The UL File Is Now Open, Episode 1
By Bandit |
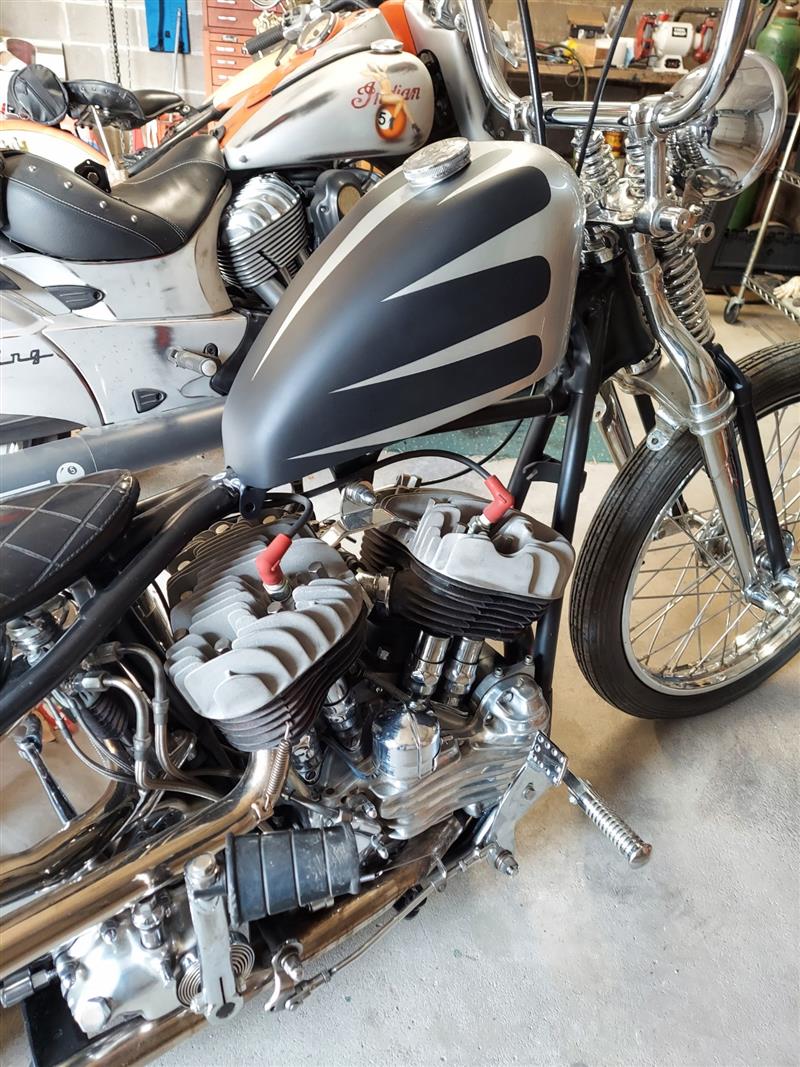
It all started in the center of an odd South Dakota winter, 2022 and a hunt for a running Knucklehead engine. I found myself talking to several knowledgeable brothers in the industry and the price for Knucklehead engines climbed spectacularly. Hell, shit, piss, way beyond spectacular.
While, discussing some vintage parts with Steve Massicot at Paughco, he mentioned an old employee who needed funds and had a UL for sale. A complete bobber, although the running aspect was in question. I remembered George Christie’s classic flathead with fatbobs. We rode to the Yuma River run in the early ‘70s.
Then Steve sent me some shots of another Steve’s 1948 UL, which I later discovered is most likely a 74 cubic inch flathead. In 1948 all of the U models were 74s. The UL was the high-compression solo-twin, the U being medium compression and the US the medium compression side-car model. Many came with aluminum heads, and they were available as an add-on. There were only 970 ULs built in 1948, the last year of the big flatheads. As a comparison, over 4,000 EL Panheads were built in 1948 and almost 8,000 FLs. About the same for Knuckleheads the previous year.
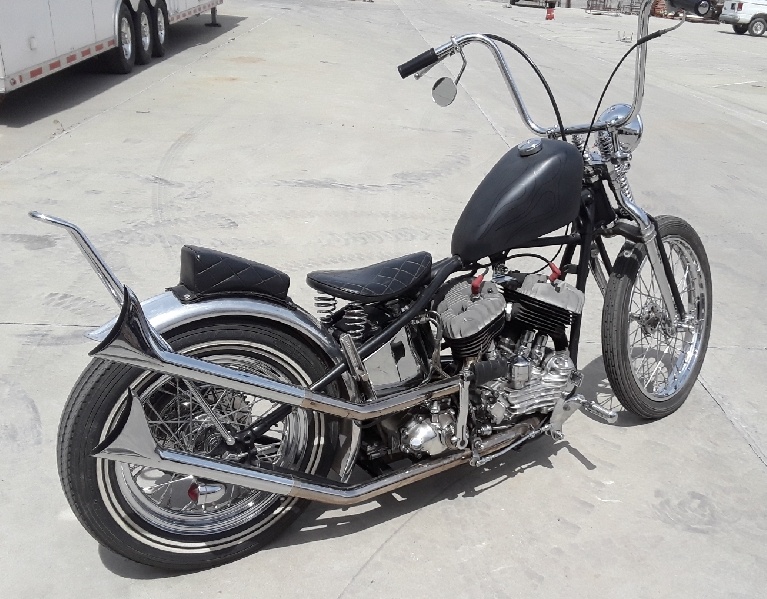
The shots revealed a lot, like no front brake, however the driveline was complete, the bike was a classic from the rebuilt stock springer and custom made extra-wide highbars. I was intrigued by the classic style, and the previous owner, builder, Steve Hannah was 6’4”. It seemed to fit him is a classic David Mann sorta way. I don’t own a flathead, which also intrigued me.
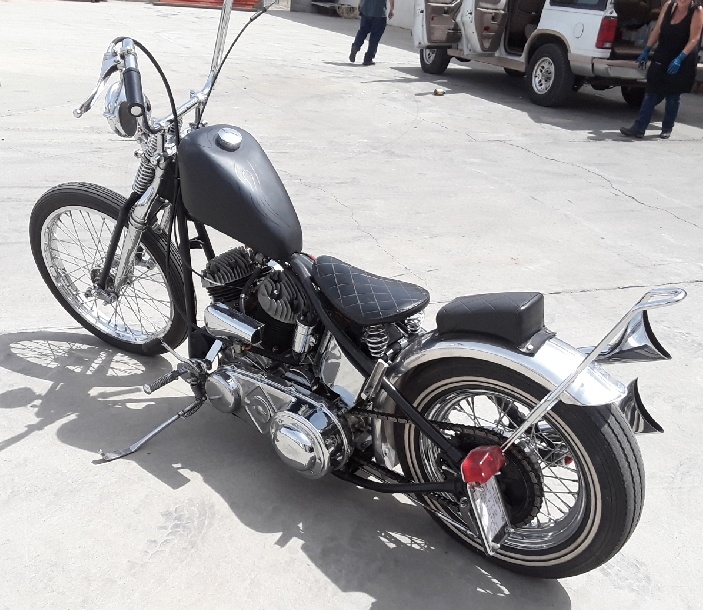
Steve still restores bikes for Ron Paugh’s masterful collection. He cleaned up the stock Knucklehead frame, rebuilt the star-hubs and transmission. According to Steve Massicot, the owner didn’t like the sound of the engine and found the valves out of adjustment. He dialed it in and rode it from Carson City to Virginia City, but was still concerned and never rode it again.
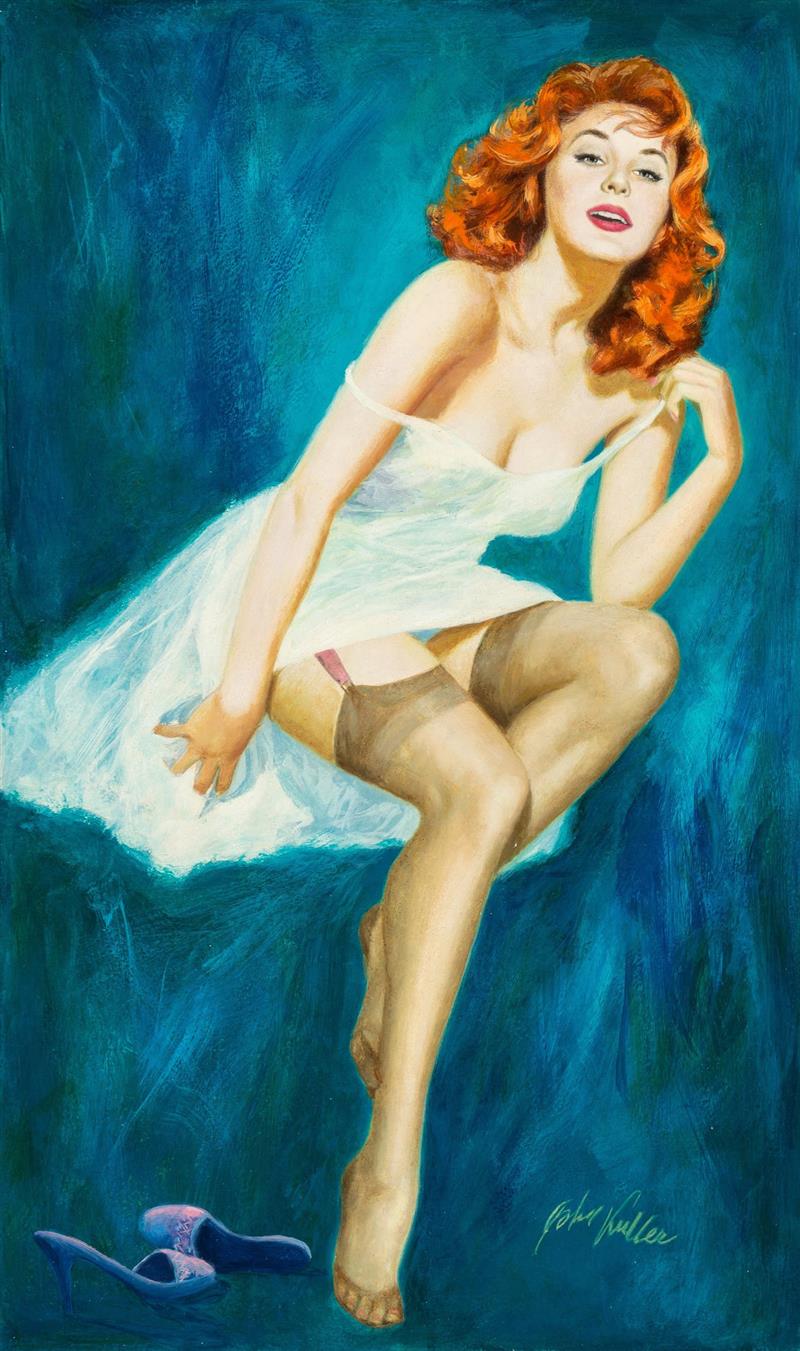
As you know, I’m nuts and believe I can fix anything. Most bikers can, so I cut a deal, but UL Steve wanted cash. I robbed a bank, and the redhead and I watched the weather closely, made rough arrangements, because you never know. There seemed to be a slight opening in the waves of snow and bitter cold making a habit of rolling over Wyoming while heading north. We took a gamble and decided to peel out at 4:00 a.m. to dodge a snowy front heading into South Dakota in January.
The cracked compass said due west for 1200 miles or 18 hours. Leaving early, when it’s 20 degrees may mean it was clear, but the roads were slick and icy. We blazed out of the black hills trying to study iffy road conditions under the lingering darkness and then over the vast and unrelenting Continental Divide three times.
.jpeg)
We have designed a short cut through Wyoming. It cuts from the northeastern corner southwest through Muddy Gap to Interstate 80 in Rawlins where it became a meandering straight shot out of Wyoming into Utah and from there into Nevada where we stopped for the night in Wendover right on the border. That night was a story into itself between sloppy casinos, bad casino restaurant help, one Wendover restaurant, a Mexican take-out joint and a Best Western Motel.
The next morning, we faced a nearly straight shot for 6 hours or 424 miles into Carson City and the Supreme Paughco Headquarters. I’ve known Ron Paugh for over 50 years. He’s one of the supreme backbones of our industry, supportive and inspirational. Last year he was inducted into the Sturgis Motorcycle Hall of Fame. He’s run Paughco through all the good times and the bad and always had the precision vintage parts we needed.
Ron was bending pipes in the shop where he lives now, which is massive, but he took a break and gave us a tour. His line of parts never stops growing.
We arrived right on the dot of 2:00 o’clock in the afternoon the estimated ETA and followed Steve Massicot over to Steve Hannah’s house a couple of miles away.
Hannah is a biker to the bone. He was suspicious, had to have cash and still had the long hair and oily Levi’s he’s been wearing for 40 years. His house was more of a garage as we moved through tarps leading into the back of his home and one room full of motorcycles after another. The UL sat in the center of one dusty room with a partially finished ceiling. It was a jewel in the middle of a myriad of semi-finished projects.
.jpeg)
We rolled it out into the hazy afternoon sun for inspection. UL Steve was sure the left case was cracked and would lead to doom. He was also confident the bike would run with a new battery and some high-test fuel. I liked the classic cut of his jib and could tell the old flathead had been built with care, but the flat black Sportster gas tank needed to be painted. I saw a couple of minor elements I would correct, but I slipped him the briefcase and we loaded the ’48 in the back of the van for the trip home.
Like most of us, the first thing we dive into is a list of improvements. I extended the rear tank mounting tabs on the Sportster tank and brazed the cracks. I worked with Jason Mook of Deadwood Custom Cycles to chase and clean the petcock threads and find a painter.
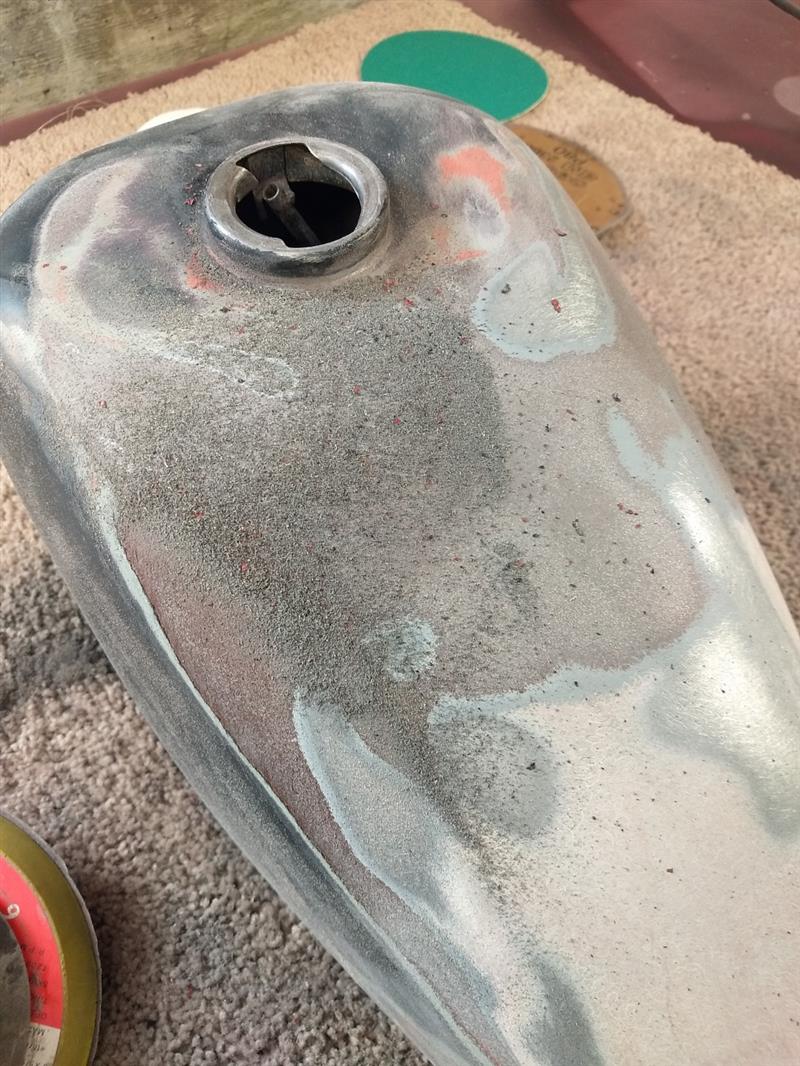
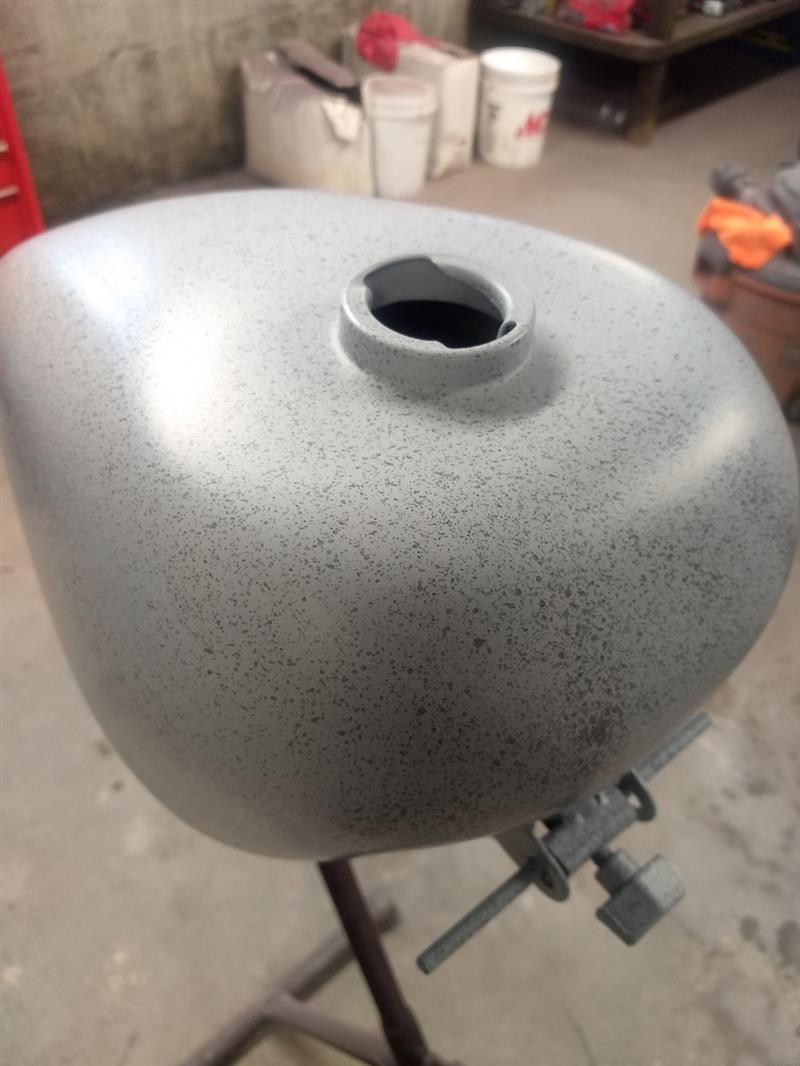
He works with a couple of guys, and one is Greg Robley in Boulder Canyon, not far away. You would think flat colors would be a breeze compared to high gloss, but that’s not the case. Greg is a painter as a hobby. He works construction at the Homestake Mine. “I’ve never been down into the caverns,” Greg said. That’s where the scientists are endeavoring to study neutrinos another break-through element in matter.
