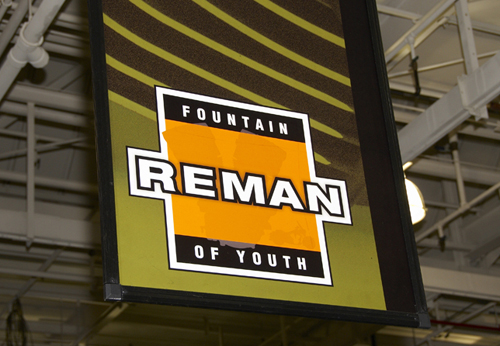
We head into Kerry's Head Works Shops for this next segment. Here's a link to the first Chapter, in case you missed something: The Reman First Chapter
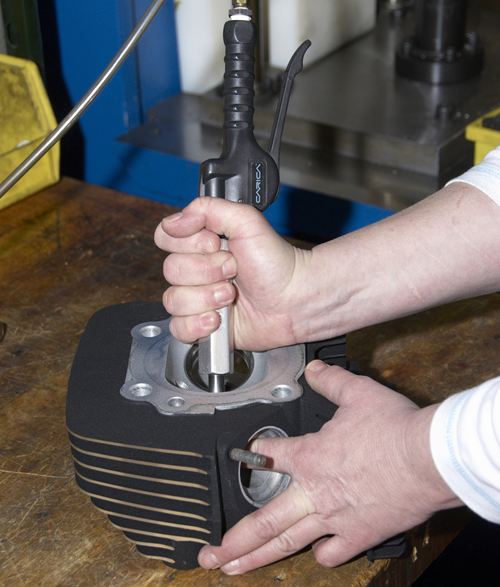
This weapon gauges the bore in the head after the valve guide is removed, to determine the guide size needed during the Reman process.

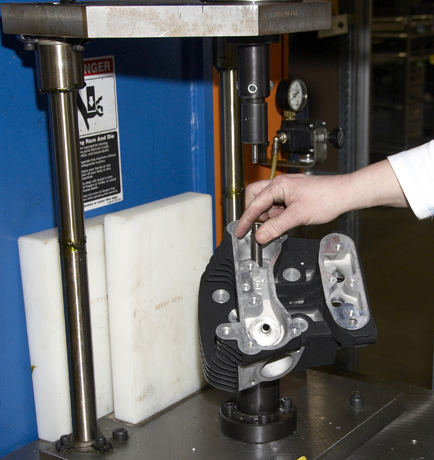
Us old builders avoided oversized valve guides because we were determined to make a set of heads last forever. We would carefully heat and tap out the old guide and pray the new stock guide would fit tight as a boar’s ass. The factory knows the average rider won’t put 200 k on a given engine and two 200 k engines would last most guys a livetime. So the factory pressed in a new set of oversized valve guides and goes to work.
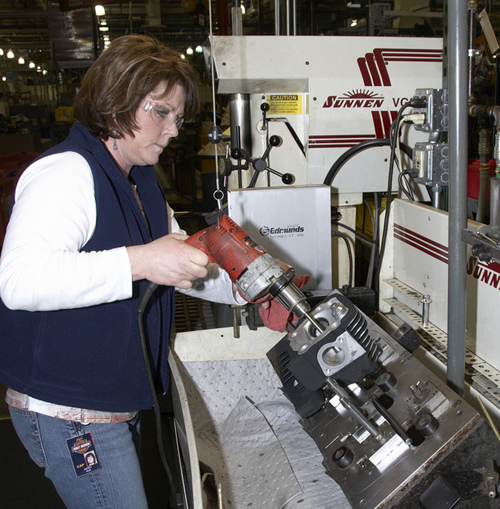
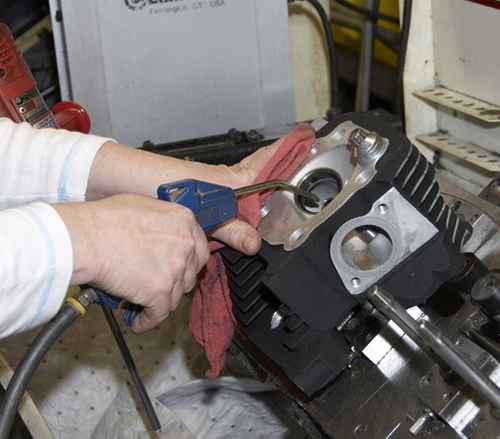
With new oversized guides in place Kerry reams the valve guides to insure the perfect valve to guide fit. Then she cleans them thoroughly, before checking them for fit.
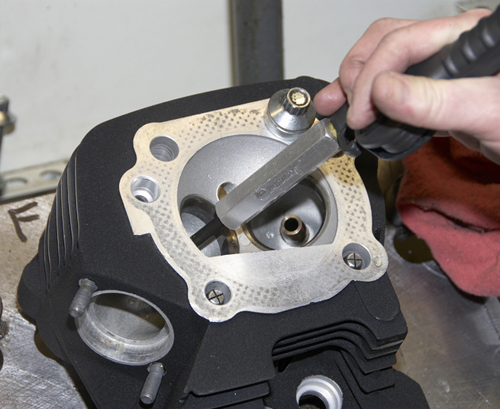
This shows the tool used when gauging valve guide fit. Too tight and the valve may drag and score the inside of the guide. Tool loose and the cylinder might smoke prematurely.
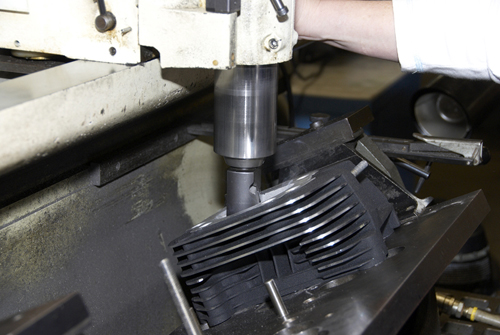
Unless there’re severe damage to the heads all the valve seats are re-cut and checked.
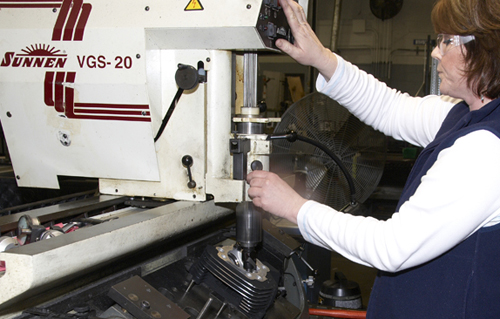
Here’s the Sunnen tool used for precision valve seat cutting.
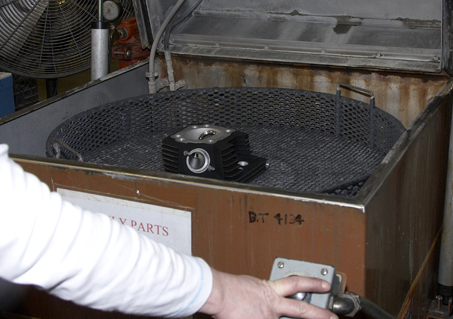
This is the final steam wash before valve train assembly.
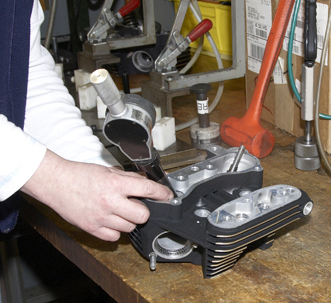
Kerry measures the valve seats to determine whether the head will need service or a standard valves
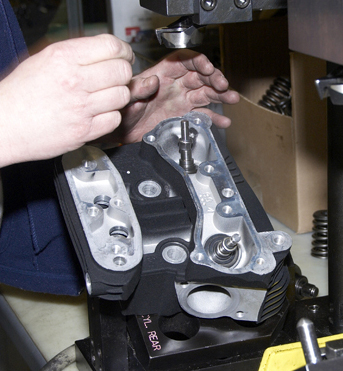
Evo heads have valve guide seals to prevent oil from seeping into the cylinders. This shows the bottom valve spring collar in place and the seals pressed on the valve guides over the valves.
