V-Rod with added Tuner and Dyno
By Bandit |
Ever since H-D started utilizing fuel injection on their bikes, I have seen and heard both the positives and negatives on both sides of the argument. I was always impressed by the crisp throttle response, reliability, and performance of the fuel injection; but I also had a few questions. A few years ago, Harley started using O2 sensors making their systems a “closed-loop” which reads the O2 of the exhaust and then adjusts accordingly…or so I understood. Thankfully there are resources available to us to discover the ins and outs of just about anything one could desire to learn about. As for me, a V-Rod based website called 1130cc.com, I was able to research a little more about Harley’s stock ECM and fuel injection tools.
It seems there are many riders like myself who could not stand the EPA choked stock engine/ muffler combination. Besides sounding like a giant sewing machine, the stock pipes and mufflers weighed in excess of 30 pounds and also emit incredible heat. Because of the restrictions placed on H-D to make their engines compliant, the stock settings tend to run on the lean side. Many of the riders questioned the need for an new ECM tuner, considering Harley’s system was set up in a closed loop already, so therefore why would you need a tune? I myself was curious, so I added the D and D Fat Cat exhaust to my 2008 VRSCDXA along with a K & N Free Flowing air filter. I immediately heard the difference from stock, but to be honest, it seemed to really hit a dead spot down low. When taking off the line from a dead stop, the bike was almost a dog, as it would stumble and cough. Once I got her going, she was a beast running like a rocket, but upon letting go of the throttle, I was always welcomed to a series of backfires and explosions. Fearing I may have been running lean, I would check the plugs on the bike to make sure they weren’t white on the ends.
On a V-Rod, checking the plugs is a bit harder than a traditional big twin as you have to remove quite a bit from under the air box to get to them. Also, just checking the plugs in the garage will tell you the condition at idle, I was more concerned with WTFO, so I took half the upper end apart and took of for a straightaway to open her up. In 4th gear, just as I had opened her up to full throttle and pulled past 7500 rpms, I shut the bike off and coasted to the side of the road. Using quick hands and some hand tools, I was able to pull the plugs only to discover the plugs are white upon full throttle runs. I went to my current beacon of information here in Houston, Republic Harley Davidson, and asked Craig Slovak, the GM, for his advice on the situation.
Craig has recently spent several thousand dollars sending one of his techs, Joshua Thomas, to Harley’s V-Rod classes and training. Josh, a well respected drag racer in his own right, is the resident V-Rod magician at Republic, having enough experience to have taken the cases apart on one of the mysterious Revolution engines. He is one of 5 Masters of Service Technology Technicians at Republic.
“These engines are extremely simple. You can remove the crank without even touching the top end of the engine. Truthfully, one of the easiest engines Harley has ever produced to work on,” Josh recently told me.
After explaining my bike’s configuration and symptoms, Josh recommended Harley Davidson’s new Screaming Eagle Pro Super Tuner. Like many of the tuners available, this will allow the technician to fine tune my bike on the dyno, but with this software he would be able to make adjustments to the stock ECM across a much broader range of parameters rather than the typical points of adjustment. Basically he would be able to adjust my air to fuel ration from idle all the way through WTFO and every point along the way. He did tell me not to expect much more out of top horsepower, as the D&D is one of the best tuned pipes for producing horsepower around. What he was going to shoot for would be a much cleaner acceleration throughout the power. This tuner would be able to hold a 15 minute run in its memory tracking along 26 variable points. Joshua should be able to dial this thing down to pull like a truck and only stop when I do.
I dropped the bike off and when I returned several hours later I was greeted with a smiling Service Department. Josh was waiting for me with dyno sheet in hand. Like he had said, I didn’t gain much in peak horsepower, but I definitely had a much more linear power curve and my rev limiter was increased from 8000 rpm’s to 9000, which also adds to the performance on the top end.
As you can see from the dyno, I gained approximately 10 hp and 15 ft lb of torque at 3250 rpm’s. Also, on the initial run the bike hit 60 ft lbs of torque almost immediately and then didn’t start climbing until 3700 rpm’s, hitting a linear point at 4200 rpm’s and about 68 ft lbs. After the Race Tuner, the torque continually climbs from 65 all the way to about 74 ft lbs at 3500 rpms. The peak hp grows consistently, pulling all the way to 8000 rpm’s steadily. 8000 was the rev limit before, and now it stays pulling at 113 hp all the way through 9200 rpm’s, so I should also feel that in the top end. The air fuel mixture was set to stay above 145, almost hitting 15 as low as 4000 rpms, and Joshua set it up to stay closer to 13.5. This would probably affect my fuel mileage a little, but make for a smoother running engine. I didn’t buy the V-Rod to save on gas anyways!
I took the bike out on a short run the next day and did notice the improved low end grunt. Where I had a noticeable flat spot in the beginning of the rpm range, now the bike pulls like a train all the way through. I was braking the rear tire loose on normal take offs, which told me I hadn’t adjusted my throttle to the new power yet. While I didn’t notice a huge difference in sound, the bike does sound a bit crisper and seems to really respond to the fuel given to it now with fervor. The V-Rod was a monster before, but now she’s an absolute BEAST! With the tuner now being “married” to my bike, it means I am the only one who can use it and only with my bike. For a price just under 500 bucks and then the cost of a dyno tune, my bike is running stronger, smoother, and much cooler; so the price to pay was pretty conservative considering the rewards.
Andrew Hines Lights it up with the V-Rod Again
By Bandit |
HINES DEFEATS TONGLET AND ADDS TO POINTS LEAD
Seventh-Straight Final for Hines; Krawiec rides Harley V-Rod to Semi-Finals
MOHNTON, PA. (October 10, 2010) – Screamin’ Eagle®/Vance & Hines rider Andrew Hines rode a Harley-Davidson® V-Rod® to his fifth NHRA Pro Stock Motorcycle event win of the season at the Toyo Tires NHRA Nationals at Maple Grove Raceway. Making his seventh consecutive final-round appearance, Hines defeated Nitrofish Suzuki rider LE Tonglet and now leads second-place Tonglet by 74 points in the NHRA Full Throttle Countdown to the Championship playoffs.
“This was a big win for the Screamin’ Eagle team,” said Hines. “We leave here with a little cushion in the championship race, up by 3.5 rounds with eight rounds left to go. Now we have two weeks off to go home and see the family, and find a little more power in the V-Rod.”
Screamin’ Eagle/Vance & Hines rider Ed Krawiec qualified second for the event with an elapsed time of 6.855 seconds, and advanced to the semi-final round of eliminations on Sunday. Krawiec is third in Countdown points. Hines was the third-quickest qualifier at 6.859 seconds. Lucas Oil Buell rider Hector Arana led qualifying with a 6.828 pass in the final round on Saturday.
Krawiec moved through the first two rounds of Sunday eliminations with red-light wins over Team Joey D Suzuki rider Joe Desantis and Run Bum Racing Buell rider Shawn Gann.
Hines defeated Mohawk Automotive Kawasaki rider Neil Jacobs in the first round, and got a red-light win over Coffman Tank Trucks Buell rider Angie Smith in round two. Hines defeated Krawiec in the semi-finals, and for the fourth consecutive event faced Tonglet in the final.
Hines used a quick 0.020-second reaction time to beat Tonglet (0.043) off the line and got the hole-shot win with a 6.916-second blast that held off Tonglet’s 6.913-second run. For Hines, the win snapped a three-race losing streak to Tonglet, and padded his points lead over his closest rival for the championship. Hines now has 23 final-round wins in his NHRA career.
“Well, we finally got by that blue bike,” said Hines. “As has been the case in the past couple of races, we were losing horsepower as the day went on, but (crew chief) Matt Hines has got the clutch tuned just right. My hole shot is really consistent, and the bike is easy to ride round after round, which is great for my confidence.”
After four of six rounds in the NHRA Full Throttle Countdown, Hines leads the Pro Stock Motorcycle class with 2,566 points. Tonglet is second with 2,492 points, followed by Krawiec with 2,351. Al-Anabi Racing Buell rider Matt Smith is fourth with 2,323 points.
Screamin’ Eagle Performance Parts are inspired by and built in the spirit of the raw adrenaline and power of motorcycle racing. Screamin’ Eagle Pro parts are specifically designed for race-use applications, while Screamin’ Eagle parts offer street-use performance options for the Harley-Davidson motorcycle owner. Visit www.harley-davidson.com for more information.
The Screamin’ Eagle/Vance & Hines Pro Stock Motorcycle team is sponsored by Matco Tools, Dunlop and S100.
Bikernet Bonneville Effort, Part 8
By Bandit |
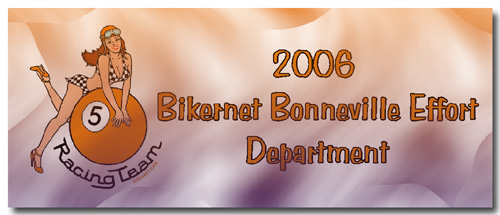
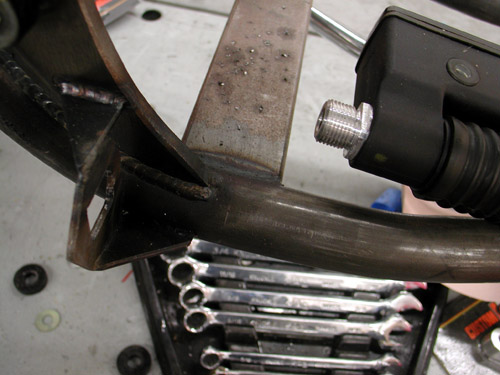
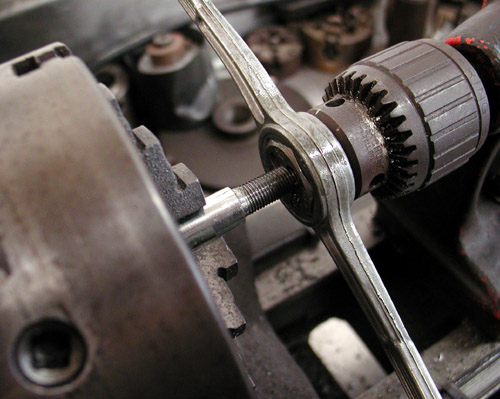
Life is bananas, and I add to the frustration by fuckin’ with everything. I can’t just bolt a part on, stand back and say, “Cool.” I’ve got to fuck with it. The V- kit comes with complete foot controls, but they were too far back and too high for my long lanky self. I cut them apart.
But first, since they were cast I had to ask the designer some questions. Fortunately John Reed, from Custom Chrome, is a good friend and here’s what he said. FXR and dresser primaries are the same dimensionally, however theouter primaries are the same on both, butthe inner primaries off the dresser has a piece on the front for the gear shifting bushing and shaft.
If you use the OEM primaries, I don’t recommend using latest models. Tochange the starter motor ratio on these the factory used a clutchbasket with more teeth on, but they are smaller than the early ones andthey break if engines with more power than stock power are used.
Late model primaries (1998 to present), use a starter motor that fitsthis year primary, it has a smaller diameter inside thread than earlymodels (‘94—‘97). It uses a smaller dia. starter shaft with smallergears to match the clutch basket.
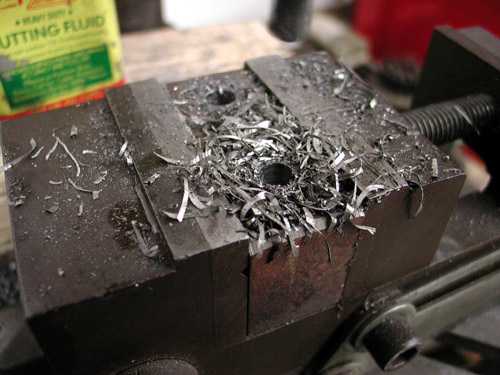
If you want to use the latest model primaries on a big inch motoryou can use a 1994-1997 clutch basket (which uses the same clutchplates ) with the stronger starter gear, but you have to use a largerthread starter motor gear instead of the OEM one. Does any of this make sense?
Custom chrome sell them on page 11.45 (bottom right hand side).
— John Reed
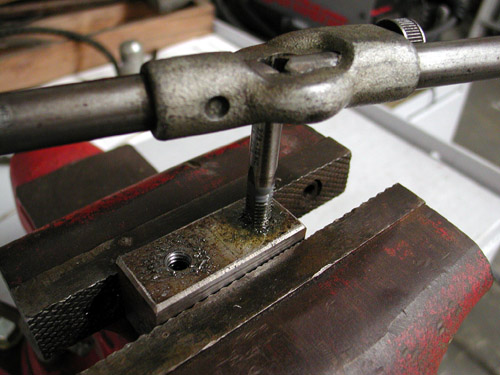
I don't know what the hell he was talking about, but fortunately Wink Eller is working for BDL, in the R&D department, on a tall geared, super strong Bonneville system. So I didn’t need to worry about the starter gearing and clutch ring gear. I always use super strong Compu-Fire alternators and starters on my bikes and have never had a problem.
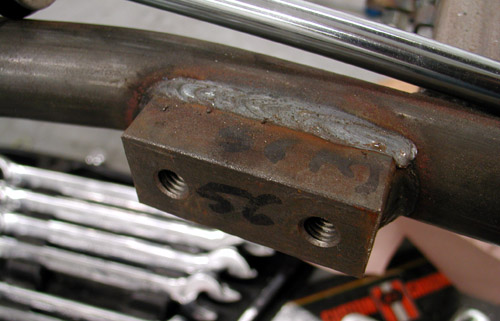
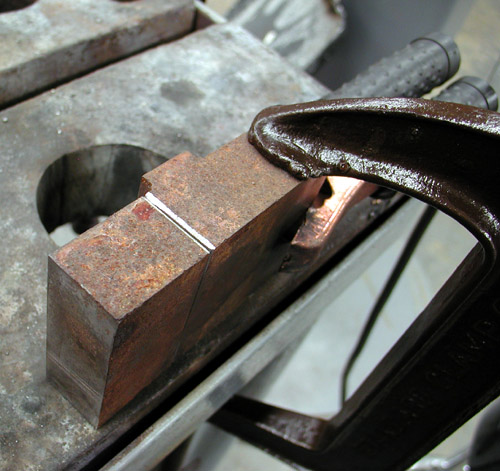
So first I cut two massive chunks of steel to move the controls forward and drilled and taped them. I noticed that the left controls with brake pedal attached had two 3/8 coarse bolts and the holes in the other side were 5/16 coarse. I drilled and taped both 3/8s.
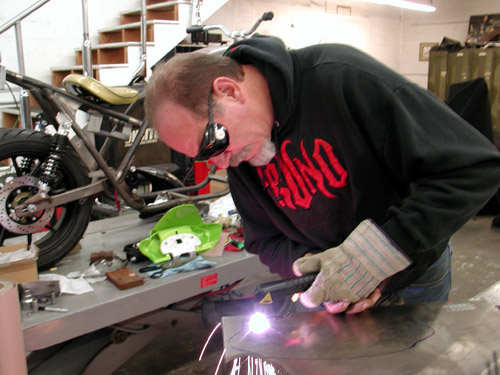
Remember the Le Pera solo seat? Well that left a massive notch in the rear of the tank for the original seat. I decided not to change tanks but use that area for a switch panel since I don’t plan to run switches on the bars or turn signals. So this is where the Plasma cutter came in handy. Jay showed up with the used cutter. He bought the sucka but never used it. It requires 220 volts and most folks don’t have those heavy outlets sticking out of their garage walls.
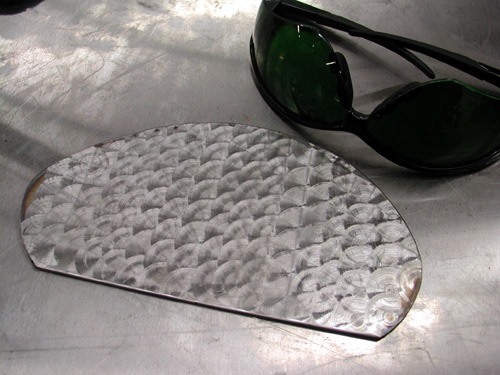
We pickup up the proper plug end from a Home Depot and wired it. It wouldn’t work. I called Kent at Lucky Devil and he clued us. We needed to have enough air in the compressor line to kick the switch, then the tip was used and wasn’t making an acceptable connection. We replaced it an went to work. Plasma cutters are amazing, safe, easy to use.We cut the chunk for the switch panel. Then we shifted to the milling machine to try our hands at machine turning the surface. It worked.
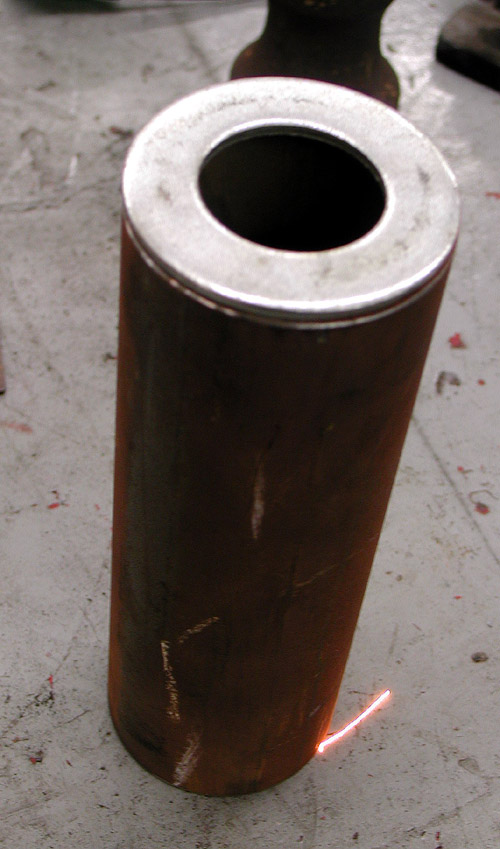
Next we moved to the bending procedure. We have pipe bending machine and a small stock bender, so we’re learning how mandrels work to form steel. We used a pipe bending mandrel and made the male out our of thick wall tubing with heavy washers welded on the ends for more strength.
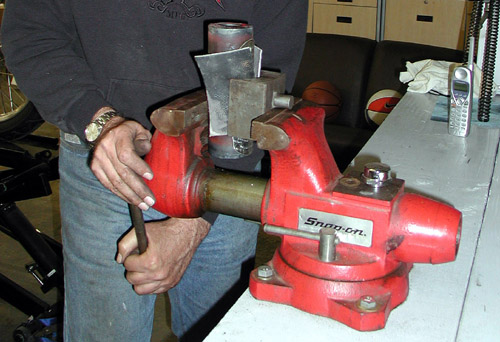
Then the massive Snap-On vice came in handy to crush our panel into the mold and is worked! We were blown away.
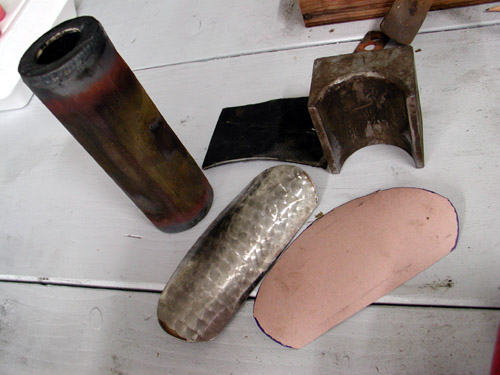
The next trick was building brackets to hold the panel in place. We used chunks of that same thick wall tubing to make arched brackets.
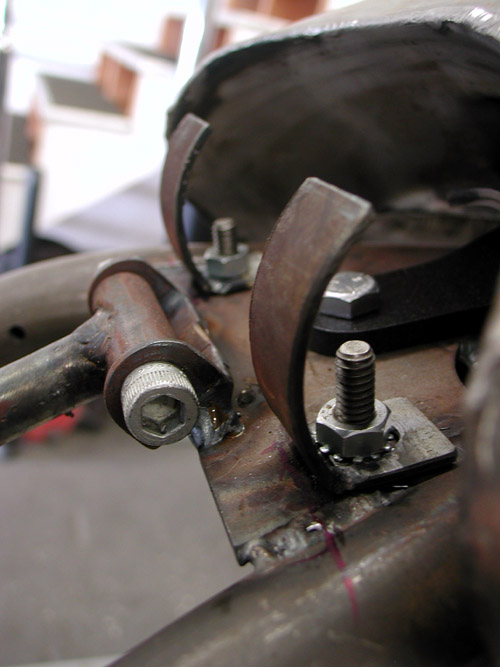
This shot shows the first aspects of building the brackets, welding them to tabs and drilling the holes for the frame connections. I needed to find a place to hold them so the fasteners would be accessible, but the brackets need to be spaced far enough apart to fit in the switches and fasten them.

