
![]() ….and then it’s time for the rocker boxes. These are installed and torqued….
![]() ….and you’re done. As you can see from the look on Fuzzy’s face….
![]() ….he’s glad to have us done and can now get back to some real work. After all the help he’s given use we’d thought we’d tell you all once again what a first class operation Fuzzy runs. We also thought we’d show you a couple of shots of his engine area.
![]()
![]() Fuzzy’s as meticulous about your work as he is about his shop, so give him a call at 805-644-5001 if you want the best workmanship in Southern California. Now I guess I’m gonna have to get busy, so I’ll see all of you on the road. Oz
|
Installing the Screamin’ Eagle Induction System
By Bandit |
![]() My life is usually peaceful. I tweak on the bikes at Bikernet, tweak on my own, drink a little beer and watch television. Ever since Bandit broke up with his last wife, I decided to avoid the pitfalls of life and stick to myself. This particular day at the Bikernet headquarters was a perfect example of why my selfish decision was justified. Bandit volunteered to install the new Holly carburetor from Screamin’ Eagle on Brenda Fox’s new Deuce. Ms. Fox works at Bartels’ Harley-Davidson in Marina del Rey when she’s not modeling or performing promotional miracles for various companies. I’ve seen Bandit ride with her and there aren’t many people who care to keep up with the big bastard, but Brenda does. Anyway, she’s determined to make this sucker into the sleek chopper she’s always wanted. For those who think only rich cats can afford new H-D’s well, check this: She shares an apartment, pays a lot of doctor bills, has a junk car and is just a working chick in a dealership. This bike is her baby, her life. Sure, she scored a deal, but she’s still a workin’ chick who managed to afford a new scoot. Now, back to my example of how downright distracting, disturbing and tumultuous Bandit’s life can be. It was slightly overcast in the San Pedro Harbor when Markus Cuff, the photog, rolled in to take these shots. Still early, this long-legged blond storms the gate looking for Bandit. She’s in her early 20s and dressed to kill. She latched on to the boss and pulled him toward the house. We had three operations to handle on Brenda’s bike in a day, plus take notes for each tech and photograph each process. We needed to move. Marcus was fashioning an all-white miniature studio in the corner of our leaning garage so he could document each product. I began to loosen the Softail shocks, then was told to leave them alone. I got a cup of coffee and kicked back while Marcus shot each product. First there were lower shocks, then the Rip Saw Samson Exhaust system, then the Holly carburetor kit. Before kickin’ off the tear-down, Markus, the scrawny film master dressed in all black, set up his lights and took a before-shot of the bone stock Deuce. The sun was cresting high noon when Bandit stormed into the garage. “Is it done yet?” he asked sarcastically. “We’re burnin’ daylight.” Finally, the shots were taken and we went to work removing the shocks and replacing the exhaust system. But with each delicate task, another woman arrived and drug Bandit into the Bikernet headquarters. There was one striking, dark-haired girl who seemed to glide along the pavement. She was of medium height and didn’t have gigantic boobs, but she had a sense of poise about her which drew my attention and distracted the big guy. I finished with the shocks and was dismantling the exhaust system when Bandit returned. “Snap it up, damnit,” he said. “Fuck off,” I returned and finished taking off the heavy stock system. He was with me throughout the exhaust install, then just as we were about to tear into the stock carburetor, Brenda arrived. She’s a bundle of energy, seemingly bounding off the walls. She was on her way to Palm Springs Bike Week when she jammed into the headquarters to lasso Bandit for what I don’t know, and he disappeared again. When he returned, the CV carburetor had been removed along with the stock manifold. We carefully set these components aside and not in the shit can. We would need some of them before the operation was over. The factory instructions call for removing the negative lead to the battery. In this case, it’s not a big deal, but still advisable. Here’s the disassembly deal: Remove the stock air cleaner, carburetor and intake manifold. See Photo 1. Remove the stock choke assembly from the stock carb (you’ll need it) and set it aside. See
![]() Take the MAP sensor off the original manifold and attach it to the new one. Install new intake seals to the intake manifold. Connect the vacuum hose to the fitting on the manifold and the electrical connector to the MAP sensor, if present.
![]() Install the intake manifold to the heads, but just finger tight. We quickly discovered that a shortened allen wrench would be beneficial to the operation. So we cut one down for use on the left side of the bike. The other side was best handled with a long allen with a ball end and a small box end wrench for leverage.
![]() Disassemble the stock enrichener cable assembly. Remove the enrichener valve, spring, plastic nut, 90 degree elbow, hex nut and star washer from the cable.
![]() Pick up the new cable from the kit and install the star washer and hex nut just removed from the existing assembly (I already had this stuff on the new cable). Install the rubber boot over the straight steel cable guide. Install the original plastic nut and spring along with the new enrichener valve. This is a simple operation, but be careful not to mix up the parts. The rubber elbow seems strange, but when you have the new cable guide in place it will straighten out the boot. It all slips into place. Slip and screw in the new cable assembly into the back of the carb body. Install the new gasket. There are two gaskets; match up the one you need and slip the carb into place with the three allen bolts. Don’t tighten them past snug at this point because ultimately the carb will come back off. Use a long allen wrench.
![]() Now comes this convoluted plumbing and hardware system. It’s simple once you get the hang of it, so here’s the score: Place a large ID washer over each banjo bolt and slip it through the holes in the mounting bracket, then place a second large ID washer over each banjo blot to seal the plumbing. Place the breather manifold over the banjo bolts with the hose fitting on the manifold toward the rear of the bike. Place the remaining two washers over the breather bolts. On Twin Cam engines, the last washers will have small IDs. While holding the assembly together, insert the banjo bolts into the tapped holes in the cylinder heads. Tighten each bolt a little at a time until the assembly is loosely held in place.
![]() Take a step back from the carb and marvel at your accomplishment, and wonder if you couldn’t just eliminate all that crap. You can’t, so keep moving. Find the 90-degree nipple hose fitting and screw into the backside of the air cleaner backing plate. Be careful not to over tighten. The hose fitting should be pointing toward the back of the motorcycle after installation. If it’s loose when you get to that position or too tight to make another revolution, take it out and wrap it with Teflon tape. Install the backing plate gasket to the front of the carburetor using three studs. Align the backing plate to the bracket by installing the two flat head screws to the mounting bracket. Again, don’t tighten that sucker. You are actually aligning the entire assembly before tightening it all down. Ultimately, the carb body will have to be removed to allow you to tighten the intake manifold.
![]() Finger tighten the banjo bolts (installed into the heads) to align the carburetor back plate and intake manifold. Making sure everything is aligned, tighten the left side of the intake manifold bolts to secure the manifold in position. Now the dress rehearsal is over. Remove the backing plate, mounting bracket, manifold breather tube and carburetor assembly, then tighten the right-side intake manifold bolts.
![]() There is one more operation before bolting the sucker entirely back together. It may sound easy, but this was the toughest part for me. You have to route and connect the throttle cables to the carburetor throttle wheel. The trick is to make sure you have the right cable going to the correct side of the wheel. Remember the push/pull system, so operate the throttle on the handlebars to determine whether you are working with the proper cable. You will need to loosen the adjustment under the throttle housing on the bars for some slack. I had a hard time routing the pull cable end into the wheel. You need to open the butterfly to make this happen. The push cable fits easily. Find the cable bracket and insert the cables. Then roll the pointed end of the bracket onto the top of the carb body and into place. Install the bracket onto the carb body and torque the allen screw to 3-5 foot pounds. Now smear grease on either side of the carb gasket for a secure seal. Install the carb with the three allen bolts and tighten to 10-12 ft-lbs. Readjust the throttle cables to factory specs. I may have caused the pull cable to bind under the tank, so be careful that the cables don’t catch. Check the throttle to make sure it’s operating properly. Look down the throat and make sure the carb butterflies are opening and closing, not sticking or binding. Install the fuel line. You may want to take the protective sleeve off the old line and use it on the new one. Secure each end with a 3/8-inch hose clamp. On either side of the carb body is a mid-range adjustment screw. Turn it in until it bottoms and back it out slowly two turns. It should be adjusted to go. Loctite the banjo bolts and put them into place with the manifold breather tube, bracket and bolt assembly to the cylinder heads. Reinstall the carb-to-backing plate gasket and backing plate to carburetor and mounting bracket using two flat-head screws and three 1/4 studs. Tighten all five fasteners 3-5 ft-lbs. You don’t need to seal this gasket with grease or any adhesive. Tighten the manifold breather tube banjo bolts to 10-12 ft-lbs. Attach the short end of the manifold breather hose to the 90-degree fitting on the backside of the backing plate and secure with 3/8-inch hose clamp. Cut the long end of the manifold breather hose to correct length, connect it to the manifold breather and secure with clamp. Install the air filter to the backing plate and secure with three Button-head screws. Tighten to 3-5 ft. lbs. Apply Loctite (blue) to the threads of the cover screw removed from the original air cleaner and install cover using screw and washer.
![]() Secure the choke knob, tighten and adjust to factory specs.
![]() We cleaned the bike and made sure the pipes were free of fingerprints. Then we fired her to life. The fleet center guys told us that we could see gains of 60 to 72 horses and 70 to 82 pounds of torque. We called Walter from Bartels’, who watches out for Brenda. Bandit asked him to check over the installation and remove the EPA canister, which was no longer needed, to clean up the plumbing on the bike.
![]() The bike seemed to run fine out of the gate. If you do have a problem, the idle mixture screws on the sides of the metering block can be adjusted. The correct adjustment should fall between half and three turns out from bottom. If it doesn’t perform well there, you may need a new slow jet. The main metering jets can also be swapped from the standard #58 to #62 to richen the mixture. So that’s the story. It wasn’t until we were taking the final shot that Bandit returned to the garage. He seemed drawn and tired, his hair a mess. Brenda slapped him on his ass and dashed out the gate. He looked over the bike and nodded a quiet approval, then pulled a pewter flask from his back pocket and downed a healthy swig. He sat hard on the shop stool and took a deep breath. “Helluva day men,” he said. “Nice work. I’m buying tacos and tequila for dinner.” Just then, a tall Oriental bombshell in short shorts stepped into the garage. Her plump tits tried to escape her top as she tapped Bandit on the shoulder. “I need to see you inside,” she said in a voice that would melt chrome off the new Samson exhaust system. Out of nowhere, Bandit seemed to snap out of his earlier doldrums. “You guys go to the harbor and order for me. I’ll be right down,” he said as he turned and followed the legs that have made good men bad, and pure men, sin. That’s the last we saw of him. –Wrench
|
Back to theGarage….
The Cyril Huze Project
By Bandit |
FLASHBACK
On the night of Jan. 10, 2001, Arlen Ness, Jesse James, Paul Yaffe and I were on different planes to the same destination: the Italian Chopper Custom Bike Show of Padova, near Milan, one of Europe’s most important motorcycle events. I cross the Atlantic a couple times a year, but it had been five years since I walked the streets of Rome, Milan or Firenze. The night flying from one continent to the other is very short because of the six-hour time difference. So when I fly west to east, I never sleep. I am excited like a kid because I love Italy so much. It is the birthplace of so many talented artists who influenced the world with their architecture, fashion and automotive designs. I spend the night drinking too much coffee and chewing peanuts (because I can’t smoke) and reflecting on what my shop has produced during these last months and on what I would like to build the next season. In the U.S., everybody and his brother (plus me!) are building choppers. In Europe, the craze is called bobbers (I would like to make one, too!). But what else to build? I am not supposed to follow trends. I have to surf on them. It’s what people expect from me. Thinking of new projects has always been for me like a sweet torture. So, I torture myself all night.
ESPRESSO ANYONE?
It’s time for breakfast before landing in Milan. “Espresso anyone?” asks the too-sexy Italian-American flight attendant. Espresso at breakfast? Did she say espresso with an S? Or expresso with an X? She said eSpresso. I am thinking eXpresso, like …so Express. That’s it! I’ve got a bike theme. I request my eXpresso, she gives me an eSpresso plus a cool theme for a fast-looking bike. If I weren’t seat belted in because of turbulence, I would jump to kiss her. Hey, of course, it will not be an ode to coffee (although hot java has always been a very good friend when building bikes). A bike with a chopper attitude and a street racer stance. A chopper to race? Attitude and speed would have to be mixed together. Is it possible?
BEFORE DAYTONA – DAYTONA – AFTER DAYTONA.
The time from before to after Daytona is a custom builder’s nightmare. There is too much to do, too much to fix at the last minute, too many people to see at the same time. Expresso is buried in the left side of my brain. The only decision I am able to make is the choice of the frame. It’s an easy choice. Since October, I’ve been teamed up with Peter Penz to market a Softail frame that I named “Kool Kat.”
I sold a lot of frames and rolling chassis, but there’s been no time to produce my full-blown “Kool Kat” custom.
The frame accepts the new Avon 250 mm rear tire with a stock belt. That’s very important when you run a big mill because 1 1/8 belts are a third less strong than 1 ½ inch belts.
The absence of the middle post and the battery relocated in the swingarm gives a lot of room in the rear, making the bike built on this frame look very agile, exactly what I am looking for. I offer this frame in many different geometries (rake from 36 to 44, stretch from 3 to 6 inches, front leg from minus 2 to plus 6 inches). And if that’s not enough, you can add one of our raked triple trees (3-5-7-degree) and you have your own ultra-custom frame. In my shop, I pick one with a 5-inch stretch and 42-degree rake.
EXPRESSO FIRST SKETCHES
The frame high neck gives Expresso the stance I need to mean attitude. Now I need to express(o) speed. It jumps to my mind that it can come from the swingarm. This part of the bike has long been neglected even on sharp customs. Only during the last few years has the swingarm evolved. A lot of custom builders are now going to the single sided swingarm, which looks very cool. But I want something different. Instead of focusing first on the overall shape of the bike, I try to imagine my “speedy” swingarm. I see it pointed in the rear, reaching far behind the axle, with stepping all along. I love computers but I hate to use CAD programs because the learning curve is very steep and usually it’s much easier and faster for me to use a pen and paper to jot down my ideas. But I know in advance that Bob, my master fabricator, is going to turn me down if I don’t bring him a sketch perfectly scaled (hey, he knows how to protect himself). The swingarm is all drawn in my mind but in a few days my briefing will have to be “engineered” as much as possible. I must CAD design this swingarm. Loading the CAD program on my computer gives me the same chill as filling out my tax return…but I have no choice. I spend about eight hours struggling with the keyboard and designing the Expresso swingarm. It’s not perfect, but in line with what I am looking for. From there I go back to paper and pen to make a first sketch of the bike.
INTERNAL AFFAIRS
I am always somewhat nervous when I present my ideas to my crew. Building bikes is not an exact science. Will they be excited? If not, I know it’s going to be a so-so bike. So, evidently, I will not build it. If they are as excited as I am, it’s going to be a great bike. Keeping the excitement alive from the first day to the time the bike is ridden for the first time is part of my job. Custom shops are horizontal structures. Everybody needs everybody. It’s a team effort. Passion is the cement holding us together for ventures lasting many months. I am the composer. My melodies have to first be approved. Then I will write the orchestration and will transform myself into music director. But that is another story.