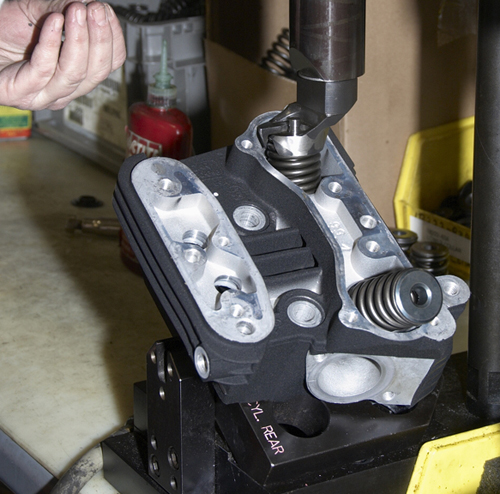
Here’s Kerry assembling the valves and springs to the heads. It’s interesting to see women in this process. There are brothers out there, who spend their lives learning the best way for building engines. This shot shows the press tool used to put down the top valve coller and insert the clips. At high speeds the valves are racing in and out of position. I was taught that if the clips aren’t inserted properly between the collar and the valve, disaster could strike. It’s critical.
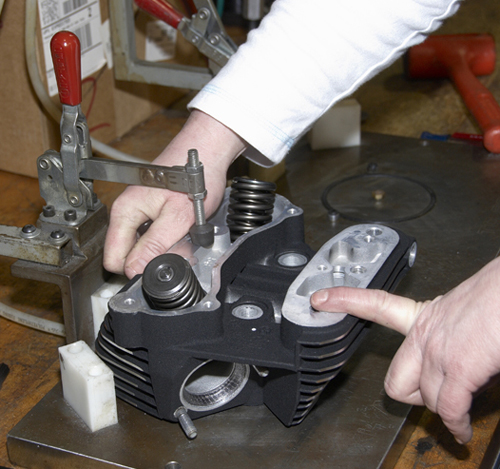
Each cyllnder is Vacuum tested to check for combustion chamber leaks. Next we will take you to the engine case station where Denise and Jeff refit an entire engine.


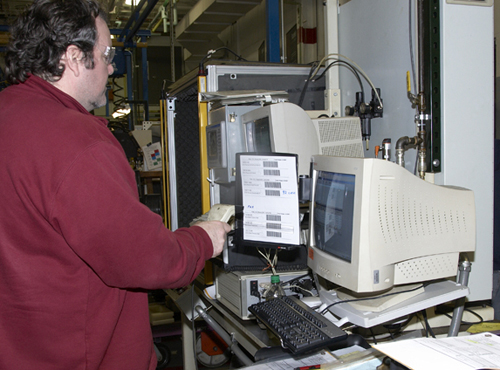
Here’s the stage where the engine begins to return to its formerself according to the customer’s order. Anytime you want to shift back to the first half of the Reman process just click here:The Reman First Chapter
I’m anxious to talk to the man in charge one more time before we put the Bikernet seal on this interesting series. At this point the paper work is checked to determine the finish type, since you can order your engine standard, black and chrome or polished.
I spoke to Scott Miller, the man in charge of the ReMan program for Evolutions and Twin Cams. He's also in charge of the new engine building program, including Evos, Twin Cams and big inch Twin Cams. I quizzed him about wear and tear, what survives and what fails. “We record and document failure codes,” Scotts said. Unfortunately he couldn't tell me if the Evo lasts longer than the Twin Cam or what is weak in their engines. “But I can tell you, if a rider is reasonable with his engine during use and changes the oil every 2000 miles, he will get a lot more riding out of it.”
He also told me many riders go for the $2000 ReMan just to freshen up engines and have the components powder-coated. Before 1994 engines weren't powdered for a much more durable and long lasting finish. He also pointed out that all the cosmetic components are replaced with new parts including chrome.
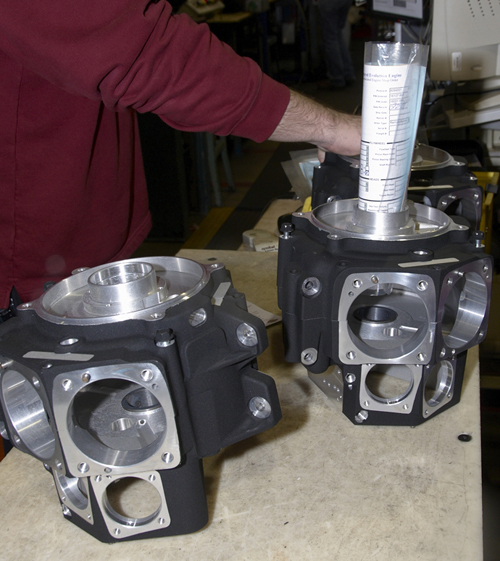
Back to the paperwork for Jeff – build the engine back up per the order.

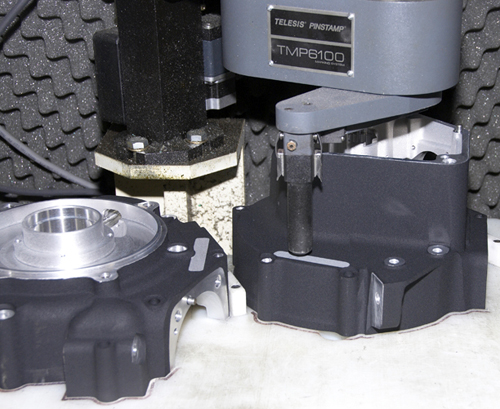
Since our original cases were not used, the original VIN # and serial numbers on my engine crank cases were stamped into the new cases.
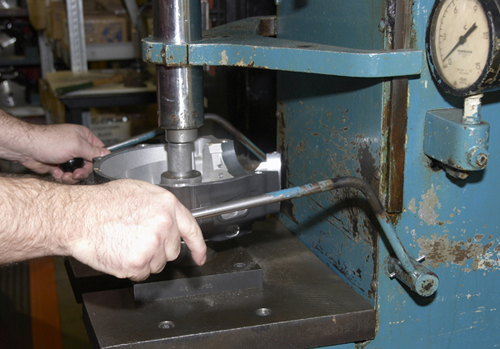
On the drive or left case Jeff pressed in the new Timken bearing race. It’s interesting to note that late model Twin Cams don’t run Timken bearings on the sprocket shaft, but shifted back to the old roller style from the Panhead era (like the ones used on the pinion shaft side here). Zippers makes a kit to exchange the roller style bearings back to Timkens for Twin Cams. Harley is satisfied with the roller style even for their 110-inch Twin Cam engines.