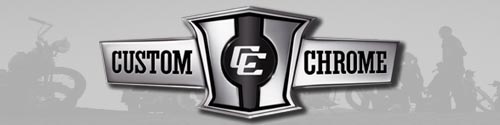
Bikernet Bonneville Effort, Part 7
By Bandit |
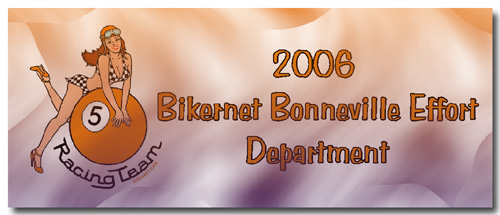
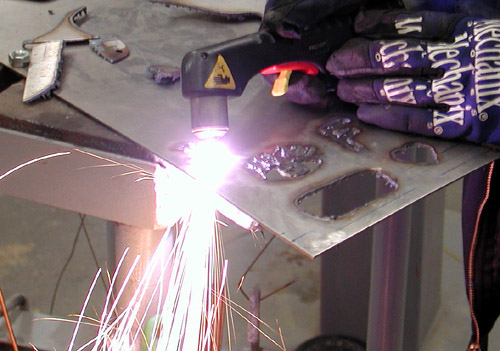
Plasma cutters are amazing, but let me back up just a taste. I needed to take care of the Devil in Houston at Lucky Devil’s Metal Works and made the brother a belt buckle. He’s going to build the lovely Nyla a Frisco style chopper in the near future—tight and light. You’ll see it come together right here on Bikernet.com.
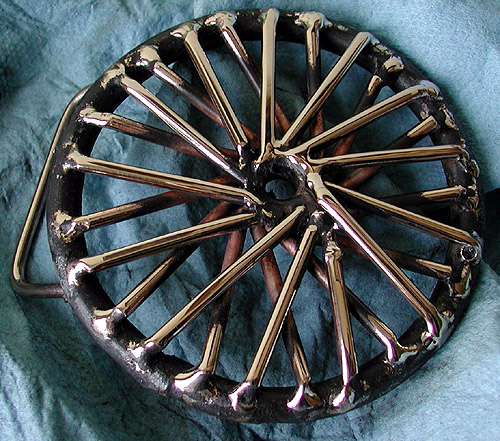
So burning the midnight oil and silicone bronze rod I made this belt buckle and shipped it to Houston. Then I turned back to the Salt Shaker, since I was waiting on 45 Flattie components. I scored this Eye Candy classic taillight since we wanted to add some old school to the Panhead Sportbike. This puppy worked out perfectly. They also make the ’59 Cadillac taillight on last year’s Sturgis Shovel.
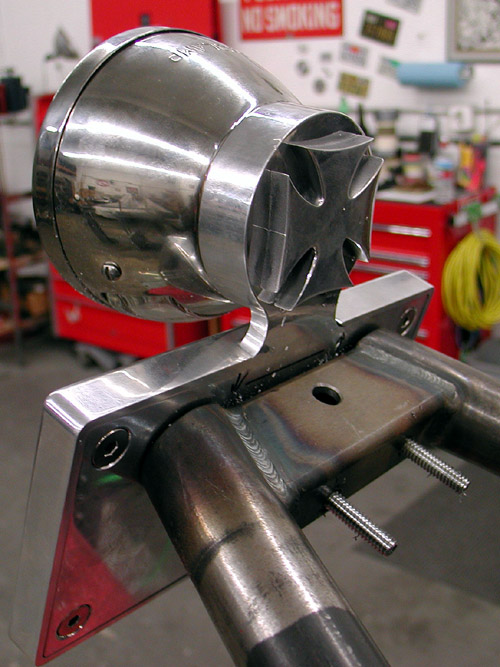
Eye Candy Custom Cycles LLC
Republic, Ohio(513) 312-1137
EyeCandy CustomCycles.com
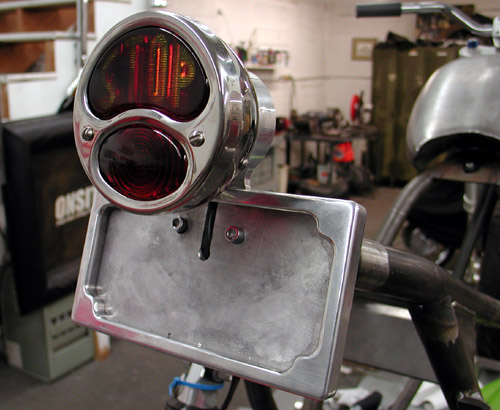
That was the easy part. Drill the holes through the frame rail and mount the sucker, so it fed the wires properly and looked cool. Then I shifted to mounting the gold metalflake Le Pera solo seat. You can order these in a number of colors and beading hues to match your theme. I’m stuck with gold Brembo rotors and calipers so I went nuts with the seat. The plan is to gold metalflake the frame and some components and shoot the sheet metal black with Bomber girl graphics.
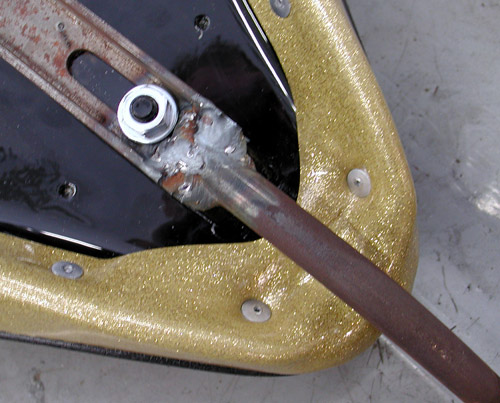
Seats can be a pain in the ass to mount on custom frames, unless they are cast into the sheet metal and won’t move. I monkeyed with this for hours trying to pick the correct position. This Le Pera seat is a classic for stock or rigid frames. It comes with a black powedered front frame mount and bungs on the back for springs–simple, easy to mount, but I changed the system. I also wanted to be able to move the seat back for a salt flats prone position. Then the damn thing needs to be centered and slightly tapered off level. Then, once the front was mounted, I needed to mess with the rear.
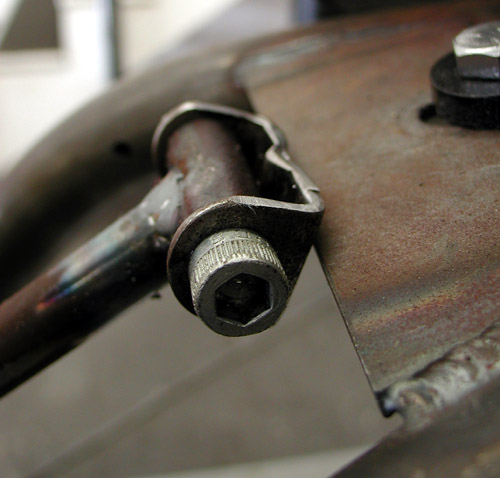
I split a stock solo-seat mounting bracket and welded a chunk of bent bar stock in between.
Then I cut apart one of my failed seat mounting systems and started to work on the rear bracket. I decided not to use springs for two reasons: The bike is rubbermounted and springs would make the seat too high.
I machined a slot in the strap so it would fit over the Le Pera support, but still be strong. Then I welded tabs to reach the frame holes.
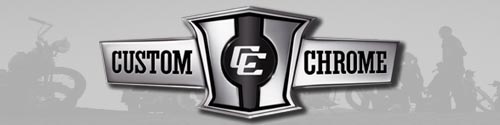
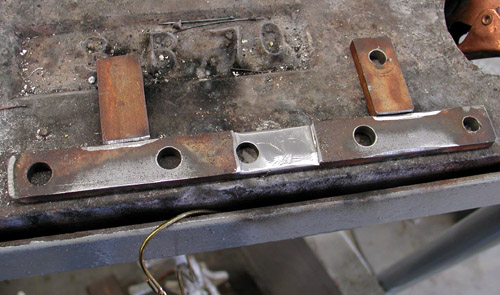
As it turned out the seat set on a couple of rubber bushings and will slide back about an inch and a half for Bonneville prone racing.
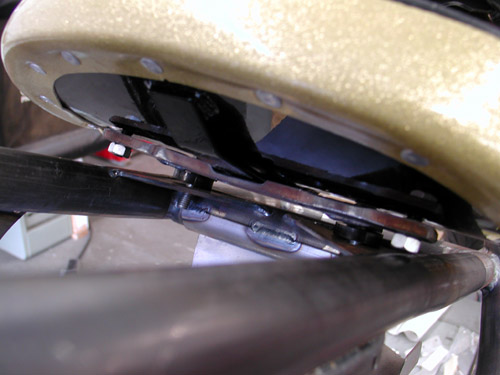
So there you have it. Three bolts remove the seat, it’s adjustable and secure. Shit, it was even comfortable. David Zelma, over at PM, keeps telling me that I’m going to hell for installing a solo seat on a sport bike. I’ve got lots of reasons for heading for the Devil’s den and that ain’t one of them.
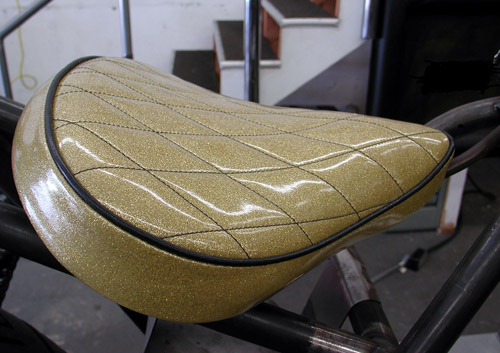
Next, I started to mess with an old triumph handlebar fairing. I wanted to run without the fairing, but the system with the V, comes with a dash of sorts. I shitcanned the original cat-eye fairing if favor of this one and a old school Bates headlight.