Thursday is D-day. The crew in charge of this custom project (Bob, Sean, Brigitte) invades my office. I talk for half an hour, show the sketches, suggest a light …… paint job. (No I will not tell you the color right now because I reserve the right to change my mind, my special privilege. Then they give me the magic words: “Nobody’s done it before. That’s cool. We can do it. Let’s do it. When do we start it?”
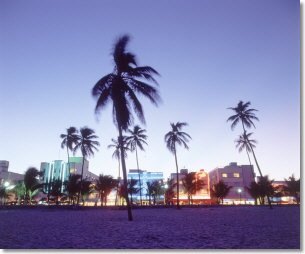
Monday, of course. We always start on Monday because weekends are made to go somewhere. And it’s always somewhere out of the office that I find new ideas. And I still need a ton of new ideas to make Expresso a great custom. What I gave them is just the first draft.
Expresso Swingarm
When we start a new custom, there is a tradition that we respect religiously: We always start with what seems to us the most difficult part to fabricate. So, on this Monday morning, the swingarm is the first part of the bike that we lay down on the fabrication table. (a.k.a. the surgery table) The first decisions to make are:
1. The number of steps inside the swingarm.
2. The thickness of each step and which one is thicker (top or bottom?).
3. How the swingarm must look from inside.
It’s my job and responsibility to make these decisions, but I would never obligate my fabricator to do anything without first convincing him, if necessary. Bob is in charge. He agrees immediately with me on the fact that: Steps always look better in odd numbers, so we keep the three steps as they appear on my sketch; The step on top will be higher. Each step must be about half the size of the one just above (to give fluidity to the lines), but the thickness of each step must look the same (as a matter of fact, they have to be a different thickness because they’re welded to the same back plate); Seen from inside the swingarm, no step will be visible because it would visually interfere with the wheel and brake designs.
Our “stock” swingarm is thick. It takes almost an hour for Bob to cut the pieces joining the main tubes of the swingarm — just the time I need to cut cardboard templates of the steps. It’s from these cardboard pieces that Bob cuts three metal pieces that he will adjust inside the swingarm. Then he will duplicate (reversed) these three metal steps for the other side of the swingarm. It’s already 80 degrees at 10 a.m. Bob has a lot of cutting and welding to do and he is already sweating. We close the bay and set the air conditioner at 75. I leave the fabrication room to work on a new chopper that I have to get started. But that’s another story… Bob and I have an agreement: I never come to check what he does. If he is stuck with a problem, he calls me immediately to decide a remedy. But if everything goes fine, he calls me only when the job is done and looks perfect to him. I estimate that the swingarm fabrication is a two-day job, including the cutting, trimming, welding and polishing. Good news — I won’t hear from Bob during these two days, and will resist to the temptation to check the work in progress (which is, for me, very difficult).
Two Days Later
Expresso gets its racy swingarm. We prime it because I hate to see a bike rusting during the fabrication and mockup process. To be sure it’s perfect, we attach it to the frame using Progressive suspension shocks. I immediately see a small imperfection that nobody saw before — a small bump on the lower part of the swingarm, just behind the rear axle. We correct it with a grinder and make a primer touchup. I already dream of mass producing this swingarm in steel or maybe billet aluminum. There’s a typical builder’s dilemma, however: How many need to be CNC machined to make it affordable to the public? How much money can I invest? Low cash flow has always been a custom builder’s main problem…
Expresso Juice
I have always been a fan of small, dry cell batteries. I use them on all my bikes. They can be easily hidden, placed in any position, and in a small package, their cranking power is double that of most standard wet acid batteries. They start big motors when the appropriate starter is used. Most times, I use small Odyssey batteries with 500 CCA and measuring only 6.69 inches long by 7.05 inches wide and 5.04 inches high..
The frame kit that we sell includes a battery bottom plate bolted to the swingarm, and a top cover with slots to make the battery connections accessible. Rubber or metallic straps are enough to hold the battery securely in place inside the swingarm. But the battery still remains visible. Customizing is about hiding what doesn’t deserve to be seen. So, I must make this battery “disappear” as much as possible. I want to conceive a simple system that the motorcycle dealer or individual builder in his garage could easily fabricate.
It doesn’t take more than five minutes to agree with the boys on the kind of battery box to fabricate. Sean volunteers to make it and is already busy measuring the battery again to cut the six steel plates to be used to conceal it from view.
It’s very simple. Instead of using the base plate provided with the frame, the entire box will be bolted to the swingarm. A box is fabricated in such a way that it slides forward. Two small, flat screws will hold it in place. The front plate is conceived in such a way that the connections are not visible. Two holes are made for the battery cables to exit the box. A battery must be charged from time to time, but we don’t need access to the connections to do it. We will charge directly at the starter, which is easier and faster than unbolting the box.
Suddenly I realize that the box must stand perfectly vertical to the ground when the swingarm is in its definitive position with the engine, transmission and primary installed. It means that the portion of the swingarm where the battery box sits must be adjusted to correct the swingarm angle when the bike is on its weight. We postpone this job until we set up the definitive geometry of the frame, which is our next step. We just prime the battery box to keep it rust free.
Hiding the Oil Tank
The Kool Kat frame is sold with a custom stainless steel oil tank, small in size but big in capacity (4 quarts because it doesn’t contain the battery).
Four steel plates are also provided. They have to be welded inside the two openings on each side of the frame, making the oil tank disappear from view when the bike is looked at from profile. These side plates are not identical for each side because of the left kick-out of the frame to accept a 250 mm tire on an 18-by-9 rear wheel.
Frame Geometry
The most frequent questions (at least 15 a day) we receive through e-mail and over the phone, are:
1- I have a frame with such stretch, such rake. How long should my tubes be?
2- I lowered the rear of my bike 2 inches. How much should I rake to keep the bike horizontal?
3- I saw a bike in a magazine with a 10-inch over. I want the same look. How much should I rake my bike?
4- Etc…
The answer is: it depends!
Not all frames are born equal. A 5-inch backbone stretch doesn’t mean the same length on the top tube from one brand to the other. (Don’t ask me why.) The neck of different frames doesn’t stand at the same distance from the ground. Front leg stretch, lowered shocks or adjustable air shocks on a Softail are examples of other parameters that affect the geometry of a frame, its distance from the ground, and the overall look of the bike. When people require a 10-inch over front end, it means 10 inches over stock. But stock Harley bikes, depending on the model, have different front end lengths!
So, here’s how I set up the geometry of Expresso. I like my bikes to be a compromise between look and function. It means high enough to be rideable, and low enough to look good. I like them when they sit at 4 3/4 inches from the ground (meaning from the ground to the lower portion of the lower tube of the frame). It’s the distance I want when the bike carries all its components, with a biker of average weight seated on it. When the bike I customize is a dresser with floorboards, I increase this distance to 5 inches minimum. Same when it’s a two-seater.
On this project, I use Progressive Suspension shocks. I attach the swingarm to the frame and bolt the shocks to the frame and swingarm. I install the 18-by-9 rear wheel equipped with an Avon 250-by-40-by-18. (At this stage I am not preoccupied by the fact that the wheel is or is not perfectly centered in the frame) We mock up the bike with cases (our engine is not ready yet), a transmission, a starter, an inner primary and all the main components available in the shop to be close to the weight that the bike will have to carry. I take measurements and I realize that the Kool Kat frame with stock height shocks sits 5 inches from the ground. I know because the lower tube of the frame is parallel to the lift table when we put two pieces of wood, 4-by-4 plus 4-by-1, on the front and back of the frame.
Now we have to figure out the tube length to keep the bike parallel to the ground. First, Sean installs a triple tree. Then we lock a 21-inch wheel in the vise of the lift (with a piece of wood covered with carpet on each side of the tire to avoid scratching the rim). We run one neon tube through one of the holes of the triple tree, and move the frame on the table until the tube crosses the center of the axle of the front wheel (the opposite can be done, not moving the frame, by moving the front wheel back and forth, but it’s difficult to keep the front wheel from moving while taking measurements). Now I measure the total front end required. It’s the distance from the top of the triple tree to the center of the front axle. It’s exactly 34 inches. Now it’s easy to figure out the tube length I need. Because tubes sit about 7 ¾ inches from the bottom of the lower legs, I need tubes 26 1/4 inches long (Front end 34 inches – 7 3/4 inches).
At the shop, we always keep tubes in different lengths. All have internals (springs, seals, etc., pre-installed so that we don’t lose time when mocking up a bike). For information, 26 ¼ inch-long tubes are 2 inches over FXDWG stock tubes (24 ¼ inches).
I install the tubes in the lower legs, slide the front end in the triple tree and lock it. We tie down the bike in front (not under heavy pressure because we need to lift the bike to remove the pieces of wood under the frame). Our last exercise of the day is to jump on the bike to unfreeze the swingarm, and then to “ride” the bike on the lift to check again the distance from the ground. Sean is 195 pounds, quite a few pounds heavier than me. So, he “test rides” the bike while I take measurements. I am all smiles when I realize that the bike sits perfectly at 4.75 inches from the table, front and rear.
It’s 7 p.m. Sean proposes to celebrate with a cup of coffee at Starbucks, not far away from the shop. I know why. It’s this time of the day when pretty secretaries must do last minute photocopies at Kinko’s. And Kinko’s are always located next door to Starbucks. Or the opposite. Whatever. Sean is single again. Let’s make Sean happy. I’m gonna drink my eighth cup of coffee of the day, and probably go back to the shop to read my e-mails. Any questions?
Expresso Rear Fender
It seems that pointed rear fenders became my trademark. Not that I don’t like round fenders, short or long. We fabricate a lot of them, too. But my most recent bikes “Dreamliner” & “High Octane” had pointed fenders that were “imposed” by their themes. Since these 2 bikes are well known, everybody’s thinking: pointed fender = Cyril Huze.
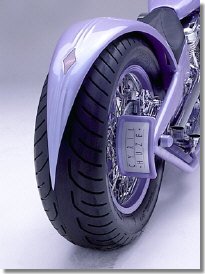
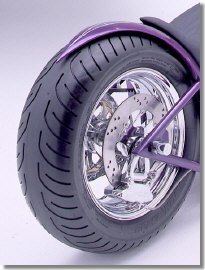
When I think of “Expresso” it’s difficult for me to imagine something else than a sharp fender matching our already fabricated pointed swingarm. So, I guess that when the bike will be finished, I am going to reinforce my stereotype. It’s Ok with me because my next project is going to be very, very different. I like change. The boys too.
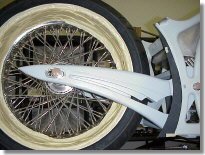
Anyone showing a bike with a pointed fender will tell you the same thing. Everybody, and I repeat everybody, is going to check: 1- if the pointe is centered on the tire 2- Move the fender right and left to see if the fender is strong enough to not vibrate. No way you can cheat with this kind of fender: 1- symmetry must be perfect 2- fender need to be “boxed” not to vibrate and crack the paint.
Before starting fabricating any fender, the most important step, the one conditioning success or failure, is to mock up the bike the way it’s going to ride: with 2 wheels aligned and perfectly centered in the frame. For the rear fender, we must mock up the bike with an engine (fake or not), a primary, a transmission, a rear wheel perfectly centered in the frame, and a belt adjusted at the right tension. Usually it’s the step of bike building when things begin to get scratched. Tape being less expensive than chrome, we tape, tape, and tape again all what is called chrome & polished aluminum. I recommend you do the same. You can trust us about this one.
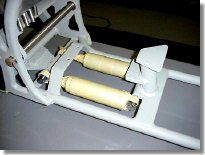
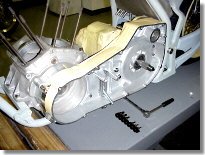
First, we estimate what is the position of the wheel to be centered in the frame. For this, we mark the center of the 250 mm tire. Then, we run a thin blue (for visibility) painter masking tape along the frame backbone to the center of the tire. Any slight bend, and you know that the wheel is off center, and or turning right or left. When our eyes tell us we are close to the truth (for now it’s only an estimation), we lock the wheel in place and cut a right spacer.
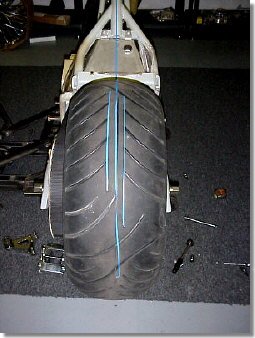
Because we are going to use a drive side pulley rotor by RC Components (where pulley is also the rotor), we bolt it on the wheel, wrap the belt around the pulley, find the right tension of the belt, and lock the wheel in place. We measure the distance from the swingarm pivot to the center of the rear axle. Of course, distance must be the same for both sides (don’t rely on the position of the axle in right and left slot of the swingarm, because some frames can have these slots incorrectly machined and not the same size on both sides). On the left side, we measure the spacing to the pulley/rotor and from the pulley rotor to the wheel. We cut 2 spacers and install again the wheel with its brake drive system. (Later a custom pulley spacer will replace the spacer from pulley to wheel). We reinstall the wheel and pulley brake system, adjust again the belt tension, and measure again the distance from swingarm pivot to rear axle center, on right & left side. Our wheel seems centered. We check again running 2 steel plates on each side on the tire going forward. After being sure that these 2 plates run parallel, using vertical plates against the frame, we measure the distance to the frame, right and left side.
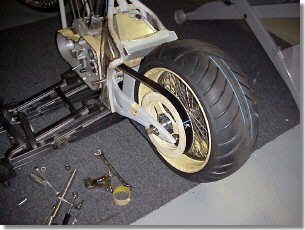
Since we had to mock up the rear of the bike to know the exact position of the wheel before fabricating the rear fender, we take advantage of this mock up to check if our pulley spacing is correct. We lift the rear of the bike with 2 4×4 pieces of wood under the frame, and give the wheel several rotations forward and backward. We observe the belt running on the pulley. It doesn’t want to go off the pulley. Of course, the belt (1 ½ inch) clears the tire on 1 side and the frame left side plate on the other side. Our wheel is perfectly in place. We lock tightly the wheel. (You don’t want it to move during the fabrication process, or be ready for bad surprises: tire too close or too far away from fender, fender not following curve of tire, etc…). Yes, it happens. Trust us again about this one. Now, we can start the rear fender fabrication.
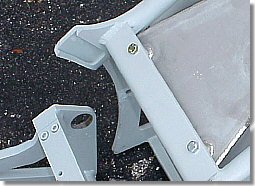
Even when we build a solo seat bike, we make our rear fenders strong enough to carry a passenger. We are very understanding of our clients: we know that may leave alone, then need to ride back with a passenger…Anything wrong with fabricating a fender stronger that it should be for a solo rider. It’s the reason why all our fenders have internal struts. These struts are quite difficult to make for a pointed fender. As starting point, we want to use the slots in the frame where classic parallel struts are supposed to slide in.