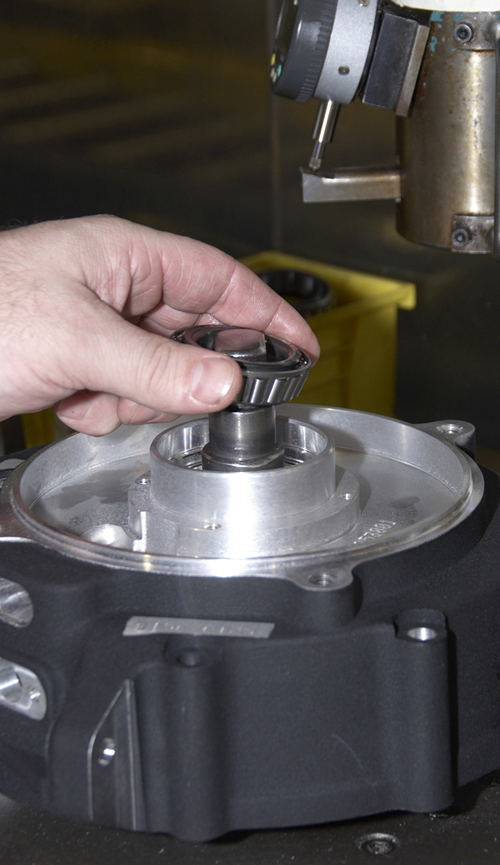
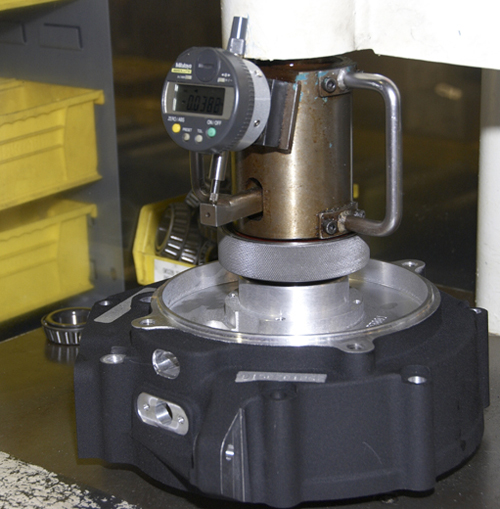
In this machine Jeff places the Timken bearing sets and the checks the fitment between the outer and inner bearing. I believe the bearing sets come complete with the inner and outer race and center spacer, but it’s always good to gauge the Timken bearing end-play.
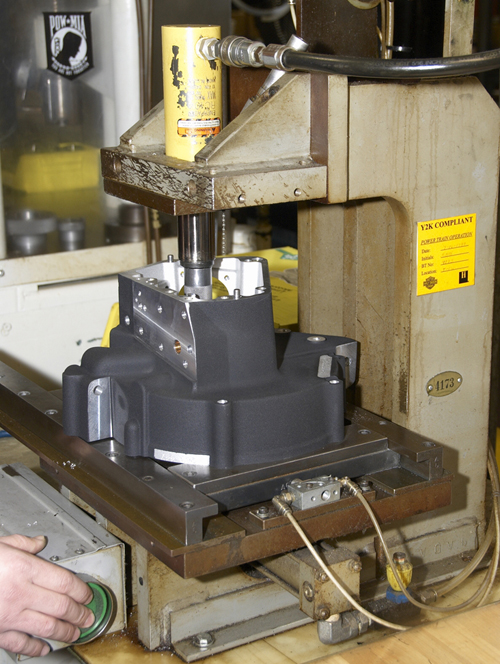
Jeff is also responsible for pressing in a new cam bearing. “The evo cam bearing used in all Reman engines is the most recent bearingused in Evolution production in 1999,” said Scott Miller from the factory. “This is the same situation forany other common parts, they are always updated to the latest andgreatest.”

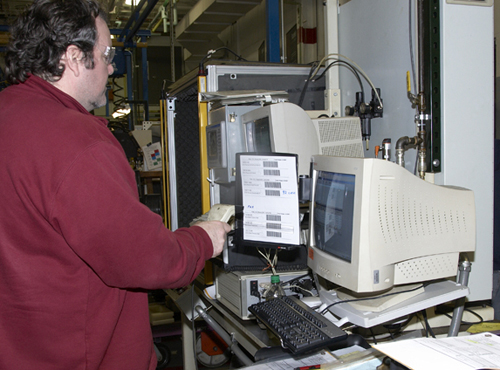
Here’s the stage where the engine begins to return to its formerself according to the customer’s order. Anytime you want to shift back to the first half of the Reman process just click here: http://www.bikernet.com/garage/PageViewer.asp?PageID=1445
I’m anxious to talk to the man in charge one more time before we put the Bikernet seal on this interesting series. At this point the paper work is checked to determine the finish type, since you can order your engine standard, black and chromed or polished.
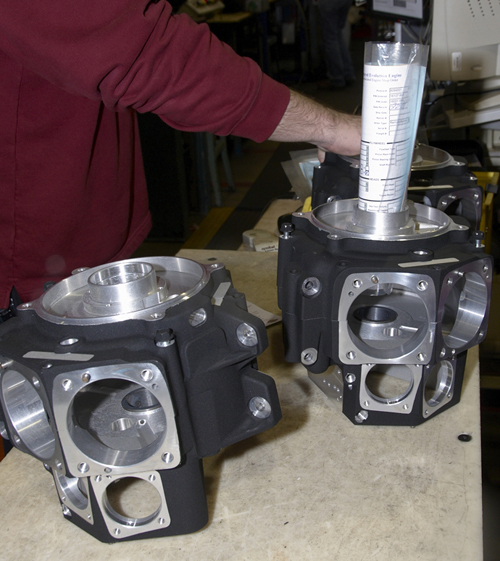
Back to the paperwork for Denise – build the engine back up per the order.

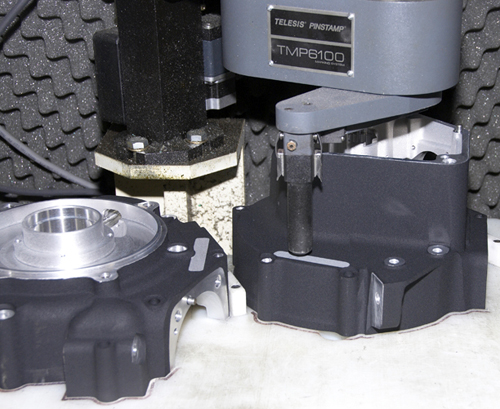
Since our original cases were not used, the original VIN # and serial numbers on my engine crank cases are stamped into the new cases.
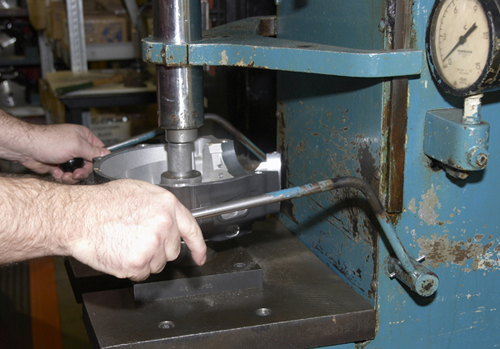
On the drive or left case Denis pressed in the new Timken bearing race. It’s interesting to note that late model Twin Cams don’t run hearty Timken bearings, but shifted back to the old roller style from the Panhead era. Zippers makes a kit to exchange the roller style bearings back to Timkens for performance Twin Cams.
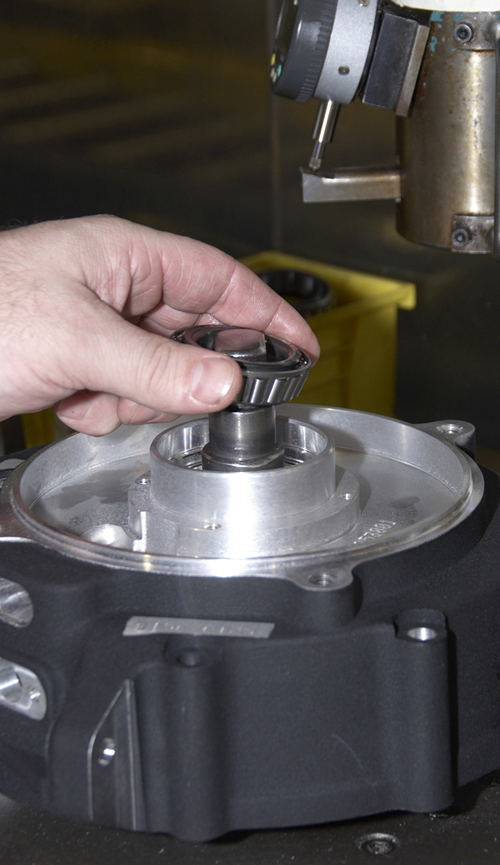
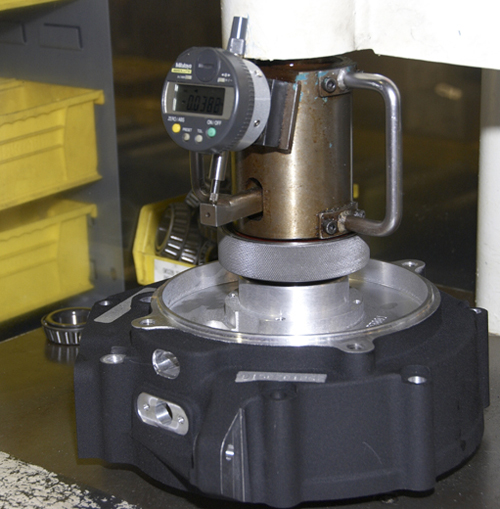
In this machine Denise places the Timken bearing sets and the checks the fitment between the outer and inner bearing. I believe the bearing sets come complete with the inner and outer race and center spacer, but it’s always good to gauge the Timken bearing end play.
