
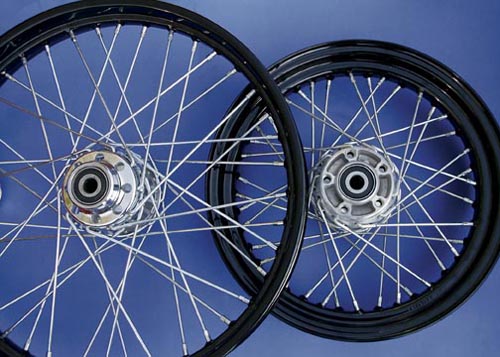
Editor’s Note: Here’s another tech from the expert tech books publishing empire of the Wolfgang. The following, Chapter 4, tech about lacing bobber powder-coated wheels came directly from the Publisher’s new book, “How To Hop Up And Customize Your Softail”. The entire book is available through Wolfgang. Just click on that banner or give ‘em a call. –Bandit
In order to make our Project Softail look more like something from the 1960s we decided to paint the rims black. Though it might seem that we could have simply scuffed the rims to knock down the shine and then spray painted them black, anyone who has tried that trick soon finds that the paint chips easily, leaving the chrome showing through. Powder coating, however, is a much more durable, tough finish. We took the rims to Kangas Enameling, where Curt Kangas started the process by cleaning them thoroughly. Though sand blasting sounds like good preparation, “It can cause the plating to lift,” explained Curt.

Power coating is the somewhat new means of coating metal objects with an extremely thick, adhesive finish sure to withstand the rigors of life on the road. The material is a polyester powder, and the “application process” has more in common with the chrome plating than it does with conventional liquid spray painting.
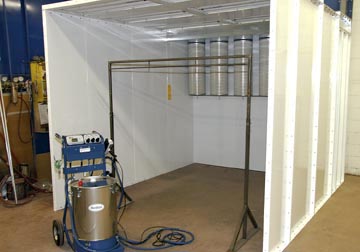
The gun puts a charge on the paint particles, which float through the air in a soft mist, attracted to the object being coated by the voltage difference between the paint and the object. There’s a ground strap on the parts shelf. Once coated, the rim or chassis parts, which are suspended on big racks, are rolled into a huge oven. The heat causes the powder to melt and bond to the metal object.Excess powder is collected at the back of the booth, which is more like a three-sided shed than a conventional paint booth. Excess powder is collected in the filters and periodically baked into a brick. Disposing of the brick is easy as it’s inert and totally non-toxic. All the hassles and risks of fresh air hoods and rubber gloves, necessary for painting with modern urethane paints, are eliminated.
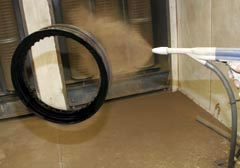
If powder coating has a downside, it’s the somewhat rough surface that it commonly leaves behind. The orange peel is acceptable for industrial parts, but not for custom motorcycle components. Over the last five year powder coating has made tremendous strides. Pearls, Candies, clears and metalflake is now available. Curt, owner of Kansas Enameling, used a special powder for our rims. “I had to special order it,” explains Curt. “The material is called Super Wet Black and it lays down really nice and retains that super glossy wet look.”
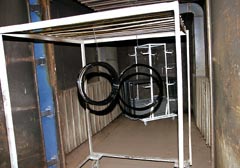
Powder coating motorcycle parts requires extra attention to detail, like knowing which powder to order for our rims, understanding how to get the powder to adhere evenly to all the nooks and crannies of a motorcycle frame, and knowing which parts of the object should be masked off with high temperature “masking tape” that will withstand the rigors of the 400 degree oven.
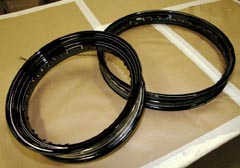
If you’re looking for someone to do powder coating of your motorcycle parts, it’s best to ask around. Each area has a shop where they understand the idiosyncrasies of coating motorcycle parts, some, like Curt, build and ride motorcycles.
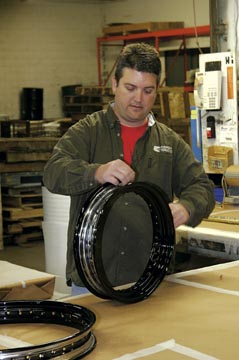
It’s critical that you work with your powder connection so they know what should be masked. Don’t take it for granted, they know. Since this finish is tough as nails, it will take hours to clean off the motormount or bearing surface, mistakenly coated. Wheel rims and hubs are especially critical. Spokes rubbing against powder will ultimately loosen and chip the paint. That’s dangerous and unsightly. An experienced coater knows to plug all the spoke holes and bearing surfaces in the rim and hub.

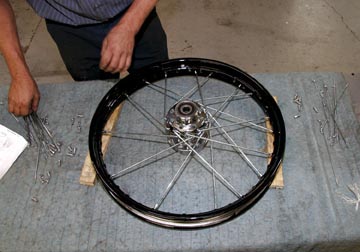
Wheel Lacing at Kokesh MC
With black powdered rims, two hubs, and two bundles of spokes we headed for Kokesh MC, located north of Minneapolis, to have them reassembled into usable wheels. Lacing a set of wheels isn’t rocket science, but it is one of those old-school arts quickly being lost in this age of billet wheels.