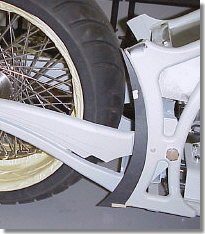
But I immediately realize that a curve starting from this position will not follow perfectly the curve of the tire. So, I cut a piece of cardboard extending rearward the frame sideplate. Using a flexible steel rod, and using the tire as a reference, I draw a curve and cut the cardboard to know the extra piece we have to add to the frame side plates. From there, 2 thick rods will be welded and will join each other where I want the rear fender to end: 1 inch behind a vertical line going through the end of the swingarm.
No English wheel to fabricate this fender. No aftermarket fender to start from. Just 2 sheets (because this fender is going to be “double wall”) of 14 gauge steel hammered and hammered during half a day until Sean gets the shape I want.
Not only our fender is very thick, but also Sean reinforces it with 2 steel lips. “Boxed” this way, no chance the fender will ever vibrate or crack the paint. Sean, who was 195 pounds before hammering it, and 190 pounds after, is finally authorized to sit on it. As strong as stone can be. I joke that we are very safe because nobody with such a bike is going to go back home with a girl his weight.
Time for spraying cheap primer. Because as everybody knows: I hate rust.
Pet owners look like their favorite pets. I guess my bikes look like me. A projection of my personality (many sides, meaning many bikes), plus the client input. Expresso is a spec bike. So I can do what I want!
The motorcycle trend is toward FAT. Fat everything: tires, wheels, front ends and gas tanks. But I don’t like fat gas tanks. They make the bike look heavy and destroy the speed effect that everybody is looking for when stretching the bike. I love rear ends muscled by fat wheels & tires, but I think it looks better when the gas tank is slim and stretched to the extreme. Fuel capacity is not my main preoccupation either. So, we are going to fabricate a one-off gas tank narrow, with a lot of arch, stretched as much as we can.
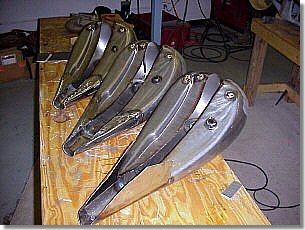
At CHC, we custom make gas tanks in 3 & 5-inch stretch for cruisers and choppers. In the fabrication room, they are laid down upside down on a bench waiting for the last cosmetic welds before being shipped to our clients. Vision of steel seagulls! We pick one in 5 inch stretch and check on the bike to see how much stretch we can add: 1 inch.
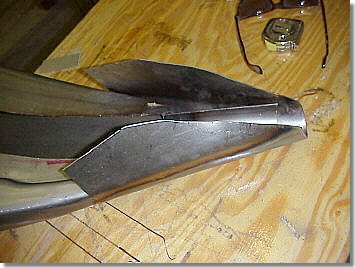
Our extension is going to be a “dry” extension, meaning no gas will be in this part of the gas tank. It would be of no interest to make it a “wet” extension because no fuel valve can be installed at such a low place: the petcock would interfere with the rear rocker box!
A Hot Match pop up gas cap is welded and then we do a fast priming of the new gas tank
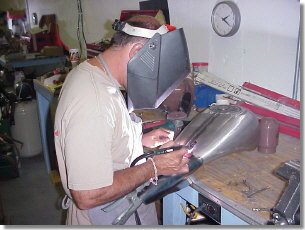
A 16-gauge piece of steel is folded around the lower part of our existing tank, and then formed around the frame top tube, and then tig welded.
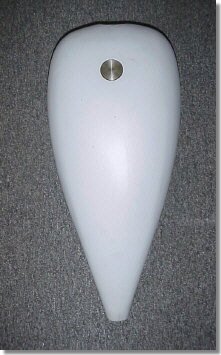
Another 16-gauge sheet of steel is U shaped on the top tube to create a 1-piece bracket with a 4-point mount system. A cardboard template is used to match the curve of the bracket with the lower curve of the gas tank.
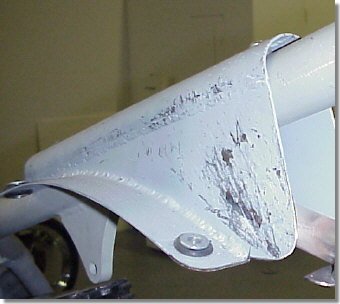
After checking the definitive position of the gas tank (I like to keep a big open space between the front of the gas tank and the frame neck), 2 holes are tapped on the top of the frame backbone and the bracket is bolted on. The bracket mounting holes are equipped with stock factory rubber grommets.
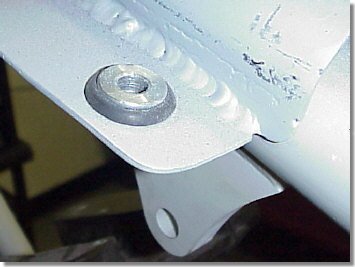
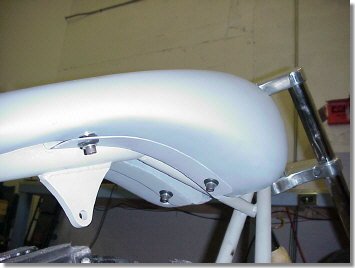
Most gas tanks look like an added piece on the frame. This is evident when you look at the gas tank from the front. We need to fill the gap between the 2 halves of the tank. A steel piece is cut to fill the gap, then curved and welded to the backbone.
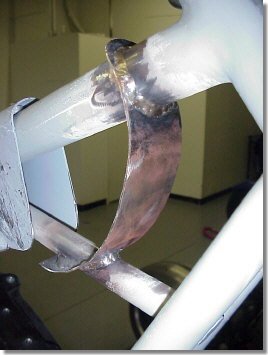
A slight gap is kept between the plate and each side of the tank. Making it perfectly flush at this time would create big problems later when the bike is painted & cleared. Later, at molding time, a perfect fit will be done. Now our custom gas tank looks like it belongs to the bike.
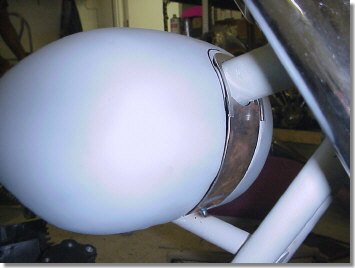
It’s time to compare the bike in progress and the initial sketch. We are on our way…
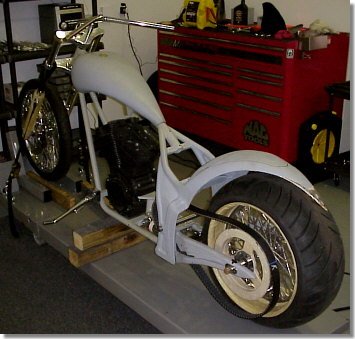
Seat Pan
One thing I learned when I was head judge in the Rat’s Hole Show in Daytona and Sturgis is that a seat is often the weakest part of many very well built motorcycles. I am not talking about the color used or even the material employed. I am talking about the seat not fitting perfectly to the frame, not being symmetric or being afflicted with wrinkles because of poor seat pan preparation.
Some upholstery shops do seat pans. Others refuse and will do only the pure upholstery job. My opinion is that the bike builder should prepare a pan for a custom seat. A seat pan being “part” of the frame, it’s our responsibility to make it right. Steel pan or fiberglass? It’s very controversial. We do both and each has advantages and disadvantages. Steel pans require metal fabrication skills to make them fit perfectly to the rear fender. The pan must be very smooth when doing thin seats, like on most top custom motorcycles. If not, all imperfections, sooner or later, are going to push the foam (even high-density foam) and create weird wrinkles and crooked stitching lines. Fiberglass seat pans don’t require any particular skills and can be built by any builder working in his garage. Fiberglass can easily be smoothed out to create a perfect base and sanded for perfect adjustments. The danger is that fiberglass seat pans have a tendency to retract when curing (usually the first 48 hours), creating an imperfect fit to the rear fender (back of the seat pan retracting). But there are several ways to avoid or correct this problem. Because this story is about helping the largest number of non-professional builders, we decided to show a fiberglass seat pan fabrication.
To get started, buy 2 gallons of fiberglass at the closest auto store, find two paint brushes (no, you will not be able to reuse them) and a roll of foil. Cut a piece of thin cardboard for the sitting part. Cover it with foil and continue up the fender (no cardboard is used on the fender part of the seat because cardboard will never fit perfectly to a curved shape). Be generous with the foil, covering more than the seat area. Cut pieces of fiberglass cloth to imitate the shape of the seat. Then, using a brush, soak the fiberglass cloth with resin. Let it dry 24 hours. The day after, do a second coat of resin using extra hardener for fast curing. Wait 24 hours more. Then with a thin felt pen, you can draw your seat. To trace a perfect curve for the back seat, I use …my welding rod.
Remove the pan and give it its definitive shape by cutting it with a small cutting wheel. To be certain that the back seat has a perfect symmetry, we cut a piece of paper imitating the back seat. We fold it in half. Right away, we know where the cutting wheel has to work again against the fiberglass. Sand the top of the pan for a smooth finish.
To hold the seat in place, it’s very simple. The pan being installed on the frame, drill two holes in the front at the place where the front tube extends to the seat. Drill through the fiberglass. We drill only one hole through the fiberglass in the back fender. Then we fiberglass three button head bolts into the three holes. Your seat can now be dropped into place. It will never move while riding and it will not need any tool to be removed. Our seat pan fits like a glove.
Each step of the building process is important, but one of the most critical is the frame preparation before the paint job. At this stage, we must check that all parts are fitting together and make any brackets or holes in the frame. Because when the paint is dry, it’s too late to make any modifications. Or it’s going to be very, very costly.
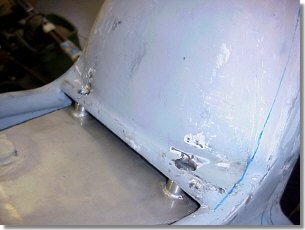
First, we need to make two slots in front of the rear fender to be able to bolt and unbolt the custom oil tank.
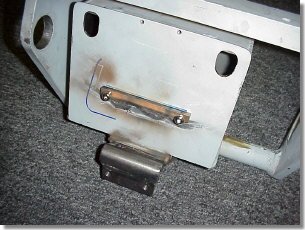
I don’t intend to do extra fabrication on the front tubes to hide the voltage regulator. Because I don’t like regulators held on a bracket in front of the engine mount, I decide that it should be “buried” somewhere else.
The best hiding place is in front of the custom battery box that we fabricated. Because the box we made fit the dry cell battery very tightly, we cannot bolt the regulator from inside the box. So we weld a block of steel, tap two holes in it and bolt on the regulator from outside.
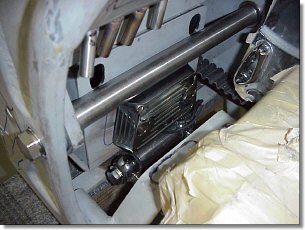
It means that we will have to route the regulator wiring through the left lower frame tube, up to the engine. For this, we drill two holes, one to enter in the frame, one near where the alternator will be plugged to the engine.
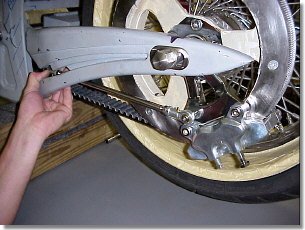
Usually I like rear brakes to be placed in a 12, 3, 6, or 9 PM position around the rotor. Because of the unusual shape of our swingarm, it seems that none of these positions works properly. The rear brake seems to “compete” visually with the flowing lines of the swingarm. After many tries, it seems to me that the 5 PM position is the best. The boys approve. So we custom make an anchor rod running parallel to the belt. A hole is tapped inside the swingarm to connect the brake to the frame.
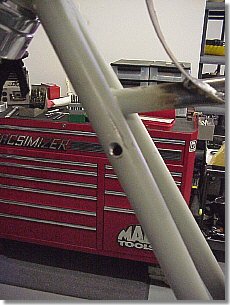
For the rear brake line, a hole is made near the master cylinder with the line jumping to the left side through the frame cross section and back to the rear brake.
Because the bike will have no turn signals, only a headlight and my new L.E.D side mount tag with a run/brake light (picture of the 1st prototype), the electrical system is quite simple.
The ignition/kill switch will be on the left side incorporated in a coil bracket, and the bike will be started with a switch from Cycle Engineering installed directly on the starter.
It’s almost time to have the frame molded and prepared for paint. I review the frame in detail, writing all instructions directly on the frame: welds to be grinded, sections to be reworked with filler, shapes to be molded, etc…
For the first time in eight weeks, Expresso is going to leave the shop for a one-week beauty treatment.
Bikernet–The 15 Year History
By Bandit |
Incredible. It’s been 15 years since we kicked off Bikernet.com. I had the audacity to believe someone might be interested in this history of an eternal search for freedom, the illustrious custom motorcycle holy grail, and the perfect woman. And since we had so many variations of our George Fleming-induced, 15th anniversary logo effort, I thought, what the hell. Let’s put down the searing saga of web site survival, virtually since the beginning of the internet, and the yellow brick road to the world wide web.
Here’s how it started. A crazy man web master approached the offices of Easyriders Magazine almost immediately after the internet exploded onto the scene. He was a long-haired scrawny biker and internet mastermind by the name of Steve Smidlen. Of course, he wanted a small fortune to change the face of Easyriders forever through the internet new age. In 1995, Joe Teresi (the owner of Paisano Publications) tried desperately to sell the company and retire. He didn’t want to invest more cash into the monster, and the internet wasn’t a proven commodity, so he turned the internet mastermind down.
I knew Steve, and of course he pled his case to me. I was a vice president and the editorial director of Paisano’s 14 magazine titles. I was also responsible for the quarterly video and involved in the events, predominately the bike shows and the coverage of the bike rodeos. I did what I could for the internet wizard, so he approached me about starting a web site as an example of his immense talent base and the capabilities of the internet. Since he wasn’t going to charge me an arm and a leg and we were all curious of the web reach, we moved ahead.
We kicked off Bikernet in 1996 with the help of Jon Towle’s black and white illustrations, due to slow-ass modems. We set the site up to sell products, including my paperback books and Bandit’s Bedrolls. We called it Bandit’s Bikernet, and we focused on the one editorial area my boss didn’t care for, fiction, the dreamy side of bikerdom. I didn’t want Bikernet to compete with Easyriders or any of our magazine titles at the time. I stayed true to my word and agreement with the boss to restrict Bikernet to mail order sales, fiction, and Jon Towle’s cartoons. For some unknown reason, the boss didn’t care for the sardonic self-attacking stubby little man with a wry sense of humor.
We banged along for a couple of years and sales were not startling, but brothers seemed to enjoy the site and asked for more. But Smidlen (not sure I have his name correct) didn’t think the vast Bandit empire grew fast enough or paid him enough, and we parted ways, and our crew began the frustrating hunt for a web master who understood business and the internet. I think I started to plug in chapters from my next book, Sam “Chopper” Orwell. At the time, Bikernet fell under the auspices of 5-Ball Incorporated, shared equally by my fifth wife, Rebecca Segal. I was busy as hell with the Paisano empire, Easyriders, and Joe’s efforts to sell the company. Life banged along and Bikernet grew slowly, sort of like notes in a dusty shop manual.