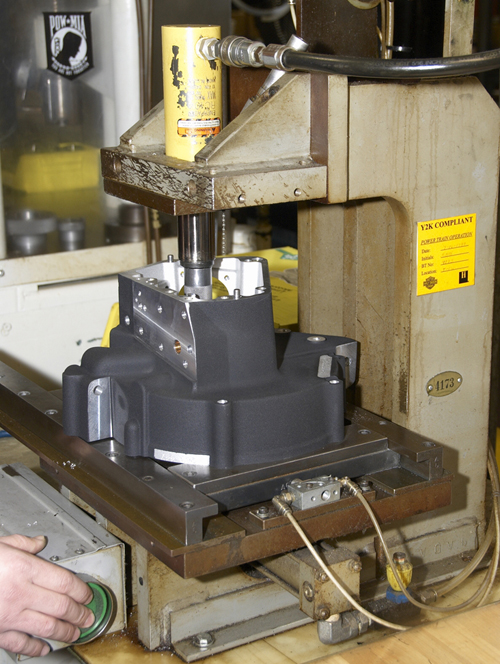
Denise is also responsible for pressing in a new cam bearing. I’ll check on the configuration of the new cam bearing. We once replaced Evo cam bearings with a more reliable model.
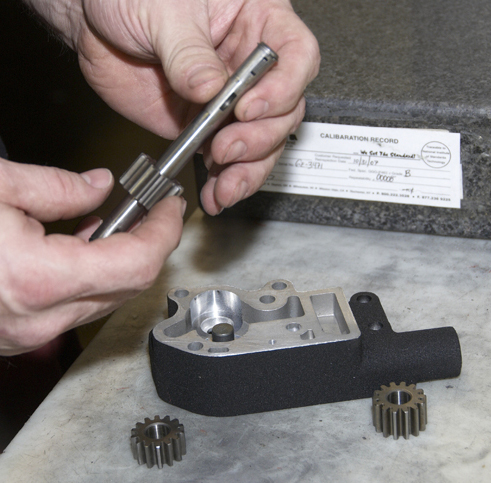
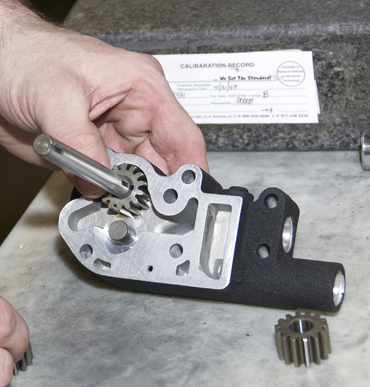
Here’s the process of putting the new oil pump elements together. I’m curious if new components are used or refurbished parts. Harley oil pumps are basically the same since 1936. These gears drive off the pinion shaft, picking up oil and sending it on it’s way throughout the engine. A simple but delicate operation. A friend in Australia just designed a new external oil pump using this design for Vincent engines.
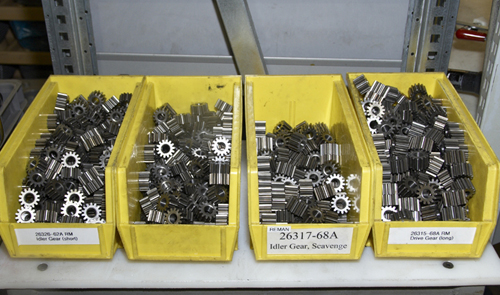
This process works fine unless you mess with the gods. I ran a Shovelhead oil pump on my old ’48 Pan. It treated the lower-end fine but cut off the top end. I had to install outside oilers to fix the problem. You don’t want to mess with the god of oil ports.
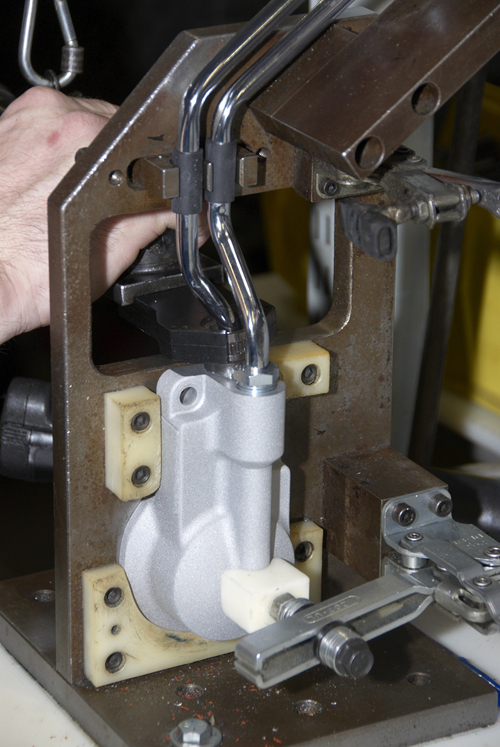
Here’s the filter mount. I’m not sure what this bracket does. It either checks the face for oil filter seal or allows the oil lines to be installed at just the right angles. I’ll check.
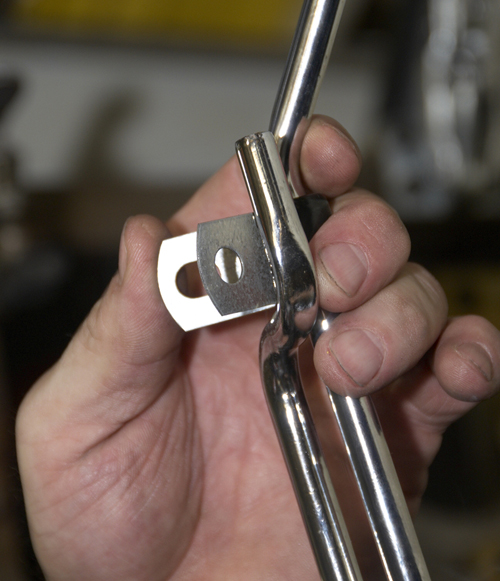
This is the process of putting the oil lines together before they’re fitted to the filter bracket. Mark handles this aspect.
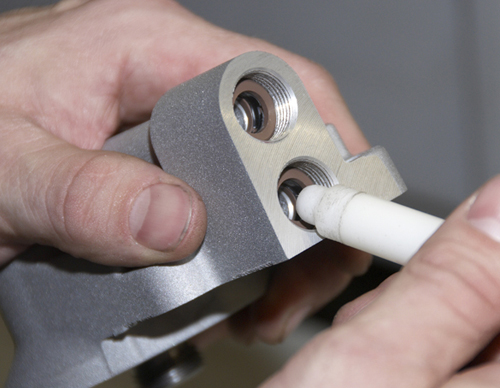
Mark installed the pre-bent oil line grommets into the filter case.