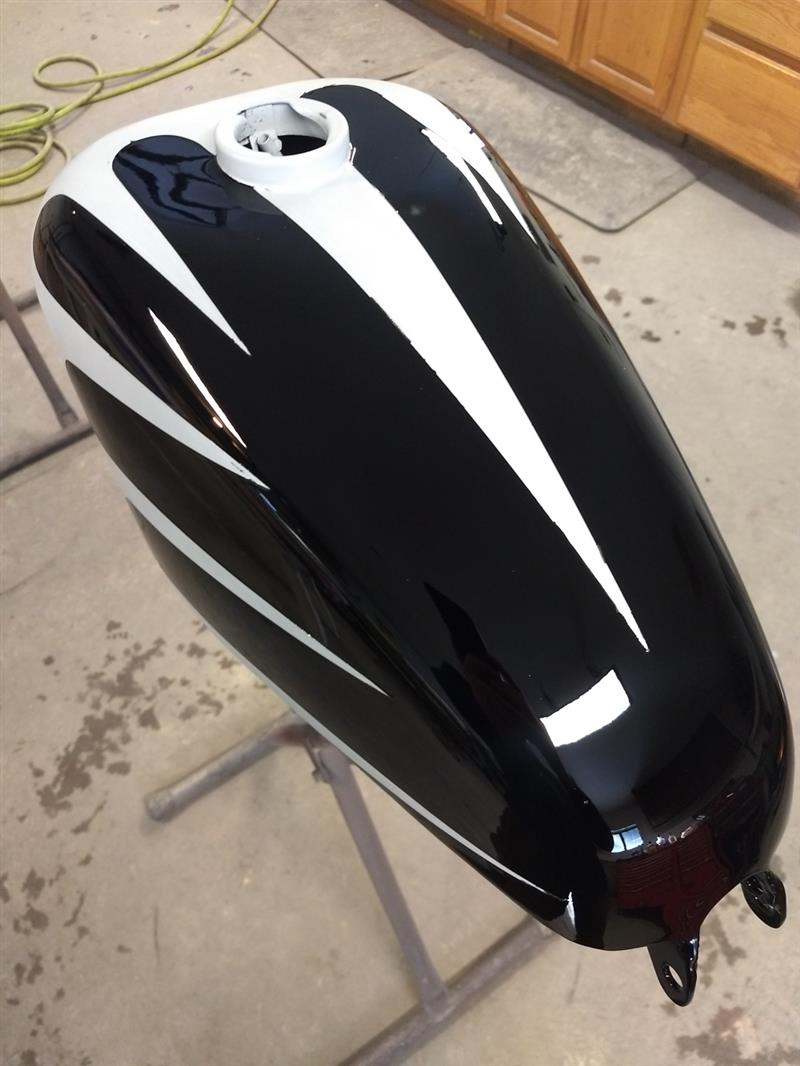
As it turns out Greg wanted me to go with gloss black, because adding the matt and lining it up with the gloss scallops was a delicate chore. He found an imperfection in the first round and was forced to paint it twice.
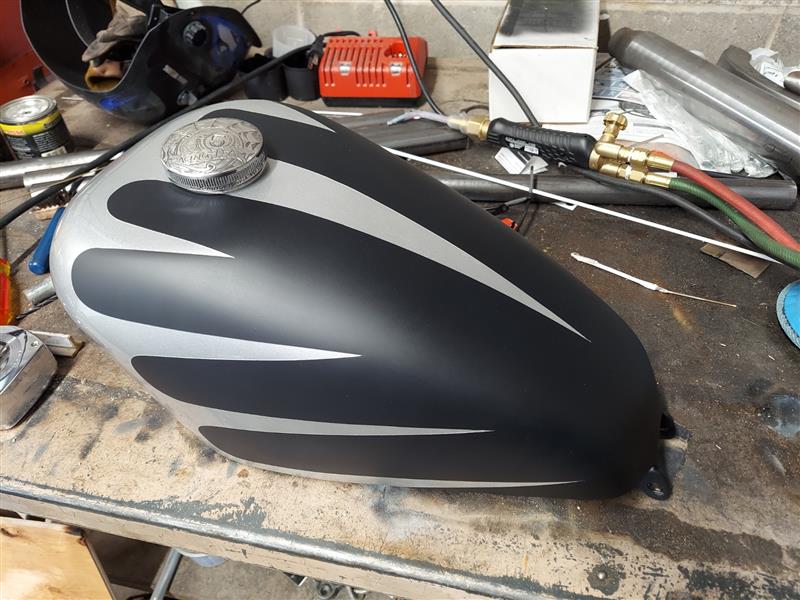
I’ve added a quart of Mobil One motorcycle 20-50 oil and started to kick it. I ordered a Knucklehead manual that includes the big side-valve models up to 1947 because Knucklehead were replaced by the famous Panhead line in 1948.
I started to read about adjusting the valves, which is straight-forward. I read about the timing and oil pump adjustments. Why is it that the manual says see (8) on image 68, but it doesn’t exist?
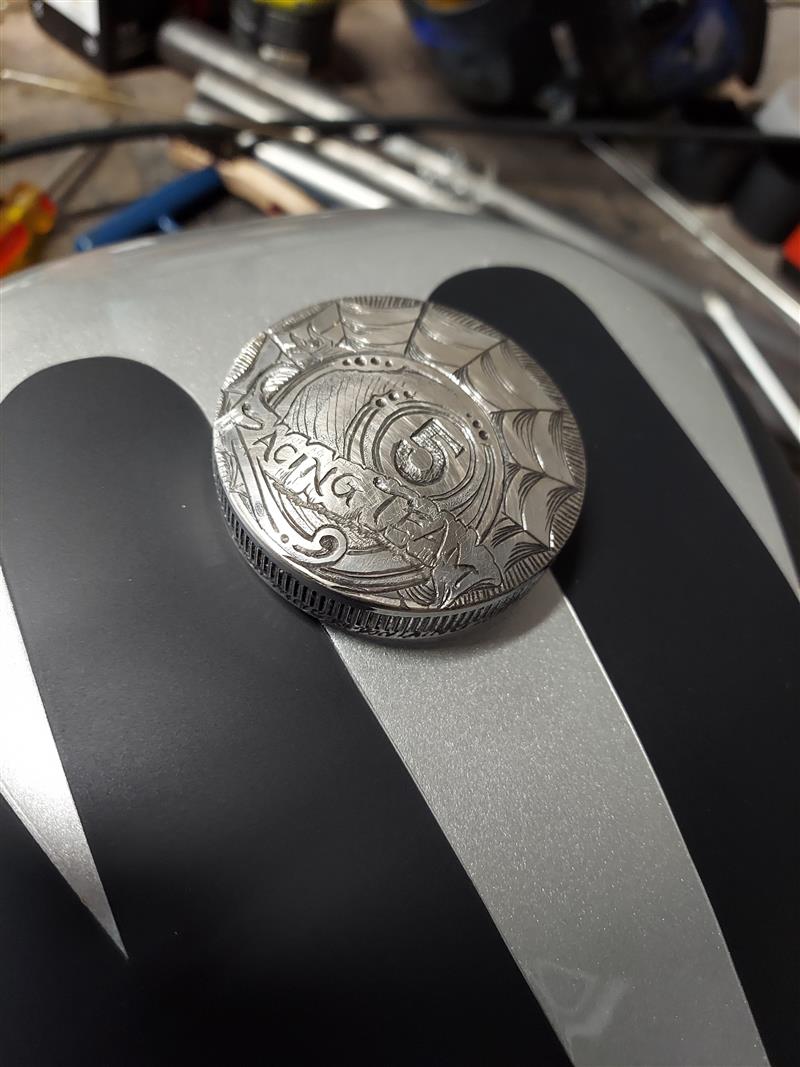
I’ll probably call Lee Clemens, who is sorta retired from Departure Bike Works and pick his brain about tuning the flathead.
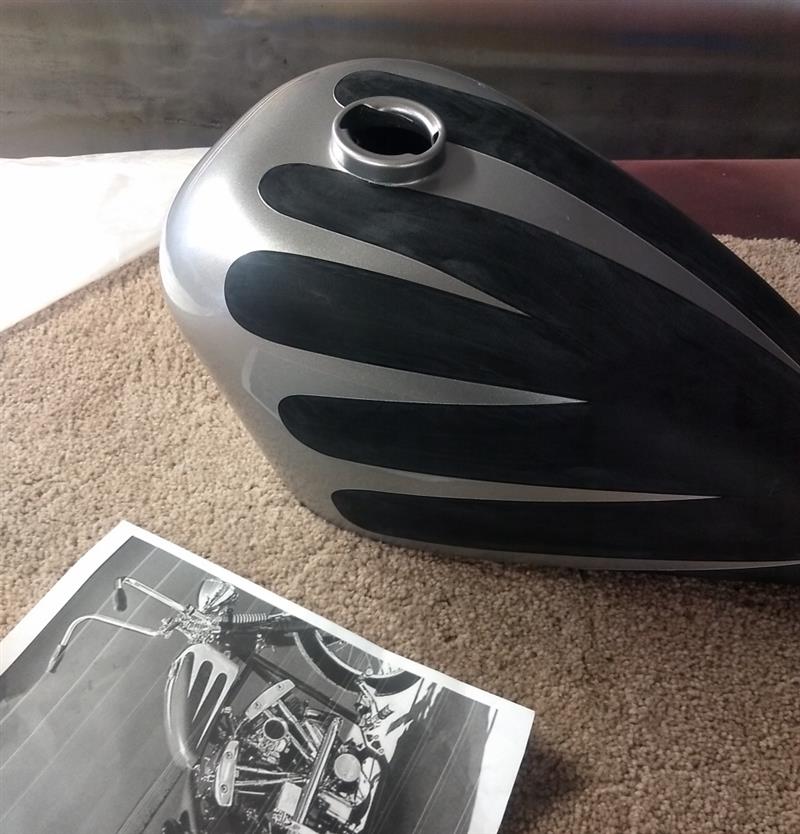
I immediately wanted to replace the classic upsweeps with a two-into-one exhaust system, and I scored some parts from Paughco. I know it would make the bike run better and give it some back pressure. But the more I look at the bike, the more the upsweeps are classic and cool. I’m still grappling with that mod.
.jpeg)
There’s a current issue hanging around my neck like a sailor’s albatross. My shop is not complete in Boulder Canyon. The UL is stuffed in a small garage in Deadwood with access to limited tools and equipment. Hell, I don’t have a milkcrate to hoist the bike onto.
I try to tell myself, “Patience my son…” The shop could be finished in three weeks.
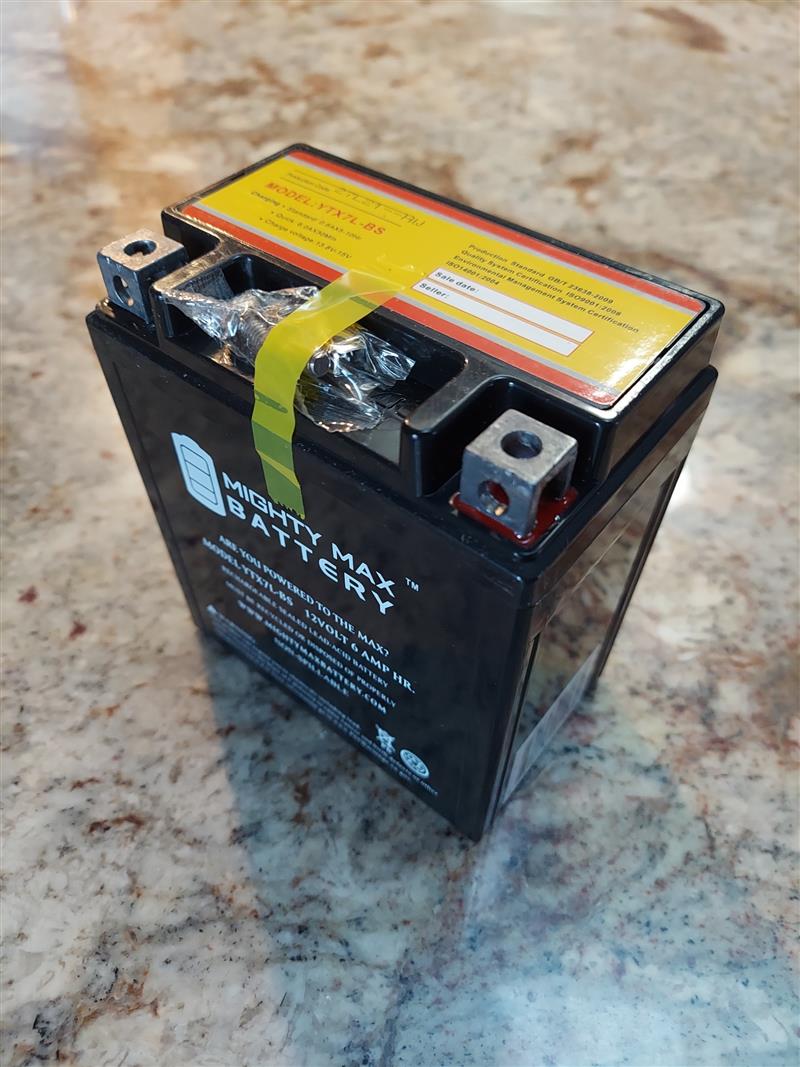
But I don’t ever give up or give in. I continued to fill in the blanks. I went on the search for a battery. Check my battery article with Lowbrow.
https://www.bikernet.com/pages/story_detail.aspx?id=15044
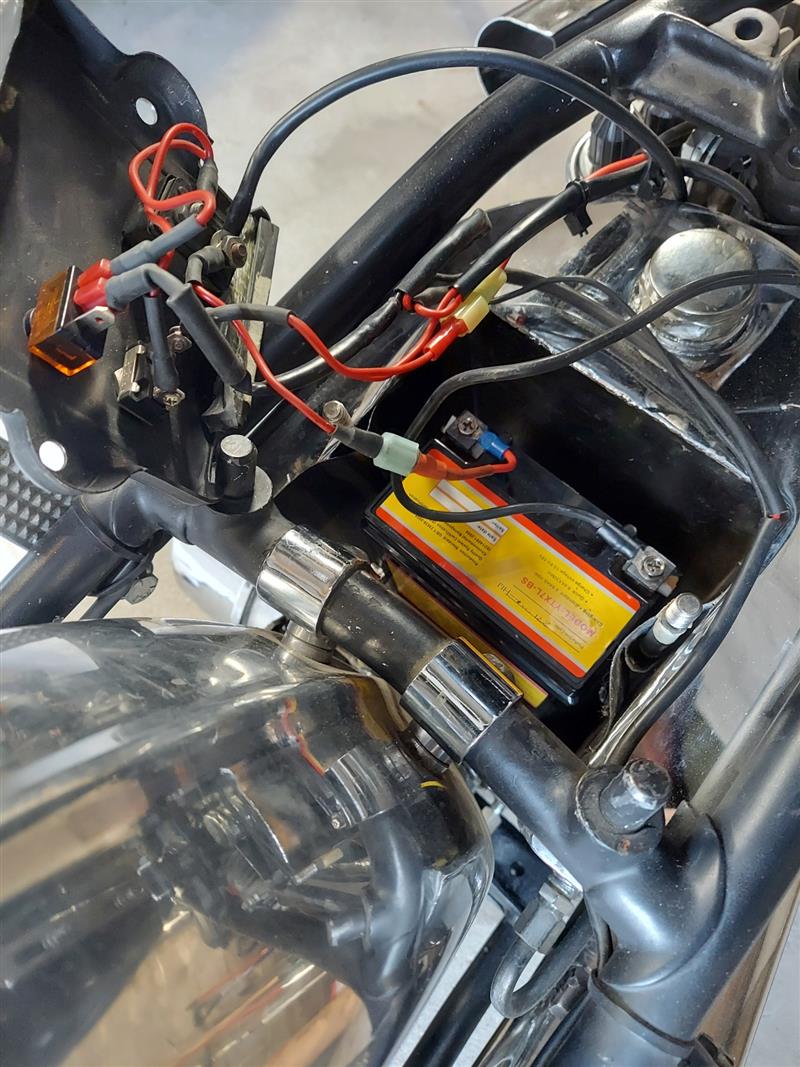
It took a while, but I discovered the Mighty Max 12-volt, 100 cranking amps battery for about $25 bucks. Amazing. Let’s see how it hangs. I took out Steve’s fake case and padded the Mighty Max into place and was able to finish it off. For some odd reason Steve wired the bike so the lights work even if the ignition is off. Not a great notion. Too easy to leave the lights on and drain the battery.