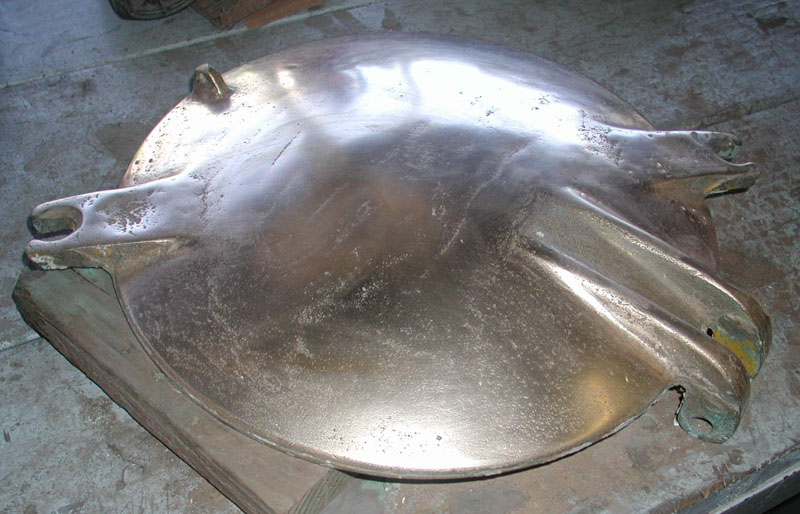
Then in 1999, Joe finally took Paisano Publications public, to become Easyriders Inc., with a partial sale to some heavy hitters who retired with millions from Taco Bell. I received a small bonus for my efforts and decided it was time to retire (escape), seek additional freedom, adventures, write some books and see the world. Sure, the notion was scary, but my timing was right on. Easyriders struggled with a new command structure and ultimately went bankrupt. I blew up my marriage with a psycho redheaded broad who lasted less than a year, and I bought a little house overlooking the Los Angeles harbor in San Pedro and embarked on a new freshly paved metallic road in life.
A couple of Bikernet fans pointed out the need to focus on Bikernet, including an Easyriders staffer, Mike Osborn. Bikernet expanded and I put my panhead desk in my dining room overlooking the main LA harbor channel, and we went to work building this motorcycle web kingdom. We started building bikes and covering every move on Bikernet. Each year, I rode to Sturgis on whatever bike we built. As I wrapped up the 1935 house remodel, I moved into this strange, blue collar union town on the edge of the port, I entered a new phase in life. The girl who said she wouldn’t move to San Pedro moved in, but then grabbed a job at Bartels’ H-D and moved to the more upscale Marina Del Rey.
The year was just turning toward treacherous 2000, and I rode with Agent Zebra to his digs around Point Fermin, then over to Long Beach to see my dear old ma and Dr. Nuttboy, who with his wife, helped me rebuild my home. Other than a couple of folks, I didn’t know a soul in San Pedro, but I loved every minute of my life on the coast. I would get up in the morning and ride to Ramona’s bakery for a muffin and a cup of coffee. I met a wild woman at Cannetti’s fish and chips who would have stormed my abode with her two kids if I didn’t watch my back. Life was good, and I started to build the Blue Flame to ride to Sturgis.
I don’t know if you can imagine this, but I was living in a motorcycle nirvana. I turned one bedroom into a gym and converted my garage into a bike shop. I carefully rolled motorcycles across new refinished hardwood floors in almost every room in the house. Each day consisted of tinkering with motorcycles or writing about them on the web. We started the Thursday news and for a couple of years, there were no images, just text. My psycho ex-girlfriend sent me scurrilous e-mails from time to time, suggesting tech upgrades to the site. I moved slowly, working through the bugs on a tight budget. I published my third book, Sam “Chopper” Orwell, wrote for several mags, including the HORSE, and I consulted for American Rider.
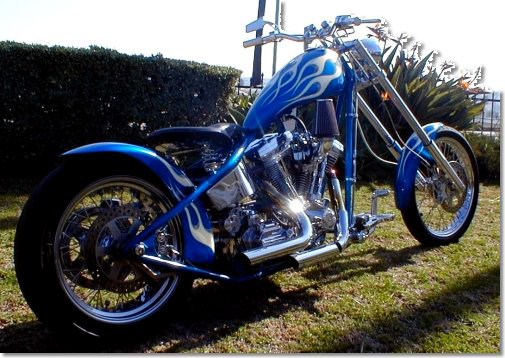
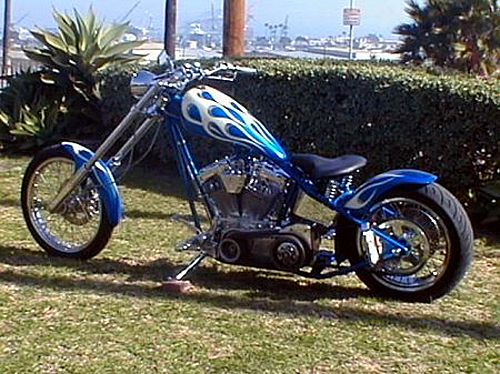
I rode the Blue Flame to Sturgis, but failed to rubber-mount the tank and Randy Aron from Cycle Visions helped me keep it alive to Spearfish. Then Paul Yaffe helped me upgrade the Flame to a better tank, properly rubber-mounted for the long road a couple of months later. We installed a new shapely stretched independent gas tank. What a terrific motorcycle and a great ride. Rumor has it, it’s still on the road in Texas.
Around this time, I met a girl in Harold’s Biker Bar, Nyla, and we started to date. She was a Pedro girl who was married to a mad biker for 15 years, until the abuse put her on the streets and back in Pedro with the support of her massive family of eight brothers and sisters. She lived with her fading, elderly longshoreman father and her three kids in a massive old crumbling clapboard home overlooking the main channel.
As the site began to grow, she worked at Epson Computers, in customer service, and took on part-time bookkeeping duties for Bikernet.
Around 2001, my mom stopped by the little house on Crescent Avenue and told me about her notion to take a ship around the world. At the time, we started on a Buell project to ride to Sturgis. Each time I spoke to my mom, she mentioned the only cruise line to circumnavigate the world. Unfortunately, it went out of business and she began looking into freighter world tours.
After one such visit, I called my 79-year-old mom.
“What’s the deal ma?” I asked in my most respectful tone. “You always mention this trip. Would you like me to go with you?”
“Yes,” she said confidently, as if she had this scenario planned for months. My mother has traveled the world all her adult life. My dad stayed home, drank beer, and went fishing while she roamed through Europe, Russia, and China. We started to make plans for a world tour.
Buell shot here
I was also modifying a Buell into a bitchin’ Joker Machine accessorized hot rod for the 2001 Sturgis run with Dr. Hamster and his girlfriend. It was a terrific ride and we hooked up with the Hamsters in Thermopolis, Wyoming for a party. I had a Wyoming babe in the next town over who always looked after me. She set up a book signing for “Chopper” Orwell, and I slipped out of town. I thought it was just five miles away, but it turned into 35. No problem for the fast Buell to slip through the countryside at over 80 mph.
We had a terrific time, and all the local riders showed up for books and wine in her beauty salon. Since I was involved with the lovely Nyla, I didn’t spend the night with voluptuous Wyoming Deb, stayed sober, and rolled out of Worland at midnight, heading back to the Hamster headquarters at the Holiday Inn in Thermopolis. I scooted along dark roads, comfortable aboard that Buell Lightning, when I spotted a road sign announcing just 8 miles to town. I quickly estimated a five-minute time window at 80 miles an hour. That’s when I spotted the first deer.
It was 50 yards ahead but its stationary eyes still glistened, reflecting the Buell headlight. I immediately backed off the quick Joker Machine throttle when another deer blocked my vision directly in front of me. Unable to even consider applying my brakes, I slammed into its hindquarter. It stopped me dead, totaled the Buell, and I was knocked out by the pavement. I broke several ribs and ended up in a Wyoming hospital for four days. Dr. Nuttboy flew out. Deborah and Dr. Hamster looked after me, and Nuttboy hauled me home.
Within a couple of months, I was back on my feet, flying to Houston with mom, and boarding the nastiest, rustiest tramp freighter in the Houston Ship Channel and prepared for a four and a half-month voyage around the world, with stops at 22 ports.
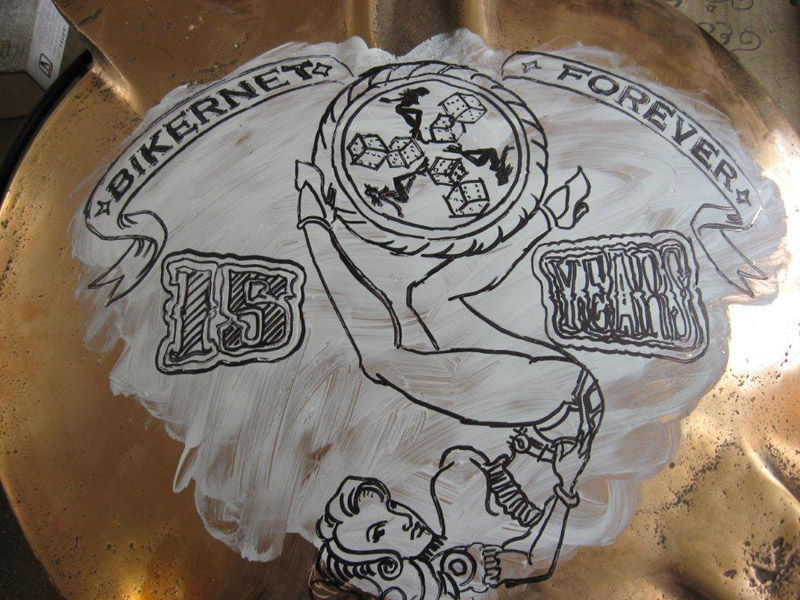
Mom and I spent Christmas in Hamburg, Germany, and New Year’s in Belgium. It was an amazing adventure thanks to the college professor Polish captain and his Polish officers, and a terrific group of Philippino crew members. Of course, we noticed that due to price of domestic labor, there weren’t many American sailors left, and the ship didn’t haul any American products overseas. The tramp freighter left stateside virtually empty.
So began 2002. The captain allowed me to set up a fixed antenna above the bridge, and I continued to write articles for Bikernet, the HORSE, and American Rider, handled the Thursday Bikernet news from afar, wrote World Tour chapters (somewhere here on Bikernet), finished my first Change Hogan novel, Harbor Town Seduction, and wrote chapters for my second Chance Hogan book, about Chance losing his girl to Chinese crime lords.
We passed on Sturgis for 2002 but built the Amazing Shrunken FXR. Nyla became a full-time staffer and we found, for the first time, a web master who understood the business, and was a biker, Jason Douglass. He built web sites for Atlas Frames and Joker Machine, and he set up Bikernet so we could launch our own articles. We were beginning to cook. We could publish the news weekly, publish full techs, bike features and event coverage.
Back in 2002 or early 2003, I was reading The Horse magazine at work and discovered an ad for Bikernet.com. I can still see the ad with the brunette riding the blue chopper with gray flames…tantalizing. My initial exposure to the web site was all it took, I was hooked. The bike reviews, Life and Times of Bandit, the girls, but most of all was the road tales. I read every one, some of them over and over. My favorite was a story called Neighborhood Watch, and another that’s name slips my mind, but the author was named Dowling; it was a Code of the West piece. I ate that shit up and it helped occupy my time working the night shift at the plant. Many a 12-hour shift was spent looking at Bikernet.com on one screen while I also watched the computer controls for the plant on the other. I had gotten so good at my job, the other operators would sleep because everyone knew I was up, either reading a magazine or looking at Bikernet.com.
In December 2004, I graduated from college and started writing more as a hobby now that my time was a bit more open. The kids were getting a little older, so sleeping was easier and I could devote some time to my passion, Harleys. Early in 2005, Bandit sent me an e-mail asking if I’d be interested in writing a few bike features for Hot Bike magazine. Now mind you, while I had been writing for Bikernet for several months, most of my stories were laced with a little bit of bullshit. As a good friend of my dad’s used to say, “Hey, Texans don’t lie. Texans just bullshit.” So, after having a limited amount of experience at writing, mostly bullshit, now I’m getting the opportunity to write for a magazine. Thankfully, there was plenty of great editing, because that relationship stands today and I occasionally still pen articles for Hot Bike today.
Later in 2005, I was able to make my first trip to Sturgis, riding alongside El Bandito himself. I learned a few things on that trip, but the one thing I will always treasure was watching that giant bastard riding through a rainstorm in Durango, Colorado freezing his nuts off! We had a memorable trip, and I have been back three times since. He started a tradition that I plan to partake in as many years as I can afford to.
Throughout the years, we’ve had several adventures, from him teaching me the ropes on judging at the Texas National Bike Show in Galveston to building my first custom motorcycle to give to my Iraqi veteran brother in 2007. We’ve been through lean times where I know every plug I can do for Bikernet is helping him keep the lights on, to the bountiful harvests where, on occasion, I’ll get a check for 20 bucks or so. Either way, I wouldn’t have traded any of it for the world. From the first custom part I ever wrote about, I always had Bandit leaning over my shoulder if I ever got stuck. Because of my relationship with Bikernet and Bandit, I realized I am really just another RUB with a bike, I just happen to have the talent and time to be able to write a few words about it…and that makes me just valuable enough to keep around.
So here I am now, a pathetic RUB who not only writes on occasion for Bikernet.com and Hot Bike magazine; but I am also a professional writer at my day job. I have been promoted to production specialist, where I spend my days writing SOPs, LOTO lists, standards, safety, training, etc. Basically, I have become a “paper biyatch,” so thanks again, Bandit!
I can’t wait to see what we do next at Bikernet, and while I am sure another 15 years seems like forever away, it’ll be here before we know it.
–Johnny Humble
We kicked off the Bandit’s Cantina department, and Nyla came up with the Sunday Post for Cantina members only, so I could never have a free weekend again. Good God! In our little shop, a small two-door garage riddled with termites, we blocked off the large doors to the street and used the small side door for bikes. When we went to work in the shop, we had to move four or five bikes into the back yard. I wanted to enlarge the shop and build an apartment above it, but city codes fucked with my ability to expand.
About this time, we started to modify a 2003 Road King as a celebration of Harley’s 100th anniversary, and to build me a touring bike for long rides. That bike was blacked out and it made several trips to Sturgis, including one with another Road King, the new 96-inch model ridden by Dale Gorman, a Hamster out of Boston. We rode to Sturgis, did our thing, then rode back to Salt Lake, where we hooked up with the lovely Nyla and her youngest son, Kyle. Kyle rode the 96-incher back, but didn’t follow returning instructions and collided with a car, destroying the King.
Nyla: Bandit’s full of crapola here. He and Dale did Sturgis in 2006 on two Road Kings, the blacked out ’03 and a new 96-inch ’06.