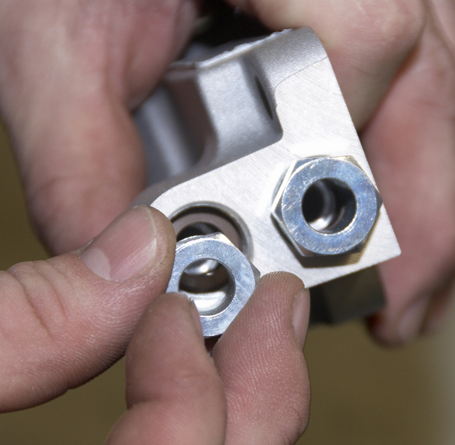
I need to dig out my Evo manual or parts book so I can describe the elements properly. These should be pipe threaded to pinch the lines into place.
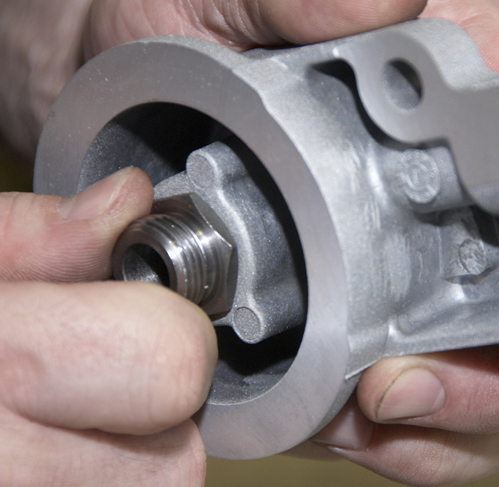
Here’s Mark installing the oil filter threaded fastener. I wonder if he used Loctite so it won’t pull out with the filter. Again, I’m curious if all these components are refurbished or new.
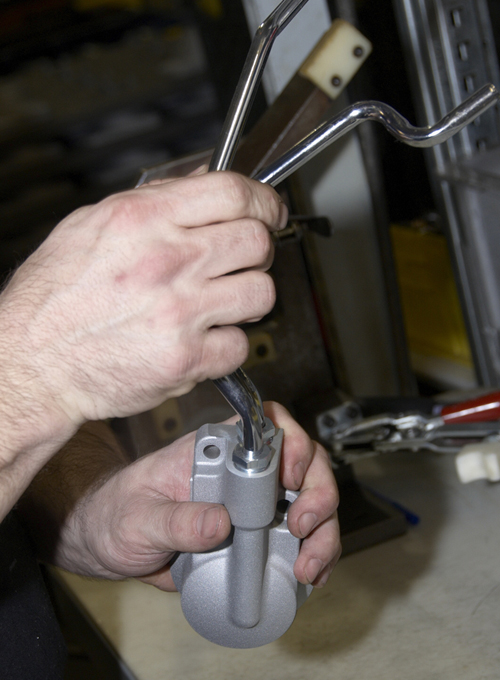
Mark Installs the new oil lines and the package is ready for an engine.
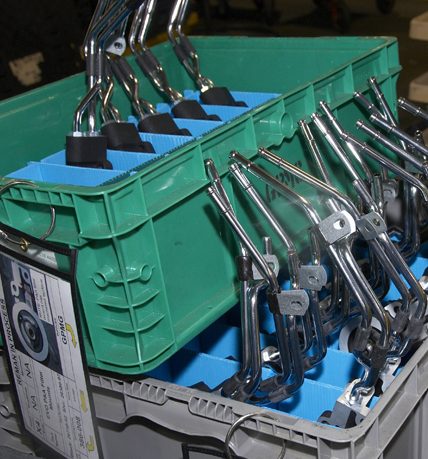
As you can see here, some of the housings are blacked out, some bare and some chrome.
Next we’ll assemble the oil pump to the case, select a set of flywheels, and Denise (that’s right, a girl) will set up our lower-end.
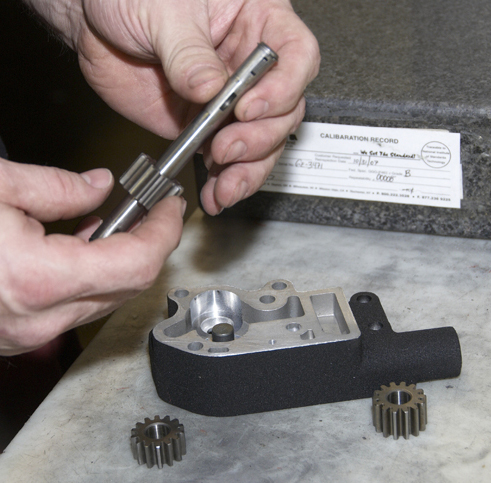
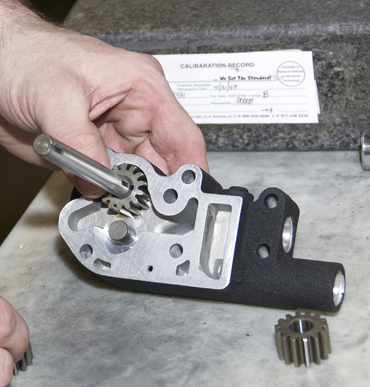
Here’s the process of putting the new oil pump elements together. I was curious if new components are used or refurbished parts. Harley oil pumps are basically the same since 1936. These gears drive off the pinion shaft, picking up oil and sending it on it’s way throughout the engine. A simple but delicate operation. A friend in Australia just designed a new external oil pump using this design for Vincent engines.
The following pump parts are refurbished and/or inspected and reusedif they meet our specifications,” Said Scott Miller. “These parts would be – gears, pumpbody, pump cover, drive shaft. All other pump parts are replaced withnew.”
This process works fine unless you mess with the gods. I ran a Shovelhead oil pump on my old ’48 Pan. It treated the lower-end fine but cut off the top end. I had to install outside oilers to fix the problem. You don’t want to mess with the god of oil ports.
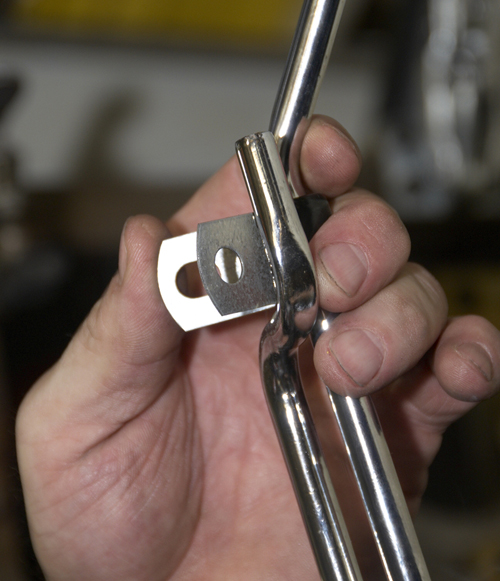
This is the process of putting the oil lines together before they’re fitted to the filter bracket. Mark handles this aspect.
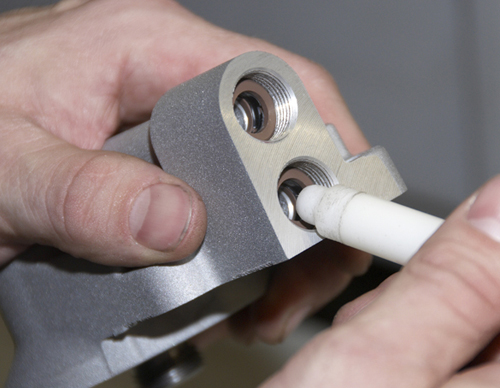
Mark installed the oil line rubber grommet seals into the filter case first.