I made headlight brackets out of spacers and tubing to at the old school touch and place the headlight just under the fairing.
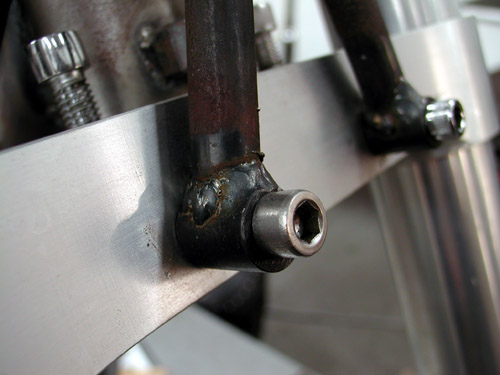
So far I liked the look for some strange reason, but we needed to finish off the dash aspect. That’s where the Plasma cutter came it so handy. Check the next episode of buiding this bike for Plasma and peg mounting tips.
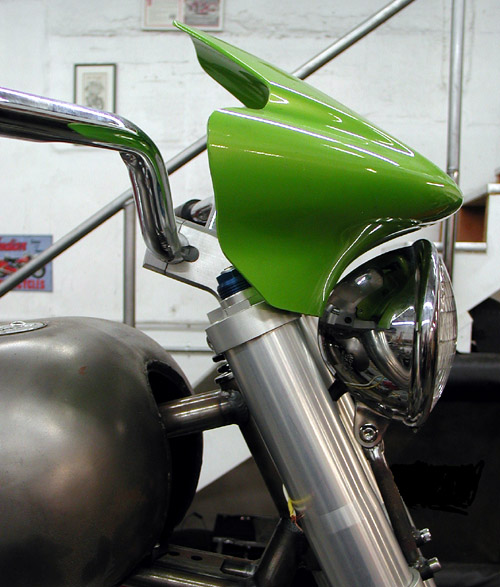
Next I’ll show you the fork stops I built for the 45, then we’ll shift back to Plasma cutting and machining extended peg mounts for my long legs. That’s where John Reed’s words come in handy. The bastard designed the bike for a midget, and for several reasons I can’t handle mid-controls anymore. Wait till you see what we did.
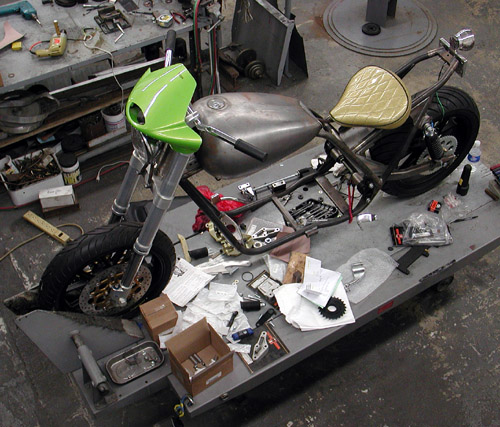
“The primaries are FXR/dresser systems,” John Reed said. “You can weld the steel footpeg brackets. I am pretty sure they aredrop forgings.I put mine in a mill and machined the shit out of them to make themlighter, but if you are using the bike on the saltyou want to keep as much weight as the motor can pull.”
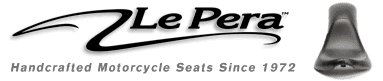
Bikernet Bonneville 2006 Effort, Part 6
By Bandit |
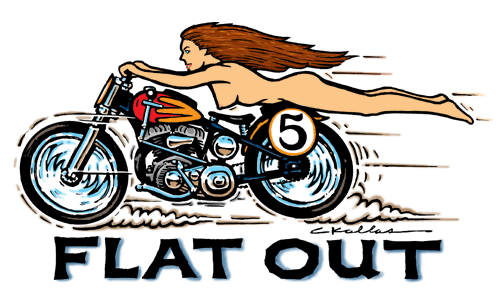
We’ve made serious progress on both bikes, thanks to terrific help from friends around the industry. The buzz is hot for the Bonneville this year.
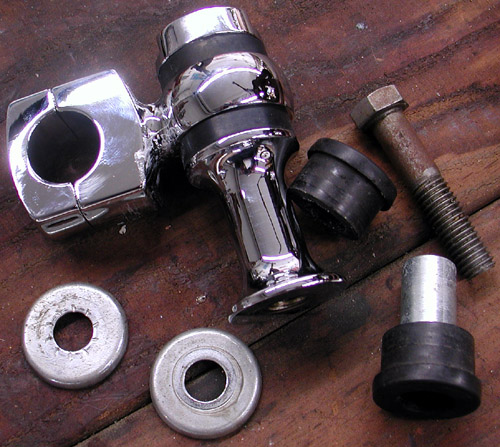
I may jump around a bit, but let’s haul ass into my first move. With the 45 frame aligned by U.S. Choppers, Rick Krost, the sheetmetal out to paint, at Jim’s Custom Paint, I needed to complete a few more tasks to finish the Bonne Belle roller. The front end needed shortening and bars, risers and fork stops. I ordered a sent of Custom Cycle engineering, 2-inch risers. I also ordered a set of 2-inch under Custom Cycle Engineering 39mm fork tubes. I still don’t understand why they measured only 1-inch shorter than the stock tubes, unless my tubes were lowered, an inch, from the factory.
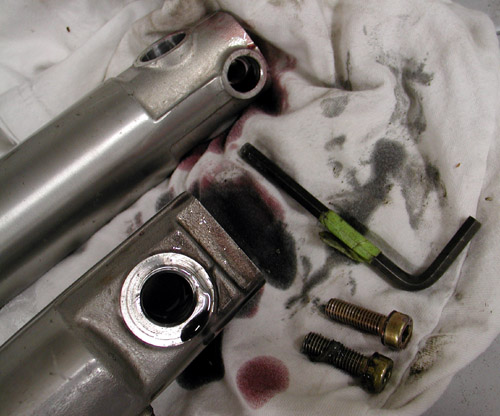
I ended up taking the front end apart a number of times. Kent, from Lucky Devil in Houston, told me to remove the metric Allens from the bottom of the lower legs first to drain them. I did. It worked alright, but there continued to be oil on the springs and inner components, so rags were necessary constantly.
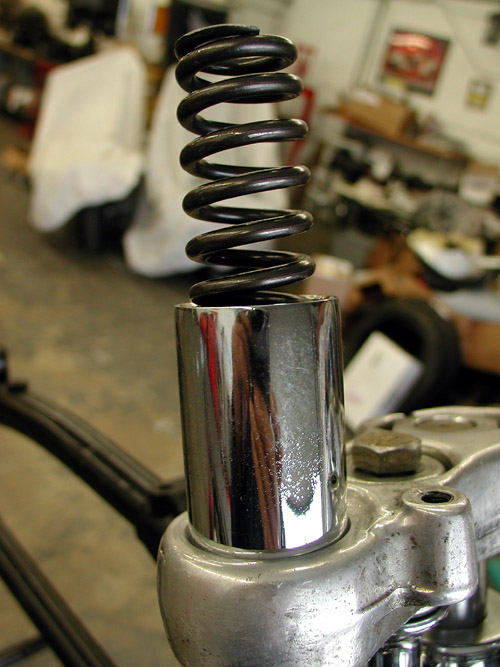
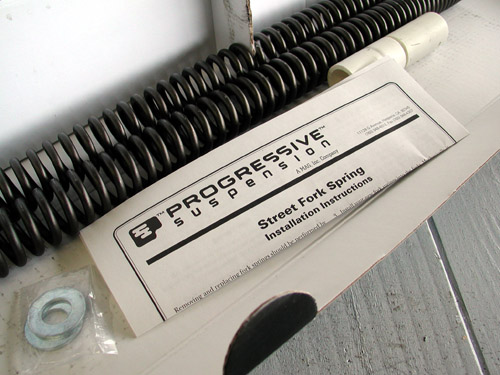
We ended up using shorter tubes and a set of Progressive suspension lowering kit springs from Custom Chrome to drop the front end even more.
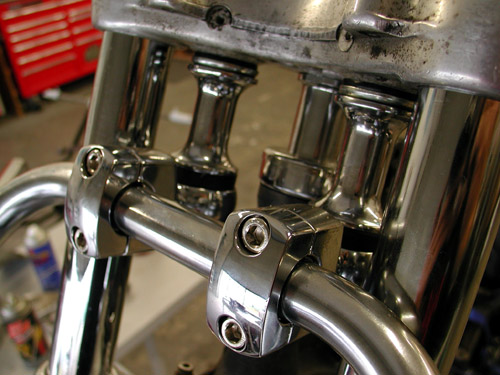
Before I finish the tube switchin’ procedure, here’s a shot of the dirt bike, 7/8 bars in place with the Custom Cycle Engineering risers upside down under the top triple tree.
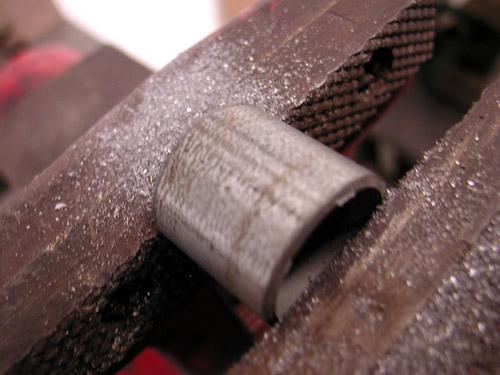
I cut chunks then sliced, in half, thin electrical conduit tubing to make shims to hold the bars securely in the risers. I used rubber trim cement to hold them in the risers, since I usually work by myself and it takes four hands to hold the riser caps, the Allens, the shims and the bars.
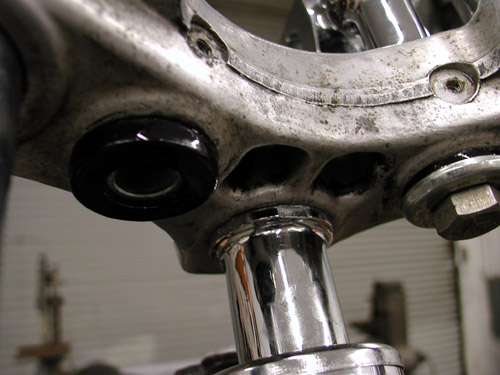
Here’s one more odd notion. We pressed a springer 7/8-inch neck stem into the Sportster bottom tree and left it Springer length, but altered the top bearing nut, so the top tree stands 1.5 inches above the top of the neck cup. That lowers the bike another 1.5 inches. We’re shooting for 4-5 inches of ground clearance.

Okay, let’s run through disassembly of a Sportster front end. Of course remove the wheel and brake components. I might suggest prying that Allen on the bottom of the lower leg loose first. Don’t remove it, but the compressed spring holds tremendous pressure on it.
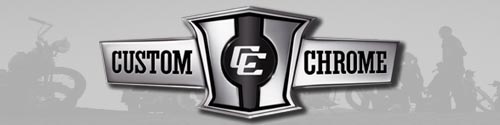
Then take the top cap off the tube with a 1 3/8 socket while the tube is still pinched in the trees. I loosened the pinch bolts and slid the legs out of the trees. I put a big coffee can on the bench and removed the Allen off the bottom of the lower leg and made sure to secure the brass washer that came with it. I slid the tubes up and down in the lower leg to pump out the fluid.

With a small punch and hammer I removed the dust shield/cap. There’s a notch in the lower leg for this chore, but be careful not to damage the cap or the leg. Tap it lightly.
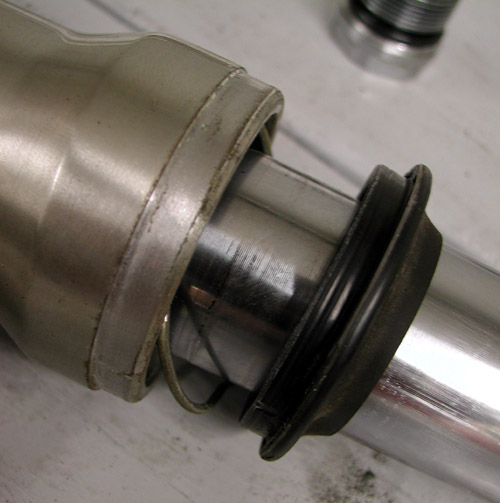
With a wedge I carefully dug under the rubber dust seal. This was a reasonably new front end, so I didn’t plan to replace these items. I took a lot of care not to damage them. Next, with a small flat screwdriver we removed the wire keeper that holds the fork oil seals in place. Then, by yanking up on the tube and sliding the damper components against the seal, it came out.
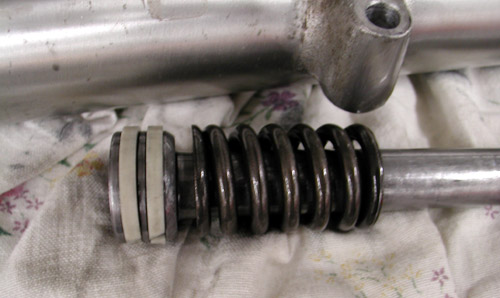
Then the damper tube came free with the rebound spring. I carefully washed all the components then reassembled the components with the new tubes.
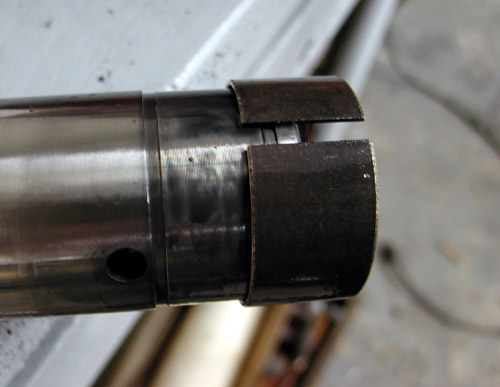
First this brass lower bushing needed to be carefully removed from the old tube and slipped onto the new one. Then the damper tube was returned to the tube with the rebound spring in first.
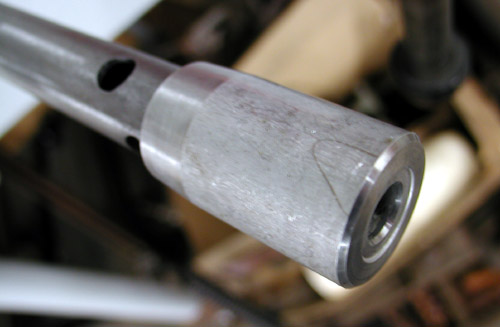
This cap slips over the damper tube and seals the bottom of the lower leg. It’s imperative that this puppy is clean and the inside of the lower leg completely free of dirt or debri, or the bastard won’t seal.
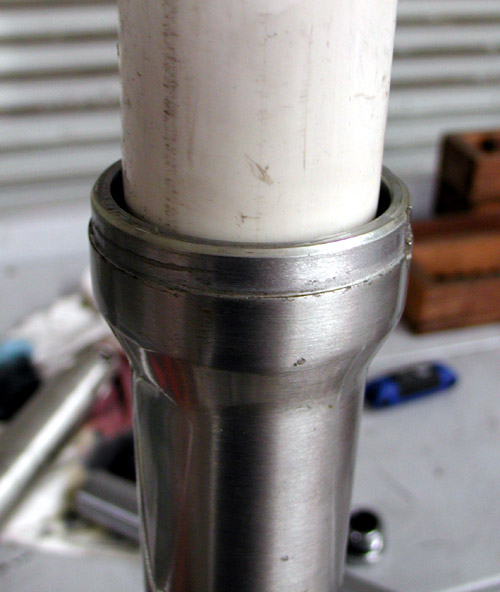
Here’s the kicker. Returning the oil seal can be a turkey. I made a tool out of a nut and chunk of exhaust pipe welded together, then wrapped it with duck tape to prevent marring the chrome. For some reason it didn’t work this time. Since the leg was off the trees I ran a chunk of 2-inch PVC pipe down over the tube and hit it with a rubber mallet. The Fork Seal slipped right into place. I returned the clip ring, the dust shield and dust cap (the PVC pipe worked as a tool here, also). I slipped the Progressive spring into the tube to hold it in place and tightened the Metric Allen at the bottom of the lower leg.
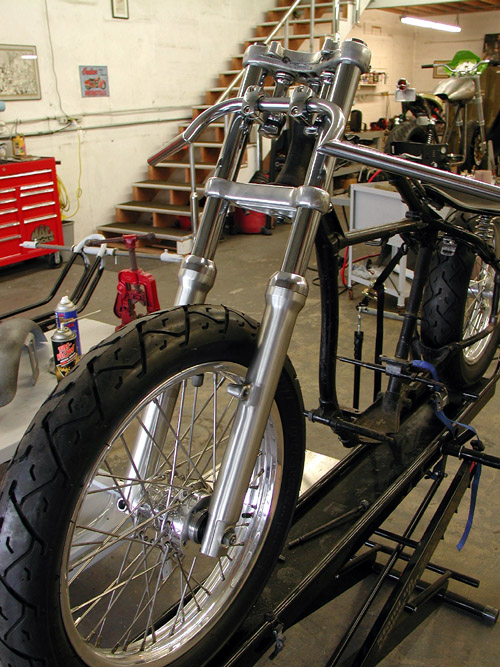
We slipped the tubes into place, tightened the pinch bolts, added 10 ounces of Amsoil Fork Oil in each tube and tightened the top fork tube caps. Shortly, we’ll have all of our Performance Machine Brake components, coupled with Yamaha 250 master cylinders, hand and foot controls for the light/small racing look. Yeah, I know, Jap stuff on our 45 flatty, but I think you’ll dig it when we’re finished.
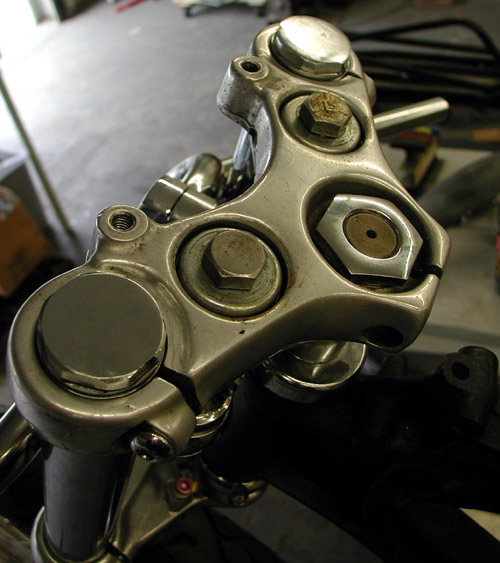


We weren’t done yet. The tanks were being painted and the last thing we needed were fork dings. I pondered the glide front end for fork stops and thought we had it made, no way. They were too low to catch the arch in the frame.
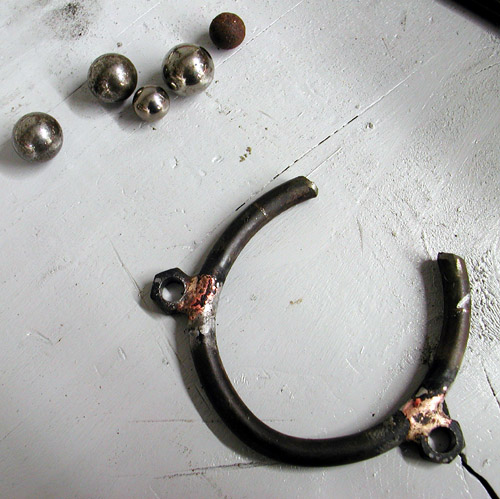
Then I discovered that even with extentions on the cast aluminum tabs the front end turned too far. That’s when the squirrely notion surfaced. I decided to connect the dots on the lower triple tree and create extensions that would reach the frame.
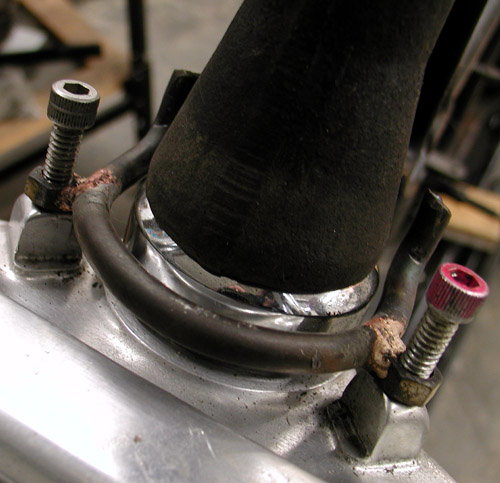
I bent a chunk of ¼-inch round stock and welded a couple of ¼ nuts in place. Then we bent the tips up to catch the frame.