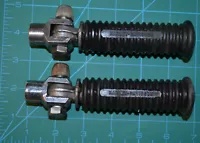
I may correct that, but I also wanted to match the foot pegs with a set of stock rubber pegs. I started asking guys I know about used H-D pegs. For years, with all the custom shit, the first thing guys removed from stock bikes was their stock rubber pegs and replaced them with chrome-billet shit. Then they encountered extreme vibration and looked for cool custom shit with chrome and rubber cushions. Some of the cool custom rubber shit didn’t last.
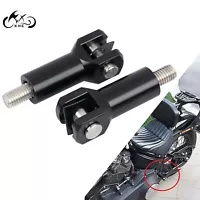
Anyway, the old, tough stock shit piled up in builders’ garages, tossed in the corner. Ebay seemed to be the source for stock shit, and I purchase two sets of pegs and one set of peg extensions. Let’s see what arrives and when.
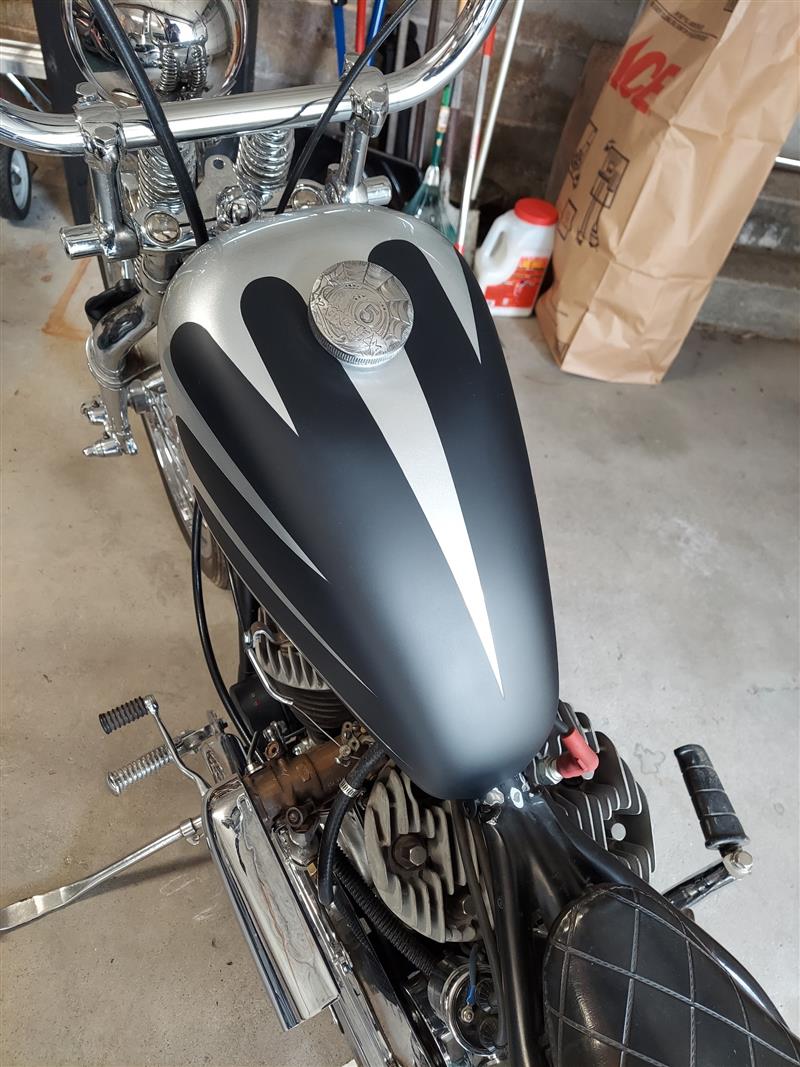
In the next episode, I will bring you a report on the starting procedures and what we found. I might also show you what I have in mind for exhaust mods. Hang on.
–Bandit
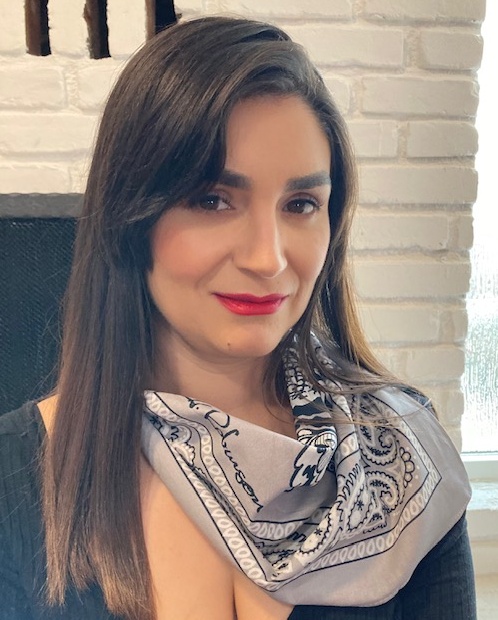
XDA Serves up another Spicy Season-Opener
By Bandit |
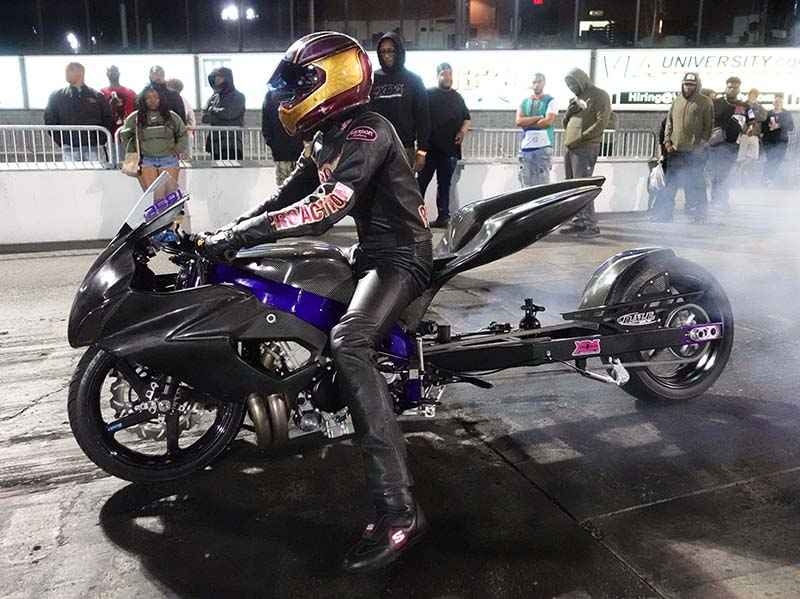
With a beautiful weather forecast and racers eager to resume racing after two years of pandemic hurtles, the pits were jam-packed with racers ready to start the 2022 racing season.
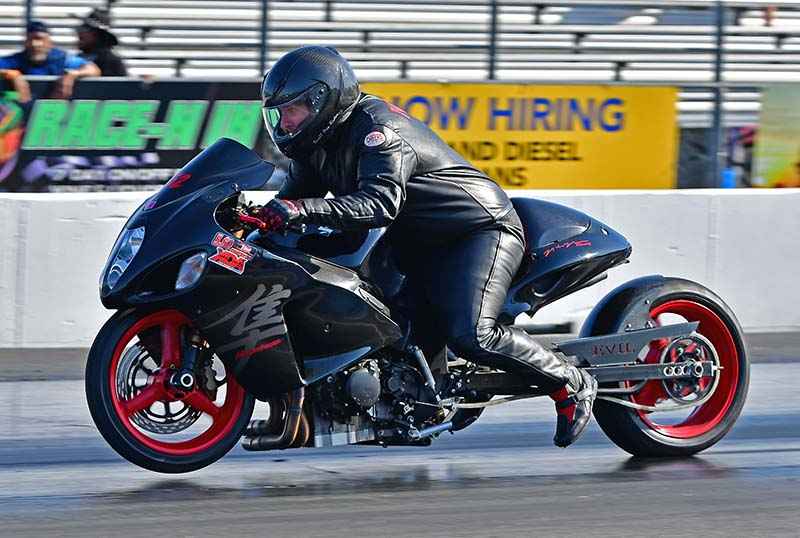
Orient Express Racing Pro Street
The Orient Express Pro Steet racers never disappoint as they always give the crowd a stellar show. Racers started testing on Wednesday at the track as the season opener is always a learning curve. These Pro Street teams continuously make upgrades to push their performance to the next level. And it was apparent as 6 second passes became the norm every round.
Class champion Rodney Williford was the number one qualifier every round. Williford turned the dials as needed every round to keep his turbo Hayabusa on top. His final number for qualifying was an astounding 6.397 made in the third qualifier.
Qualifying was exciting as several racers dropped their personal best ET’s and put big numbers on the boards. By the end of qualifying, fifteen racers were running in the six-second zone. Justin Shakir struggled in the first two qualifying rounds, but then in three, he ran a 6.467.
The first round of eliminations was action-packed as fourteen of the sixteen competitors easily put 6 second times on the boards. Williford took wins against Rudy Sanzoterra, Jordan Haase, and Greg Wallace before facing Ryan Hable in the final. Hable took wins against Ricky Wood, Justin Shakir, and Darion Payne on his road to the final.
In the final round, Hable needed to cut a great light for any chance of a win. Williford, who could efficiently run in the forties with a wrist twist, is a tough competitor to beat. And Hable did his job cutting his best light of the weekend, but it wouldn’t be enough for the Williford Racing powered Hayabusa running a 6.472 at 225.63 to Hable’s 6.962 performance.
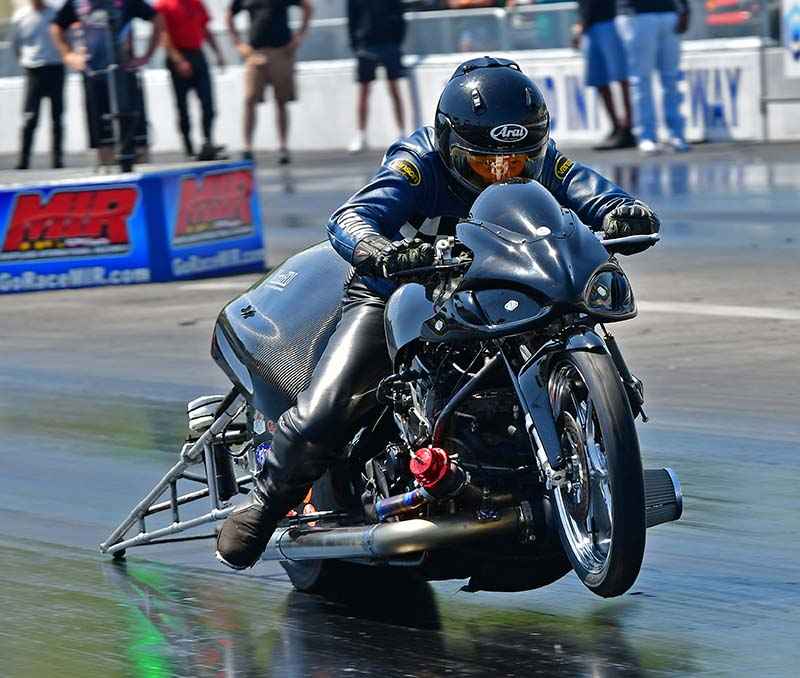
DME Racing Real Street
Class champion David Stewart took the number one qualifying spot in DME Racing Real Street with a 7.569. And Stewart looked to be on track for a season-opening win as he took wins against Courtlan Whiting and Rickey Gadson to land himself in the final against Ben Knight. Knight was not on his ProCharger this season. Instead, he is aboard Ralphie Navarro’s Hayabusa, and he took this all-motor platform to the final after taking wins over David Fondon, Chad Sosnowski, and class champion Mark Hylton.
In the final, Knight did what he does best and cut a light on Stewart to make it an exciting side-by-side run as the pair raced towards the stripe. Stewart ran a faster 7.634 to Knight’s slower 7.677, but that holeshot will get you every time, and Knight’s win light came on for his first Real Street win!
MaxxECU Pro Xtreme
This weekend John Collins qualified #1 with a 3.988 in XDA’s quickest eighth-mile category, MaxxECU Pro Xtreme. Collins would not be able to turn the qualifying position into a win as Chris Cutsinger took him out in the semi-final round. Cutsinger would face Canadian racer Terry Schweigert in the finals.
With these bikes pushing the limit every round, Schweigert’s bike would suffer damage to give Cutsinger a solo pass in the final and his first Pro Xtreme win. Cutsinger gave the crowd a show despite the easy win when he blasted down the track and threw a 3.994 on the scoreboard!
MaxxECU Pro Xtreme is presented by Billy Vose Racing, Fast by Gast, Dunigan Racing, DME Racing, Grothus Dragbikes, Harley Haul, Rob Bush Motorsports, Robinson Industries, Schnitz Racing, Timblin Chassis, and Worldwide Bearings.
HTP Performance Super Stock
HTP Performance Super Stock features stock wheelbase motorcycles with limited modifications. This class is all about the riders and what they can do to squeeze the most power out of these motorcycles with just their clutch hand in control. The challenge with a stock wheelbase motorcycle in drag racing is controlling the torque off the starting line to keep that front tire on the ground for a quick and smooth transition from launch to acceleration.
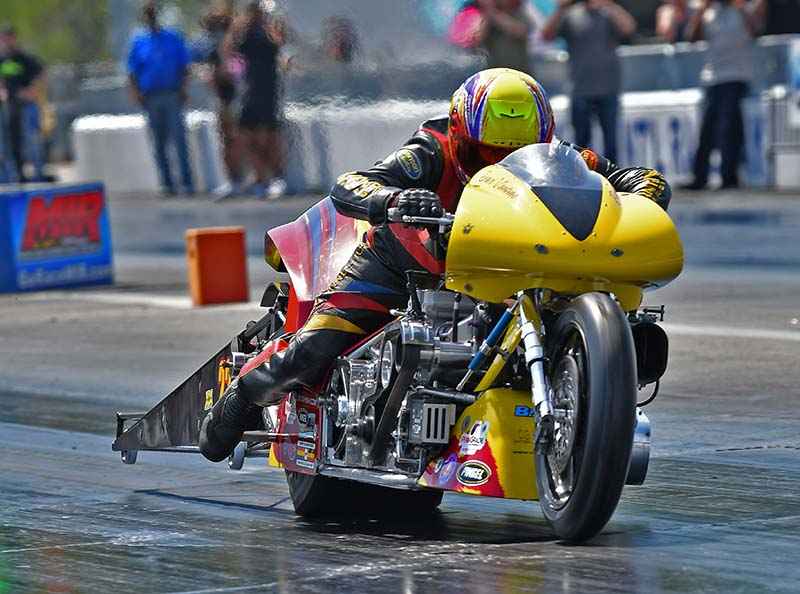
Vance & Hines 4.60
The country’s quickest and most popular 1/8th-mile index class is Vance and Hines 4.60, and thirty-two competitors showed up to fill the field at the Platinum General Services Spring Opener. Durwood Rawlings took the number one qualifying spot with a 4.601, followed by the class champion Ronald Procopio with a 4.602. Procopio would get right back to work, winning four rounds to land himself in the final against Michael Ostrowski, who qualified with a 4.605.
The final round was won at the tree as the champ turned on the red light with a -.003. This red light handed the win to Ostrowski and gave him the 2022 championship chase advantage.