Shortly thereafter, we starting customizing a new 2004 rubber-mounted Sportster with the blessing of Harley-Davidson. A series of articles followed on Bikernet and in American Iron. Each modification was installed using primarily H-D components. We built a very slick customized Sporty. Ultimately, the lovely Nyla was intimidated by the power band and the tall sitting position , which of course we enhanced , preferring a Buell Blast instead. She wasn’t riding motorcycles. She was a passenger.
The Sporty collected dust in the shop until a long-time motojournalist from Easyriders was let go and his freelance revenue stream dried up. He was forced to sell his only running motorcycle, so I turned the Sportster over to a brother so he would have a reliable ride.
About this time, or maybe in 2003, we started to build a bike to support the Beach Ride, through George Hayward, the benefactor. It was a Custom Chrome kit bike, and a very sharp build. Dr Nuttboy helped with the operation. Jeremiah Soto dry-walled the shop, and I believe Jon Towle helped. I had been on the Beach Ride Board for years and always supported it and the Love Ride. I discovered something vast and wonderful about the Interplanetary Bikernet nerve center based in a large brass base anchored to the deck, and topped with a hazy glass globe. It told me that the Bikernet Empire could be used for the good of all bikers, so a code was born out of the globe’s radiant light.
We would do whatever we could to keep motorcycling alive, free, and the industry successful. On a daily basis, we helped spread the word, worked with and supported motorcycle rights groups, and fought for less legislation. Why not? What could be more beneficial to the world than more freedom? We started publishing the National Coalition of Motorcyclist’s Coast to Coast Legislative News, authored by Bill Bish, on a monthly basis. Right around this time, the one major drawback to internet access was replaced. The slow-ass modem was upgraded through cable modem supplied by the local SBC cable TV provider. Suddenly we could publish at warp speed. We thought that it would allow us to launch articles quicker and give us more time to chase broads and ride. Not so; it meant we could launch two and three articles a day on Bikernet and steam started to pour from our window. We were cookin’.
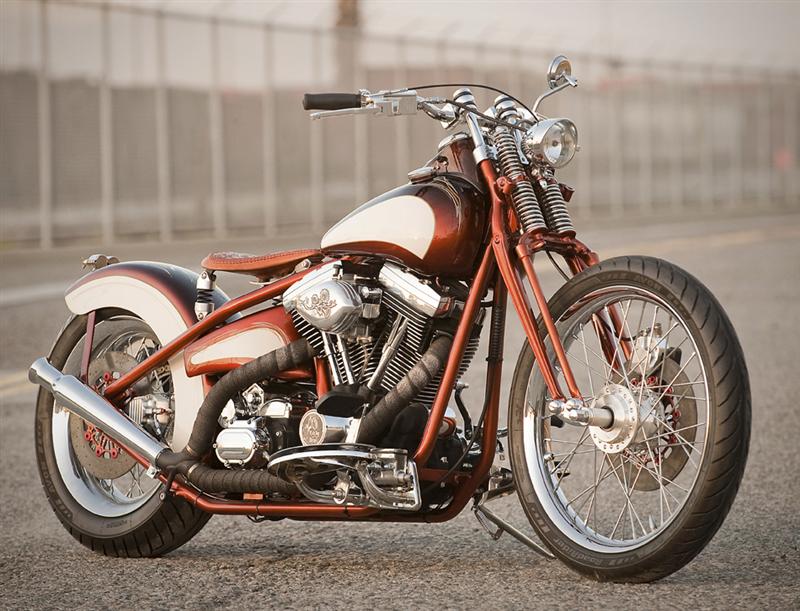
While shooting the Road King for American Rider on a back streets in Wilmington, the next town over and directly behind the port of Los Angeles, with famous photog Markus Cuff, I discovered an old rundown hotel for sale on the corner. An old man gave me a tour of this 1923 clapboard, lathe and plaster hotel. It had been gutted in 1981 and portions were refurbished to become an industrial building and a fish processing plant. The entire building was stuccoed and vast concrete rooms created. As I walked through this wild cavernous hideout, my imagination went wild.
Of course, I had to convince the lovely Nyla that this would be a step in the right direction. She was born in a small home in Wilmington, and never looked back. Most Wilmington residents drink margaritas and dream of how they can escape this third world country between Long Beach and San Pedro. It’s as industrial as a town can get. It’s bordered by the Port of Los Angeles, the Port of Long Beach, oil refineries, power plants, train depots, and more 18-wheelers roll through the streets daily than cars. Since this is not a white bread, upscale community, over 85 percent of the population is Hispanic. Hell, longshoremen haul ass to the dreaded Wilmington union halls daily to pick up their jobs, then scream out of down.
Since I was somewhat involved in some community efforts in Pedro, I made a couple of phone calls and was introduced to the Wilmington Waterfront Development Committee. I discovered that this building was at the corner of every future corridor to the water project being discussed. I made an offer. Nyla foolishly agreed, then panicked. We moved in and a new adventure began, plus we started to develop the Bikernet Independent Motorcycle Noise Study, since bikers were being harassed with roadblocks in Pedro and across the country. Suddenly we had a joint that allowed us a large shop. I was awarded the Silver Spoke award by the National Coalition of Motorcyclists, then inducted into the Motorcycle Hall of Fame in Sturgis for God only knows what. I have always supported the Sturgis Museum.
About this time, Jesse James called and asked me to be on the 50th Anniversary Monster Garage Team, building a wrecked Softail into a mighty fine custom chopper. The team was made up of Mark Rowe, the master welder and frame designer, John Reed the master Custom Chrome builder and parts designer, Don Hotop, one of the finest custom bike builders in the country, Carl Morrow, the master engine builder, who doubled the horsepower of this twin cam, and me, a so-so mechanic. I was the guy who recommended Jesse for his first Discovery Channel gig. We had a blast and built one very cool chopper.
A Word from the Bikernet Official Copy Editor :
Shit, when did I get involved with Bikernet? Must have been 2004 or 2005 near as I can figure. Like the Robert Hunter-Jerry Garcia song, The Wheel says, “You can’t slow down and you can’t stand still; if the thunder don’t get you, the lightning will.”
The last economic downturn about ten years ago found me divorced and unemployed for a year back in Allen, Texas, but I got the itch to ride again and bought a 2000 XL1200C Sportster anyhow. A couple of contract consulting jobs came my way that summer and put me in Columbus, Ohio. I swapped the Sporty for one of those rare (not), black, 2003, 100th anniversary edition FXST.
Jobs took me back south to Baton Rouge, Louisiana; north again to St. Louis, southeast to Raleigh, North Carolina, where I picked up a 2007 Road King. Currently, I’m still single and living and working in Colorado Springs.
Me and my big mouth; back in 2004 or 2005, I sorta broadsided Bandit one day about sloppy editing and missed deadlines. Next thing I know, I’m editing tech features, Cantina episodes, World Tour chapters, Building a Bonneville Salt Flats Racer, Harbortown Seduction, Bandit’s biography of the international president of one of California’s 1% clubs, and contributing articles of my own now and then.
Mostly, I do it for fun; it’s a welcome respite from the insufferable pricks and pompous asses that I have to deal with in my real job as a proposal manager for a defense contractor. But it has its perks, too, and it allows me the creativity that’s lacking when you make your living writing, editing and managing dry government documents.
And somewhere before and during all of it, I left an ex in Texas, lost a few girlfriends in Louisiana, Missouri and North Carolina, slid on my ass down a patch of black ice in Ohio, got splattered with bird guts on a Kansas highway, and got to ride and party with a lot of kick-ass brothers and sisters from around the country. On the flip side, I buried a father and a few friends, too, but I choose to celebrate their lives rather than mourn their deaths.
So, yeah, it’s been a helluva ride. I’ll be 60 next fall, and I’m looking forward to riding and celebrating the next 15 years with the Bikernet crew.
– Bruce Snyder, 2011, Colorado Springs, CO
In 2005, after spending a year as the editorial director of Hot Bike, Street Choppers, and another Primedia title, I started on the Sturgis Shovel, my first ground-up project in the new Bikernet Interplanetary Headquarters. We rode to Sturgis.
In 2006, I built the first Sportbike Panhead, with a partial Custom Chrome, John Reed-designed kit bike and an Outlaw 120 engine from Accurate Engineering, and we decided to ride to Bonneville. I met Valerie Thompson, a professional drag racer and a very pretty face in the motorcycle racing community. She wanted to race Bonneville, so I offered her my ride, the Salt Shaker. We didn’t know what the hell we were doing, but we did it. I believe our first pass grabbed us a speed of 152 mph and I was impressed. As it turned out that year, we took home a world land speed record at 141. That same year, we watched the World Land Speed Record for motorcycles broken for the first time in 16 years, from 321.5 mph set by the Easyriders team in 1990, and I was on that team. Interesting. I believe Dennis Manning took the record at about 345 mph. What a year! We were hooked!
After Sturgis 2006, I jumped into Dr. Hamster’s ’53 modified Lincoln and we drove to the bottom of Mexico, then raced in the 2006 LA Carrera PanAmericana vintage road race to the top of Mexico. Then with our 2nd class award in hand, we drove home. All the other teams had rigs, trailers, and tool sheds. We were the only bastards to arrive in our car and everyday, we threw our luggage in the back and went racing. What a ride!
In 2007, we decided to build an aerodynamic bike to fit Valerie, and go after a 200-mph Worlds Fastest Panhead Record. At the same time, Jeremiah Soto rolled into the shop and started his Shovelhead bobber project, and we went at it like mad dogs, building his bike and the Panhead. We hit a top speed at Bonneville at over 160 mph and set another partially streamlined record at around 156 mph. We knew the bike was capable of much greater speeds, but the salt conditions prevented strong runs.
In 2008, I finally published my first Chance Hogan book. We were also contacted by Tim Remus of Wolfgang Publishing to publish a book about our 2007 run to Bonneville, based on the rough chapters about the build on Bikernet. Every year, we were fortunate enough to sit back and make a list of goals we wanted to accomplish. As we rolled into 2008, I was turning 60 years old. I rode to Monterey with Billy Lane and the boss of Sucker Punch Sally Bikes for a vintage meet. Billy traded me a 1926 OHV 350 cc Peashooter engine for my 1913 Pope engine, and we started to build a vintage single cylinder engine bike for Bonneville the following year.
But the stars weren’t aligned for the 5-Ball Racing Crew in 2009. Barry Wardlaw forgot to send us a set of rings for the Assalt Weapan and we couldn’t take it back. We rolled to Bonneville with just the Peashooter and Ray Wheeler’s turbocharged Dyna. He had handling problems and we blew a head gasket with 14:1 compression. We had a great time, but stumbled home early.
I also jumped a jet for the annual meeting of the minds meeting produced by the Motorcycle Riders Foundation, a Washington D.C.-based legislative group that’s the federal arm of motorcycle rights groups across the country. Bikernet presented several efforts, including our popular Independent Motorcycle Noise Study, a freedom movie effort, and our effort to start an aftermarket motorcycle rights group to support the industry. We are a sponsor of the MRF and run their news releases often in the Bikernet news. We publish legislative reports from any state or national organization. Actually, Rogue, a brother and freedom fighter I’ve known since 1972, has sent me reports daily since 1999 from all over the country. He is now in the Sturgis Hall of Fame and still rides like a madman at over 70 years of age.
During this period, every extra dime we could muster went into refurbishing one room at a time in our vast 10,000-square-foot building. I started to build a Crazy Horse Indian engine, 5-Ball Factory Racer with primarily Paughco parts. The frame was initially designed by Rick Krost of US Choppers and he was having a problem getting his board track frames built, so I introduced him to the legendary Paughco family, and immediately he had frames whenever he needed them.
Somewhere along here, Mike Jones called me and invited me to be apart of his movie effort, Born to Ride. I tried to memorize a handful of lines and play a motorcycle journalist, asking the hero questions in an interview. This summer, the biker film will be released in Phoenix. Branscombe Richmond plays one of the slap-stick bad guys. Mike is already working on another film.
“Bandit was always the one who always got away, the one they could never catch or censor. May Old Glory wave over the Bikernet headquarters another 15 years.”
In 2010, we suffered through the economic downturn, but completely rebuilt Bikernet. I moved it to a new location in Columbus, Ohio within a family operation. They oversee over 300 web sites and said they could handle the vast Bikernet empire. We are still grappling with them to upload all of our features onto the new platform. Sure, it’s better, with more bells and whistles, but it means more work. We could work on this bastard 24/7. When one of the bosses, Joe, started to monkey with Bikernet, he called me.
“This site is amazing,” Joe said. “We have designed sites with millions of dollars and they don’t have a fraction of your content or your readership numbers.”
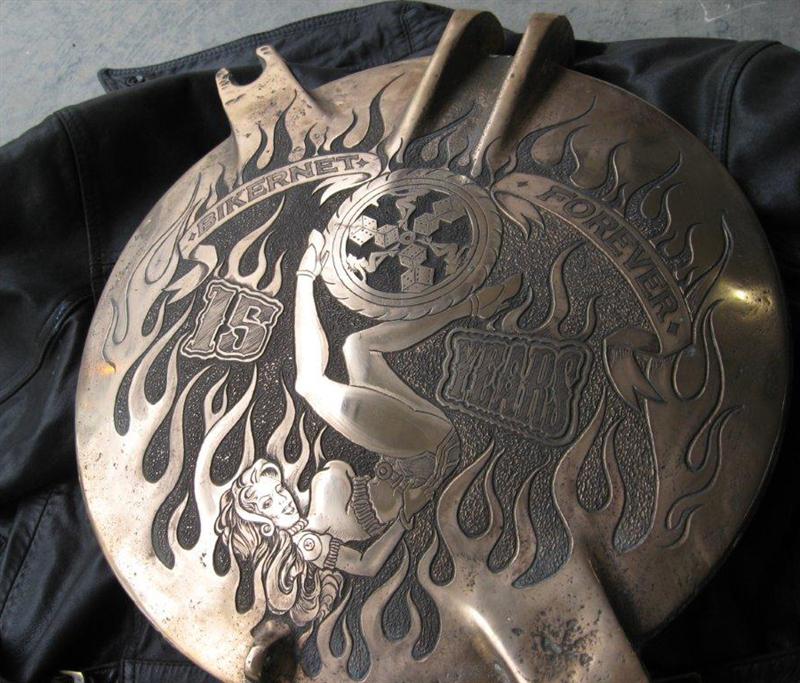
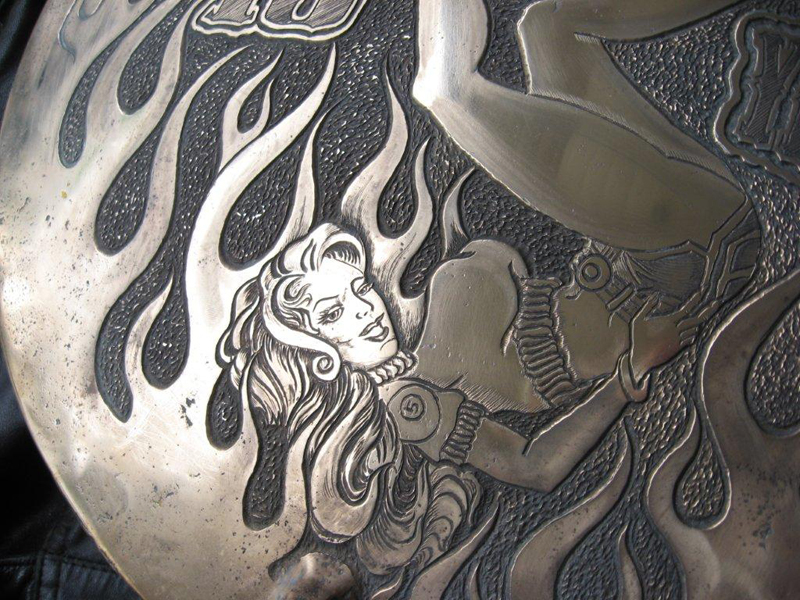
Every year, we made a list of adventures and goals, and flew at them like rabid dogs. In 2010, I was approached by Motorbooks to write a book about a 1%er, the international president of a club for 24 years. I was still writing features for American Iron, the Horse, Cycle Source, and Heavy Duty in Australia. A handful of righteous brothers in the custom motorcycle business, including Kiwi Mike and Billy McCahill were still trying to assist the industry by forming an aftermarket motorcycle organization to support motorcycle rights and motorcycle freedoms. Nevada is trying to repeal their helmet law. Other states are trying to pass helmet laws. California is trying to smog test motorcycles, and the noise battles are being fought all over the country.