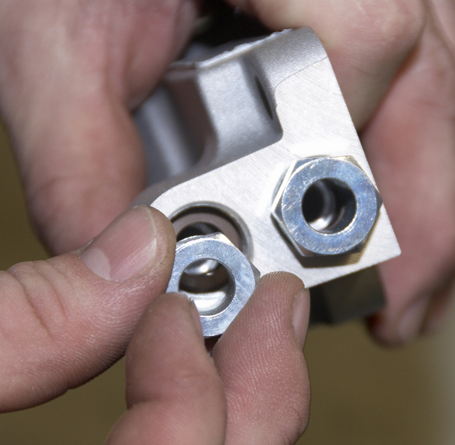
I need to dig out my Evo manual or parts book so I can describe the components properly. These should be pipe threaded to pinch the lines into place and seal them from leaks. I checked they're called compression nuts.
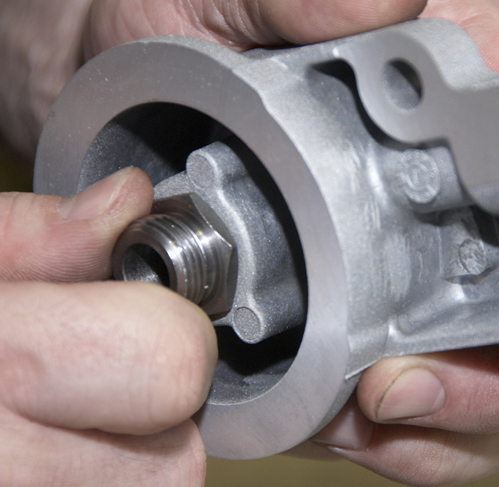
Here’s Mark installing the oil filter threaded fastener. I wonder if he used Loctite so it won’t pull out with the filter. Again, I’m curious if all these components are refurbished or new.
Damnit Bandit, only filter the mount body is refurbished (paint stripped andre-powdercoated),” barked Scott. “All other components are new, and don't forget it.”
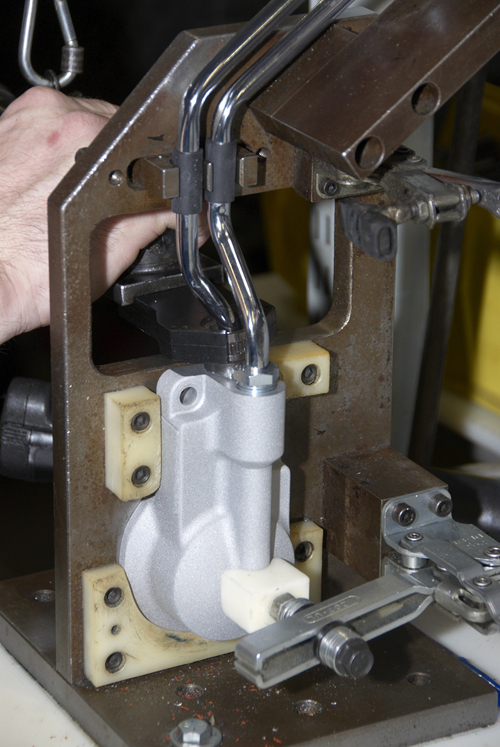
Here’s the filter mount. I’m not sure what this bracket does. It either checks the face for oil filter seal or allows the oil lines to be installed at just the right angles. I’ll check.
“It holds filter mount to assemble lines in correct orientation,” said Scott. “Thesealing is checked during engine hot test.
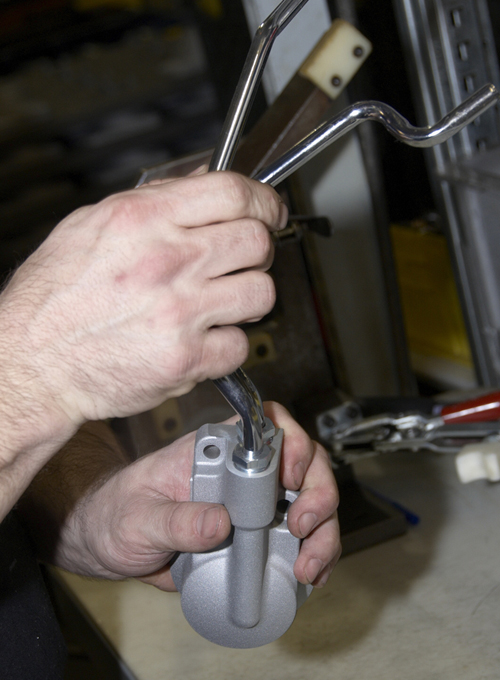
Mark Installs the new oil lines and the package is ready for an engine. Some of the housings are blacked out, some powder coated silver.
“All of our silver parts that appear bare are powder coated silver(crankcase, heads, cylinders, filter mount),” said Scott, “to give a consistent,corrosion resistant appearance.”
Next we’ll assemble the oil pump to the case, select a set of flywheels, and Denise (that’s right, a girl) will set up our lower-end.

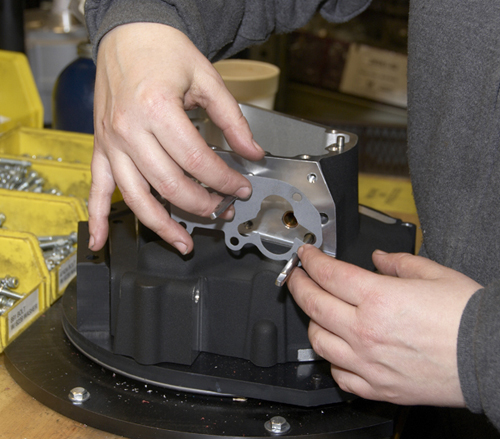
Here’s Denise assembling the oil pump to the case beginning with a fresh gasket.
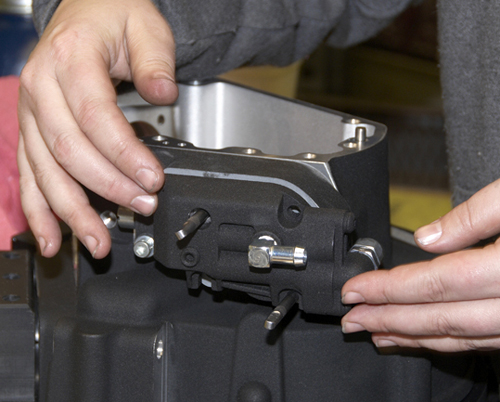
She slips on the oil pump containing new gears, shafts and keys.
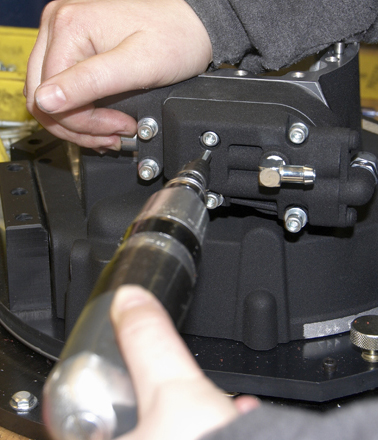
The fasteners are buzzed right into place with an air-wrench set at the correct torque rating.
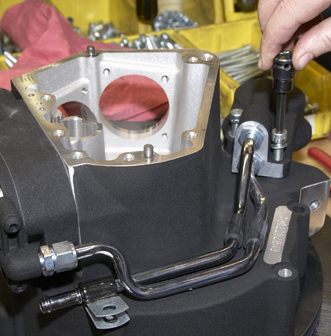
Then Denise installed the oil filter bracket and attached the return line to the oil pump.
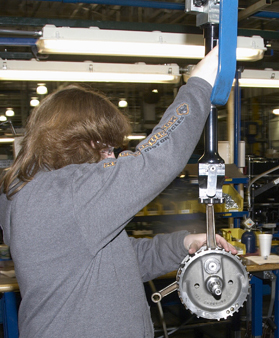
Here’s a reburbished lower end selected by Denise for the next set of cases.