Boosted Bulls
Boosted Bulls is back this season as a championship earning class as XDA is looking to bring the turbo grudge bikes back into the arena and give them a place to show out. The class started with sparks as Frankie Stotz on DME Racing’s ‘Reddi-Wip’ crashed in round one against Malcom Phillips. Stotz was fighting a wheelie and keeping the bike away from the wall when the bike washed out from under him as the front wheel hit the track. He walked away from this crash with bruises and will be back out later this season.
Phillips on ‘Billy Mays’ went on to take on Desmond Spalding on ‘Moonshine’ in the final but someone drank all the shine and Spalding was a no show due to engine carnage and handed the first win to Phillips.
APE Nitrous Bulls
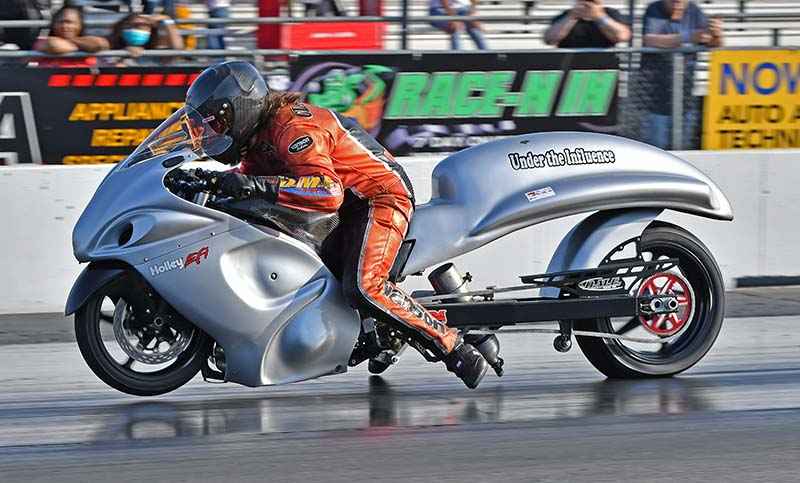
3 Sixty 5 Monster Bulls
In 3 Sixty 5 Monster Bulls the class champion David Page went out in round one to David Martin on ‘Unknown.’ Martin has been in a battle with Page for the last two seasons trying to dethrone him. And this weekend Martin got the jump on him and did not waste that win as he went on to win the next round again Howard Gerken on ‘Son of Sam.’ This win landed him in the final against Spencer Claycomb on ‘Under the Influence.’
Spencer Claycomb has put in a lot of work on the off season and has been racing and testing for the last few months, so he would not be easy prey for Martin. Mullet power would prevail in the final as ‘Under the Influence’ found his way to the win light to start the season with the points lead.
Tommie’s Motorsports DMV Bulls
The Tommie’s Motorsports DMV Bulls class was sold out by Friday night with 16 entries. This affordable grudge class is designed for races who have not competed in the elite Boosted Bulls and Nitrous Bulls classes of XDA.
Class champion Cody Lowe on ‘Codeine’ was ready to defend his thorn this past weekend as he easily turned win lights on against Geoff Godfrey, Carl Lucas, and Derek Sobiech to make it to another final. John Carter on ‘The Gray Matter’ would be the last victim of the night as Lowe made easy work of him in the final to take his place in the winner’s circle once again.
1 Stop Speed 5.60
In the eighth-mile class of 1 Stop Speed 5.60, class champion Dustin Lee took the number one qualifying spot with a 5.601 over forty-three competitors. However, Lee was eliminated in round two of competition despite grabbing the top spot.
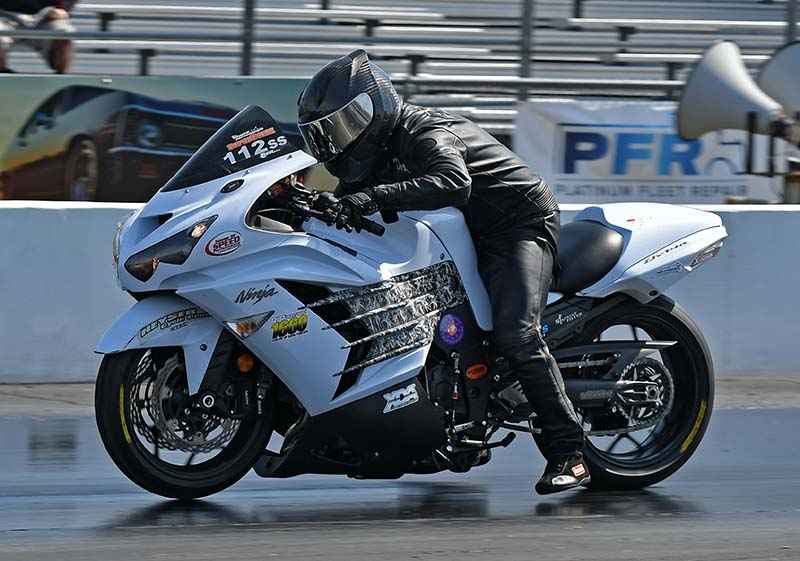
Mickey Thompson Tires Top Sportsman
In Mickey Thompson Performance Top Sportsman, the fastest ET racers on the property competed for one of the thirty-two spots available. Pablo Gonzalez, who won two events last season, took the number one qualifying spot with a 7.462. Unfortunately for Gonzalez, he would not make it past round two.
However, Boo Brown and Hank Lovett had no problems cutting down the competition to win four rounds to face each other in the final. For the second time of the weekend, Brown would be chopped down at the tree with Lovett’s .003 reaction time over his .079 giving Lovett the advantage to get to the stipe first and turn on that coveted win light.
MPS Racing Pro ET
The MPS Racing Pro ET class had a tremendous turnout for Sunday competition, with one hundred and thirty-five racers. The semi-final featured heavy hitter Hank Lovett, Kenny Webster, Dustin Lee, and class champion Mike Schulz. Dustin Lee and Hank Lovett would come out victorious to make it to the eighth-round final.
Hank Lovett, who won Top Sportsman had merged into Pro ET at the fifth round and was looking to double up for the weekend. The final round would be a letdown for Lovett when his bike broke on the starting line, and had to be backed out of the beams. Dustin Lee would break the beams for the win and start the season leading the points.
Brock’s Performance Street ET
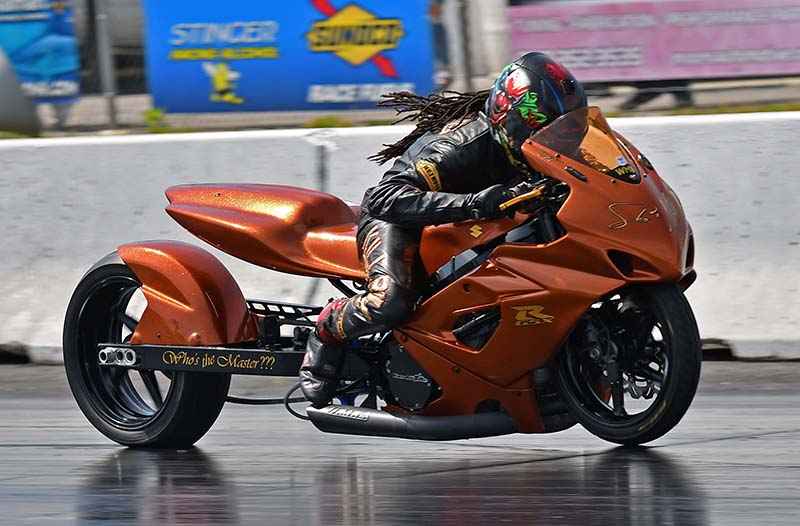
VooDoo Components Bracket Bash
The VooDoo Components Bracket Bash featured on Saturday had a stout 135 entries. But with a season opener riddled with oil downs and on track delays, only four rounds of competition were completed before the decision was made to call it a day and split the purse among the remaining riders.
Hard Times Parts & Service Gambler’s Race
The Friday Hard Times Parts and Service Gamblers Race featured sixty-four sportsman racers looking to get competitive action before event qualifying. With a payout of $4,000 to the winner, this Friday-only race is intense, with racers throwing down double-o lights and running dead on their dials.
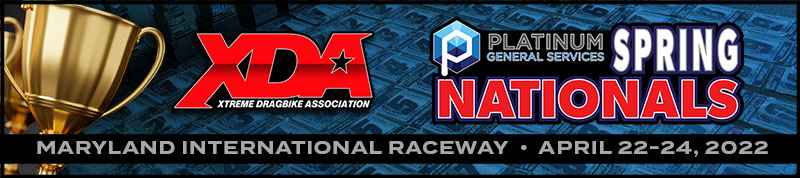
Notable
The Platinum General Services Spring Nationals also featured the Top Fuel Motorcycle of Dave Vantine as his team came out to test his nitro monster. And he did not disappoint, running a 5.935 at 256.26 to set the MPH track record at Maryland International Raceway.
The next stop for the 2022 XDA season will be at Virginia Motorsports Park for the 36th annual MTC Engineering Summer Nationals on May 20-22, 2022. There will be over 700 Professional, Sportsman, and Grudge motorcycle racers in competition, battling it out for over $80,000 in cash purse. Make plans now to watch the best drag racers in the country put on the premier horsepower show the East Coast has to offer.
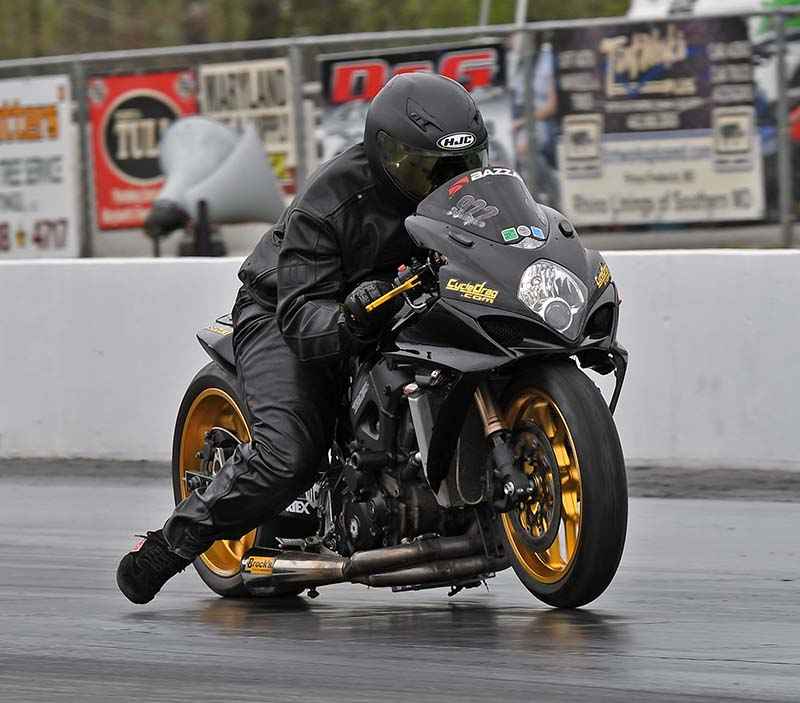
About XDA Racing
LAUGHLIN RIVER RUN–2022
By Bandit |
“The Run that Wasn’t “
It was Thursday mid-morning as I was sitting in my work truck… My phone rang I looked down to see who it was, and it was Hicks. Hicks is one of those friends who normally only calls when he needs help. He’s married and has been going through drama. Knowing this I answered the phone with some apprehension.
He said, “Conway are you down to go to Laughlin with me on a ride, I want to get out of town because my wife is driving me absolutely crazy and it’s the River Run this weekend.”
He mentioned he had a room already and that one of his other Bros had backed out on him. As I sat in my truck, I contemplated back-and-forth the pluses and negatives of going to Laughlin on such short notice. First thing to mind was–fuck it let’s go. I had just moved my girl out two weeks prior, after a decade together and needed a little time to clear my head.
So, I gave my supervisor a heads up. I was taking tomorrow off and to clear up my schedule. Friday morning came in the blink of an eye, with restless sleep throughout the night anticipating the fun I was about to have. The alarm went off at 7 AM. As I woke up to take my morning piss, I received a text from Hicks telling me his front tire wasn’t holding air, so we needed to wait till 10 AM for MC Tire Works to open up, so he could install a new front tire.
Since we couldn’t check in to the Tropicana until 4 p.m., this really wasn’t a setback. Now, it’s 10:45 AM and we’re at Hicks‘s parents’ house doing a once over on our Dynas to make sure they were roadworthy, and then to the gas station to top off our tanks. Getting a late start landed us smack into heavy LA traffic. Snaking the Dynas through this LA traffic was a lesson in stark concentration. We were able to squeeze through the endless number of cars, each one a threat for 40 miles.
We hit Barstow which was the halfway point to fuel up and stretch. As we pushed the Dynas through the Mojave Desert at their sweet-spot 90 mph, I started to go into that highway trance, thinking about life, what the future held for me and with my Asian female shadow mirrored my every move. I knew I would find some relief, when I hit Laughlin.
Did I mention the Saddlemen, San Diego Customs edition seat I just recently bought kept me locked in and comfortable for the 5-hour journey. We checked in and immediately got into our board shorts to hit the Jacuzzi to soak away the 5-hour mostly desert trip.
Back up to the room for a quick shower then down to the lobby to grab a bite to eat at the local diner named Carnegie’s. The cover band in the bar was playing a shitty version of Guns N’ Roses “Welcome to the Jungle” as we ventured over to check the action.
I ordered my usual Tito‘s and cranberry. Then we ventured down to the casino floor where we hit the roulette table for a little fun. The vibe of the casino was great, and everyone was having a good time, we played roulette for a few hours then back up to the room to catch some Z’s.
As 8 AM approached, we were up, dressed and out to the bikes to go for a putt around the city. We grabbed a bite at some diner that I don’t recall because hangover wouldn’t let me remember. And as I looked around, I didn’t see any vendors, live music or motorcycle related shit. Oops!
I thought to myself somethings missing here. We gassed-up and followed a group of bikers out to a western town called Oatman. Oatman is an old mining town from the 1900s that’s been a tourist destination ever since.
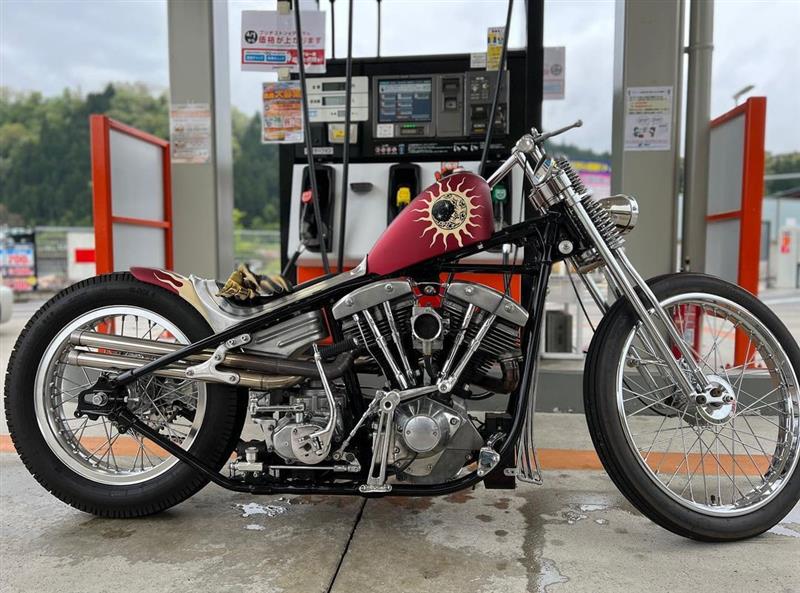
The main attraction is the Burros, seems people like feeding these asses. Packed with bikers it reminded me of the old Wild West of outlaws taking over a small town, bikes everywhere.
With the desert heat we had to refresh ourselves with some ice-cold beer, then something sweet with some ice cream. Hicks and I decided to go back to the hotel room to lounge around the pool.
Feeling life stresses loosen up I realized this was a well needed trip to clear my head. Back up to the room where we cleaned up and then downstairs for some dinner. The same band was playing a Zeppelin tune as I walked up to the bar. I ordered my usual drink, when the bartender told me about the woman at the end of the bar who covered my cocktail.
I looked across the bar and saw a beautiful lady sitting alone smiling at me, a “Cougar” one might say. I smiled back and walked over to show my appreciation. I introduced myself and she told me her name was “Sharon Peters” and she wanted to take Hicks and myself up to our room… we excepted her request and I’ll let your imagination figure out the rest.
The alarm went off at 8 AM sharp, we wiped the sleep out of our eyes wondering what the hell happened the night before… Not saying much, we got our shit together to begin our journey home.