I try to spread the word as much as possible, and we even considered trying to make a film about freedom in this country wrapped around motorcycling. That’s another adventure we may embark on as we move forward. I may have slipped in the above timeline and scrambled the dates, but that’s basically the story. I don’t want to go into the goals for 2011, since you see them mentioned every week on Bikernet, but I would like to thank about a thousands folks for their support, leadership, talents, and contributions over the years. I know I’m going to forget someone, but this is the internet, not a page in a magazine. We can correct or add to any aspect of an article, anytime night or day. Just ping me and I’ll make it happen–I hope.
I was interviewed last week by a writer from Random Lengths, the local newspaper. He mentioned that I was blessed to have created a pure custom motorcycle paradise and live smack in the middle of it. If anything is green, Bikernet is. We don’t destroy trees; we don’t even commute to an office. It’s fuckin’ amazing. Thanks for stickin’ with us, and maybe we’ll hook up on the ride to Sturgis 2011.
Bob T.
Chris T.
Jason Douglas
Chris Kallas
Doc Robinson
Johnny Humble
Paul Garson
Kirk Willard
Jeff Hennie
Sin Wu
Jeremiah Soto
Jon Towle
Peter Linney
Markus Cuff
Rebecca Segal
Uncle Monkey
Nyla Olsen
Eric Herrmann
Ray C. Wheeler
Cigar Marc B.
Joe Tripp
Tedd T.
CarlR
Bruce Snyder
Ladd Terry
River Rat
Vickster
Patty Hamster
Myron Larrabee
Agent Zebra
Tramp Scotty
Uncle Monkey
Barry Wardlaw
Holger Mohr
Richard Lester
Pepper Massey
Mike and Vicky Pullin
Jim Gufra
Rick Krost
Ron Paugh
Danny Gonzalez
Lorenzo Lamas
Branscombe Richmond
Edge
Robin Hartfiel
Bikernet Betsy
Genevieve Schmitt
Paul James
Charles P.
Jenn Gruber
Michelle McCarthy
Lisa Pedicini
Buster Cates
Wordman
Frank Kaisler
Dick Allen
Quick Throttle Art
Ian
Donna
Arlin Fatland
Marilyn Bragg
Charles Young
TBear
JoAnn Bortels
Buckshot
NCOM Coast To Coast Legislative Update for May 2011
By Bandit |
Incredible. It’s been 15 years since we kicked off Bikernet.com. I had the audacity to believe someone might be interested in this history of an eternal search for freedom, the illustrious custom motorcycle holy grail, and the perfect woman. And since we had so many variations of our George Fleming-induced, 15th anniversary logo effort, I thought, what the hell. Let’s put down the searing saga of web site survival, virtually since the beginning of the internet, and the yellow brick road to the world wide web.
THE AIM/NCOM MOTORCYCLE E-NEWS SERVICE is brought to you by Aid to Injured Motorcyclists (A.I.M.) and the National Coalition of Motorcyclists (NCOM), and is sponsored by the Law Offices of Richard M. Lester. If you’ve been involved in any kind of accident, call us at 1-(800) ON-A-BIKE or visit www.ON-A-BIKE.com.
NCOM COAST TO COAST BIKER NEWS
Compiled & Edited by Bill Bish,
National Coalition of Motorcyclists (NCOM)
WASHINGTON STATE ENACTS NATION’S FIRST ANTI-PROFILING LAW
Motorcycle riders routinely report being profiled by law enforcement, but a new law in Washington State is intended to prohibit police from singling out bikers for stops without clear and legitimate reason.
Modeled after a 2002 state law outlawing racial profiling by police, the nation’s first “anti-profiling” bill passed unanimously through both the House and Senate, and was signed by Gov. Chris Gregoire on April 13. Sponsored by Rep. Steve Kirby (D-Tacoma), the new law will force local law enforcement agencies to adopt a written policy designed to condemn and prevent the profiling of motorcyclists, and it institutes training to address the problem.
Motorcycle enthusiasts presented compelling evidence to legislators, including a video of a state trooper crawling through bushes near the Legislative Building in Olympia two years ago and writing down motorcycle license plates while bikers were holding their annual “Black Thursday” legislative rally and lobby day.
Outsiders M/C member David “Double D” Devereaux, spokesperson for the Washington Confederation of Clubs and US Defenders of Washington State, testified in Olympia that almost every member of every club, and even motorcyclists who aren’t in clubs, has been profiled. He said many lawmakers were unaware of the problem until they saw the video of police gathering information on the bikers as they were inside the Capitol building ironically seeking sponsorship for a bill that would stop motorcycle profiling.
Also lobbying on behalf of the bill was Donnie “Mr. Breeze” Landsman, Legislative Affairs Officer for ABATE of Washington, who told The News Tribune that he’s been denied service at restaurants for wearing a bandana and a leather vest; “Motorcyclists aren’t looking for special rights,” Landsman told the newspaper. “We want the same rights that are afforded to every other section of the population as American citizens.”
Double D and his club brother Jeff “Twitch” Burns, who produced an 86-minute video that chronicles the growth of the emerging anti-profiling movement within the motorcycling community, reported their success at the Patch Holder Meeting during the recent NCOM Convention in Albuquerque, N.M., to the resounding approval of bikers rights activists and COC reps attending from all across America. “This is something that could be done in every state,” Double D told the enthusiastic crowd…and should be.
STATES COMBAT MOTORCYCLE-ONLY CHECKPOINTS
Calling motorcycle-only roadblocks discriminatory and unconstitutional, ABATE of California is pushing a bill that would ban state and federal funding of such so-called “safety checkpoints”.
New York and Georgia have initiated roadside barricades under the auspices and guidance of NHTSA to coral motorcycle riders en route to major motorcycle events to check paperwork and equipment for violations, and for other illegal activity.
AB 1047, authored by Kevin Jeffries, Vice Chairman of the Assembly Transportation Committee, would prohibit the CA Office of Traffic Safety (OTS) from issuing grants to law enforcement agencies to stage Motorcycle-Only Checkpoints and also require the OTS to conduct audits of the safety checkpoint grants to insure that law enforcement is complying.
Similarly, North Carolina is currently considering two bills (H375 & H381) aimed at preventing law enforcement agencies from establishing patterns for vehicle stops at checking stations based on a particular type of vehicle.
In Congress, Rep. Tom Petri (R-WI) and some of his colleagues have authored legislation to de-fund the checkpoints. US House Resolution 904 would prevent the US DOT from providing funds to states which would be used for motorcycle roadblocks.
Motorcyclists across the country are also awaiting a court ruling on the constitutionality of the New York checkpoints, being challenged by N.Y. Aid to Injured Motorcyclists (A.I.M.) Attorney Mitch Proner, which could wind up on the docket of the U.S. Supreme Court.
MOTORCYCLE FATALITIES CONTINUE DECLINE
Motorcycle fatalities declined in 2010 by at least 2%, according to a new state-by-state report released on April 19 by the Governors Highway Safety Association (GHSA).
Based on preliminary data, GHSA’s motorcycle fatality report projects that deaths declined from 4,465 in 2009 to 4,376 or less in 2010. The projection is based upon data from 50 states and the District of Columbia for the first nine months of 2010. The decline comes on the heels of a 16% drop in 2009, which followed 11 straight years of steady increases in motorcycle deaths which mirrored annual increases in motorcycle sales and registrations.
GHSA is projecting declines in approximately half of the states, with notable declines in many. In Texas, for example, based upon data for the first nine months of 2010, motorcycle deaths are expected to be down 16%, while Oregon and Oklahoma are down 27% and 30%, respectively.
But fatalities had started to climb back up during the last three months in the study, prompting fears that the improving economy and surging gas prices will lead to increased motorcycle travel and thus increasing exposure to risk.
NHTSA UPDATES MOTORCYCLE HELMET STANDARDS
The National Highway Traffic Safety Administration has updated the federal motorcycle helmet standards (FMVSS 218) in an attempt to stop riders from wearing non-DOT approved “novelty” helmets. The new standard does not affect the construction of helmets directly, but changes the way they’re labeled to make it more difficult to mimic DOT compliance certifications.
Effective immediately under the final rule issued May 13, helmets that conform to Federal Motor Vehicle Safety Standard No. 218 will carry a sticker with the manufacturer’s name, the helmet model and the words “DOT FMVSS No. 218 Certified.” The move to make non-compliant helmets harder to sell comes after the number of riders sporting novelty helmets increased dramatically in 2010 over 2009.
According to NHTSA statistics, in 2010, only 54% of motorcyclists wore a DOT-approved helmet. Around 14% wore a novelty helmet, and 32% rode without a helmet. In 2009, those numbers were 67%, 9% and 24%, respectively. In 2010, 75% of riders who did elect to wear a helmet wore a DOT-compliant one. In 2009, that number was 86%.
NHTSA says 5.2 million helmets are sold annually. Twenty states require all motorcycle riders to wear helmets, but only 13 states specify that the helmets must meet federal standards.
“DEAD RED” LAW ALLOWS RIDERS TO RUN STOPLIGHTS
Motorcyclists in several states have been given a green light to run red lights, and now riders in Kansas can proceed with caution through a stuck signal if it has failed to change green within a reasonable amount of time because the signal has malfunctioned or failed to detect the cycle.
HB 2192, The Dead Red Law, has been signed into law by Governor Sam Brownback and goes into effect June 1 for intersections across the state with sensors. Traffic sensors imbedded in the roadway normally tell the light to change when a vehicle approaches, but motorcycles often aren’t heavy enough to trigger it, argued ABATE of Kansas in support of the legislation.
The measure was packaged with a series of road-related measures, including provisions raising the state’s maximum highway speed to 75 mph.
Nine other states currently allow motorcyclists to proceed through a signal that fails to detect their presence, and similar legislation is being considered in Illinois where HB 2860 passed the House 104-0 and is awaiting further action in the Senate.
MOTORCYCLE SALES STOKED BY GAS PRICES
Motorcycle sales in the U.S. rose 7.2% during the first quarter OF 2011, compared with the same period a year earlier, says the Motorcycle Industry Council.
In its retail sales report, which tracks sales among the 18 leading brands sold in the U.S., the industry trade group said scooters posted the biggest sales increase of nearly 50%. Sales of dual-purpose motorcycles, which are designed for highway and off-road use rose almost 25%, attributed in part to the segment’s overall fuel efficiency.
In a separate but related report, a recent survey of Harley-Davidson dealerships suggests that retail sales improved in the first three months of the year. According to an analysis by Raymond James & Associates, 55% of the dealerships surveyed said they had a year-over-year sales increase in the quarter, and nearly all reported that inventories were “ideal” or “light”.
The MIC also reported that tire sales, which it says are an indicator of motorcycle use, also rose in the first three months of the year. Motorcycle and scooter tire sales increased 29%, while sales of tires for on-highway bikes rose 28% and scooter tires jumped 49%.
The industry council’s owner survey estimates the number of motorcycle miles traveled rose 5% to 27.6 billion miles from 2008-09. The percentage of U.S. households with at least one motorcycle grew to 6.8% in 2009 from 5.4% in 2003.
E-CYCLE GROWTH FORECAST
More and more motorcycles and scooters powered by electricity are hitting the road, and some experts predict that the number of electric two-wheel vehicles could swell to more than 100 million worldwide within the next 5 years.
Currently, there are about 17 million electric motorcycles and scooters on the road, but a new study by Pike Research shows that that the global market could expand to more than 138 million by 2017.
“Electric motorcycles and scooters have strong appeal for many consumers,” says senior analyst Dave Hurst. “They are relatively low cost to own, do not take a lot of space, and are easy to maintain.”
Electric motorcycles are becoming more capable every day. Chip Yates recently set a land speed record with his electric motorcycle, reaching nearly 200 mph, and the TTXGP racing series was just officially sanctioned by the FIM.
VICTORY FOR INDIAN
America’s oldest motorcycle brand now has a new owner. Polaris Industries Inc. (NYSE: PII) has announced the acquisition of Indian Motorcycle, adding one of motorcycling’s legendary brands to its stable of Victory cruiser and touring bikes.
Polaris, which has manufacturing plants in Roseau, Minn., and Spirit Lake, Iowa, will close down the Indian Motorcycle production facility in Kings Point, N.C., and move all production to Spirit Lake.
Polaris said it hopes to capture a bigger share of the $11 billion heavyweight cruiser market by operating Indian as an independent business unit, combining Polaris’ “engineering acumen and innovative technology” with Indian’s “premium brand, iconic design and rich American history.”
RIDE TO WORK, WORK TO RIDE
Every year more and more riders are finding cycles and scooters to be an economical, efficient and fun way to commute. Because of this, the 20th annual worldwide Ride To Work Day, scheduled for June 20, 2011 is expected to be one of the largest ever.
On Ride to Work Day, the practical side of riding becomes more visible as a large number of America’s 8,000,000 cycles and scooters are ridden to work, which helps to demonstrate how these vehicles make parking easier and help traffic flow better. Studies have shown that across equal distances, commuting motorcyclists reach their destinations in less time than those using automobiles, and that motorcycles and scooters consume less resources per mile, and that they take up less space on roads.
For further information and promotional materials, visit www.ridetowork.org.
QUOTABLE QUOTE: “One man can make a difference, and every man should try.”