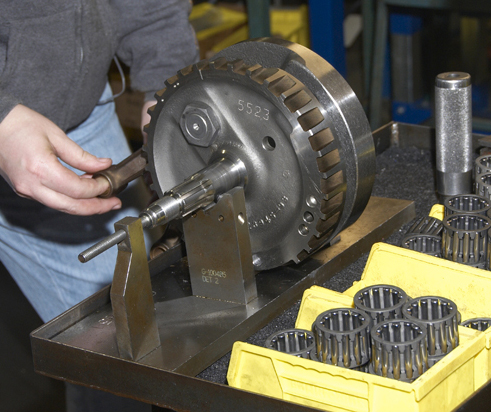
Denise checks the pinion shaft run-out one final time. The wheels have been trued and balanced, but she double-checks then pre-oils the crank shaft bearings and the pinion and Timken bearings as the final assembly takes place.
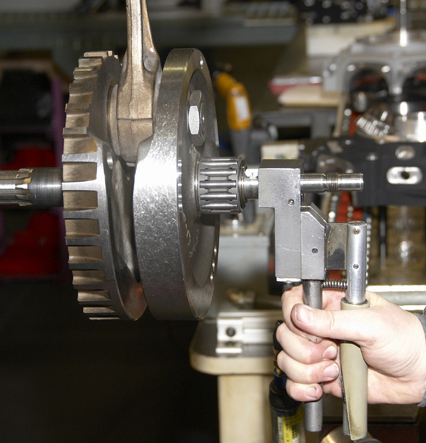
The factory has all the cool shit, like a tool to install the pinion shaft drive key.
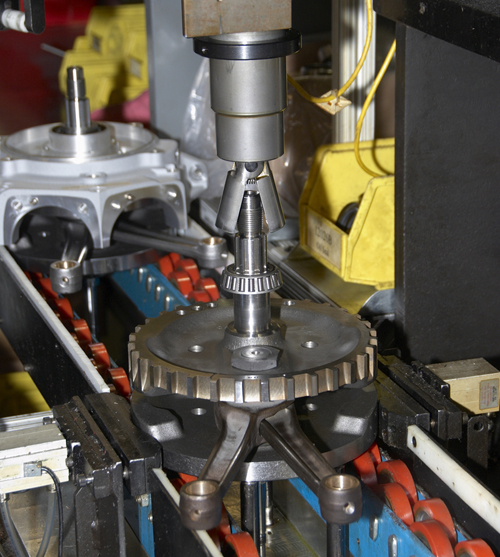
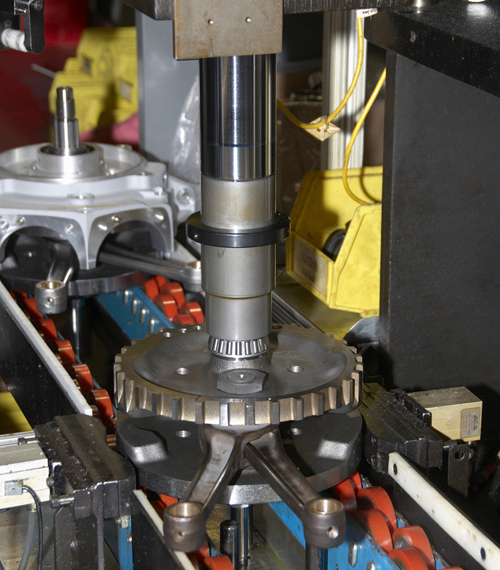
Denise this presses the Timken bearing on the sprocket shaft.
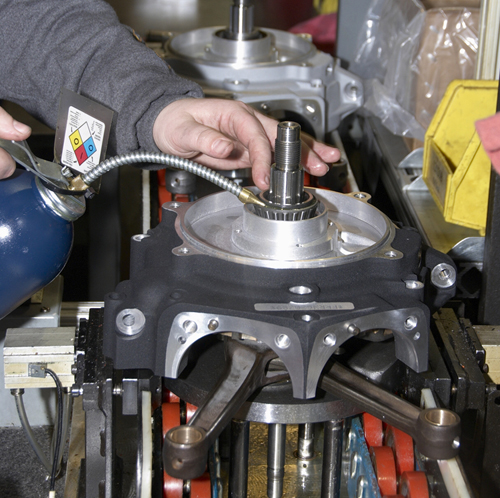
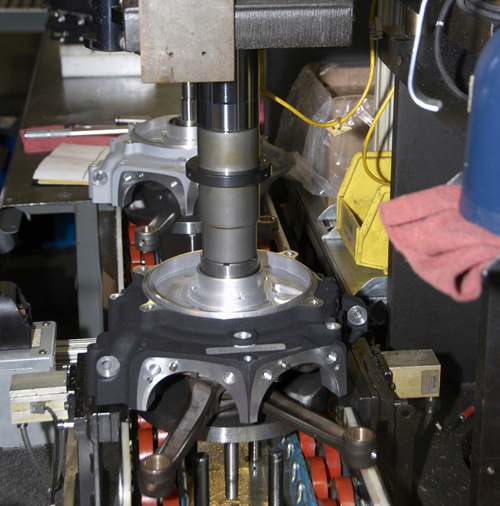
With the case set in place she oils the bearings and prepares to press the outer Timken bearing into place.
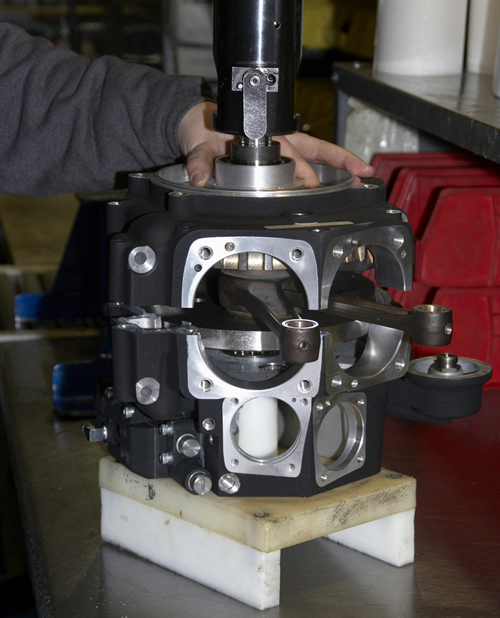
With a pinion shaft guide/protector the shaft is slipped through the right case, no pressing required.
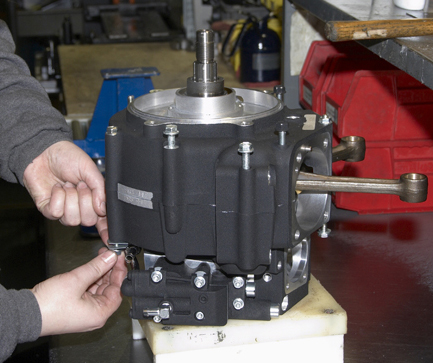
At this point Denise torqued the cases together. They use silicone based RTV sealant to seal the cases, but you don't see the action here.
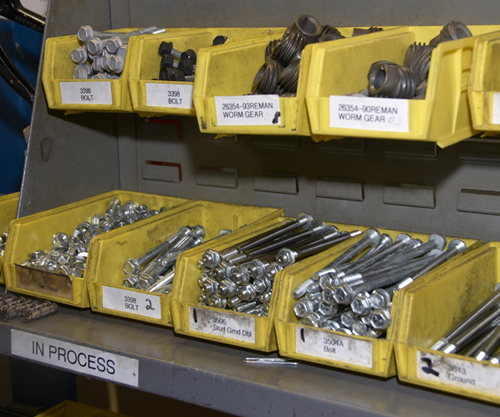
Here’s the stash of case fasteners and oil pump drive worm gears for the pinion shaft.