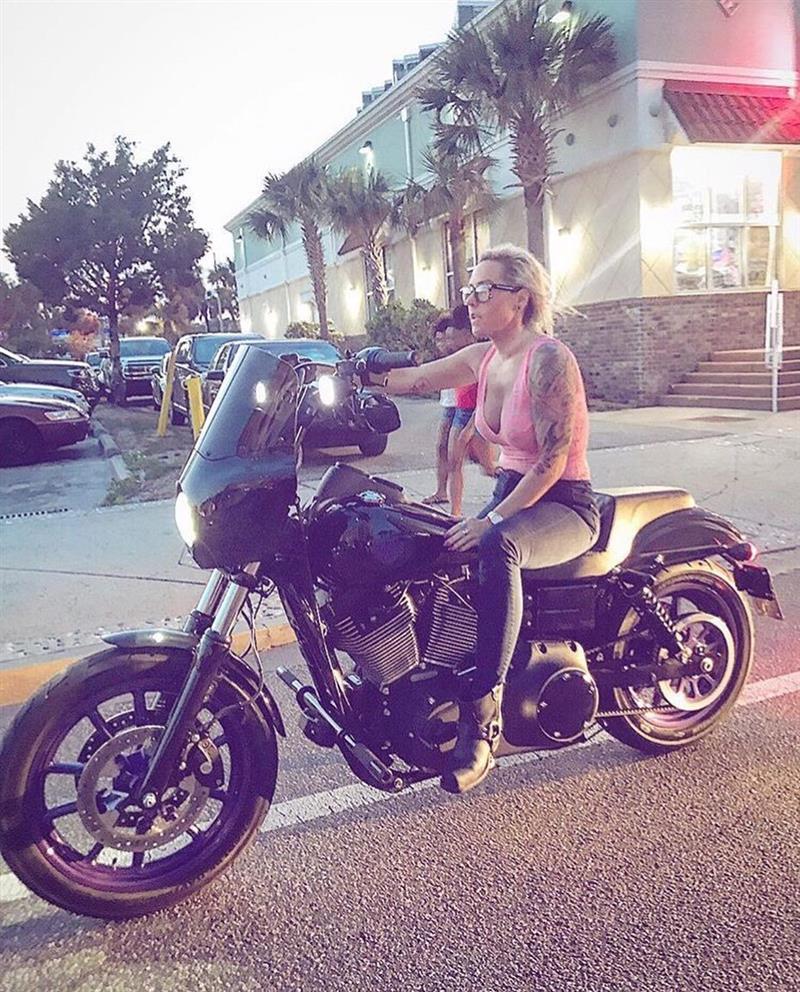
We checked out of the hotel, hit the gas station, and turned on to Route 66. As I mentioned the Dyna’s smash through the desert at a cool 90 mph not skipping a beat. Our shadows followed us to confirm we were going in the right direction home.
We hit Barstow again to top off our fuel and stumbled into the famous McDonalds Barstow Station. I’ve been coming here for many years, and it brought back many childhood memories with my family. Plus, Hicks had never been there before. I introduced him…
As we jump back onto the highway, I felt the reality I left in LA starting to creep back into my mind. Hicks and I rolled back into town and at the fork in the road where he went his way and I hit mine, we gave ourselves the usual middle finger goodbye as we went on our separate ways.
Then I realized…It wasn’t about the event we missed, it was all about the ride with a good brother and the mystic desert vibes.
Motorcycle Awareness Month by ABATE
By Bandit |
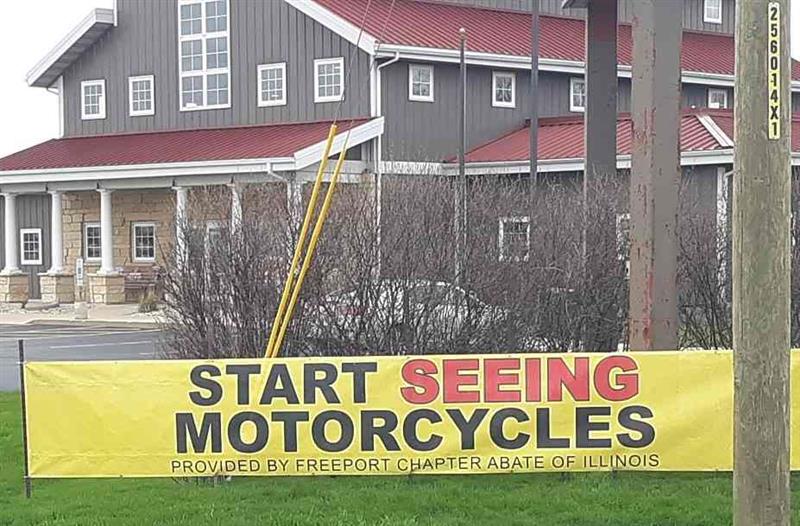
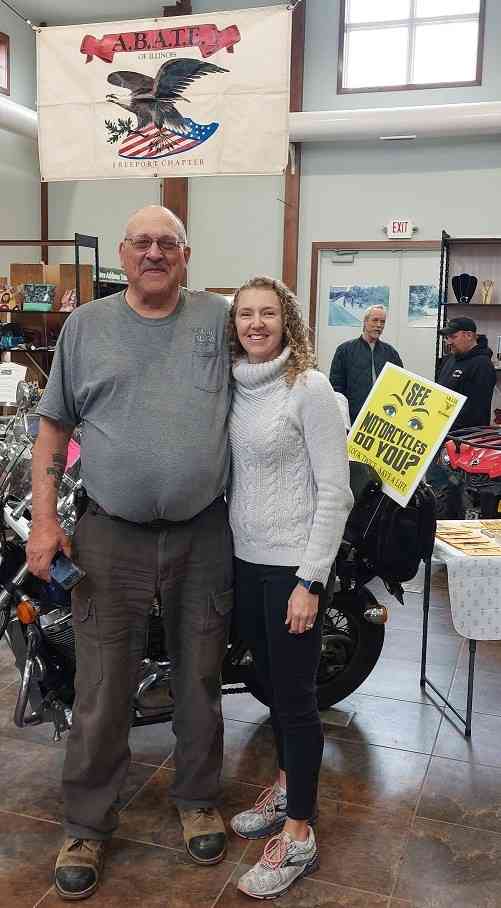
Over the years we have gone from a table of information and one bike maybe, to the full floor, and back again. Using dealership bikes, when we can and then COVID-19 hit town, and 2020 had nothing on display and the Visitor Center was locked down tight. 2021 a last minute phone call and one week later the display was up again with two members’ bikes. (4) This year with a better game plan, we came up with 8 bikes, from as many members.
One Hell of a team within the Freeport Chapter of A.B.A.T.E. of Illinois!!
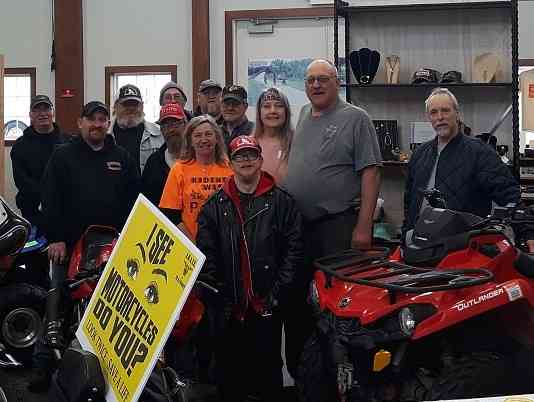
https://greaterfreeport.com/visit/visitorcenter/
Stephenson County Visitor Center, 4596 US Highway 20 E, Freeport, IL 61032
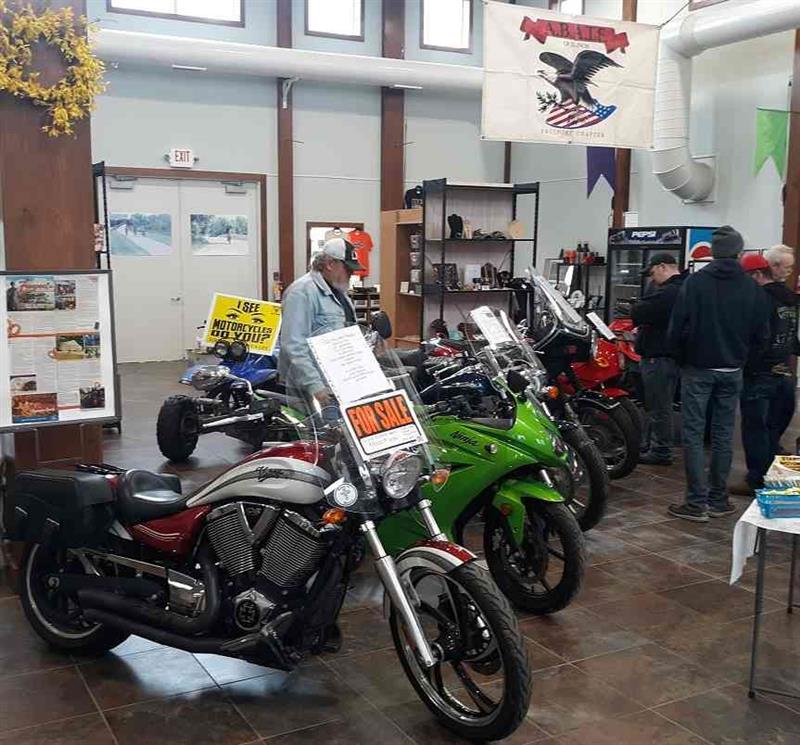
May is Motorcycle Awareness Month. We have been able to set up a display from today May 2nd, until June 1st, 2022. The Freeport Chapter of A.B.A.T.E. of Illinois did a bang-up job helping out with this display.
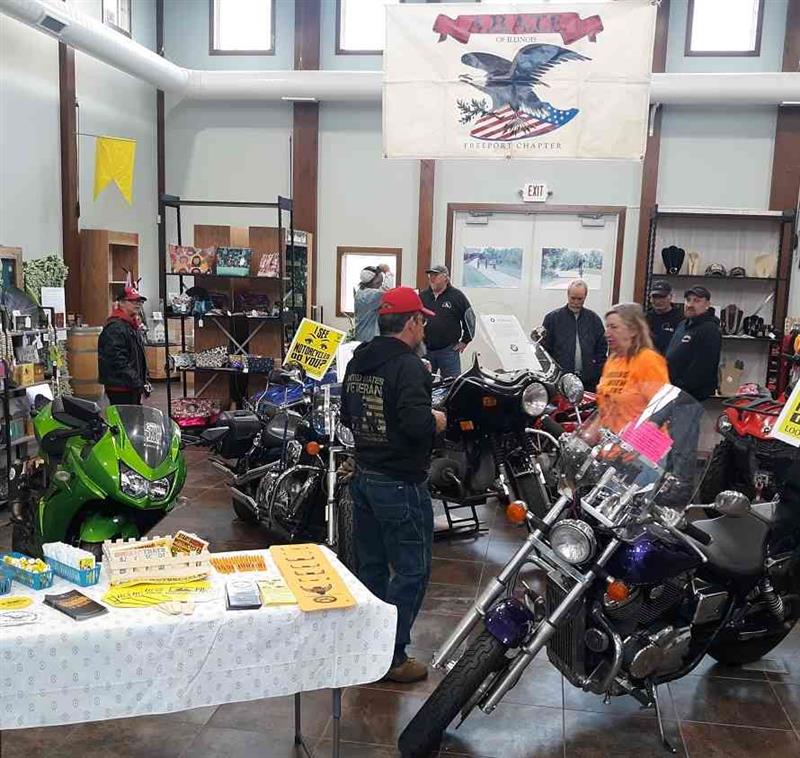
We had bikes donated by chapter members:
Arnie Binning: Victory, Katie Schneiderman: Honda, Pat O’Brien: BMW, Chirs Zimmerman: Kawasaki, Doug Fleming: Ducati, Neal Toepfer: Honda, Raymond Munchie: Yamaha ATV, & Dan Bragg CanAm Outlander Max ATV.
We at A.B.A.T.E. of Illinois & and the MRF fight for all motorcyclist rights. Join today www.abate-il.org & www.mrf.org
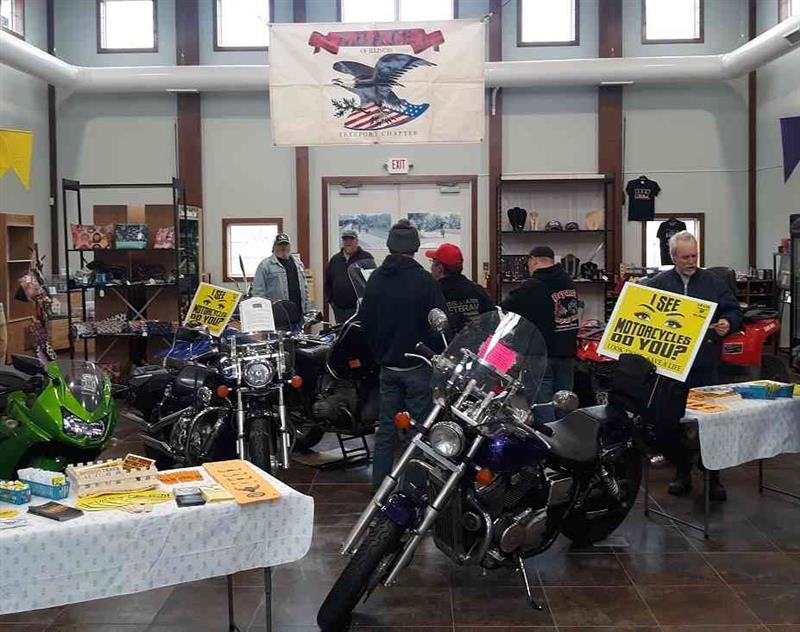
The Mysterious 1913 Jefferson/Waverly
By Bandit |
The Jefferson motorcycle was only made for one year–1913!
–St. Francis Motorcycle Museum
This is a strange one. I was also told that only one twin OHV Jefferson exists. As the years pass the stories fade and alter. This particular machine has been a treasured piece on display in the secret Don Whalen/Richard Bunch Collection. I can’t tell you where or I would be in sever trouble. Don is the founder of the Sierra Madre Motorcycle Company.
Somewhere in this article we will discuss where the second 1913 Jefferson twin is. “As soon as someone says there’s only one,” Don said, “three more show up.”
In December 1910, the press announced a new and innovative OHV single engine manufacturer. The Waverly was manufactured in Milwaukee and was the brainchild of Perry E. Mack, who débuted his new vertical-overhead-valve engine in 1910; one of the earliest motorcycles to have valves ‘upstairs’.
The company only sold engines initially to the Kenzler Company of Cambridge, Wisconsin, under the Kenzler-Waverly name. The single, and then the twin gained a reputation as an excellent racing puppy, due to the better breathing afforded by overhead valves.
In 1911 the Kenzler team fitted the Waverly single into an Indian Racing chassis and with Ralph Sporleder behind the bars won several events including several open races competing with twins.
In 1911 the company re-organized and moved to Jefferson, Wisconsin. During a board of directors’ meeting the decision was made to change the Waverly engine name to P.E.M. after the founder and designer, who was accomplished in the motorcycle and the automotive industry.
The engines continued to be produced by the Waverly Manufacturing Company until 1913 when they named the motorcycle after the Wisconsin town of Jefferson.
Side Note: Dudley Perkins started his dealership with Al Maggini and sold Deluxe and Jefferson motorcycles in 1913 in San Francisco. Perkins, a racer supported the shop marketing with his racing victories. His successful Jefferson twin was called “little Jeff.”
An interesting feature of the twin roadsters was the use of short-link suspension both front and rear. In each case suspension was controlled by short bell cranks connected to leaf springs, providing 1.5-inch travel to absorb bumps; another innovation from the Waverly Company.
Company names changed during the rough war years and economic times of the area. When the company moved to Jefferson, they ultimately opened Universal Machine Company in Milwaukee. The Mack (P.E.M) motors were manufactured in the twin configuration (7 and 9 Hp) and as OHV singles at 4 and 5 horsepower. The engines were available outside the Jefferson name to other motorcycle builders and cyclecar manufacturers.
WWI rocked the world from 1914 to 1918 and impacted the materials needed to manufacture motorcycles and engines. The Jefferson brand was reliable, well made and fast, but couldn’t survive as a company. During 1914 the company closed. Maybe the crew went to war.
Unfortunately, innovation and race wins simply weren’t enough to keep small manufacturers alive in those brutal early days of the American motorcycle industry.
This magnificent Jefferson twin was sold to Mike Bahnmaier, of racing fame, Mid-Continent Racing and was once the youngest rider to open a Harley dealership in Salina, Kansas in 1978 at 25. His father had to co-sign for his first shipment of motorcycles, although he was severely nudged by mom. Mike’s been a collector ever since.
Mike loaned this bike, the black cyclone, to the Marquette, Kansas Museum devoted to famous racer Stan Engdahl, who ran a TV and radio repair shop in the town of 600. He also built a dyno, tuned and balanced neighborhood bikes out back, including race engines for Mike. Engdahl took home over 600 racing trophies and was National Scrambles Champ 5 times and Kansas state champion 16 times. During the last race of a season he had a broken leg, but he cut the cast off and raced and won the championship.
When Stan retired, he donated his building to the city for what is now the Kansas Motorcycle Museum. The building needed work, but as you can see it’s a classic and now houses over 100 race and antique bikes. Mike loaned his ’13 Jefferson, a ’28 Cleveland four, a ’39 Indian four, a ’38 Chief and a ’28 single hillclimber. That’s not all, but we’ll end the list there.