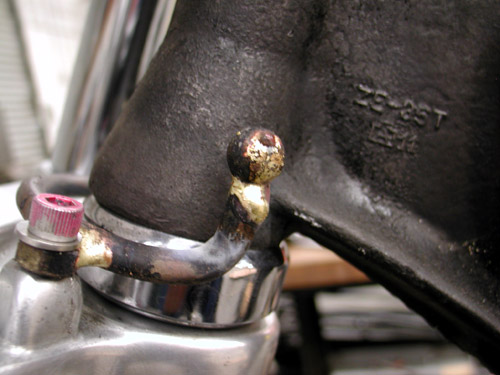
Then for “Bandit” style I brazed a couple of old ball bearings on the tips to finish them off. Brazing works well for small pieces that don’t need excessive heat or strength.
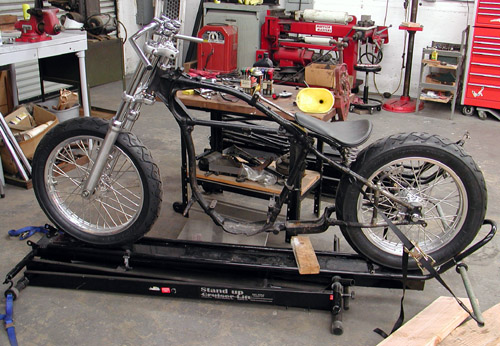
These puppies won’t allow a whole lot of turning ability, but generally we’re running straight down the salt and these will be easy to adjust once we have the tanks in place.
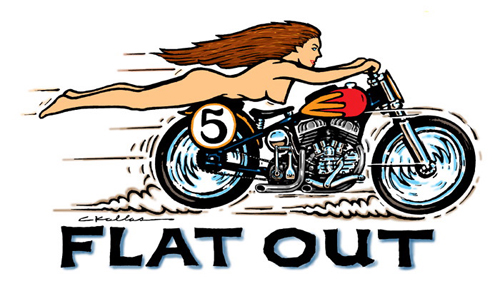
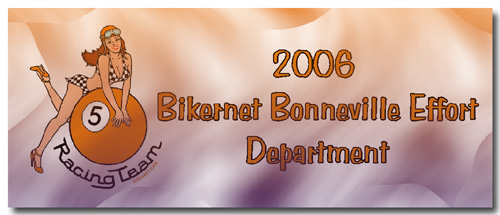
Bikernet Bonneville 2006 Sponsors
By Bandit |

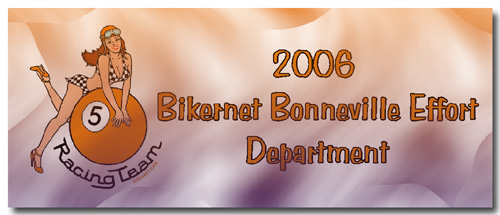
I don’t know where to start with this? It’s all come together so fast. Last year while blazing across Mexico, with Dr. Hamster, in the La Carrera Pan Americana, World’s Most Dangerous Road Race, he asked me if I would be his partner the following year? At first I was pumped as the ’54 Hot Rod Lincoln rattled across Texas, then I realized that my adventure for 2006 was, and will always be, motorcycle destined. I was forced to decline his offer. We had decided to run to the Bubs Bonneville International Speed Trials, September 3-7 in Wendover, Utah.
As I started to work on our bikes in the Bikernet Garage, notions started to fly. Bob T., a Bikernet Contributor, contacted me from 14 Palms, California and the Chop N Grind effort formed, another bike was added to the 5-Ball Racing Team. Shit, I don’t know squat about Bonneville, except for being on the Easyriders team that took, and still holds, the World Land Speed Record. I wasn’t going after that record. We just wanted to have some fun on the Salt for our 2006 Motorcycle Adventure. Suddenly we had a team of three bikes and a department was formed on Bikernet. Jeff Najar called and said, “Can I be a sponsor?”
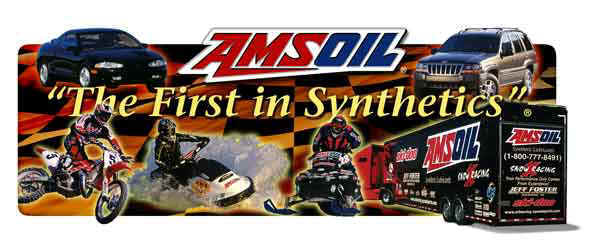
Next thing we knew, we had sponsors, brothers contacting Bob T. to help. Bob T. calling me for parts and we needed to form a Bikernet Sponsor system to credit anyone who bought us lunch, sent us a part, welded a frame or sent a check.
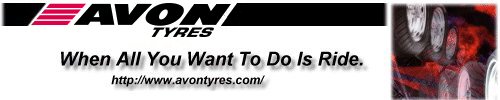
I’m not kidding when I say I’m flabbergasted at the response and the interest in our race effort and Bonneville. I immediately pitched in to help Bubs Bonneville effort as a sponsor to support the motorcycle-only event.
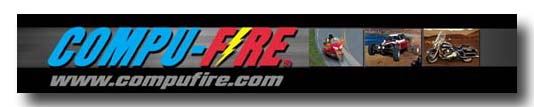
So here’s our growing list of sponsors. We will update this list on at least a weekly basis and try our damnest to give all the people and companies credit where it’s due. Don’t hesitate to contact me, if I screw-up or if you want to be involved.
–Bandit
Bandit@bikernet.com
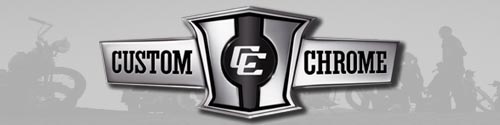
BIKERNET BONNEVILLE 2006 5-BALL TEAM SPONSORS
“So far our sponsors include AMSOIL, BMC Choppers, Jims USA, AVON Tires, S&S Cycle, Leinweber Cams,” Bob T. said. “We also have help from my brother at Expressive Designs in Oahu, and LMC Concrete Pumping. We want to thank each and every sponsor and we will in our articles, on our Bonneville Banners, truck and bikes.”
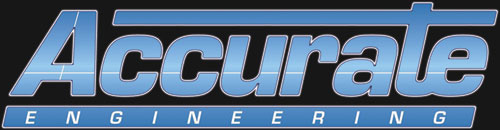
Bikernet Platinum Level
Custom Chrome Inc.
Accurate Engineering
Baker Drive Line
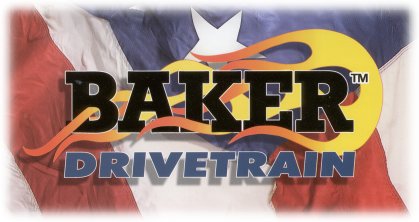
Departure Bike Works
Jim’s Custom Paint

Bikernet Gold Level
BDl
Avon Tyres
Nick’s Performance and Amsoil Oil
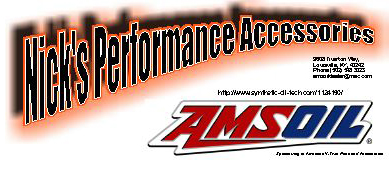
BMC Choppers
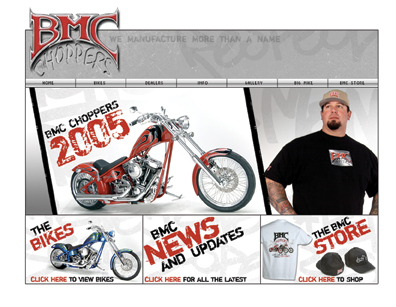
JIMS USA
U.S. Choppers
Randy Aron – Cycle Visions

True-Track, Wil Phillips

Bikernet Silver Level
Chris Kallas
Glen and Kerry Priddle
Nick Roberts – Nick's Performance Acces.
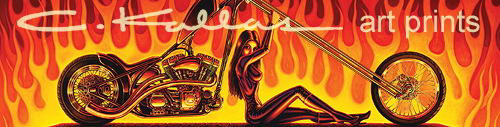
Expressive Designs
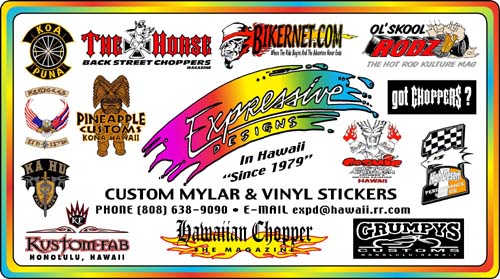
Rollin Sixes Custom Choppers
Two-Bit Choppers.com
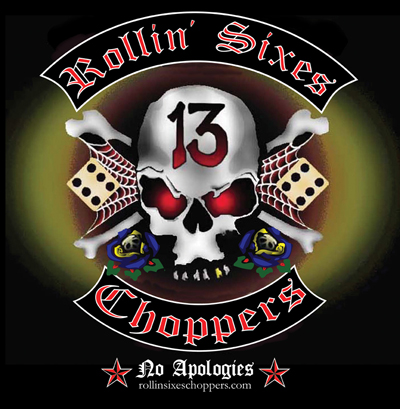
Bikernet Bronze Level
Andrea and Beach
Thebeachcruiser.com
Gene Koch
Peter Hagen, P.M. Fine Knives
Dr. Christian Reichardt
Jeff Najar, HorsePower Marketing
Glen and Kerry Priddle
Hank Hill
Jim Flickinger
Clyde Fessler
Lee Wimmer
California Customs
Randy Lee Meissner

Bikernet Rider Level
Mike and Meanest Pullin, Stealth Bike Works
Johnny & Salena White
Ray C. Wheeler
James Fly
Donald Magalhaes
Michael L. Turner
Two Wheelers Motorcycle shop
Bob Illingworth
Rick Fairless


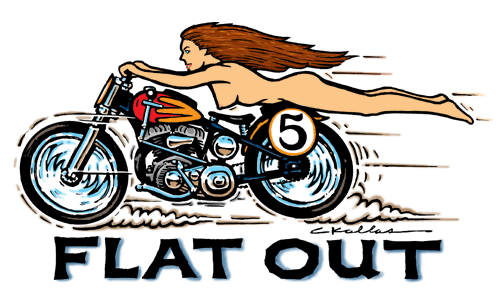
Bikernet Bonneville 2006 Effort, Part 5
By Bandit |
This is nuts. But let me try to explain. We’re making progress fast. Even our Bonne Belle art improved from a Chris Kallas black-and-white line drawing to a colored rendition by the master. Rick Krost straightened and strengthened the frame last chapter and we ordered Paughco cups designed for this frame (with Timken bearings) with a 7/8-inch, Paughco Springer stem. We (Settle’s Cycle, in Harbor City) machined the stem and pressed it into the Sportster bottom tree. Larry Settle also laced the PM hubs to the aluminum Sun Rims, mounted the V-rated Avon Tyres and balance the lot. We were rolling. Our goal was to turn this puppy into a roller, ship the sheet metal to Jim’s Custom Paint, while the frame and brackets were being powder coated. I’m getting ahead of myself. We were jazzed to pick up the wheels. We machined the rear hub, estimating the distance to the sprocket face from the frame, aligning it with the transmission sprocket. Fortunately we had access to a 1939 WLDR and made measurements. We ended up machining both sides of the rear PM hub before the wheel was laced. With complete wheels in our hot welding gloves, we returned to the Bikernet Headquarters and went to work. First we had to shave 1/32-inch off the rear axle landing to slip in the new Custom Chrome ¾-inch big guy axle. We looked at grinders, and various tools and decided to hit it with the traditional metal file and some cutting fluid. It took no time at all for the axle to slip in securely. Next we installed the front wheel on the stock Sportster front end with the springer stem. The bike set way too high. The stock ’39 stood between 4.5 and 5.250 inches off the ground with an original springer is place. Rodan, an avid Bonneville racer and SCTA official, told me recently, “You want your bike to set as low as possible and eliminate anything off the front that will interfere with air passage.” We need to keep lowering this sucker. It’s currently close to 6 inches in the air with the tubes pushed up through the top Sportster triple tree.
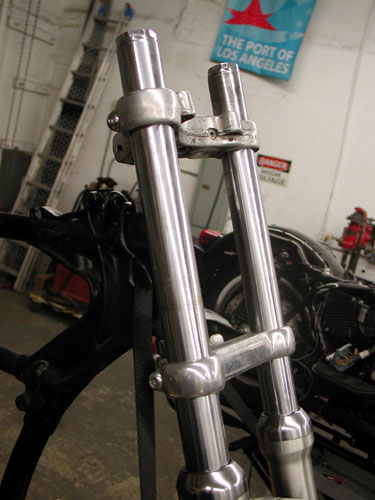

Next we needed to mount the rear fender so it would be ready for Jim Murillo, the master painter, to go to work. He already has the tanks and a stock Sportster front fender. We looked for a narrow front fender for the small Avon, 120/18, rear tire and discovered a heavy gauge Kraft Tech front fender and started pondering do-ability. We laid it over the tire and found some old rubber (used to vibration dampen handlebars). We cut it in two and duck taped it to the tire. For racing clearance we gave it about ¾-inch of clearance from the tire surface on the top. It was sorta tight on the sides.
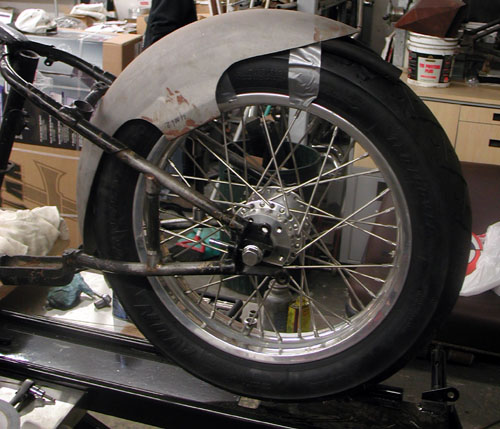
We decided to use the front fender tabs instead of shaving them and running standard fender struts. We dug around the shop for some stock that might match the material used to gusset the rear fender arms. We wanted to give it the same caped look as the gusset tubes with an outside sleeve at the ends.
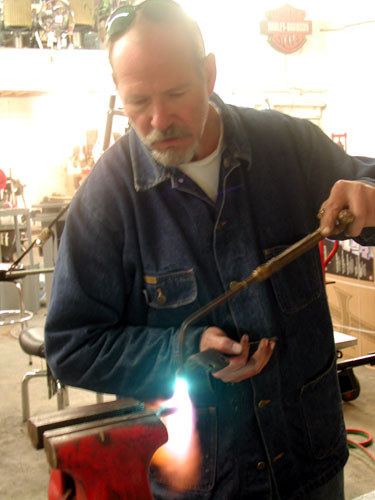
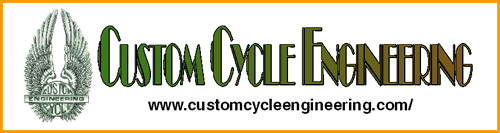