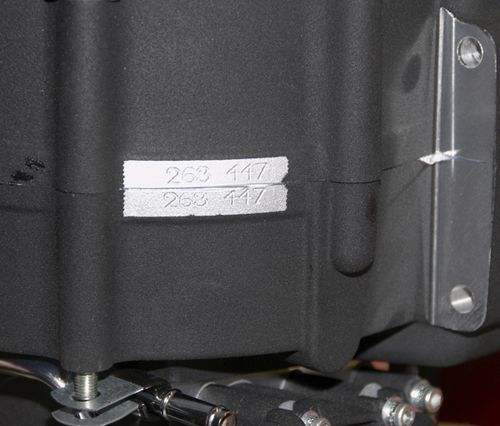
Matching Case Numbers, a must.
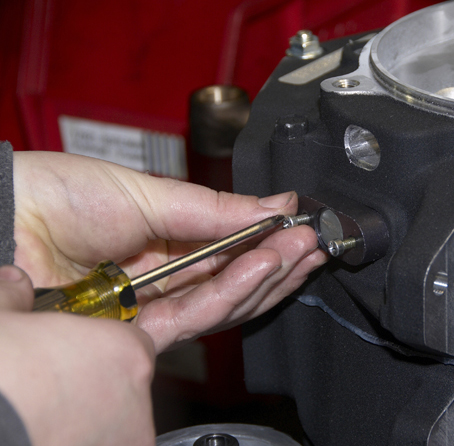
This is where the sensor housing for the fuel injected models goes. They don't return the engine with the housing, but use this for Hot testing the engine.
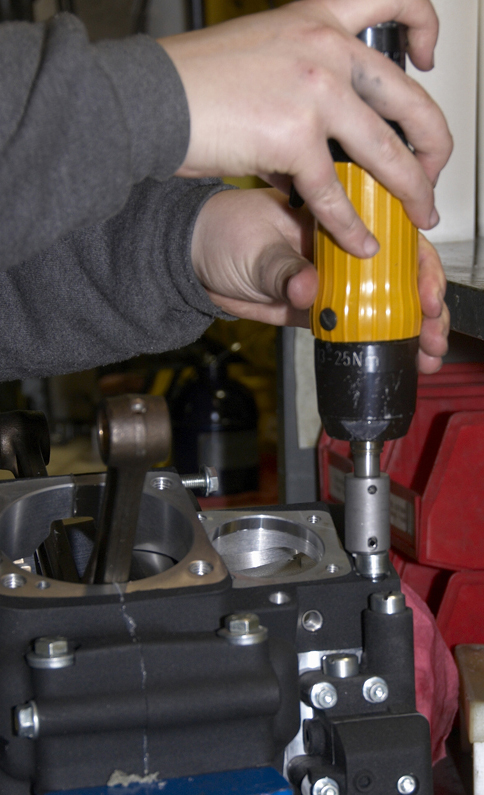
At this point Denise installed the relief valve, spring, plug and O-ring. She also installed the check valve spring, cover, O-ring and ball.
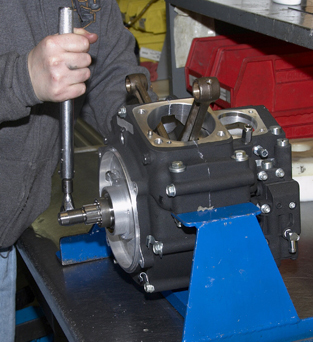
The wrench looks like it’s on the sprocket shaft, but it isn’t. She has a torque wrench on a case bolt.

Here’s where Denise says bye, bye, and the lower end rolls over to the Top End Assembly line.
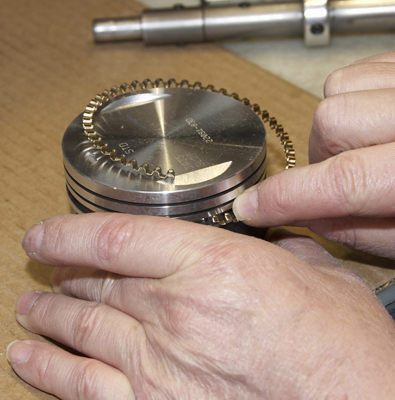
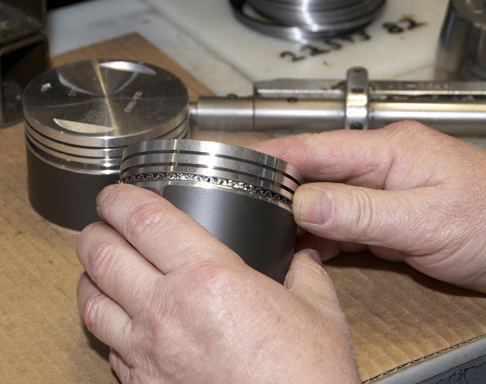
Pistons can run oversize, .010, .020 or .030. Here Mark begins the process of installing the three piece oil rings.
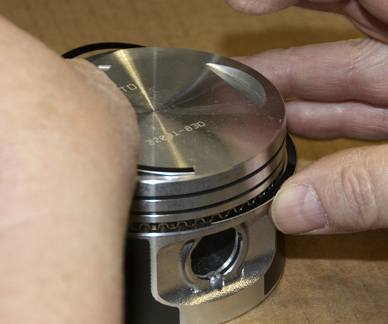
Each ring has a particular position for the ring gap to insure they don’t line up to allow oil into the combustion chamber, or compression into the crank case. This three part oil ring system keeps oil from reaching the compression chamber.
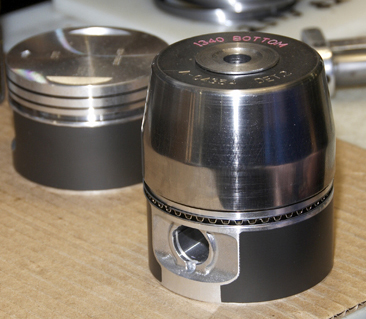
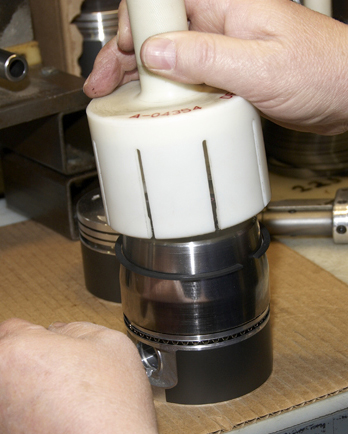
Here’s a terrific tool for installing compression rings.
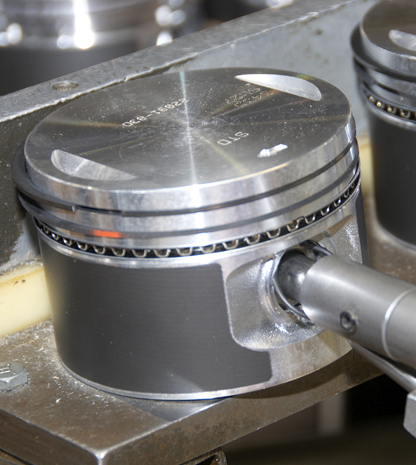
Here Mark installs one wrist pin keeper before the piston moves to the next stage.
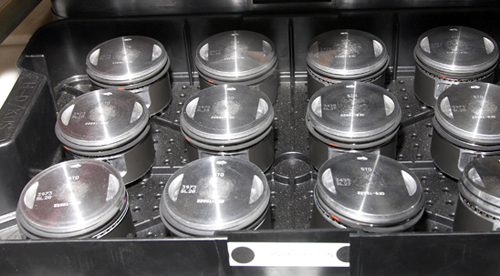
A batch of pistons ready for the road. Hang on for the next installment. We’ll move onto cam installation, then lifter stool, lifters and pistons. We’re getting there. Here's a link to the final segment: Part III, H-D Reman Process