Mike also owns another semi-restored Jefferson twin, so there are two of them in Kansas. It’s housed in St. Francis, Kansas, 300 miles from Wichita, but just 180 miles from Denver. Mike’s son, Brett Poling, lives in St. Francis and is very involved in the museum. The town said they would build a motorcycle museum, and a local banker handed over a check for $200,000, after a resident donated the land. “The driveline of this Jefferson is original, but the chassis and tins have been refreshed and painted,” Mike said.
Ultimately the St. Francis museum became a state-of-the-art 11,000 square-foot motorcycle museum with a twist. “We suggested a tornado-proof basement,” Mike said, “to house the very rare motorcycles.” They live in tornado country. It was determined that the basement would be cost-prohibitive, but they found an alternative. They built a steel incased and reinforced vault in the center of the museum to house the rarest antique bikes from Mike’s collection including an early Pope, an Orient single and of course the Jefferson twin.
Every few years Mike rotates bikes from St. Francis to Marquette almost 300 miles away. He sold his H-D dealerships and has recently helped a young man, David Hope, start a small dealership in Dodge City, with a population of 30,000.
There’s another missing link to this story. Neither of these bikes have swingarm suspension in the rear as claimed. Indian did create a 1914 model with a swingarm, but I would bet the additional costs during WWI was prohibitive. Mike mentioned that the one-year rumor may have come from a name change. “Maybe they called them Waverlys in 1914 dropping the Jefferson name. We need to find a 1914 OHV Waverly with swingarm suspension on the rear… Wait, how about a 1913 single?
Hang on for the next antique motorcycle story. If the motorcycle doesn’t tell a wild tale of survival, the collector, the restoration master, or the rider has another twisted tale.
Music, Meaning & Motorcycling
By Bandit |
Sound has more impact on life than we know or credit it for. Sound is not just significant to humans but many lifeforms. When we hear a loving voice, our mental mood & thoughts are different compared to a roaring voice of a harsh boss at office. The first voice of a newborn baby has deep mental impact on a mother, while hearing an authoritative voice of a policeman when you are repeatedly getting pulled over at checkpoints for riding on a ‘cool’ chopper may bring a different response.
Long-time pet owners will vouch that their dogs or cats hear and respond to their voice, maybe even specific words. I had a cat who recognised his name when called. He also knew and loved the word ‘chicken’ among other words. Cats and dogs also have a strong sense of hearing, while most people only ‘hear’ (punny) about their sense of smell (or the smell of what the cat left behind in your shoe).
The music company HMV stands for the words ‘His Master’s Voice’. The HMV official logo illustrates a painting titled ‘His Master’s Voice’ by Francis Barraud of ‘Nipper’ listening to a Phonograph cylinder, which was bought by the Gramophone Company in 1899. It shows a dog looking at the gramophone, supposedly playing the recorded voice of his master, hoping his master will appear soon.
A famous experiment conducted by Jagadish Chandra Bose at the Royal Society of London in 1901 demonstrated that just like humans, plants too have feelings. He was also the first to study the action of microwaves in plant tissues and corresponding changes in the cell membrane potential (Bose was a physicist, botanist and a pioneer in radio science).
Humans with their fast improving lifestyle and diverse cultures have developed sound into great folksongs, retelling histories and unexplained mysteries. People further developed them by writing songs and using musical instruments. With standardizing of common musical instruments, music composition and changes to ‘what is considered a singing-voice’, we now have a whole range of music genres to choose from – for entertainment, for ‘edu-taiment’ of kids, for relaxing, for hitting the gym, for romantic night dinners, for wild parties and more.
(Note: Regarding singing voice, it is true that: when he was 14, young Elvis was given a C- grade for music, “below average”, with his teacher specifically commenting that he “had no aptitude for singing.” Later his audition to a local quartet failed, again because of his perceived lack of talent. After a performance at Nashville’s Grand Ole Opry (Oct. 2, 1954), Elvis was allegedly told by an Opry manager that he was better off with his day job as a truck driver because he would never make it as a singer. Two weeks later he appeared on Louisiana Hayride & signed on for 52 Saturday night appearances on the radio show, thus launching his legendary career.)
Do songs or prayers motivate you? Does instrumental music for meditating or repeating a particular word/phrase/name help inspire you and give you desired results? Did a recording of historic words after first footsteps of man on the moon make you want to learn more about science or mechanics of how rockets or engines work?
Below are references to these misconceptions about songs written by legendary singer-songwriter John Fogerty of Creedence Clearwater Revival (listed at no. 40 on Rolling Stone magazine’s list of 100 Greatest Songwriters).
1. ‘Lookin’ Out My Back Door’ is not about drugs at all.
This song appeared in the album: Cosmo’s Factory.
The intriguing name of the album had trippy lyrics such as –
“Won’t you take a ride on the flyin’ spoon? Dood-n-doo-doo
Wonderous apparition provided by magician
Doo, doo, doo, lookin’ out my back door”
The song came up again in the trippy iconic movie ‘The Big Lebowski’ (1998) where ‘The Dude’ is looking through his rearview mirror as the song is playing. A movie by incredibly talented writer-director duo Coen Brothers.
All this will make any parent grab and destroy that CD (unless they are really hardcore Rock fans and look up stuff).
Well, the song is what John wrote when he came home to his 3-year old son.
With reference to: www.AmericanSongWriter.com
In interviews and in ‘Bad Moon Rising: The Unauthorized History of Creedence Clearwater’, John Fogerty is quoted as saying the song was actually written for his then three-year-old son, Josh. He has also said, the reference to the parade passing by the door was inspired by the Dr. Seuss story, ‘And to Think That I Saw It on Mulberry Street’.
2. Another hit song from this wonderful album was ‘Run Through The Jungle’
No Sir, it is not about Vietnam War.
With reference to: AXS TV interview and quoted in www.rollingstone.com
In a TV interview that was also mentioned in Rolling Stone magazine in Jan-2016, the master-songwriter said:
“I’ve seen it written that ‘Run Through the Jungle’ is about Vietnam, but that’s not true. I was speaking about the landscape in America. I had been thinking about the idea ever since 1966, when Charles Whitman had gone on a rampage, killing sixteen and wounding thirty-two others, shooting from the observation tower at the University of Texas. The song is really about gun control.”
That said, there is his unique take about such a control:
“Now, I’m a hunter. And I’m intrigued, even fascinated, by weaponry through the ages. But you don’t take a machine gun to go deer hunting,” he said. “There’s got to be some sort of lid on this thing.”
(since 9/11 & Snowden and diminished rights of citizens) “I think it is important that our citizenry is armed. I believe this acts as a deterrent – whoa! Deterrent? Against what? Let’s just say that the fact that there are millions of armed people ready to defend their homes probably acts as a huge roadblock against those who would try to seize the country for their own ends.”
Fogerty also wrote about this song in his 2015 autobiography, ‘Fortunate Son: My Life, My Music’, echoing much of the same, saying he was a hunter that favored gun control.
3. Well, does that overload your heart & mind and wanna listen to the trippy song about Seuss’s characters with some whisky & women?
Well, here is another gem from this very album that promises a better stress-buster and true freedom. Freedom to ride, enjoy, explore, party, make friends, see the unseen beauty all around.
The name of the song is ‘Up Around the Bend’. Yes! It is about riding your motorcycle with the wind blowing, a smile for company.
With reference to: www.unmask.us
John Fogerty explains, “This was inspired by riding my motorcycle. I just remember riding along, and the title phrase came to me. Just the feeling of going. Movement.”
Well, movement is definitely important. Apart from physical, metal exercises, make sure to exercise your motorcycle engine, gears, throttle & roll those wheels. While a laid-back man may joke about moving parts causing more wear and tear, a biker knows by experience that a human body & mind regenerates only through exercise, not by stagnation – especially not of ‘spirit’.
And of course, the biker takes enough care to service & repair his/her motorcycle. Bikers personify their bikes, treat them like a person, with dignity & respect! They give their bikes a name. Some may advice you that, abuse of your machine will throwback bad surprises on some faraway highway. It may also be a metaphor for your life & health!
Life has it’s ups and downs, just like riding a big V-Twin on winding mountain roads or dirt tracks in small detours. You also get to ride smooth and fast on many highways and outside big cities.
Depending on all the mental / physical luggage, you may or may not reach your full-engine-capacity / efficiency. One man’s life though is not as similar as their friend or neighbour’s motorcycle of the same make & model.
So, there would be some rocking and some rolling & tumbling – depending on the path you choose to ride on. But you gotta gotta ‘Ride On’ !
So, cheer up and listen to this one below:
* * * * * * * * *
Song: “Up Around the Bend”
written by John Fogerty
from Album: “Cosmo’s Factory by Creedence Clearwater Revival
There’s a place up ahead and I’m going
Just as fast as my feet can fly
Come away, come away, if you’re going
Leave the sinking ship behind
Come on the rising wind
We’re going up around the bend
Ooh
Bring a song and a smile for the banjo
Better get while the getting’s good
Hitch a ride to the end of the highway
Where the neons turn to wood
Come on the rising wind
We’re going up around the bend
Ooh
You can ponder perpetual motion
Fix your mind on a crystal day
Always time for a good conversation
There’s an ear for what you say
Come on the rising wind
We’re going up around the bend
Yeah
Ooh
Catch a ride to the end of the highway
And we’ll meet by the big red tree
There’s a place up ahead and I’m going
Come along, come along with me
Come on the rising wind
We’re going up around the bend
Yeah
Do-do-doo-do
Do-do-doo-do
Do-doo-do
Do-do-doo-do
Yeah
Do-do-doo-do
Do-do-doo-do
* * * * * * * * *
References: Very brief excerpts of lyrics or interviews are taken solely as examples for further explanation. Their copyrights remain with their author & copyright owners.
Royalty-free images courtesy www.unsplash.com and its contributors