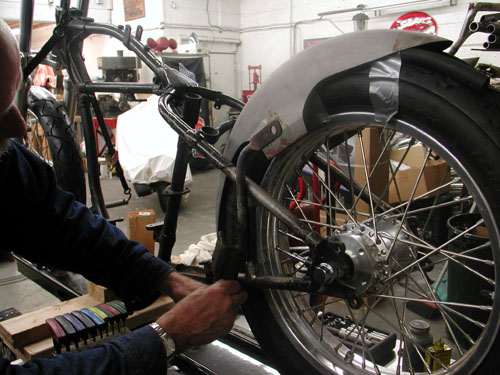
We discovered a solid rod, muffler bracket with tabs already in place. For a couple of days we monkeyed with the tabs, bending them, twisting the flats and fitting them to the fenders. We decided that since we were going with this configuration, that we would set it up so the fender could be moved to the right and left, if the wheel needed to be re-aligned.
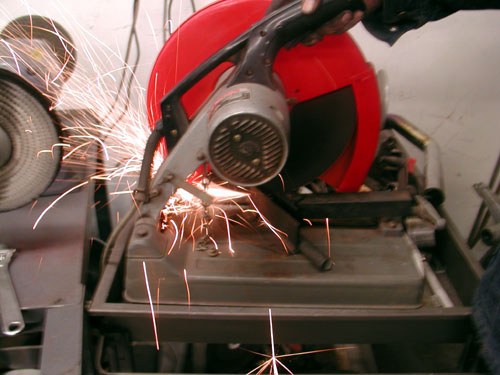
It took a lot of balls to make the initial cut. Even with adjustments built in, it’s nerve racking to fit fenders. The slightest shift throws everything out of whack.
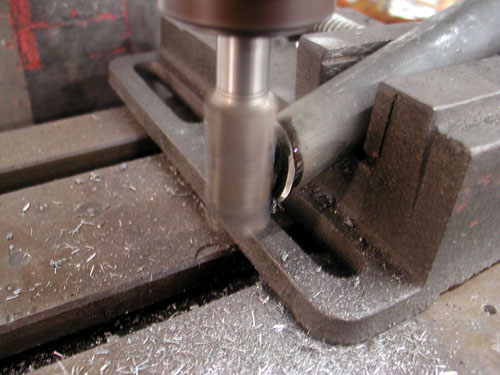
We found the right sized tubing to make sleeves from and began by setting up my mill so we could trench cut the tubing to fit the fender rails. This brings up a couple of wild stories. We’ve been fortunate to stumble into caches of machining equipment and I don’t throw a damn thing away. A buddy inherited his dad’s pad. When he moved in, he discovered a complete machine shop in the small teetering garage. He was rapidly building a business around “On-Site” hazardous waist collection bins. He needed to clear out the garage and called. We scored. Then we bought a cheap, used milling machine from Settle’s Cycle. This was the first time we put all the pieces together and fired her to life.
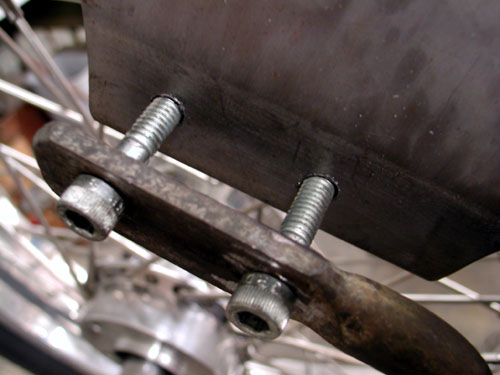
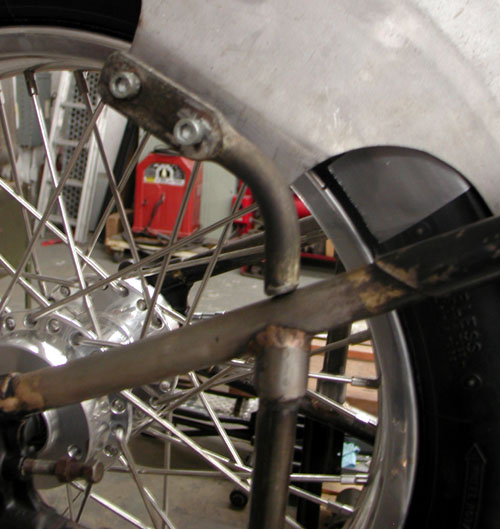
Next we drilled the tabs. They already had one hole, so we drilled matching holes in each tab and on the fenders. Then I went to work on developing spacers to hold the fender centered in the frame and over the tire.
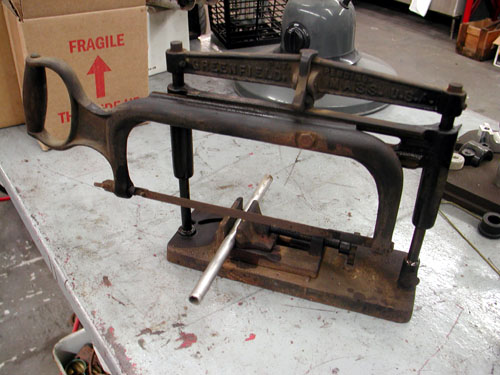
One of the wild benefits of living in an industrial ghetto is the strange opportunities that pop up. The Welder down the street was force to move, since the shop property was sold. He turned me onto a bunch of stainless tubing which would work out perfectly for this operation. Get this, recently a homeless guy called and told us about a shop that burnt down and the people were being forced out. We scored a bunch of old tools, including the above antique hacksaw guide.
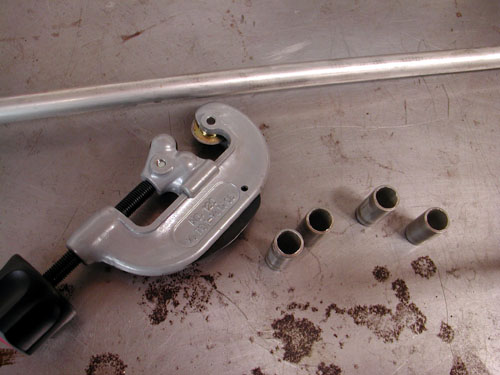
Unfortunately I didn’t have any blades that small. I turned to a tubing cutting tool that worked like a charm. I could cut segments almost any length accurately and cleanly. I cut a variety of sets, ¾-inch, 1-inch and 1.250-inch.
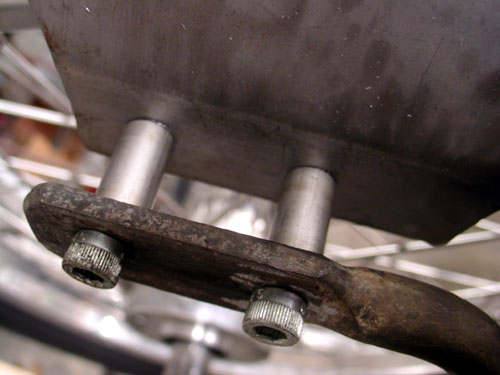
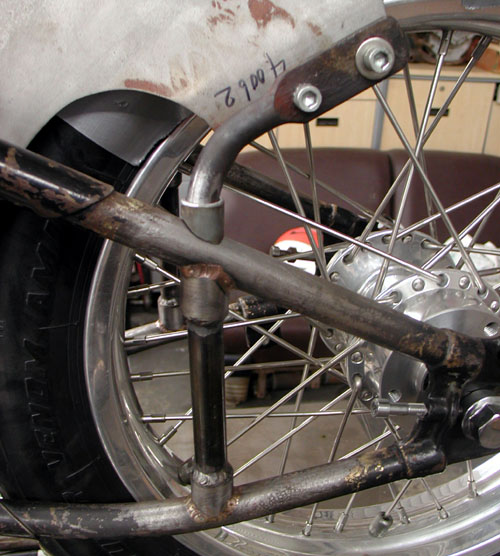
With the grooved sleeves in place and the spacer juggling act completed, we believed we had something going. There was a question about the welding, though. I called master builder Rick Krost, from U.S. Choppers, the man who straightened our frame. We discussed the frame sweat-brazing and avoiding any contact with brass. We also discussed his TIG welding with silicone bronze and the need to keep extreme heat away from delicate welds.

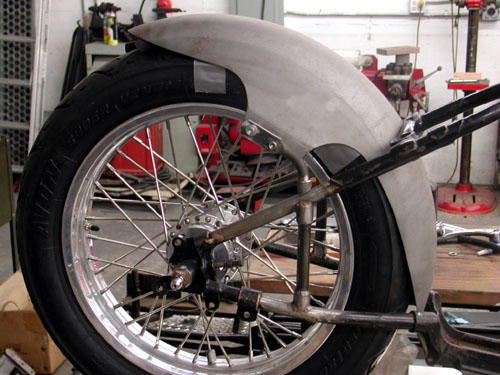
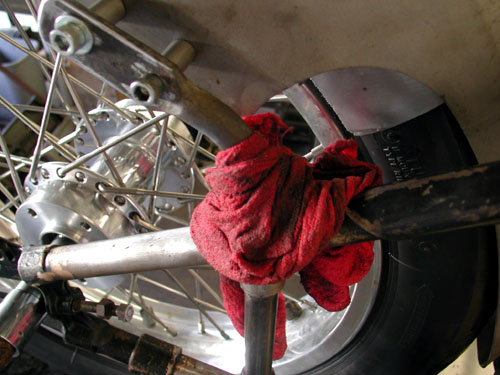
We decided that the best method was quick MIG welds that wouldn’t produce excessive heat. He suggested that I tack them, then rotating from side to side, welding from one tack to the next. I tacked them front and rear, then welded from tack to tack on one, then shifted to the other and finally doused them with a wet rag to prevent the heat from lingering.


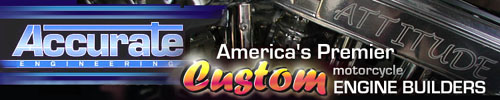
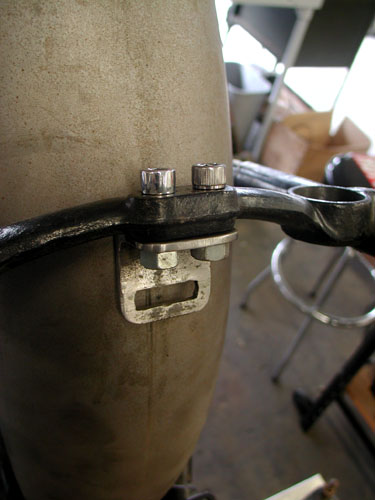
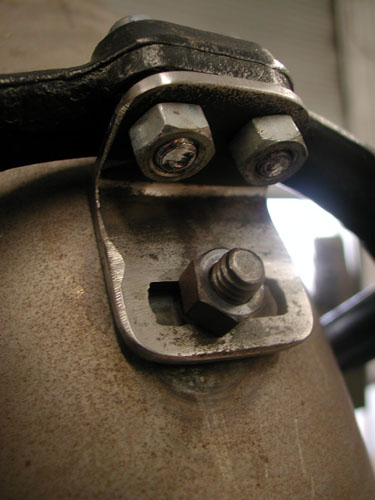
With the fender rails in place and fasteners tightened we discovered that we still needed something in front, although we were elated with the outcome. They were solid as hell. We cut a chunk of angle iron and drilled it to fit the frame. Then by drilling and using a Dremel tool cut-off blade, we cut a slot in the bracket to allow the fender to be shifted right or left. Finally we welded a bolt to the inside of the fender for ease of installation and adjustment.
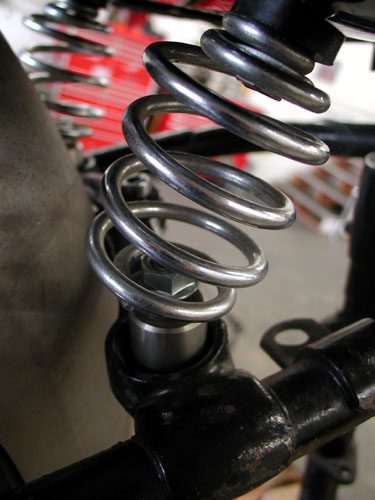
The last element we could mess with, at this stage was the seat. I’m constantly shifting seats around the shop. This seat was destined for the Salt Shaker for awhile, but it fit the 45 like a glove, so I looked for spacers so it would sit enough above the fender and the springs wouldn’t rest against the frame and fuck with the finish. I save anything that might be considered a spacer. We dug through the drawers and discovered two perfect units, made of stainless steel, a bonus.
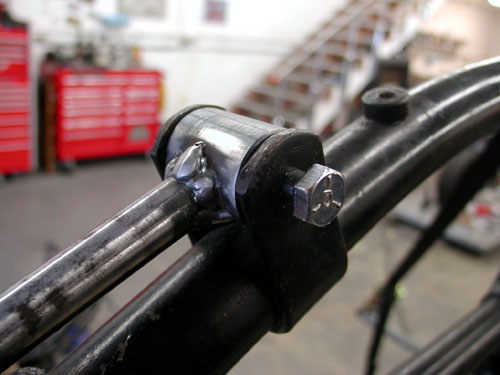
Back to the milling machine and shop lathe we cut a spacer for the front of the seat and machined it for a perfect fit. We furrowed another chunk of tubing and welded it to 6-inches of steel strap. It was drilled for the bottom of the seat then welded to the tubing.
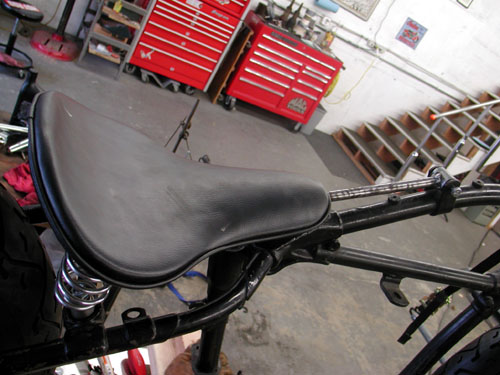
The seat fit perfectly with the bike. We are trying to position Valerie so she can tuck in and low for the blast along the salt. Wait till you see the handlebars in place.
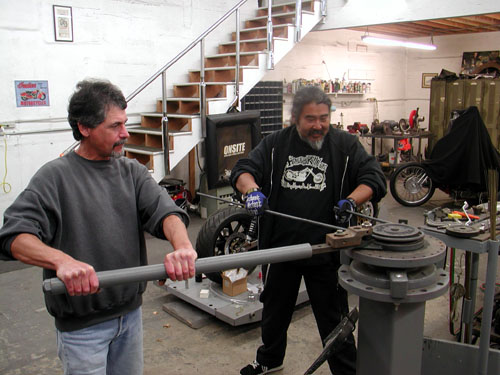
We were just about to slam the door shut on the shop for the night when Japanese Jay showed up and asked for help building his sissy bar. It was another chance to get some experience with our Bill Hall strap-bending machine. Chris Kallas our official Bonneville Team artist was helping us with the 45 and gave Jay a hand bending the solid stock.
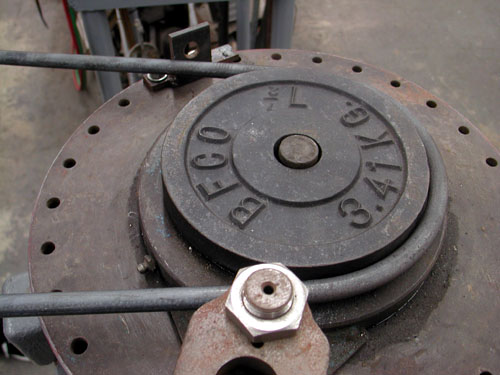
We looked around the shop for the perfect diameter guide and discovered various weight plates, from the Bikernet Gym, might do the trick. We tried 2.5 pound, 5 pound and ultimately 7.5 pound, which worked like a goddamn dream.
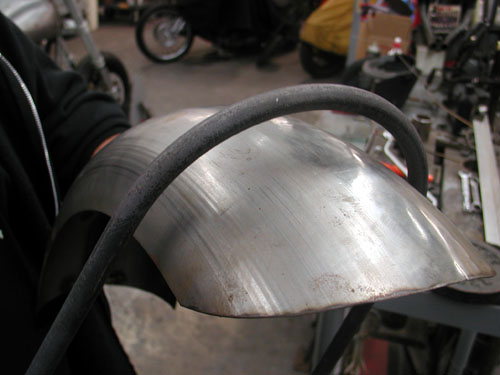
This move could be introduced in any shop with a weight plate and a strong vice. It would be tougher to handle than with this bastard, but you could pull it off. The rail fit Jay’s fender like a dream.
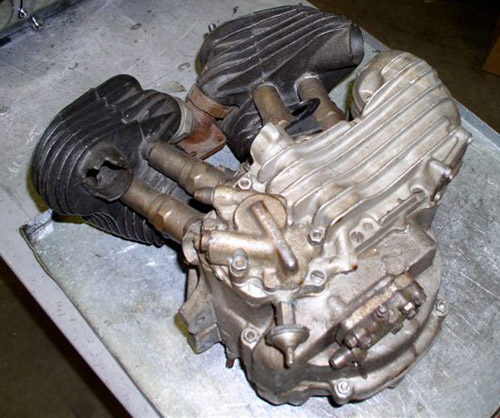
Wait, there’s more. The brothers, at Departure Bike Works, have stripped the Bonne Belle engine and are preparing for hop-up rebuild. The initial plan called for running two front cylinders, dual carbs and bigger valves and pistons. I snagged Greg from the Service Department:

Klink Walton (resident guru of flatheads & other things ancient), and Billy Wheatley (resident motor wizard & stripper afictionado) were the two brave souls who tore into this old, decrepit hunk of iron. Overall, things went pretty smoothly, although Klink forgot to bring all of his special 45″ tools (some guru, huh?)
A few things we noticed were, one of the cylinders had a broken exhaust flange. No biggie, Klink wants to use a set of WLDR cylinders (if we can find a set, hint,hint Bikernet readers). We also noticed the motor had a military oil pump set, by the olive drab color they were sporting. Nothing major, just an interesting little tidbit.
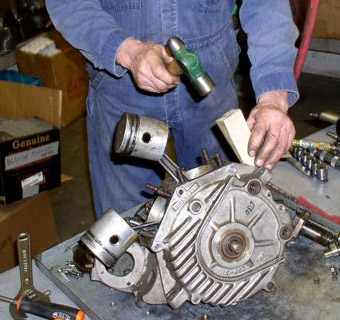
We noticed that the cases will need a bit of welding and machining, but WTF did ya expect on a motor of this vintage. It was about this point that Klink realized the need for a special case splitting tool, so off he went to the bandsaw, and returned with the tool you see pictured. I'm sure it'll be available in the JIMS catalog shortly…
Anyway, the cases were split, the flywheels removed & disassembled, blah, blah ,blah, and we were left with a large pile of parts that smelled like the funk of forty thousand years. Our next step will be to separate the good from the bad & the ugly, and order all the trick parts we're planning to use in this beast(if you can call a 45″ flatty a beast), so STAY TUNED!!!!!
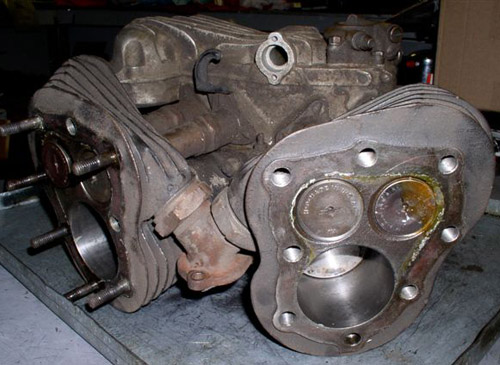
These are WLD cylinders and WLDR already have larger valves and better ports with less distance to the cylinder. The Departure Bike Works boss asked if I could find two front WLDR cylinders, which seems an impossible task. I don’t feel right about breaking up a set either, so I think we’re going to weld up and machine the ports and machine the heads for larger valves. We still need to find another front aluminum head.
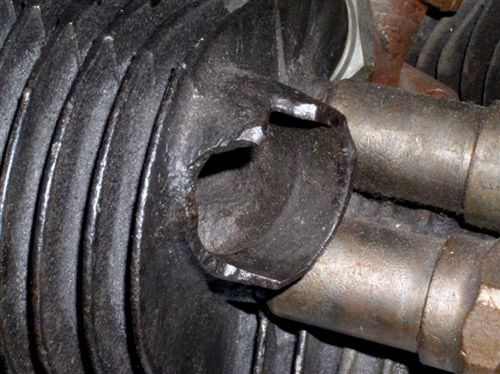
The next challenge is having new cams ground. Again, I spoke to Rodan who told me that KR cams will work, or Andrews Bonneville Sportster cams for higher lift. We need to separate the lobes from the gears, switch gears for the reversed valves and put the sets back together. We’ll see. More reports coming soon.
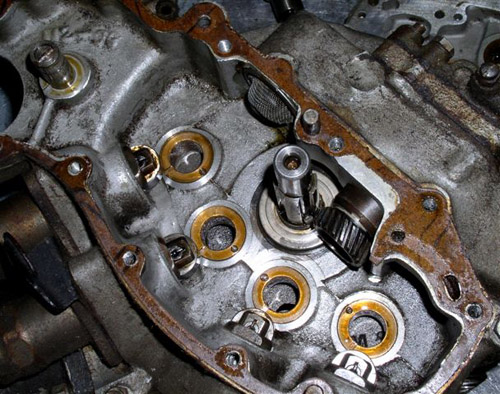
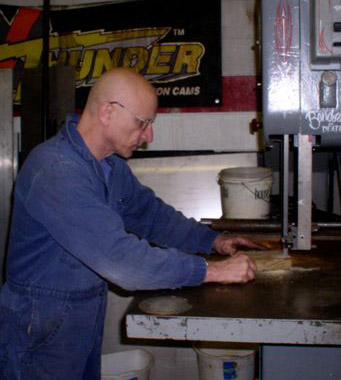
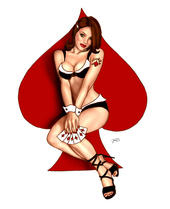
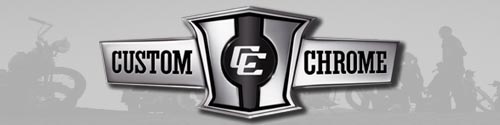

Bikernet Bonneville 2006 Effort Part 4
By Bandit |

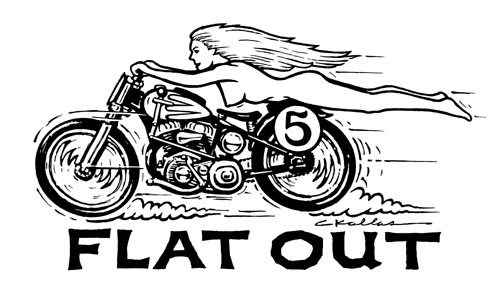
In the last segment the crew of U.S. Choppers straightened the Bonne Belle, 1940 45 frame, but I asked Rick Krost, da boss, if he felt any gusseting was necessary. He pointed out all the strong factory gusseting in the front and even on the single down tube, but suggested that we gusset the rear legs to strengthen the point as which the power hits the salt. My concern was in many respect for Valerie Thompson, our Bonneville Salt Flat rider.
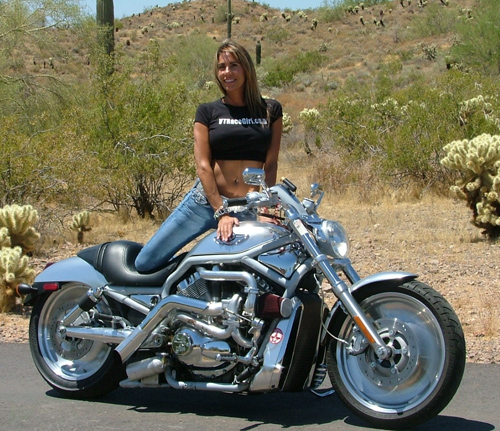
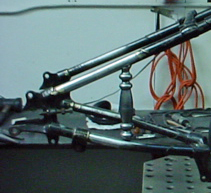
I could tell, while working with Rick, and witnessing his watery blood shot eyes that he was either coming down with something or hungover. His first rocking chair gusset notion met with mixed reviews.

First, I coped the pipe after fitting it all to make sure it would all line up right and fit snuggly to the rear frame rails,” said Rick Krost. “I compounded the top “fish lips” by running the mill head at an angle… 25 degrees to be exact.”
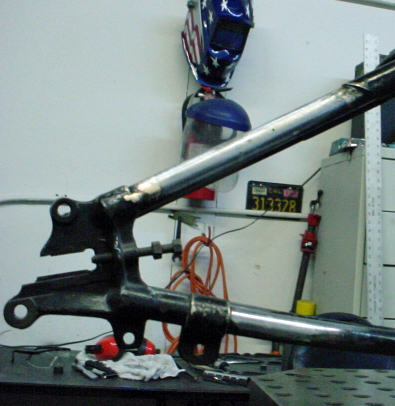
It's real important to have the weld area clean before welding… nothing like emery cloth and elbow grease.
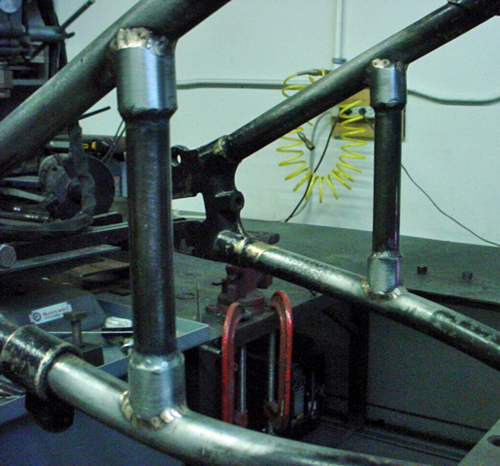
To make matters fun, these old frames are all furnace brazed. There’s brass everywhere on these frames. A lot of the times the pits in the metal keep you from cleaning all the brass out of the clean metal, which is bad for welding mild steels with 70S2 rod. It will contaminate your welds and they will fail.
“I chose to weld the pipe to the stanchions with steel,” Rick said. “and then weld it to the frame with Silicon bronze to avoid any contamination issues or weld failure.” Another benefit of SIB is that we can work around the tubing quicker as it has a lower melting point so as not to put too much heat into this old brazed frame..
”I used a clay heat sink in front of the castings or a sloppy wet rag,” Rick said, “depending, so the heat doesn't crawl over to that nice furnace brazing and loosen it!!! This could be bad!!!”
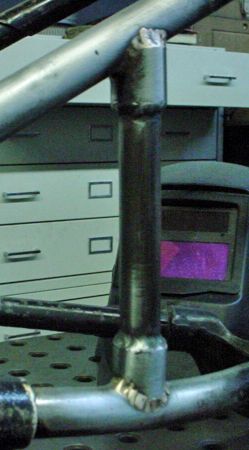
Done deal– the supports lined up well and were symmetrical. The 3/4 tube was used to help with any possible chain rubbing issues and they tuck up nicely between the frame rails.
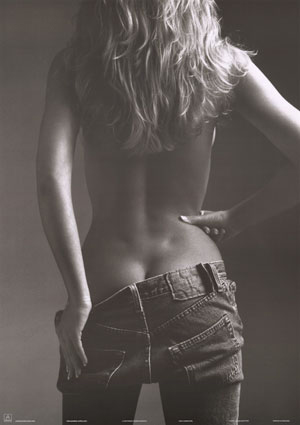
Look at those rear frame rails. Notice how they line up and are parallel to each other? That was the frame fairy's work the other night…. boy is she good. “This frame was about 3/8-inch out of alignment, when we started this project,” Rick said. “U.S. Choppers putting old steel back into use again!”
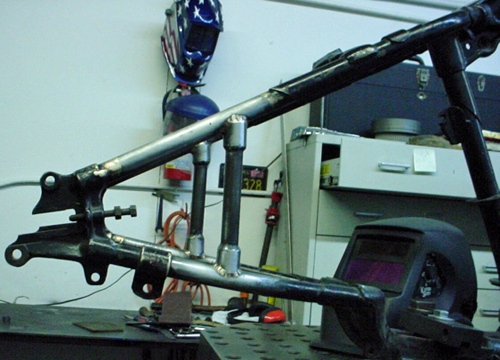
“Hey Bandit, come down with this flu…,” Rick sniveled, “I'm outta here… go cuddle up to my wife and her girlfriends. It's 8:00pm and I'm hoping your liking the finished result.”

He only uses Proto-Fab tubing. It is seemless, cold rolled and drawn over a mandrel bender. No seems or scale that must be removed. “All size increments will slip-fit over the next size,” Rick said, “so no machining was required.” He welded each piece with silicon bronze rod using a Lincoln TIG 355 battleship welder.