–John Fitzgerald Kennedy (1917-1963), 35th US President
Flathead Indian Engines
By Bandit |
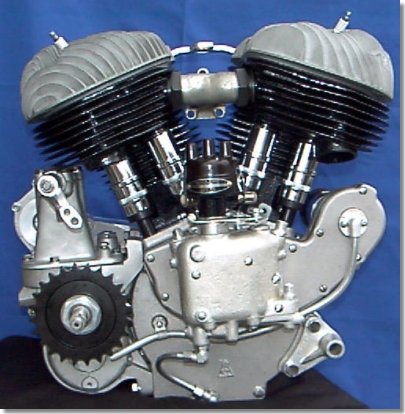
Kiwi is proud to introduce the worlds first operationalproprietary Indian engine and transmission powerplant. The first new Indianengine since the factory closed its doors in 1953. We utilized our proprietarycomponents and built it larger than stock to 84 cubic inches (80 and 74-inchversions also available).
We call this the “Kiwi Integrated Engine” which means that all of thecomponents are manufactured by Kiwi. This characteristic guaranteesthe fit and operationalperformance of each and every part.
Since we have been manufacturing all of the internal components for sometime and been test riding the heck out of the stuff, this task was alreadywell proven.
The biggest benefit of taking an integrated approachis that the customer can feel confident of having absolutely thefinest quality engineavailable.
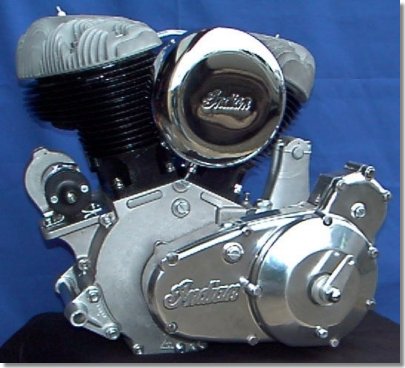
Price for complete engine less oil pump $7499.00 (unassembled $5999.00).Price with transmission and primary to follow. We will also offer the enginein short block form without cam parts. Sub assemblies will also beavailable including complete cylinders with valve covers etc, ready to bolt to an engine.
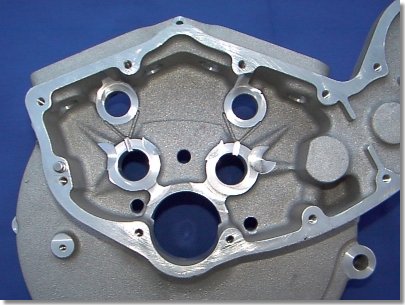
The central new part of our engine is of course the engine cases.These cases look outwardly identical to stock cases, but have been improvedconsiderably over stock. Cases are1948-53 style and are available now with matched cam cover for anintroductory price of $999.00.
We are not kidding when we say we test ride the heck out of our stuff.We put serious miles on every part we make before we release it for sale,and the new engine is no exception.
Even if the prototype powertrain has been assembled for some months,we wanted to make absolutely sure everything was perfect before releasingit.
Our slogan says “Quality Parts, Built to Ride” and we stand behind that!
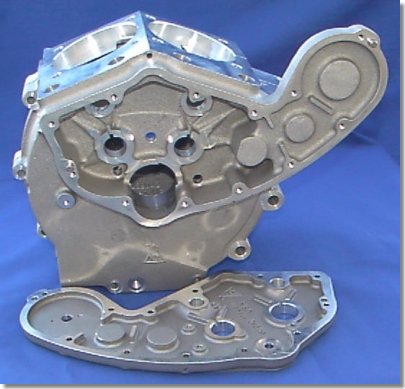
Cases come stock to accept 84-inch strokes and are fully CNC machined.
Aluminum is a high end 356-T6. A 65% increase in structural strengthover original cases and that’s before our structural improvements.
Drive housing external boss increased from 2-5/8 to3-1/4-inch.
Drive housing inside boss increased from 2-5/16 to3-1/4-inch.
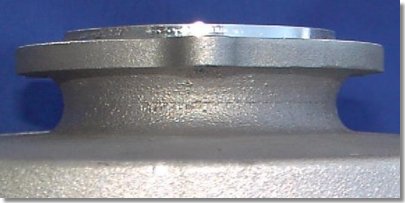
Drive side bearing oiling is aided by a windage trapto ensure a constant supply of oil.
Integral cast in dry sump pick up.
Case walls thickened and baffles have been strengthenedto suit 84-inch strokers.
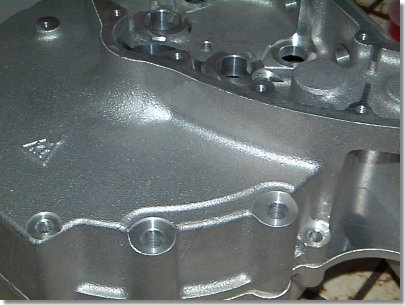
Cam chest wall increased 1/16-inch.
2 sets of baffles to reduce oil splash and mist ontothe breather.
Case to cam cover gasket surface area increased up todouble in critical areas.
Both case and cover are matched and line bored.
Engine to primary mounting flange threaded for a cleanlook (no untidy nuts).
All housing and bushing bores are line bored and canbe enlarged to accept needle bearings.
Crankcase half sealing surface increased upto 75%.
Dowel pins for accurate case half locating. One ofthe benefits was to eliminate the radial locator groove so as to increasecase half sealing surface area.
Breather location can be changed from cam cover toback side of crankcase for a more visual appealing finish.
Front engine mounting bosses are sculptured for a matchedand finished look
Polished case option is available.Patterns were computer recreated utilizing CMM technology. The foundrywe use is one of the top within the aircraft, automotive, motorcycle andracing communities. The machine shop is a major manufacturer to the otherAmerican motorcycle company so fit and finish is a slam dunk deal. Caseand cam cover sealing surface improvements were consulted by James Gasketsand the other American motorcycle company.
SPECIFICATIONS:
42 degree V twin, air cooled.
Bore: 3-1/4″.
Strokes: 4-7/16″ (74-inch), 4-13/16″ (80-inch) and 5-inch (84-inch).
Kiwi forged pistons, three ring design with three piece oil ring.
Kiwi forged 4340, H-beam connecting rods.
Kiwi/Truett and Osborn flywheels.
Flathead design, hardened valve seats, stainless steel valves, hardchromed stems, 2-inch diameter heads.
Gear drive twin cam.
Billet Bonneville cams.
Billet Bonneville cam followers.
Positive Kiwi pinion shaft oil seal.
Black oxide push rod guides.
Chrome valve covers with silicon o-ring seals.
Chrome wide flange cylinder base nuts.
Stainless steel hardware.
James Gaskets.
Cam cover accepts cast iron or aluminum oil pumps.
Price for complete engine less oil pump $7499.00 (unassembled $5999.00).Prices with transmission and primary to follow. We will also offer theengine in short block form without cam parts. Sub assemblies will alsobe available: Complete cylinders with valve covers etc, ready to bolt toan engine.
Visit http://www.kiwi-indian.com for more details.
In Tech We Trust
By Bandit |

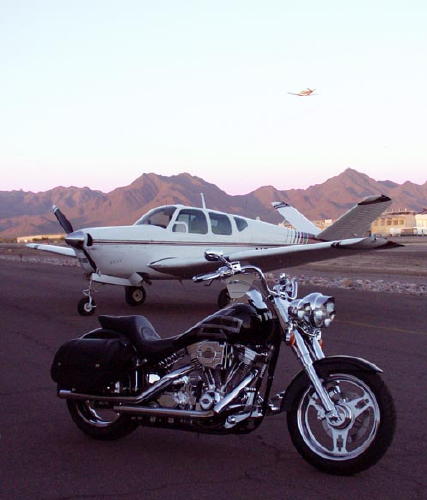
If you ride a motorcycle, you have a relationship with a machine.Your motorcycle will bring you years of joy and satisfaction if youhave a positive relationship. Just like the association with yourspouse, kids or buddies; the amount of energy you put into yourmechanical connection with your motorcycle directly correlates withyour level of enjoyment. If you aren’t a mechanic, you’ll need anassociation with a trustworthy motorcycle technician. Your life ison the line every time you throw your leg over your bike, so yourdependence on your chosen tech is vitally important.
“In the wind”. This Airplane/Motorcycling analogy is right on themoney. It describes the feeling you relish in flying down the asphalton your two wheeled freedom machine. It’s a cliche’ phrase that isused to describe the experience that you have when you’re out on theopen road with the wind in your hair. It describes the exhilarationand thrill when your scooter is functioning smoothly.
Everyone is aware of the eminent dangers associated with riding amotorcycle; just ask your mom. That’s part of the thrill involved.Nobody I know wants the “thrill” that a mechanical failure can bring.With motorcycles, unlike airplanes, you have the option to serviceyour machine on your own. Did you know that even if you are a masteraviation technician, the FAA (Federal Aeronautics Administration)does not allow you to service your private airplane yourself? Theirrestrictive reasoning prevents cutting corners to save a buck or twoon routine airplane maintenance. If you did, you’d risk your ownsafety, the safety of your passengers and others who could be injuredif a mechanical failure occurs during flight– Otherwise known as”mechanical Russian Roulette”.
Before each flight an airplane pilot will physically walk aroundhis craft and inspect his plane for basic safety issues. Amotorcycle rider should be no less vigilant. User-friendly checks oflighting, horn function, tire pressure, and oil levels should be aroutine. Usually at 2500-mile intervals the manufacturer requires a”maintenance service” to sustain your motorcycle’s warranty, safetyand reliability. This requirement dictates a periodic service, anditís much more than just an oil change.
Most people who ride dont have all the specialty equipmentrequired to properly maintain and service their modern motorcycle.Even certified automotive mechanics usually do not have the tools orexpertise to handle a typical 10,000-mile service on aHarley-Davidson motorcycle. So chances are, no matter how crafty youare in the home-shop or garage, you’ll end up requiring the servicesof a motorcycle repair facility sooner or later. This is where the”relationship” starts, and I’d like to provide a littleinformation on how to foster a positive relationship with a shop ortechnician that you’ll entrust with your safety.
Just like a certified aviation technician, a certified motorcycletechnician should consider your safety as priority one. The key toany relationship is trust. If you fell and shattered your wrist,would you trust a medical student to set your bones correctly so yourwrist would function as good as new? Or would you rather have aboard certified orthopedic surgeon with several years of experience.This isn’t such a far-fetched analogy when you consider how high thestakes are when you’re zipping through traffic at 80 mph. You areentrusting your life to an individual holding a wrench. If you arecomfortable with having your buddy’s friend who just enrolled inmotorcycle school work on your bike in his backyard, so you can savesome dough, that’s great. Then you should be aware that you wouldalso settle for that first year medical student to set your bones ifyour bike goes down because your budget-mechanic forgot to properlytorque your axle nut.
Everyone is human, and even the most highly experienced andconscientious mechanic will make a mistake occasionally. However, aquality facility will own up to its errors and make it right whenthey screw something up. Who knows if your buddy’s friend workingout of his home garage will do the right thing when he accidentallydrops a wrench on your fender and gouges your fresh custom paint job?A penny saved isn’t always that penny earned.
Take the time to visit several shops and investigate each. Meetthe people who work there and who own the operation. Find otherriders and ask them who they intimately trust to work on their bikes.Find out how much experience and education the mechanics have Don’tbe intimidated by the whole razzle-dazzle speed-secrets that somemechanics will throw at you. If you don’t understand what they aretalking about, just ask. If you cant get a straight-forward answeror solution to any mechanical problem, run away. These really arejust machines. Machines need maintenance and will break. There’s nomagic wand to repair your bike. It takes knowledge, skill, and thepersonal awareness of the technician to deliver a quality of serviceon which you stake your life. That’s the key. Find a technician orshop that you feel has your best interests in mind. Sometimes therepairs required are not cheap, but neither is that ride to thehospital in the helicopter from the middle of nowhere.
If you don’t respect the facility thatís working on your bike,find another. Remember that commercial from a few years back, theone that asked the guy if he was in business for ëfun or profití?Believe it or not, serious motorcycle businesses are run for aprofit. Thereís many a shop that has been opened because the ownerthought it would be fun, but then discovered that fun does not keepthe doors open for very long. Thereís an old adage that ìlong afterthe sweetness of cheap has vanished, the sour taste of poor qualityand inferior craftsmanship lingers on.î Look for a shop that is runprofessionally. You should get a complete estimate that fullyexplains the cost of all your repairs before you leave your bike forany work. If there are additional repairs needed, they should callyou and inform you of what is going on and what it will cost. Thisinsures that you will get what you paid for and nothing less.
Become involved in understanding what is going on with your bike.Don’t be afraid to ask questions. Buy a manual and read it. You’llbe amazed how much knowledge will help your understanding andcommunication with mechanics. Expect the same courtesy from yourmotorcycle shop and technicians that you would expect at a goodrestaurant. It is a “service” business, so expect to be served.
Mail order motorcycle parts are proliferating everywhere.”Discount” catalogs, mail order, and on-line motorcycle parts areeasy to peruse. Sometimes you’ll save a few dollars, most of thetime you’ll end up paying less for the same part at your local shop,and they have it sitting in stock right there on the shelf. Once youfigure in your time, the costs of shipping and any defects orwarranty issues that may arise with your mail-order part; you mayfind that what you thought was cheap, really wasn’t the best deal.Once again, take the time to find a business run by people with whomyou are comfortable dealing with. Check their prices with pricesthat you’ve found in the catalogs or on-line.
Relationships are also built on timeliness. A quality facilitywill respect and value your time. You’ve got other things to do inyour life besides schlepping your motorcycle to the shop, getting aride home, and then missing a weekend ride with your buddies becausea part was “back-ordered”. It is reasonable to expect the parts thatyou need for your project to be available when you are scheduled tohave the service or customization performed. Ride your bike untilall the parts are in stock and the service-calendar at your shop isready for your operation. If you feel like the shop can’t organizethe components that you need, before you drop the bike off, there’s agood chance that they won’t know what you’ll need to get the job doneright. After you’re committed and your bike is in pieces, thenyou’re in way too deep.
Finally, whats right for the goose isnt always right for thegander. Just because you saw some new whiz-bang omni-gobulator onsome show-winning machine in a magazine doesn’t mean that it willperform on your bike. Ask your trusted mechanic or shop-owner whatthey think of a component in regards to your machine. They work withthis stuff everyday. Chances are they will steer you towardscomponents that are proven to work. Experience dictates that if apart fails more than once, a reputable shop will stop offering thatcomponent. A motorcycle shop can’t exist for very long suggestingfailed parts. Look for an existing track record of long-term qualityrelationships with vendors and customers when choosing a shop foryour machine. Components from different manufacturers don’t alwaysfit together, and it takes years of experience to know what fits what.
Relationships are a two way street. Your relationship with yourlocal motorcycle shop should be no different. Respect is earned,and a shop should earn your respect and confidence before receivingyour hard earned money. In turn, you deserve to have the piece ofmind to know that your bike is performing up to its highestpotential. Be prepared to pay a reasonable price to keep it that way.Most of all, respect anyone, who is working hard to make a living,keeping you rolling down the road safely. Then you’ve got asuccessful relationship with the man and the machine. In tech wetrust.
Remember, keep the rubber side down.