unsplash.com Images Acknowledgement List:
“silhouette starry sky” by Greg Rakozy
“kid singing aloud on the microphone” by Jason Rosewell
“girl listening to radio tape-player” by Eric Nopanen
“uniformed men holding rifles with military motorcycle” by Kyppy84
“misty mountain (empty) roads” by Fritz Bielmeier
“man riding motorcycle loaded with lot of luggage” by Lars Bo Nielsen
Edited mages:
“vintage military motorcycle resting against a wall in Rhodes Greece” by Mason Summers and “compass market direction” by AbsolutVision – was further edited by Wayfarer as “wayfarer-stagnant-direction”
Unsplash.com License:
https://unsplash.com/license
Unsplash grants you an irrevocable, nonexclusive, worldwide copyright license to download, copy, modify, distribute, perform, and use photos from Unsplash for free, including for commercial purposes, without permission from or attributing the photographer or Unsplash. This license does not include the right to compile photos from Unsplash to replicate a similar or competing service. Photos cannot be sold without significant modification.
“flaming-cat-wallpaper” from http://wallpaperswide.com/flaming_cat-wallpapers.html
(public domain distribution, unaltered)
A Modern-Day Incarnation of Lincoln Cosmo Carrera Panamericana
By Bandit |
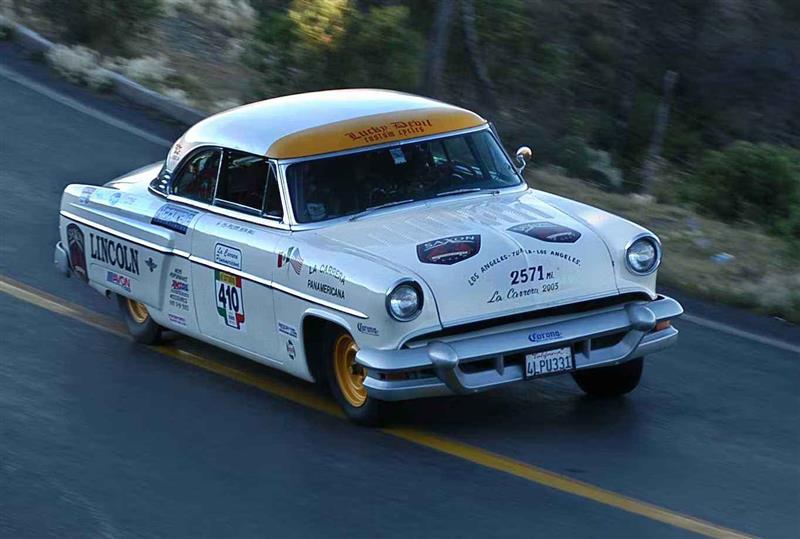
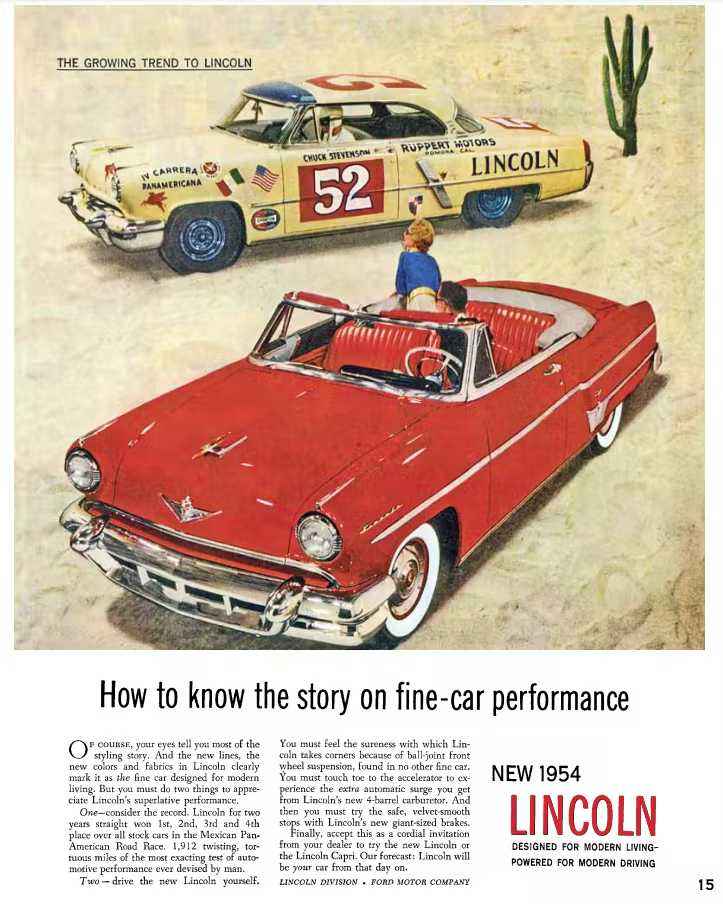
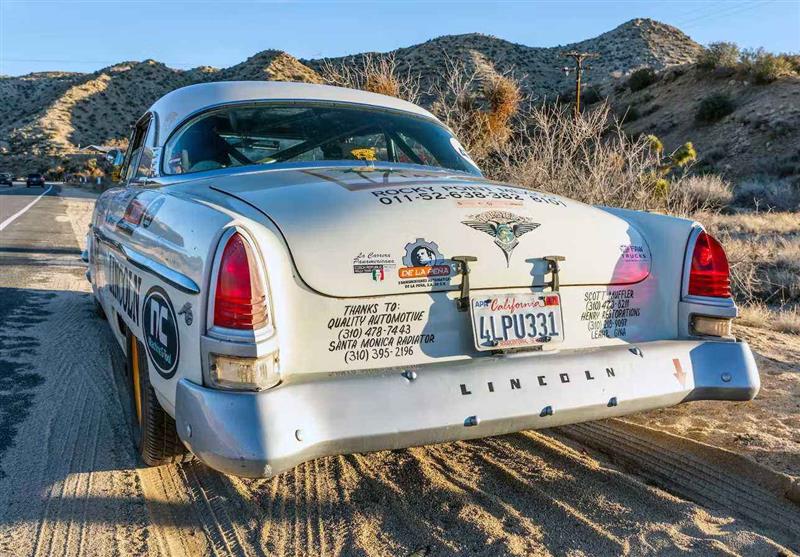
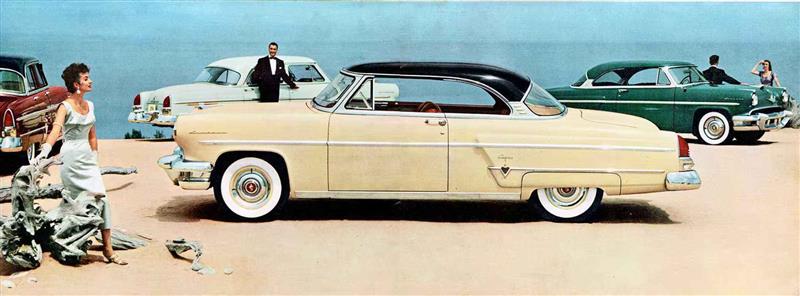
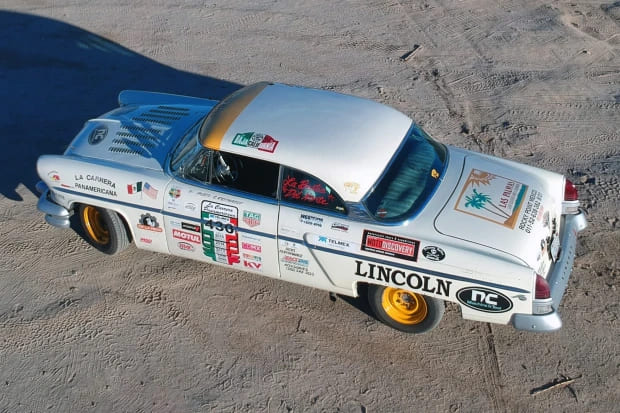
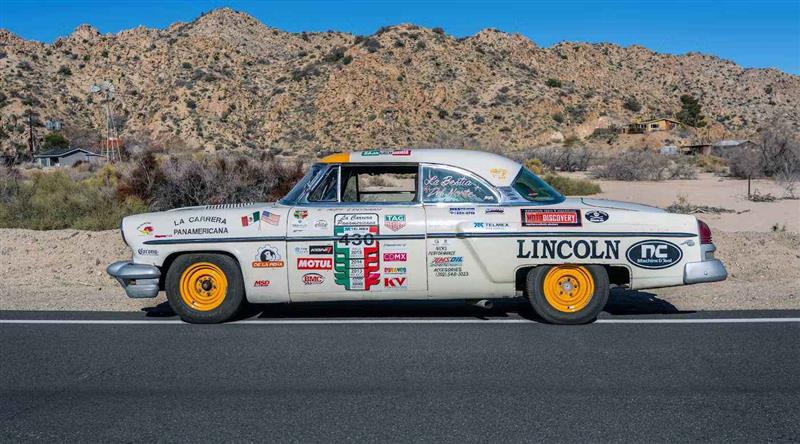
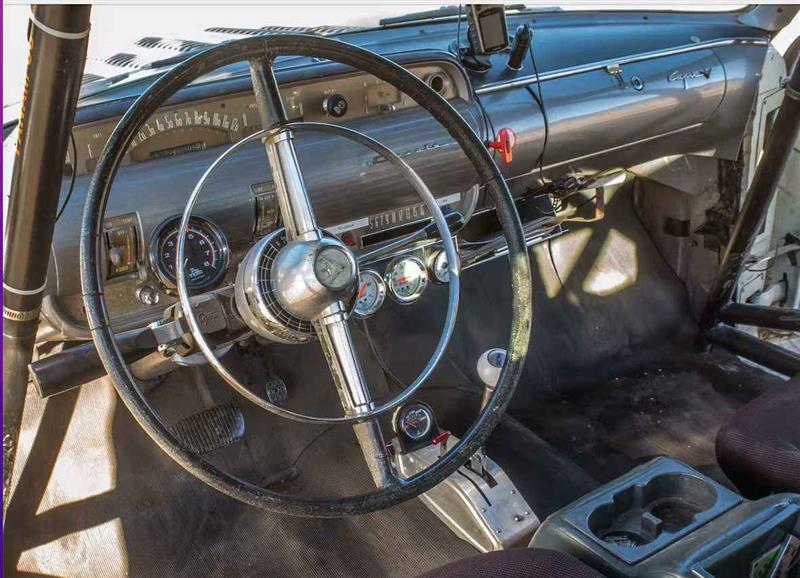
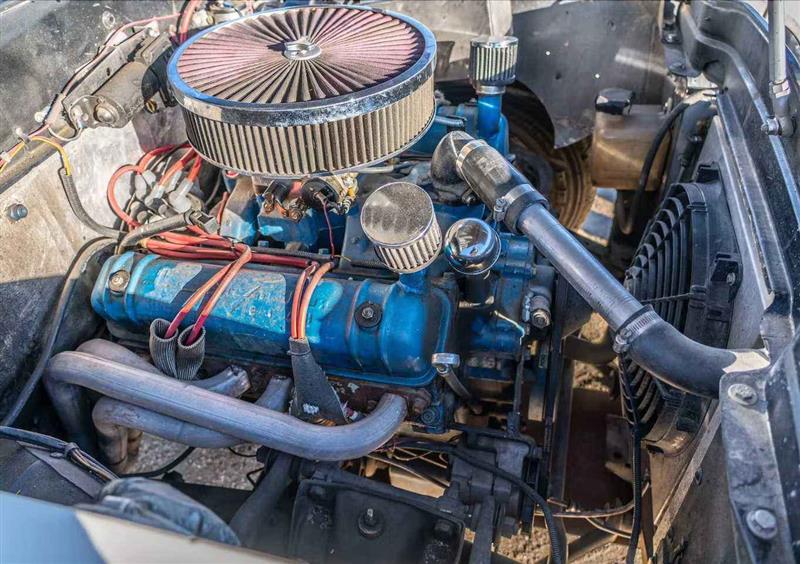
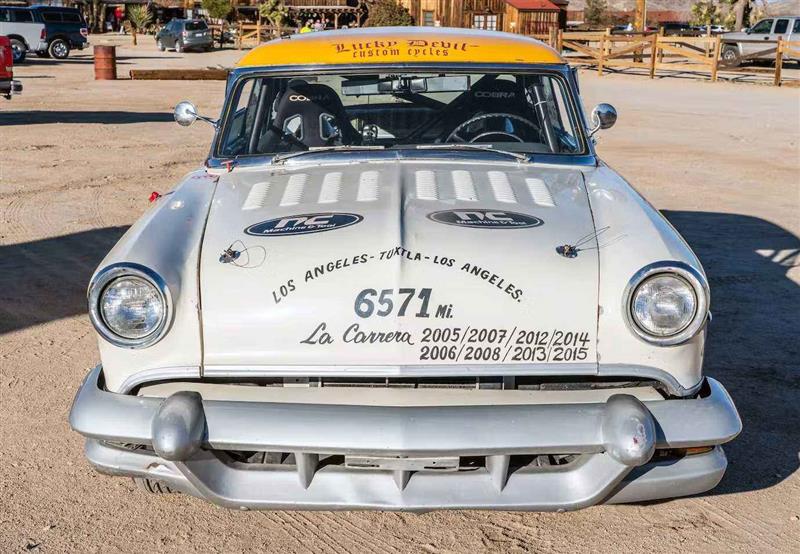
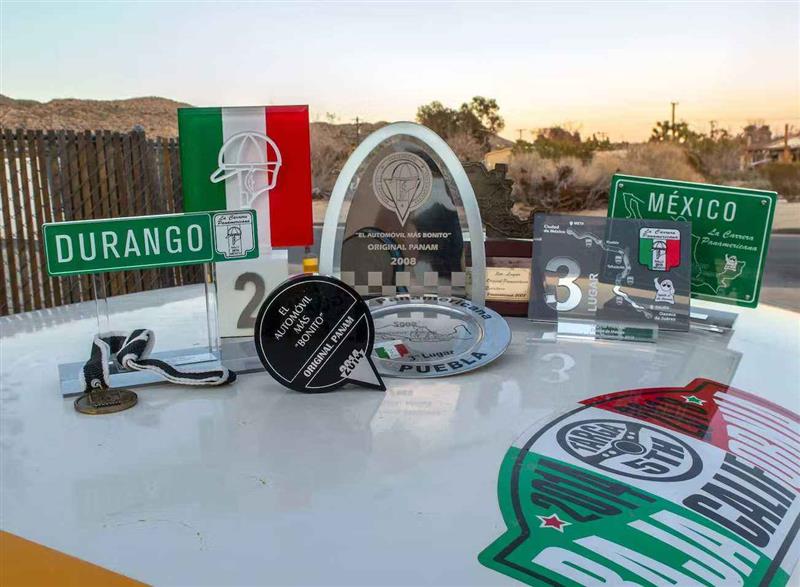
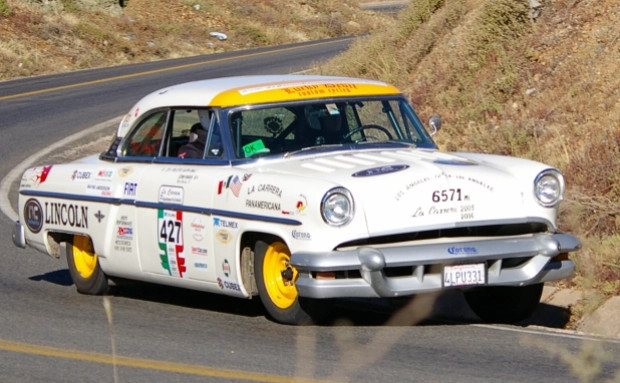
World’s Simplest Starter Tech
By Bandit |
Okay, so here’s the confession. When I build bobbers or choppers, I try to keep everything simple and super reliable. For instance, electric start circuits, which involve starter relays, buttons, handlebar switches, you name it. Maybe Billy from Spyke came up with this system that eliminates almost everything.
They are the shit for reliable, no mess starting every time. There’s but one issue with these puppies, position. They are usually located on the front of the starter solenoid under the oil tank, which can be an issue for stock bikes.
It can also become an issue for bikes with pipes running over the transmission. The original design was chromed and clean but cumbersome to point a single finger at with its rounded surface. Gloves could help or hinder, plus it’s on the same side of the bike as the throttle.
On the very positive side, it’s the shit for reliability, clean bars, reduced wiring and the chopper spirit. So recently, I built a Panhead with a ’69 right case (kidney) and a ’79 left, alternator case. It was a crazy engine deal but turned out to be the perfect system to build something reliable, yet vintage. I had a blast building this bike.
But I had one issue with starting. I was cool, when the bike was cold, but when it warmed and the pipe was blistering reaching that puppy was a challenge, besides the chrome didn’t go with the vintage patina of the bike’s finish. One more item. The original design was clean as a whistle, but the spring pressure in the solenoid, made depressing the button somewhat of a challenge. Plus, the chromed button was rounded and easy to slip off.
Somewhere in the last decade of the ruling Spyke starter buttons, Taber Nash ran into these issues and started to think about a cool, safe, secure, and tough alternative. First, he realized how much a tad more push surface would help the operation. Then he discovered the need for a longer throw to bring the button into the light.
Here’s the company description:
Regular price $140.00
The newest addition to the original NMC Starter Button! The “PUSH” button starter comes in bronze or stainless-steel ?? button and is available now!
The “PUSH” button threads (1/2-13) onto the 4 ¼” starter button shaft. The plunger comes with a black powder coated steel body, steel shaft and bushing.
Just give it a push to start your bike! Fits most all 1.4 kw and 1.6 kw starters .
When first introduced to the Nash Push Button I was intrigued. My first consideration was the size and surface of the button. I didn’t realize how much farther it stuck out compared to the original almost 1-inch. I ordered one.
First, I removed the ground strap to my battery.
With an Allen T-handle wrench, I removed the three small fasteners holding the solenoid in place. It sprung out at me slightly. The Nash unit didn’t come with a new gasket, so I carefully removed the existing gasket and installed it into the new unit.
With the two units in hand, I discovered the differences in weight and the massive bolt Nash used to depress the solenoid. I became concerned and studied both units.
The extended casing was also bulky and steel. Again, I was concerned about the overall weight and the tiny Allen head fasteners holding it in place. It took a while to get my head around the differences in the units.
Once installed and carefully tightened, the benefits became apparent. I installed the fasteners with the T-handle again. I’m not a fan of torque wrenches especially for smaller fasteners. I’ll use them on head bolts, engine shaft nuts and massive stuff, but when it comes to smaller fasteners, it’s easy to over tighten with that long-handled bastard. If you don’t feel or hear the click, you could be fucked.
I have a couple of pals who won’t attach any fasteners without a torque wrench. In a sense that wrench removes the responsibility, knowledge and feel from the mechanic.
There are other factors to consider, like the fastener material, the thread pitch, the base material and the age of the fasteners and material. The feel, knowledge and prep are everything. There’s that notion of tightening a bolt until it feels snug then tightening just enough to put the correct tension against the fastener and the threads to keep it in place and doing its job without damage.
Okay, fuck it. I snugged down the stainless Allens, hooked up the battery and tested it. Worked like a champ, even with gloves. The extended unit delivered the button into the light of day and made it easier to reach and depress.
Let’s ride.
I reached out to a longtime Harley tech to review my article. He made some very good points:
Anytime you can reduce extra wiring relays etc. It’s a good thing.
The Nash starter button does all that. The bronze button looks good to me. More character for me.
I hear you on using torque wrenches on small fasteners. You need good torgue wrenches when using them on inch-pound specs.
Also, I go with lower setting than is specified. Then maybe go to the middle spec. I have a Snap-on inch-lb. clicker and a Matco needle/dial inch pound wrench also.
I use the Matco needle/dial mostly when servicing late model H-D Springer rockers. A clicker torque wrench doesn’t work for rocker-stud adjustment. In addition, the Matco goes below 40-inch-pound limit that the Snap-on has.
So, when you can make any part of an H-D electrical system easier and less complicated, do it. Simplicity means more reliability on a H-D!!
–Pablo
The Glory Hole from Court House Customs
By Bandit |
You’d think a town named Washington Court House and a shop named Court House Custom would both contain staid and conservative attributes, like an old Carnegie Library or a shop fulla bridal dresses and fine crystal. Not so kimosabe.
Court House Custom is in Washington Court House, Ohio which is located centrally between Columbus, Dayton and Cincinnati. Washington Court House (often abbreviated as Washington C.H.) is a small city in Union Township, Fayette County, Ohio.
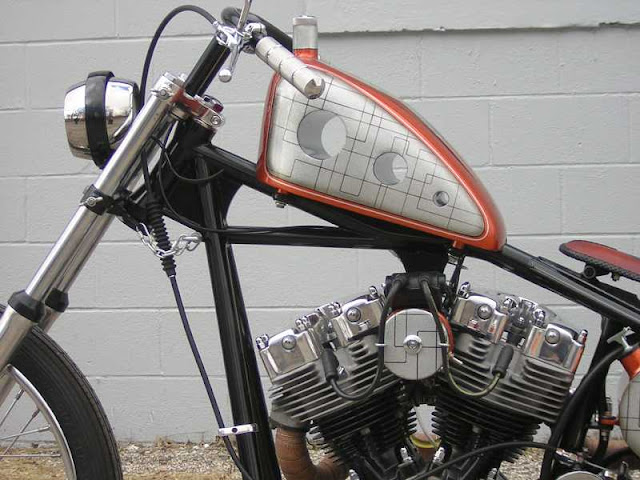
Colonel Alonzo B. Coit ordered his troops to fire through the courthouse doors, killing five men. Colonel Coit was indicted for manslaughter but was acquitted at trial. After the trial, Governor McKinley stated, “The law was upheld as it should have been … but in this case at fearful cost … Lynching cannot be tolerated in Ohio.” The courthouse doors were not repaired or replaced and the bullet holes from the 1894 riot are still present in the southeast doors.
In 1910 the “Court House” suffix was used to distinguish the city from other places in the state with “Washington” in their name. The nasty history doesn’t end there.
The Court House shop was owned by Jason Stritenberger and D.J. Jenkins, two longtime friends who have known each other since grade school. Jason and D.J. started welding, building bikes and powder coating in Jason’s garage in 2004, but D.J. had a twist. He started building gas tanks with holes in them.
In late 2006 both of them decided to leave long term jobs to follow the American entrepreneurial dream and start their own business doing something they love, but Jason wanted D.J. to change is evil ways. The chopper spirit takes on odd and sometimes foreboding characteristics.
Since opening, the Court House Custom grew into a reputable company but faltered when D.J. built a scooter named Dirty Sanchez. D.J. welded into the night turning out strange components with bizarre designs. He snorted powder coating pigment and lived in the oven. His partner became wary of his macabre behavior, while trying to keep the calm reputation of the Court House.
Then D.J. started talking about glory holes and tasteless women. That did it, the partner split.
D.J. never turned away from adversity. He snorted a line of Tangerine pearl powder and went to work doing everything he could to keep the Court House lights burning, he turned out some of the finest powder coating in the region. He changed tires, did tune-ups, restorations, metal polishing, chroming, machining services and engine rebuilds.
Hell, he had the only shop in this small town and had to do anything and everything to keep the cash flowing and the brothers on the road.
In mid 2008 Court House Custom launched a new line of custom motorcycle parts designed and hand built by D.J. and Jason, but with Jason out of the picture, ground up chops and new product design waned. “I had to focus on keeping the lights on,” D.J. said and replaced the drive-chain on a customer’s Sportster.
But in his eyes the flare of the chopper lives.
In November 2008 CHC gained national recognition when the CHC Triumph was featured in Cycle Source Magazine after it won best of show in a Cycle Source Bike Show.
In early 2009 Chris Callen, the boss from Cycle Source offered CHC a spot as an advertiser in the Limpnickie Builders Manual. D.J. continued to keep The Court in the spot light earning a 3rd Place win with the Glory Hole at the Easyriders Bike Show in Columbus in February 2009.
After the win at the Easyriders Show, the boys traveled to the Horse Smokeout in North Carolina in May of 2009.
The Smoke Out proved to be a successful venture when The Dirty Sanchez and The Glory Hole were both picked as 2 of the 10 winners. Throughout 2009 they continued to travel the country attending many motorcycle events and spreading the word about Court House Custom and the Limpnickie Lot. See, the chopper spirit lives!