Bikernet Bonneville Effort Part 3
By Bandit |

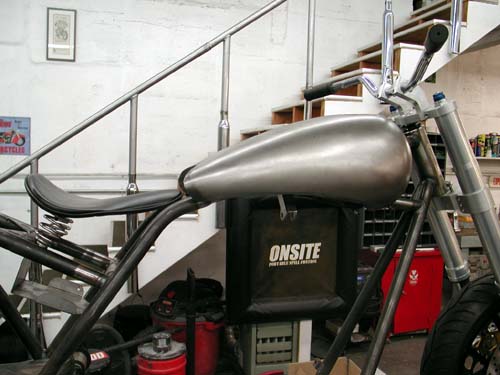
We’re rockin’ with this project. I’ve never built two bikes at once, Bonneville aside, but we’re having a blast. Both projects are hustling and this report will bring you up to date.
The CCI V-Bike Panhead is still a roller and we’re waiting on the drive-line elements so we can mock-up the pipes before shipping anything to powder. But we decided to grapple with tank mounting and messing with the seat. But first here’s what Berry Wardlaw said about the 120-inch Panhead from Accurate Engineering:
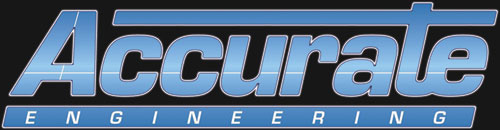
First off, good morning! I am sending a mock-up engine so you can continue the build and I will give you the theoretical specs for the exhaust diameter and the length. The specs for the exhaust will be for stepped and straight headers. I came to this design from a computer generated program which has been very successful for me in the past.
The REAL engine is going to be pure race and the components have already been ordered. Still waiting for the crankcases but believe (have been told) they are ready. The exterior dimensions of the engines will be the same.
I will include the 3-bolt exhaust flanges. I am using many titanium internal components, modified components as well as custom squish areas, custom oilers and coatings. Ryan Baisley is blue printing my rocker arms (true 1.5:1 ratio). We have been overwhelmed with orders and the Biker build-off thing is getting to be a too much but we are hanging on.
I have two court dates this week, so maybe I can get this shit behind me. I promise to be good. As good as I can be.
–Berry
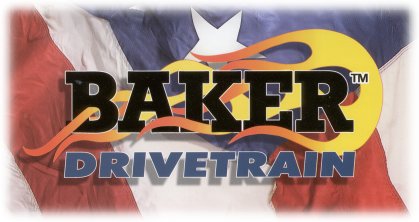
We’ve sent the transmission specs to Baker Transmission, but haven’t heard anything back. They’re a tough group to communicate with. I’ve offered to write articles about their products, but can’t get a return phone call. We’ll keep trying. I have a lot of respect for their components and we’re determined to use one of their transmissions. Following are communications with John Reed, Custom Chrome Designer regarding the transmission:
The V uses a touring tranny, but any FXR unit will be OK. It uses one of the CCI extended chain sprockets, with the same teeth as stock. But Baker sells a sharp one, If there is any problem with the offset /teeth, etc. let me know and I will go down and measure one. If the back of the engine is the same as a (rubber mount) FXR/dresser, and the front part of the tranny is for a (rubber mount) FXR/dresser, it should be OK.
As far as I know, the back end of the engine mount is the same on Shovel and Evos, and I’m sure Panheads, and late model FXR rubber mount trannies bolt straight to the engines. It’s only really early r/m trannies that need a separate bracket.
The twin cam tranny won’t bolt to a non twin cam bottom-end engine.
On my Vs, with a 110 revtech, I have never had a problem with the engine moving with the tranny, using a stock OEM inner /outer primary, which is a really good stabilizer.If you are using a belt drive with a good billet piece that takes the place of the stock inner, you should not have a problem.
How much hp/ torque do you have on the engine you are using?The V is a lot different than a the Softail setup, that most choppers use, the primary is shorter, and seems to be a lot more rigid.
CCI has a V going to Daytona, Why don’t you ask Your butt-hole buddy, Sean, if you can ride it around, so you can get used to it.
–John Reed
Custom Chrome
John’s in constant trouble with the brass. We will run a BDL primary drive. That brings you up to date on the driveline. Now lets shift to the tank installation.
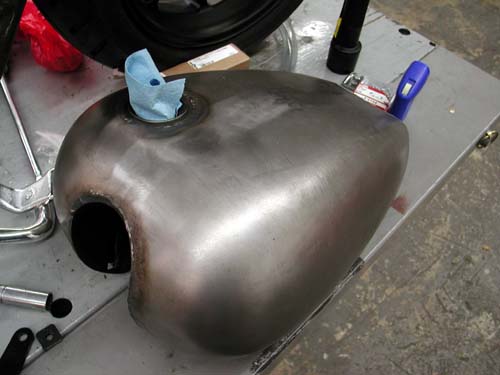
I believe this is a Regency built tank for Custom Chrome. It was designed as an adjustable stretched fuel tank for Softails, 2000-up to contour a seat, in this case a Corbin job. Because of the multi-fit business I received all the brackets to make the tank fit an H-D chassis, then separate fasteners for the V-frame. That often creates confusion. Actually Bikernet Black Market John saved our ass. “Hey, this is going to mount like a lot of Jap Bikes,” John said. “It slips into that scoop thingee and just bolts to the rear.”
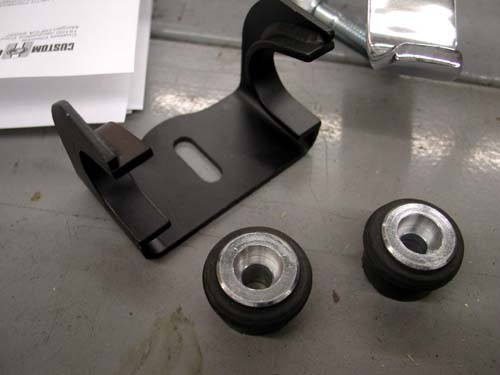
Fortunately mounting to the V-frame eliminated a lot of heavy bracketry that we endeavored to use, only to find out we could shit-can them. I never toss any brackets. You never know…
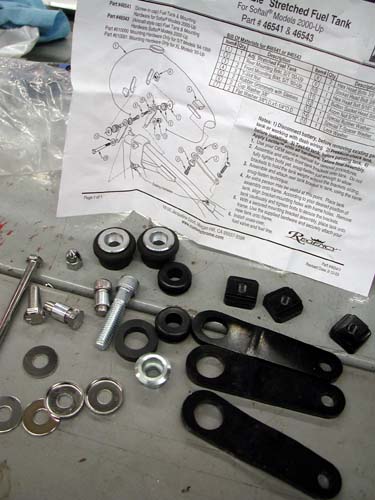
Some of these extra motions I don’t mind, because we become familiar with their use and will know how they work for future reference. Never know when we might wrench on a Softail.
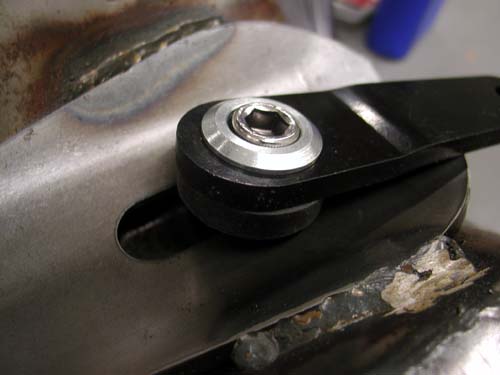
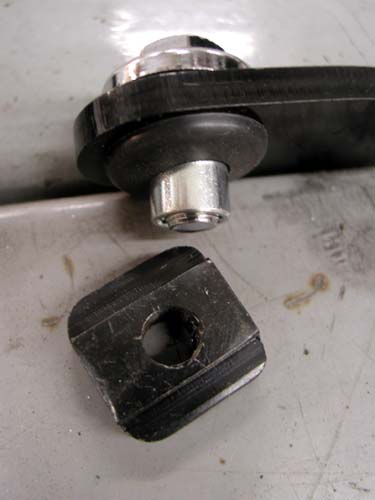
I asked John Reed if I should put a gusset in the neck. Here’s how he responded:
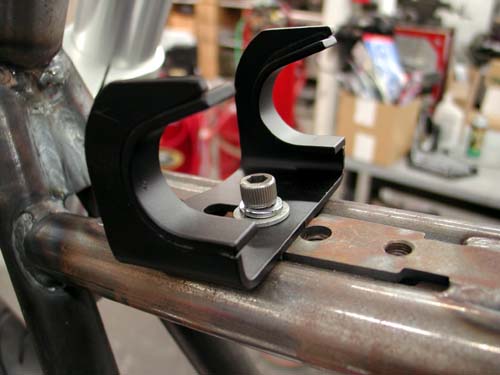
Good news. The frame passed the European TUV test.Our engineeer is back from the states and has just talked to the TÜV.
To pass the TÜV test a frame has to bear 100.000 load alternations. As we have tested the Paioli front fork at the same time the frame was tested with 500.000 load alternations. So the frame beared more than 4 times the standard test.
regards
–Günther
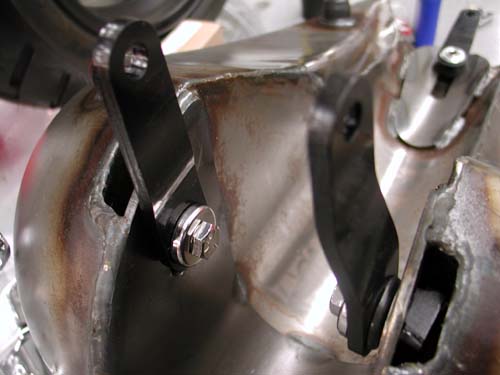
The above shot shows the front Softail mounting brackets in place. The shot below demonstrates how these brackets weren’t going to work. I must have installed and removed this tank a dozen times before I discovered the error of my ways.
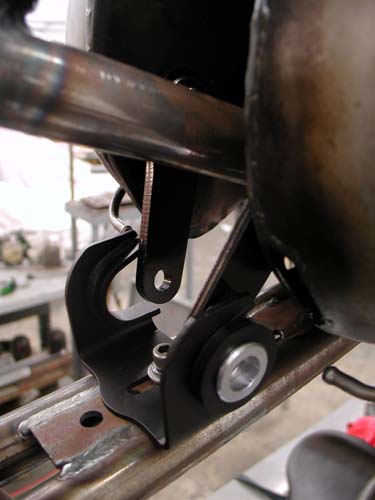
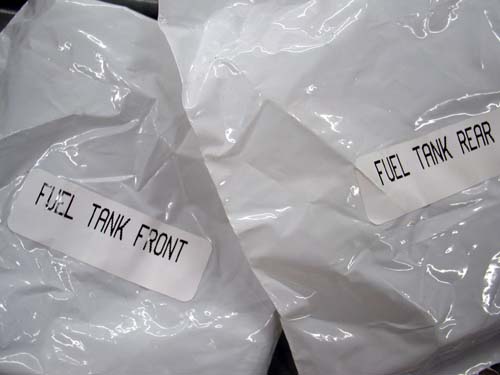
Once Black Market John straightened my sore ass out, we discovered the additional fasteners, carefully labeled in a box. Suddenly the mounting system seemed extremely easy. Mount the rubber grommets into the slider rails, fit them to the scoop, set the Corbin seat in place for accurate tank placement, tighten the Allens in the front tank mounts with the tank adjusted to the perfect height, and we’re golden. That’s the way it should go.
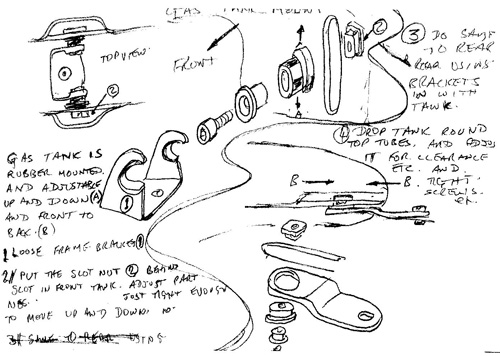
I dropped John Reed a note and he sent me the above sketch, which answered some question, but then we ran into a problem. The scoop is a half-inch narrower than the thick slotted slab of steel bent to fit into the tunnel of the tank and the slots don’t line up. They’re not even. We added spacers to the rubbermounts so they would reach the bracket. That would have been golden, but we couldn’t squeeze the tank over the backbone of the frame.
We removed the spacers and tried again. What seemingly would been the simplest way to mount a gas tank had us completely perplexed. Even with the spacers removed, we can’t get the tank on without removing the scoop, which defeats the purpose of this system. We’re still investigating.
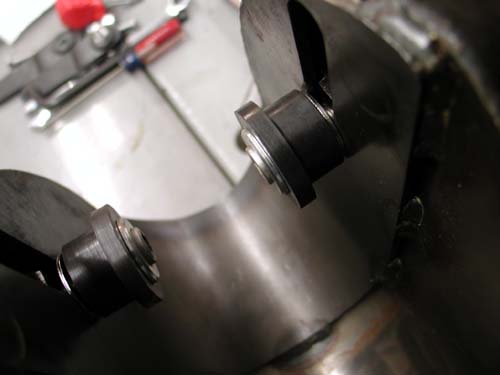
Since this is going to be ridden at Bonneville and we’re calling it the first Sportbike Panhead, we removed the Corbin seat and the plastic tail section and decided to run a sprung slim solo from U.S. Choppers and make the brackets that we can slip way back so the rider can lay on the tank for a fast run on the flats.
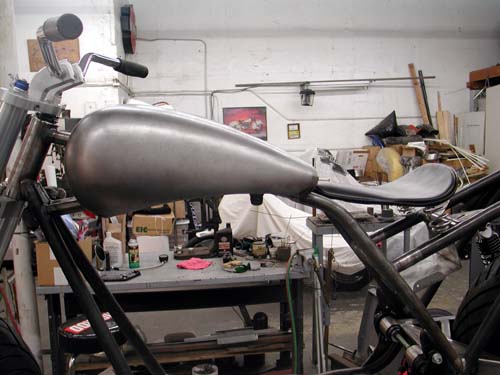
We’ll get to the bottom of the tank mounting and mount the seat in the next segment. Hang on. Let’s move onto the Bonne Belle, 45 Flathead progress report.
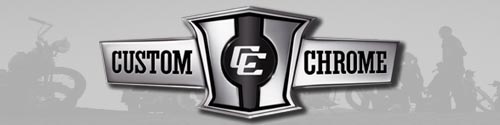


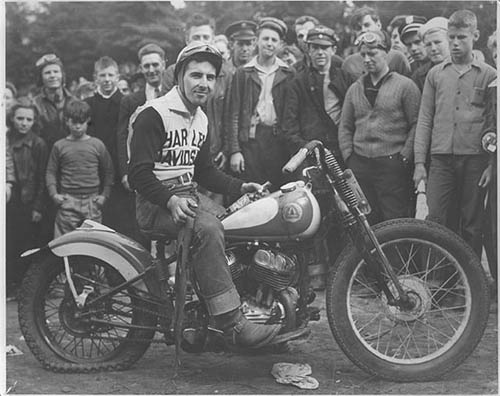
We’re working like mad dogs to create a roller while Klink and the crew from Departure Bike Works rebuilds the engine and transmission. We’re basically building the 45 cubic inch flathead above, with a handful of upgrades, including the recent 39 mm Sportster front end and PM disc brakes and wheels. We are also planning to shift it to a foot shift bike using Tedd’s cycles mods.
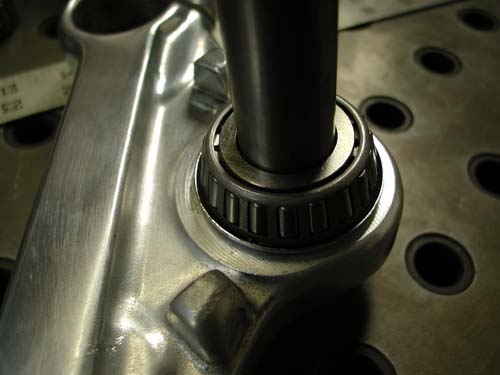
With the help of Larry Settle’s bike shop in Harbor city we machined a Paughco 45 springer stem and pressed it into the late model Sportster aluminum tree. Larry bore a hole in the bottom and taped it ¼-20 so we could install the below Allen and washer to prevent the stem from pulling loose.
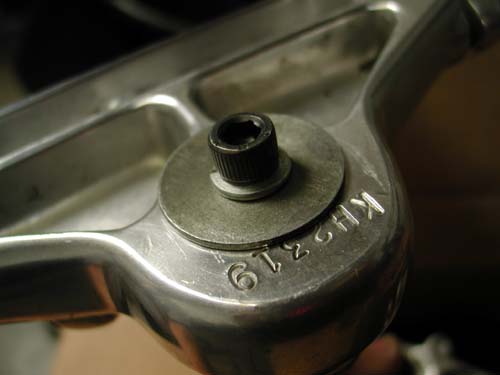
We installed Paughco neck cups allowing us to eliminate ball bearings for Timkens. See shot below.
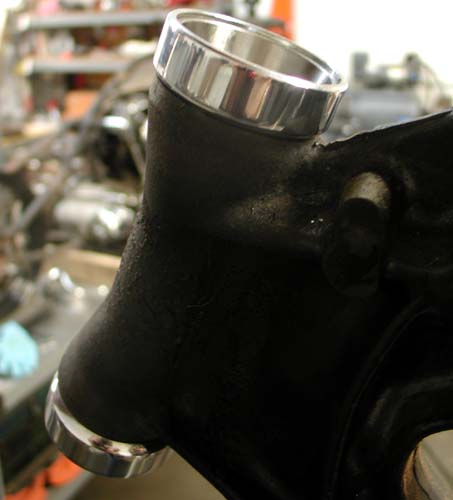
This created a quirky dilemma. The stem was long for a springer. We had a choice to make and an unforeseen opportunity. From Timken bearing to bearing the neck measurement was 6 3/8 inches. We discovered later that today’s Sportster neck is 7 ¼ inch from top to bottom. We could have turned the Sportster stem to 7/8-inch, but we decided to try the springer stem. For one reason, this system will allow us a more secure pinch bolt system above and below the top triple tree.
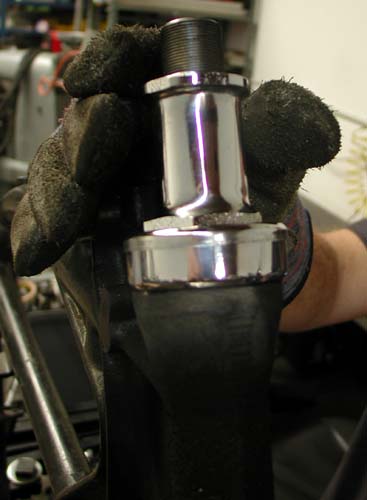
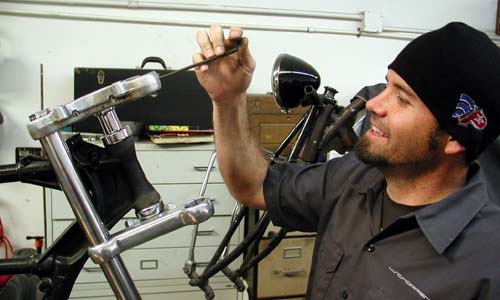
We took all the re-machined front end parts to Rick at U.S. Choppers so the frame could be checked with both axles in place for the most accurate frame check.
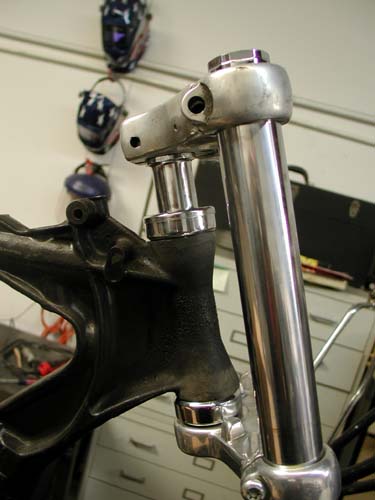
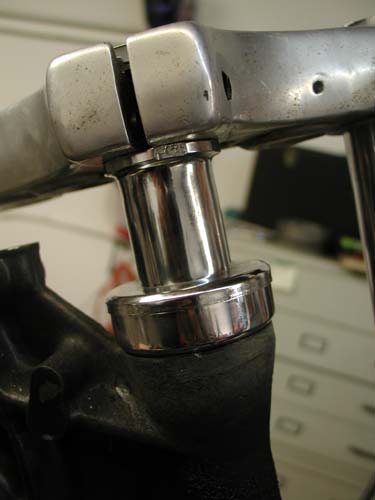
Larry Settle machine chamfers in the springer nuts to slip inside the top triple tree for the most accurate secure fit. We also machined the springer nut down to make the best use of the stem with a nut on the top and bottom.
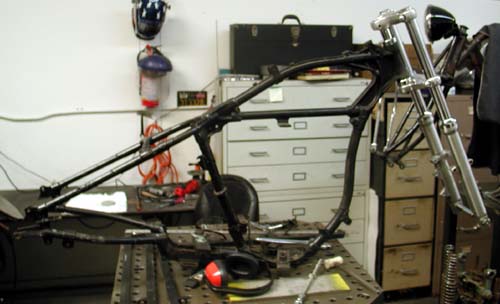
Above shows the frame with the front end in place. We will fit up a PM wheel shortly and decide if we need to shorten the tubes more. Actually doesn’t look too bad. Using the springer stem lowered it almost 2 inches.
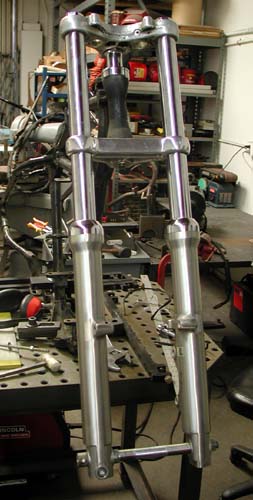
We already have a set of black powder coated lower legs ready. We will probably powder coat the trees black also.
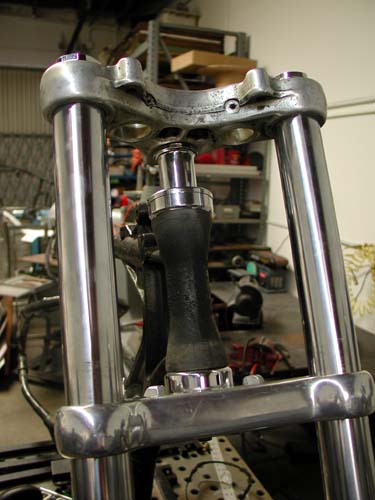
Here’s a close up of the trees in place. After Rick checks the frame, we’re ready to pick it up.
Here's The Report from U.S. Choppers