–John at Steeds

Back to the Surgical Steeds…
Bikernet Interviews John Covington Of Surgical Steeds
By Bandit |
John Covington has been in the custom manufactured motorcyclebusiness since Don Bitman started the trend with the IllusionMotorcycle Line. He is a devoted performance minded builder from thePhoenix area. We caught up with him at closing time in a Scottsdalebiker joint called the Billet Bar and quizzed him on the conditionand future of the custom market.
KRB: What’s your perception of the clone market today? Is it strong? Is it wrong?
First off, don’t piss me off with that tired clone label. I just got the new “Complete Illustrated Encyclopedia of American Motorcycles” (Tod Rafferty, Courage Books) and it doesn’t take much research to find out that Mr. Harley and those Davidson bros back in 1903 didn’t come out of the chute with their own engine or anything very unique or proprietary in their first decade of operation. At the turn of the last century, about 25 other contemporary manufacturers were building two-wheeled, motorized transportation using similar technology of the time. Those early motorcycle companies used the same engine and drive train from company to company. Were they all clones?
In our relatively short time as an American manufacturer, Surgical-Steeds has made it into the same encyclopedia, so I guess that’s proof that we definitely have our own identity.
I think some marketing guy at H-D came up with that clone word about 1996, when they obviously felt threatened by a few small companies improving on the status-quo machines that they were pumping out. Let’s give Harley credit for a lot of stuff, but breaking new ground in engineering, performance, reliability, fit and finish is not the reason people buy their bikes. Those marketing guys at H-D have done an excellent job of building a mystique around their brand.
KRB: OK, I give. Clone is a shitty word. It’s condescending. Do you prefer hybrid? What would you call them?
Motorcycles. That’s what I build. If you need to put a name to it, I would prefer alternative American motorcycles, while Surgical-Steeds builds “pedigreed custom motorcycles.” We’ve been in business since ’89 and I got into the business because I love to build custom bikes, and that is what we still do to this day. I plan on doing this for as long as I have fun walking, talking, breathing, dreaming and building motorcycles. I took my company through all the fed’s bullshit to become a legitimate American manufacturer of motorcycles for several reasons. We can call Surgical-Steeds a manufacturer because Steeds took the time and invested the cash to achieve EPA-, DOT- and California CARB-approved certifications of compliance to legitimize our niche in the market. That is why I believe that the pedigree status applies to the Steed brand. Our motorcycles have had federal VIN (vehicle identification numbers) since 1994.
I started building complete frame-up customs back in 1989. We decided to get our federal license because I was tired of being treated like a criminal when I went to the Arizona MVD to title our custom bikes. Donnie Bitman, who started Illusion Motorcycle Co., inspired me to get a federal manufacturers license. I figured if he could get one, Surgical-Steeds should too. About a year later in ’95, there was a handful of companies like Titan, Big Dog, Pure Steel, American Image, American Eagle, Castle, California Customs, et al, that also decided to build and legitimize their “alternative” motorcycle companies and got licensed. I think that each of these companies had a unique and genuine vision of how they could improve an American motorcycle.
KRB: What killed the companies that are going away?
GREED. I think a lot of companies started building bikes for all the wrong reasons. Once you’ve lost the passion for what you’re doing and are only out for the money, you are doomed to fail. Everybody has to make a living; I think that most of the companies that have died were out to make a killing. The whole ’90s rush to do an IPO and make a fortune building thousands of motorcycles was flawed. How custom is a bike if there are more than two that look exactly the same? Why would anyone want to pay thirty-five grand plus to have a bike that is exactly like somebody else’s?
I remember in 1997, during Daytona Bike Week, when everyone was buying a certain trail-blazing brand of American bike. One afternoon, on Highway A1A in front of our booth, two guys pulled up to a stoplight with the exact same white motorcycle with a purple scalloped paint job. Both of these guys thought they had the coolest custom bike on the planet, until they came face to face with the other coolest bike on the planet. How many more just like their `custom’ existed? Right then I decided that there was no other reason except for laziness and greed to manufacture identical bikes. “Volume produced customs” was one of the best oxymorons in the business. Look where it got them.
KRB: What’s the market? Who buys these bikes and why?
People who buy Steed bikes are looking for a unique bike that they intend to ride. Our bikes are all individually designed to be durable and attractive while each has its own curb appeal and personality. We don’t make “jewelry” show bikes. Our bikes appeal to the guy who has done his homework and wants a quality machine that fits his personality and riding style, as well as one that is designed to be physically and ergonomically comfortable and balanced to ride. That’s what a custom bike should be. Not just a few of those qualities, but all of them in one machine. That’s what we offer in our bikes. By becoming a licensed manufacturer of custom bikes, we also offer the consumer the security that we have done our part to maintain the value of the motorcycles we build. No excuses, no compromises.
KRB: People like yourself build bikes because you love it. What happenswhen you try to standardize your craft or try to make it mass market?
Standardization can lead to quality, but it also brings the risk of being complacent or boring. Certain quality issues may arise by being too custom, and using the latest and greatest parts. Relationships with quality vendors who are in the business for the right reasons are very important. There is a new company springing up selling a new product every week. A lot of these new products are great, but far too many of them have not had the proper amount of R&D and are prematurely placed the market. When you are leading the way with innovative parts, it is very important that you have a confident relationship with your suppliers. I can’t, in good conscience, put someone out on one of our bikes that has parts on it that may not be tested, safe and durable. That level of confidence only comes with good relationships with your suppliers, and that takes time.
Since we are a small volume manufacturer, we can see which components are holding up, which are failing and can make improvements to the components on the run. We don’t need board meetings to make design changes. If it doesn’t work consistently, that part won’t be a component on our motorcycles. We work closely with our suppliers to keep improving all the components on our machines.
KRB: Most of the guys in the clone industry must buy the majority of theircomponents from another source. That means they’re paying an extramargin. How tough is it to build these bikes and make a profit?
Harley-Davidson has tons of suppliers that they source their products from, so does GM and every company that produces anything. I guess the guys who make steel or copper just make it directly from dirt, but all the stuff that it takes to build a Steed motorcycle comes from somewhere. A lot of it we design and test in-house and then have specialists build for us to our specifications, like our Monoglide chassis. Some of the components come from distributors, but as a manufacturer, we’re working closely with the people who directly create the components we select for our machines.
Now the person who is trying to build a bike in his garage has a much bigger challenge ahead for himself if he thinks he’s going to save money by building a bike at home. Too often it is too late for them to turn around after they realize what they’ve gotten themselves into. The prices of quality components really do add up. The level of expertise to build a reliable machine is rarely calculated into the equation, nor is the time it takes to assemble and paint the project. Usually the home scratch-built bikes don’t get finished, or when they do, their owners have difficulty insuring them for what they are worth. I have heard that in some states they are imposing limitations of registering homemade vehicles, and the insurance companies are getting more particular with the special construction titles.
KRB: Where are the most sales? Easyriders stores, bike shop/dealers orwhat? Do you have a dealer program?
Until this last year, all of our sales were directly through our shop in Scottsdale, Arizona. We”mailto:dealer@surgicalsteeds.com>
KRB: For the guy on the street, is he better off buying a manufacturedcustom or would he be better off paying a little more and having aone-off custom built?
At Steeds we offer both of those qualities to the consumer with our pedigreed custom bikes. You asked, so I”ll tell you: He’s better off buying a Steed. That’s my one moment of shameless self-promotion. There’s a reason I organized this company like it is, and I’m glad that you are asking these questions to help spread the word about what a true manufactured custom is all about.
KRB: At one time the average manufactured custom was the full-blown customon the street or at the shows. Some guys will spend a chunk of theirlives hand building a custom in their garage that won’t come out asnice as one of these bikes. On the other hand, it’s forced the trulycustom shop to take a giant step forward to be competitive, such asCyril Huze, Paul Yaffe, Jesse James or Donnie Smith. What has thatdone to the market?
I don’t think that anyone on your elite list has the federal manufacturing licenses and certificates that we do. We offer personal attention to our customers and we work closely with our clients and dealers to build each Steed with all the features and accessories that are important to them. All of the guys on your list are incredible builders and are very talented and innovative movers and shakers in our chosen profession. The challenge for all of us is to be innovative, consistent, ride-able and to maintain the value for the consumer.
KRB: Does the Twin Cam make manufactured customs passe if they continue to use the Evo platform?
The Twin Cam is the result of Harley-Davidson engineers catching up to the improvements made by the aftermarket and complying with government restrictions on valve train noise. The Twin Cam was basically derived and evolved from the need for Harley to compete with what S&S, Merch, T.P and all the other alternative motor and component companies were doing for many years — building reliable big-inch motors. Now Harley has definitely made the pricing more competitive with its motor program, but when you have the choice, the alternative manufactured drive trains are generally way ahead of the curve. The aftermarket is already offering improvements to upgrade the factory Twin Cam. You do the math.
KRB: What could happen next that would harm this market? In contrast, whatcould happen that would make it even stronger?
The worst thing that could happen to this market would be to see another manufacturer bite the dust, or see new companies spring up that haven’t done all of their homework and fail when they aren’t managed properly. I feel very strongly that the consumer confidence in the alternative American segment has suffered some enormous blows and a big negative hit with the financial failures of Big-X, Titan, Confederate and Quantum. I hope the other established alternative American companies can weather the storm and keep building quality machines. There are enough people out there who want what we all have to offer for us all to be successful at what we do, and each of these companies cater to a different consumer. That’s what America is all about, choices, and it sucks when our choices are limited by anything.
KRB: What is your perception of the metric cruiser market and its impact on ours?
A totally different guy is going to buy into the metric machine. I think that you are trying to compare apples to oranges. On the other hand, it exposes more people to riding who hopefully will want to trade up into a custom American machine someday.
KRB: Here’s an interesting one: Guys buy these bikes to be macho. At onetime, a guy who built his own custom and rode it around the countrywas macho. He did it himself. He lived or died by his abilities andskills. Now a guy can just buy that machine. Is he macho?
Muy macho, yes indeed. Either way, these guys are on a bike because they want to ride and have the experience. You can appreciate what it takes to build one by doing it yourself, or understand your own limitations and have a professional build it for you. Here’s the whole “land of the free, home of the brave” concept coming into play again. Do you hear a song kicking in?
KRB: The reason I ask that question is that there’s a much smalleraudience out there that rides 180 mph sport bikes. They considercruisers of all forms as lightweights. They are the ones riding onthe edge of the curve from a technology standpoint. What do you think?
Technology meets American traditions in our machines. These guys are muy macho in their riding and opinions, and there is plenty of room on the road for all of us as long as the cops aren’t watching.
KRB: I’m a big bore fan. What performance formula do you prefer forreliability in a variety of situations?
I’m riding a 98-inch motor in my personal bike. I like the torque. We also offer 107s and 120s for the guy who wants more. We’re doing a couple of bikes with Patrick Racing 113s that are supposed to be the best of all worlds. Just like blondes, brunettes and redheads, too many versions and not enough time in the day to ride them all.
KRB: What’s your perception of the future for Surgical-Steeds and the industry as a whole? Will we all ride sport bikes to hell?
I think that this will be a year of slow, sustainable growth for Surgical-Steeds. We’re looking for a few good dealers, and I know that they are out there. I think it may take until next spring to see how it washes out with all the other alternative manufacturers. I just hope that the industry as a whole does not suffer too much of a beating in the court of public opinion. When the dust settles, I know that I’ll still be building custom bikes for people who can appreciate them. It’s a pretty cool job to go to every day, and I’m not ready to retire quite yet.
Web site: www.surgicalsteeds.com
Online store at www.musclebikes.com
Back to The Garage on Bikernet….
Joker Machine
By Bandit |
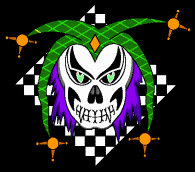
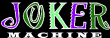
![]() If it weren’t for the precision parts that came from Joker Machine, Bandit would still be in the leaning Bikernet garage trying to make forward controls from old rods and wrist pins for the Blue Flame. Bandit ran into Geoff, Joker’s general manager, at the Indianapolis dealer expo, where Geoff reminded the old guy of his past offers to collaborate on a project bike. Bandit had been intrigued with Joker since it started. He could spot quality and design capability and, of course, good-looking girls. Bandit reveled in the Joker Machine logo with its Mardi Gras colors. The company obviously was cutting edge, and ranked with the very best in its league of components. Through the years, Bandit was devoted to helping a number of companies that already built billet components. His hands were tied. Yet he continued to be impressed with the Joker level of quality and style. Finally, the old guy had the pleasure of working with the ailing Geoff, the boss, Diane, and her brother, Richard, the masterful designer. Joker began as a machine shop cranking out military spec components for the aerospace industry. Diane’s father bought the business with his partner in 1971. Diane, also came on board the same year. Her brother followed in 1987. They continued to fill government aerospace contracts and build hot rod automotive parts and irrigation components. Behind the machine shop, her father and others built bikes. These riders, who were working hard to make a living in their smog-filled Azusa, Calif., machine shop, had no idea that some day they would be able to aim their talents and expertise at the industry they loved most — Harleys.
They started manufacturing parts for the marketing arm of Pro One in 1991. They continued until 1995, when they established Joker Machine to market their own parts. At the time, they were building a new custom project and Diane came up with the Joker notion for the tank art. Richard took her concept and created the Joker artwork, which was never intended for a business logo. The cutting-edge notion kicked off the risk-taking, bad-boy image we see with numerous companies in the industry today, including Jesse James’ West Coast Choppers. It was all in fun, yet it brought the risk-taking nature of bike riding to life. You couldn’t miss it. The company took on a new aura with the Joker line, although government contracts continued to provide a stable income. “Aircraft contracts are a miserable way to make a living,” Diane said. “The red tape is stifling.” They enjoy the creativity, style and constant movement of the custom motorcycle industry. “All the kids in our family are creative. Plus, Richard understands the entire process of creating and manufacturing components. We just had to pick up the marketing end. Richard enjoys continually upgrading our line with new technology and developments that keep the line on the cutting edge of the industry,” she said. They started with lighting products, then expanded to hand controls and forward controls. They work with one major distributor, have a growing dealer network and continue supplying the retail market. In the future, Joker plans to roll into accessories for the twin cam motors. “Our parts are top of the line and expensive,” Diane said. “But we stand behind each and every component.” Joker’s shop is a pristine, 8,000-square-foot facility on a large lot. The major players at Joker still ride, including Diane with a Road King, Richard is building another custom Softail with the Joker touch and Geoff who rides street and drags. “Three years ago, we got involved with racing,” said Diane, her eyes sparkling as she talks about the drags. “Geoff used to race dirt bikes, but then he started practicing on a Buell at the drags. That’s when we started to sponsor Ron Fringer, who raced top fuel. Joker Machine is also the HDRA pro-stock series sponsors, with Geoff racing in the H-D modified class. We’d like to see more prize money for these guys, but we find the drags to be an outstanding outlet for marketing our products. The enthusiasts are very dedicated.”
Geoff has qualified fourth in his class in the AHDRA. Although the family owned business is built around precision and exact detail, the crew is jovial and easy going. I suppose it comes with knowing what you’re doing and being confident in your product.
–Wrench |
|