The future of CHC will be focused on offering continued service work from oil changes to engine building, building one-of-a-kind custom motorcycles once in a while and improving the efficiency of their powder coating processes.
“The Glory Hole Specs”
Year: 2009
Model: 1980 Harley Shovel
Engine
Carb: S&S
Air Cleaner: Bare Knuckle Choppers Glass Jaw
Pipes: CHC
Transmission
Model: RevTech
Type: 4 Speed
Accessories
Gas Tank: CHC
Battery Box: CHC
Grips: CHC
Tail Light: CHC (Made from Vintage Microphone)
Pegs: CHC
Head Light: CHC (Made from Vintage Spot Light)
Bars: CHC
Rear Fender: Led Sled
Oil Tank: CHC
Handlebars: CHC
Seat: Outside The Box Cycle Seats
Frame
Type: Rigid
Builder: Maximum Metal Works
Paint
Painter: Darren Williams @ Liquid Illusions
Paint Color: Cinnamon Pearl and Silver Flake
Awards
3rd Place in Street Custom Judged Class, Easyrider Invitational Bike Show, Columbus Ohio 2009
SHOW WINNER 2009 Horse Smoke Out 10
2022 Motorcycle Week Laconia New Hampshire
By Bandit |
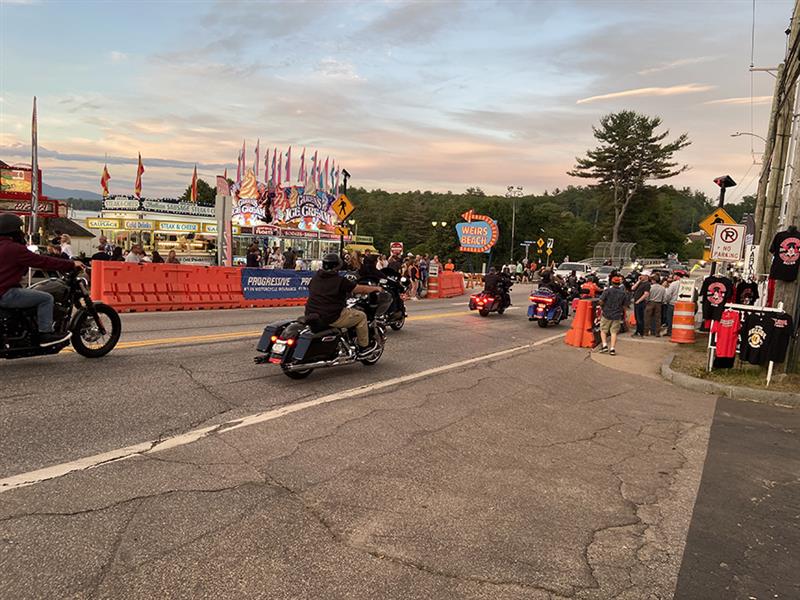
It has been a lot of years since I was last at the Laconia Rally, and so far it has been very interesting. Usually I ride my motorcycle to the rallies and am there to take photos and do an article on the event.
This year I am here to be part of an event celebrating and honoring people in motorcycling put on by Paul Cote with Check Twice – Bikers Helping Bikers. https://checktwice-savealife.com
I do not think I have ever flown to a motorcycle rally before, But I am honored to be invited to this and time did not allow to ride and hell, with gas prices it was cheaper to fly.
Okay, so I flew in and met Paul at the airport and a motorcycle was there for me to ride. We made it to Weirs and the motorcycle just quits in the middle of busy Saturday traffic. Motorcycle had gas and acted like a dead battery. I get a push and try to jump start it without any success. Ended up at the Weirs Beach Convenience and Gifts Food Mart.
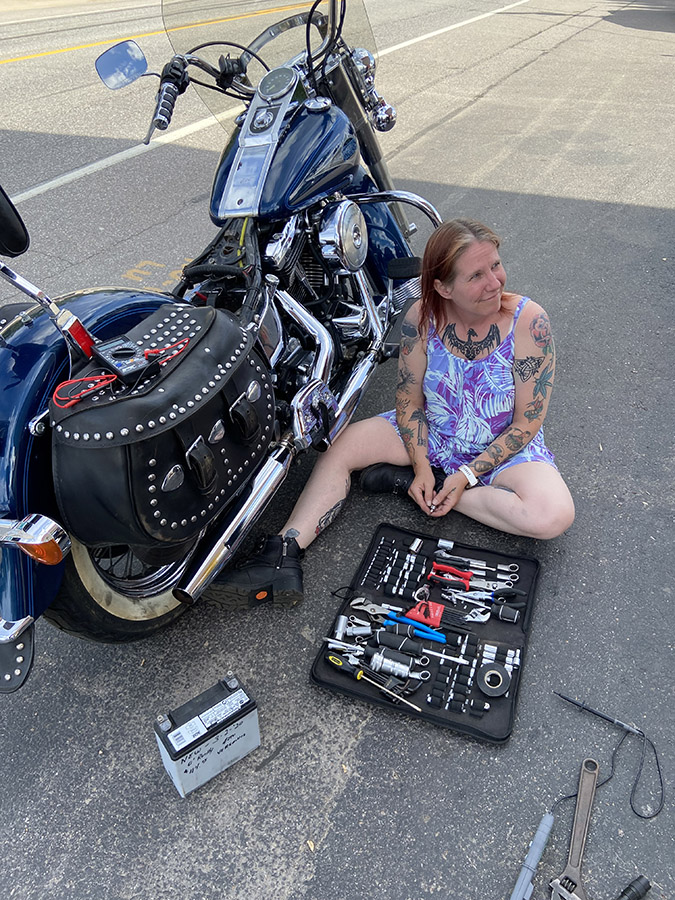
As we figured out how we are going to handle this Paul checked with the owner about us parking there. It turns out her name is Jennifer and she said not only can we park there, she will help. Next thing I know she had the seat off and one of those hand held jump start tools. It did not start the motorcycle. I am lucky enough to know a lot of women who wrench on motorcycles and Jennifer knows what she is doing, I was in good hands so I stood back and watched.
She and I both believed it was a bad battery. Off Paul and I went to the parts store. The guy at the part store said he tested it, and it was okay. Well technically it did have voltage but No Cranking Amps. We ended up buying a volt meter and went back to the motorcycle and Jennifer re-installed it. We put the meter on it and 12.5 volts. She hit the start button and meter dropped to 5 volts.
We were scheduled to be at the Chop Shop Laconia Beer Tent for a raffle drawing, so arrangements are made to have motorcycle towed and repaired.
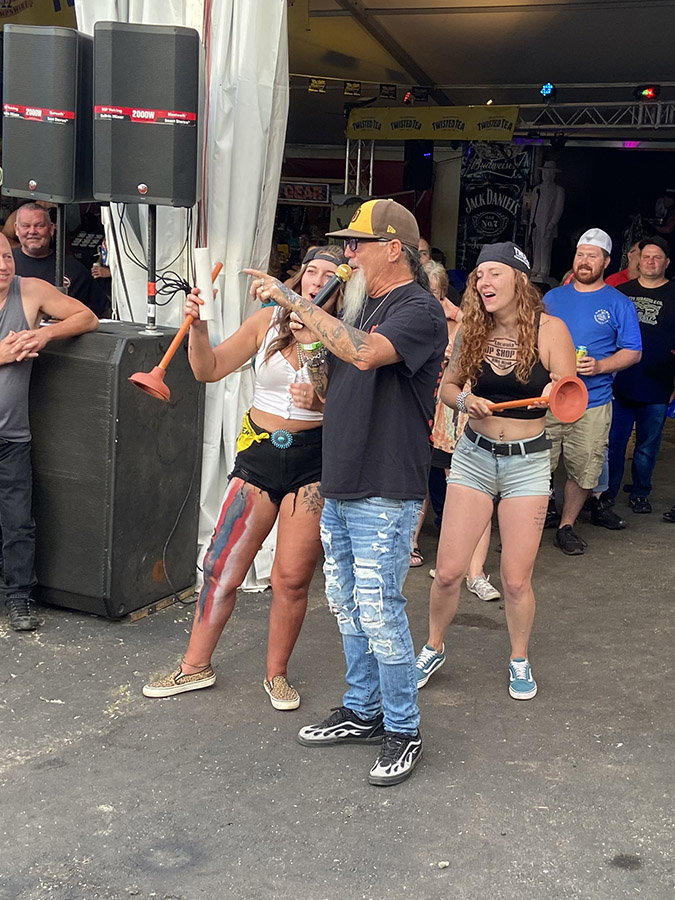
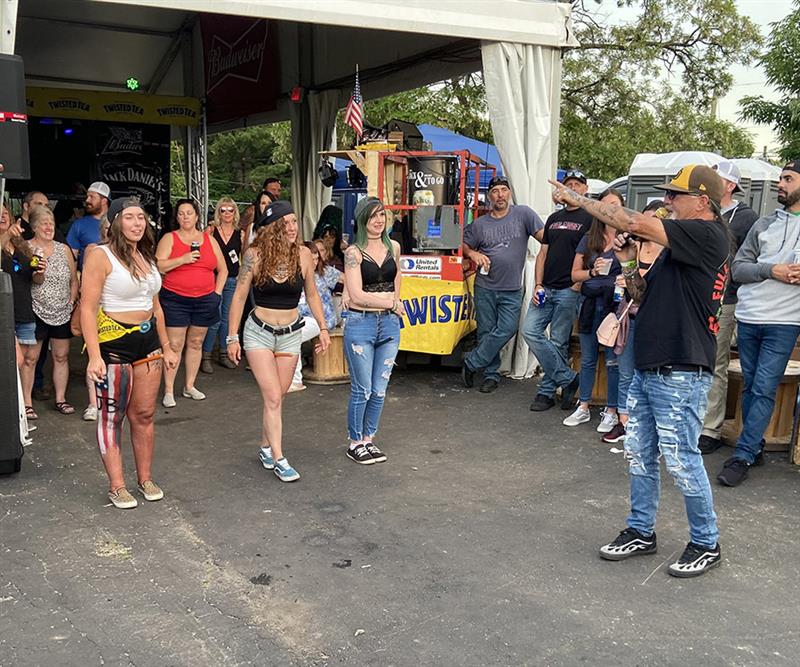
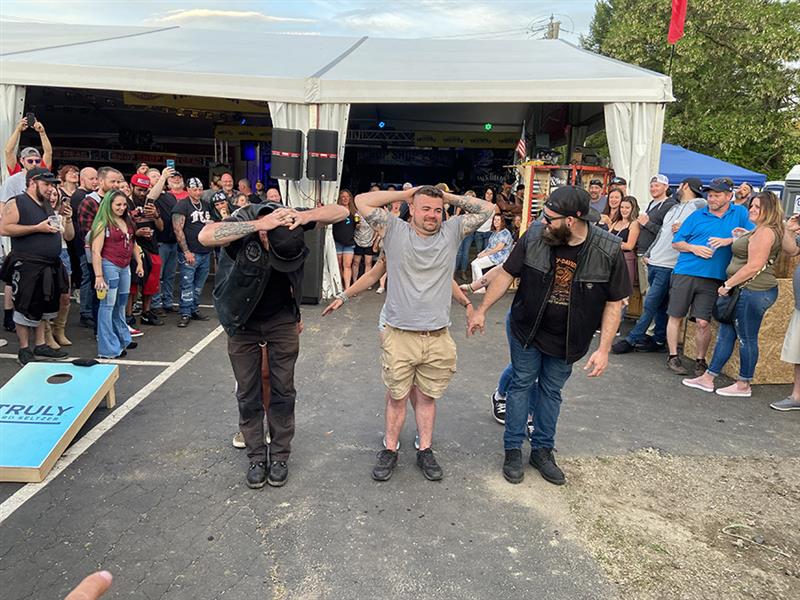
The Chop Shop was crowded with folks partying. Time for some adult games. This one was where the guys held a piece of pvc pipe between their legs and the women with a plunger between theirs and try to insert the handle in the pipe without using their hands. Interesting at best and a lot of fun had by all.
The motorcycle ended up at EVL CYCLES in Belmont, and the owner Tony Tal installed a new battery and checked the charging system and got us back on the road by Sunday.
In the meantime Patrick let me ride his Softail to ride to Weirs
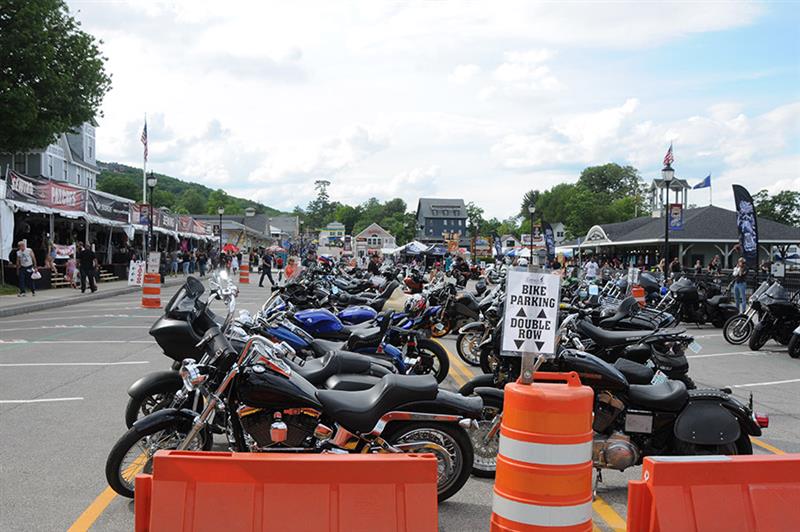
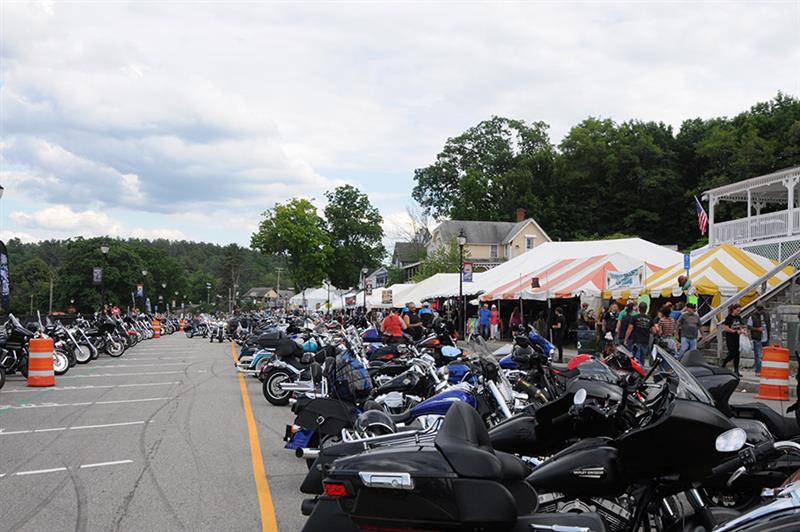
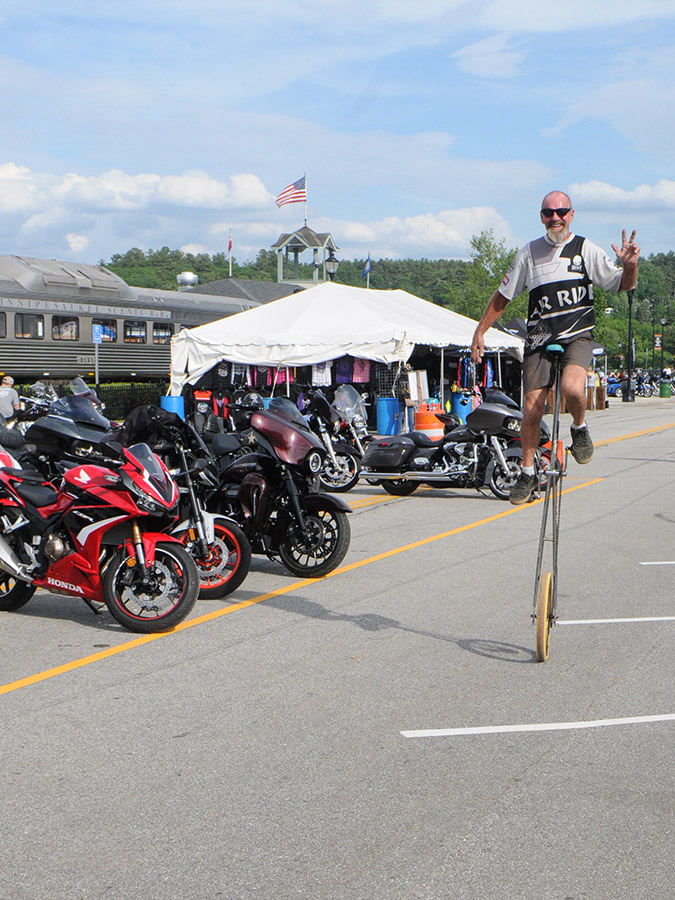
So far it has been interesting and enjoyable and still have a few more days here. Hang on for more reports.