First, we cut through the frame in several places, making sure to cause as much damage as possible. Actually we're cleaning up an old mess with da grinda. It’s a highly technical and grueling operation requiring skill and tenacity.
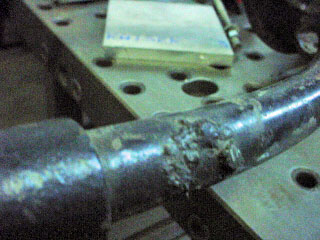
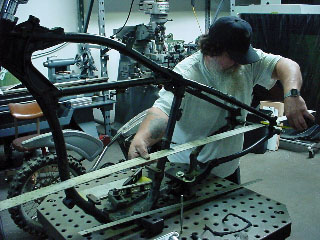
Local expert vet and living legend, Fat Paul, bending the frame into place with shear strength using a hardened piece of spring steel which acts as our straight edge. Go Paul, go.
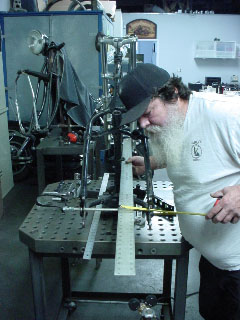
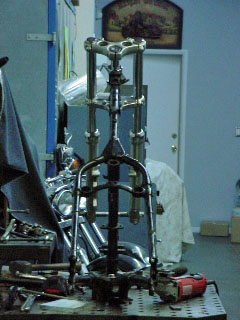
The frame fairy came over night and delivered a fresh straight frame….. straight and true like an arrow. Disclaimer: no heat was used nor animal testing in conjunction with this experiment.
U.S. Choppers
2039 S. Lyon St
Santa Ana, CA 92705
714-546-4699
Appointments Only Please
http://www.uschopper.com/
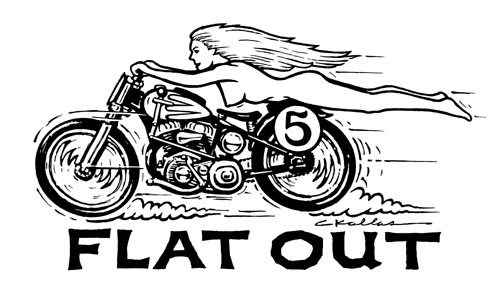
And now a report from Departure Bike Works, in Richmond, Virginia– Lee Clemens and his crew are responsible for the engine and trans rebuild and hop-up. Fortunately we had a set of performance aluminum heads and an extra front cylinder. Lee is planning to have special cams ground and run two front cylinders with dual carbs.
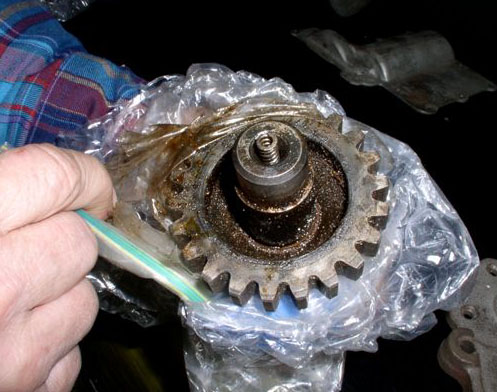
”I know, I know, better never than late, right,” Greg, from Departure said? “Not a whole lot to report yet. I finally got Klink to come by & take a preliminary inventory of what you sent. He just had one comment…..’You CAN'T put an ELECTRIC START on a Bonneville contender!’
I'll have more soon…..”
Keep It Greasy,
Greg @ DBW
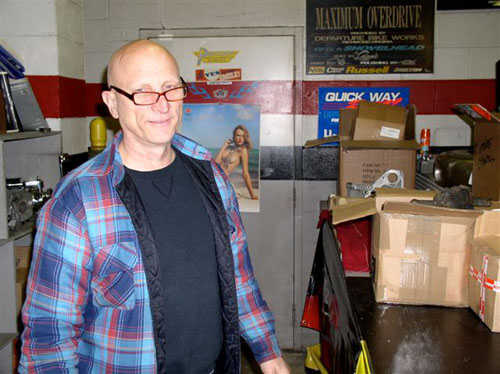
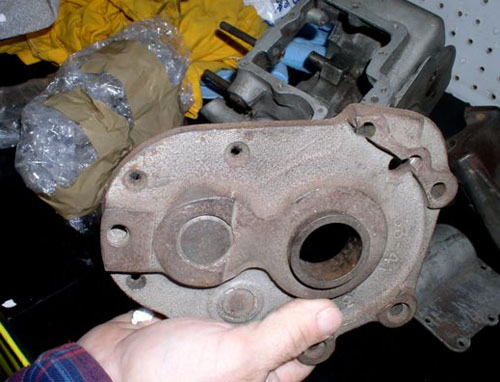
I’m pumped. I may pick up the frame tomorrow and then I’m working with PM and a dirt-bike-foot-controls guy to set up the complete roller. Once we fit the tanks with a new petcock they will be shipped to Jim Murillo for paint with the fenders.
Hang on for the tank and sheet metal tech, coming soon.
–Bandit
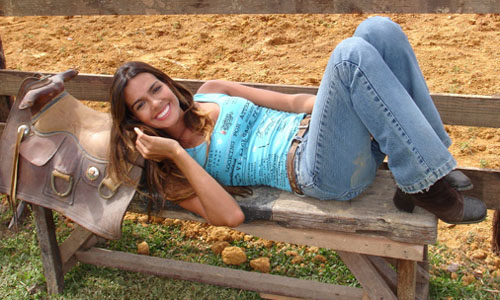


Bonneville 2006–Salt Shaker/Bonne Bell 2
By Bandit |
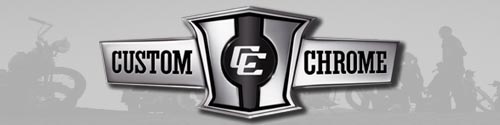
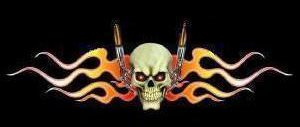
We’re building two bikes to take to Bonneville for the Bubs International Speed Trials, September 3-7th, 2006. So each segment we publish may contain elements of both, the 1940, 45-cubic inch flathead and the first ever Sportbike Panhead designed by John Reed of Custom Chrome. It’s his V-Bike and we’re dropping a 120-inch Accurate built Panhead engine in it with a Baker 6-speed trans and tie the two together with a Compu-fire/BDL primary drive.
Since this is a learning experience for all of us, from several standpoinds, I’m going ask numerous questions. Hell, I asked anyone who will listen to me. I’ll watch the World’s Fastest Indian over and over. I may stop folks in the street. I asked John Reed about the fasteners supplied with the V-Bike from Custom Chrome. I had a couple of concerns. This wouldn’t be the ordinary street bike, but a rubbermounted scooter that we’re going to push as close to 200 mph as possible. We want it to hang together and especially of Valerie Thompson is aboard the beast. Here’s what John had to say:
I think because they are a lot bigger than they have to be, so I think they are quite adequate if you have washers both side, I usually change hardware on my own stuff, because I try to make them as small and neat as I can, like on race cars or airplanes. I like good quality stainless, so I can machine the heads and wire lock them without rust. I take things off/on a lot of times in the busy areas. I tend to use better quality air plane qty stuff if I can get it, I hate chrome hardware.
Tim Remus phoned me years ago and asked if he could come down and photograph my hardware stash because he was going to write a book on it.
”Why,” I ask?
He said, “Because you are anal.” I had never heard the word before, and I racked my brains to see if anything I had done before has come out of its closet and was going to kick me up my anal passage. I was worried. I am all mouth, but perhaps he didn’t think so.
He worked diligently for a couple of days pulling parts out of the screw racks, documenting and photographing, and I asked him what the fuck was anal, and who has been talking, etc. etc. etc.
He pulled out a little box filled with washers. He said, “What about these?”
I said they are machined, high quality stainless washers that are chamfered on the inner face, so they fit perfectly in the high quality stainless screw, hollowed in the head for lightness, with small holes in 6 places for lock wires.
“Where did you get them,” he said?
“I got them in an airplane scrap yard when I lived in England.”
“When did you get them,” He continued to question?
“About 30 years ago,” said I.
“Why haven’t you used them for 30 years,” Tim kept grilling me?
“I’m waiting for a special project,” I replied. “It’s a shame to waste them on something mundane.” I found out…… that’s fucking anal.
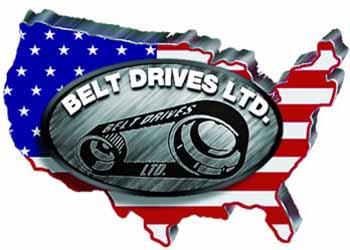
Axle adjuster on the Sportbike Pan
We installed the rear swingarm axle adjusters and were curious about two things. First I like a solid slider on the inside of the retangular swingarm to support and add strength. Plus the CCI chromed caps for the back of the swingarm didn’t seem to fit. John Reed filled me in:
They sell the kit with the OEM adjuster with the steel plate, you use the axle spacer with the thread part of the adjuster, but there is (or there should be) a billet cap which replaces the oem steel one with your hardware.
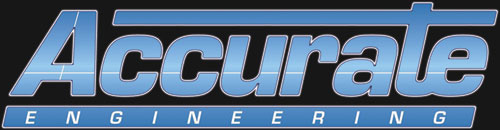
V Steering Neck
I also asked John if I should add a gusset to the neck. The frame appears very strong, but I considered a neck gusset. John set me straight:
I have never had any problems with the head, The frame tube is way thicker wall than needed. The lower tubes have a gusset below and the double top tube takes the weld round a lot of the neck. The FXR style big diameter necks spread the load round a larger area and are a lot stronger than the smaller dia ones used on Softails, etc. I don’t think they need additional gusseting,
I have had problems when I used the lower bearing straight on the lower tree, and I always put a spacer (about 0 .150-inch thick) under the bearing.
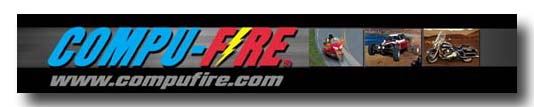
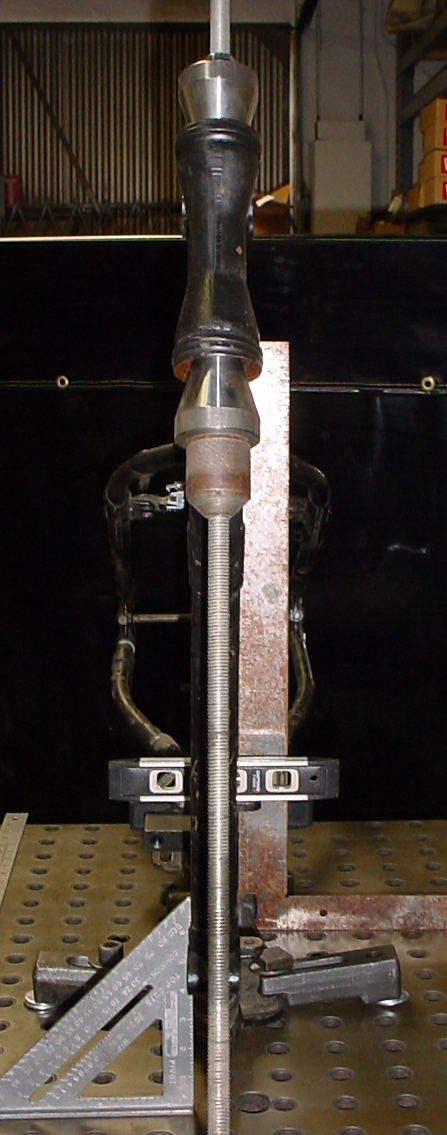
45 Flathead Frame Straightening by U.S. Choppers
First we put the frame on the table and leveled the table with a Starrett master precision level. This gives the table .001 accuracy. Then we began to level the frame to the table. Starting by the motor mounts we leveled the frame in both X and Y axis. When this was achieved we checked that the motor will sit level in both X and Y planes. Once it is determined that this was the case, we can assumed that the front down tube and the center post were in alignment for both X and Y axis as well as the top motor mount was parallel.
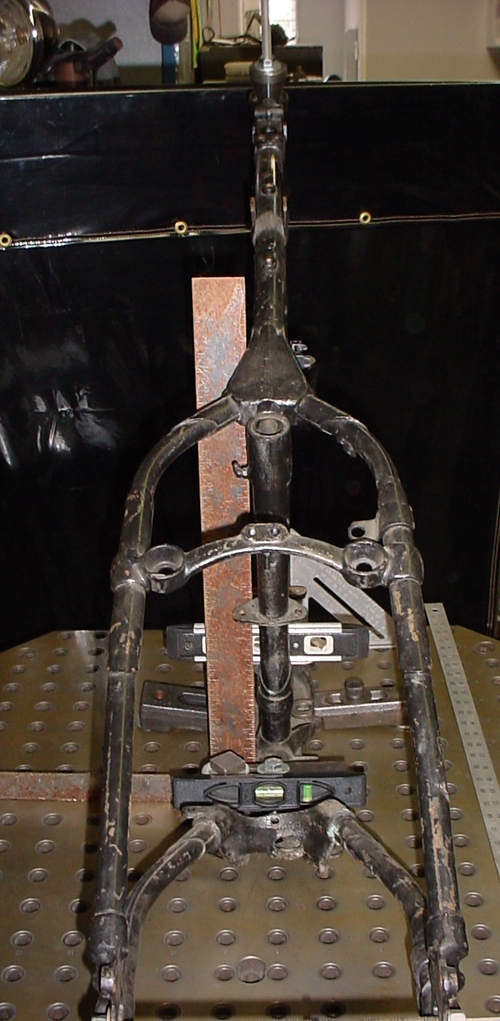
From there we worked back to the tranny mount. The trans must sit parallel with the motor mounts in X plane so as not to cause excessive chain binding. Working back to the rear axle we needed to determine if the rear chain stayed (the rear triangle) in alignment with the rest of the frame, especially in relation to the steering stem alignment rod. The rear axle must be directly perpendicular to the steering alignment rod.
Following this, measurements will be taken from the center point of the rear axle in relation to the steering alignment rod to make sure the rear axle stays are not swayed to one side or the other. This process will begin next week.
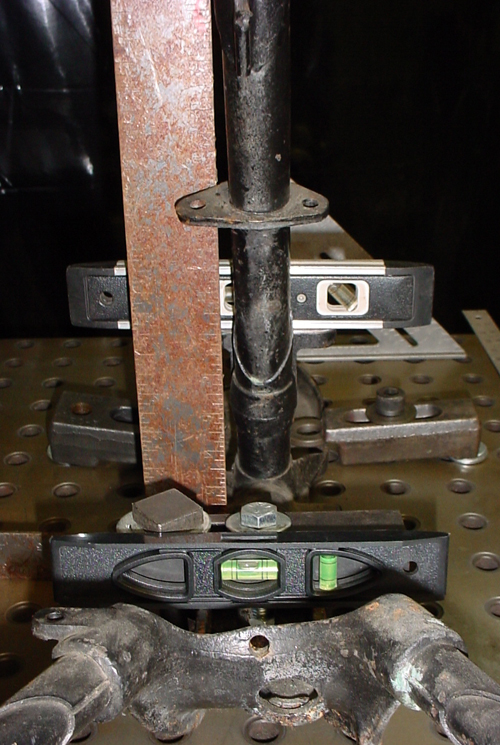
So far we have proved that the neck post, motor mounts and tranny are in sync with each other. Next the most important part will be examined… determining the rear axle position to the steering neck for frame bowing and alignment.
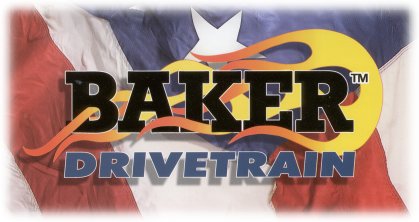
Hope all is well…. been thinking about this EPA deal. I'm with the MRF on this one and am planning on putting the questionnaire on my site for people to forward on- keep up the good fight. You’re one of the few who are persistently posting EPA stuff….. We need to stay on these assholes!!!
-Rick
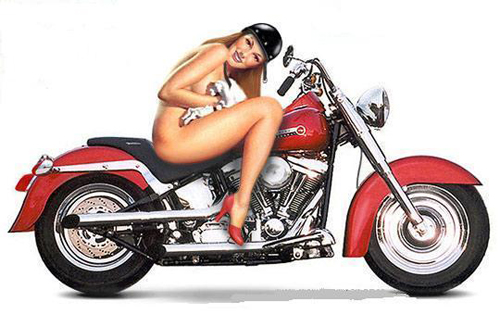
U.S. Choppers
2039 S. Lyon St
Santa Ana, CA 92705
714-546-4699Appointments Only Please
http://www.uschopper.com/