“Bug,” longtime Kokesh employee, started by laying out all the parts and supporting the rim on two pieces of wood. At his right Bug placed the service manual, a useful guide in setting up the initial relationship between the hub, spokes and rim. “The holes in the rim are heavily dimpled at an angle,” explained Bug. “So it would be hard to get these rims assembled one spoke off.”
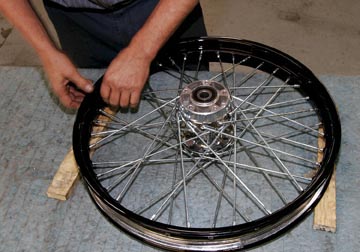
Once the spokes are in place on one side, Bug flipped the wheel and inserts the spokes on the other side of the hub. If all the spokes are in their correct locations, each will have the same amount of thread showing.
These are all new or nearly-new components and they screw together easily. “Stainless spokes often come with a tube of thread lube,” explains Bug, “and I’m careful to use the lube they recommend.”
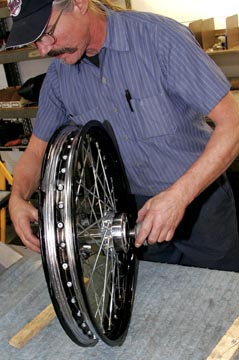
The Jig’s Up
Once all the nipples are finger tight the rim was set in the wheel truing stand, as shown. Bug identified four equally spaced groups of spokes, and will use these to adjust the rim so the side to side motion is minimal and the radial run out is close. Next, he uses an electric screwdriver to snug down all the other spokes. Now he tightens all the spokes evenly going around and around, until they are all tight.
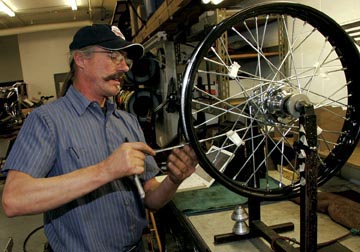
“Then I go back and do the final true,” explains Bug.For the final truing Bug makes sure the four groups of spokes have the same amount of threads showing on each one and that the offset is correct. “Each rim has a specified offset,” explains Bug. “The manual says the offset for this Standard Softail should be between 1.665 and 1.685 inches. So I measured from the hub to the edge of the rim” (note the photos).
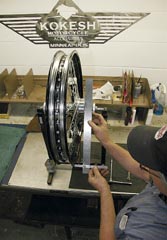
Bug measured and adjusted the offset four times, at each of the marked group of spokes. He loosens two (loosen first) and tightens the other two the same amount, to get the rim to go in the right direction. Once the offset is correct at the four locations all the spokes are tightened to the same tension, “plus one flat.”
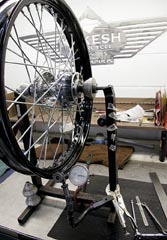
“Now I take off all but one marker,” explained Bug. “I figured everything off the one set, that will be my stop and start point. Getting the radial run-out true is harder than the side to side, but it all needs to be done together. For the final truing some people use a pointer, I use a dial indicator. Harley says .030 inch or less for both the side-to-side and radial run out. I get the side–to-side close, then the radial where it should be,” explains Bug. “Then I come back and fine tune the side to side run out. This one won’t be too tough because the rim is in good shape.”
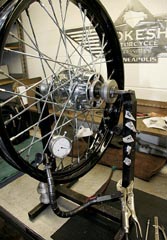
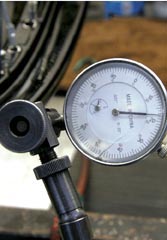
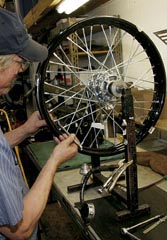
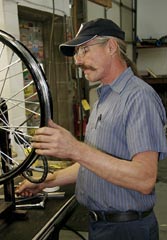
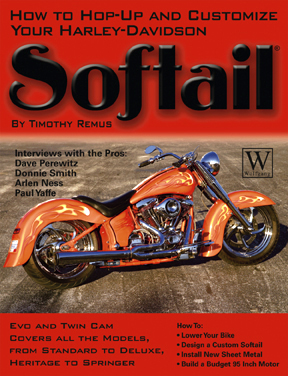
How to Hop Up and Customize your SOFTAIL
Got a Softail? Got a hankering to separate yours from all the other Softails parked outside the bar? Search no farther than this new book, How To Hop-Up and Customize Your Harley-Davidson Softail, from well-known author Timothy Remus. Whether your goal is to personalize that two-wheeled ride or give it more than 60 horsepower, the ideas and answers you need are right here.
Learn how to install a 95 inch kit with over 100 horsepower, add a 250 rear tire, lower the bike, and add extended fuel tanks. Included are customizing ideas, start to finish photo sequences of engine, chassis and paint work, and a list of suppliers for lights, engine hop-up parts, paint and chrome accessories.
The various Softail models are among the most popular bikes ever built in Milwaukee. Make yours faster, sexier and more personal with this all-color book from Timothy Remus and Wolfgang Publications.
Printed in color, this 144 page book is available for $24.95 + $5.50 S+H (in the US) from Wolfgang Publications. Order by mail at: Wolfgang Publications, 217 Second Street North, Stillwater, MN 55082; By phone at our 24 hour order line: 651 275 9411, or on the web at: wolfpub.com.
–Jacki Mitchell
Wolfgang Publications
217 Second Street North
Stillwater, MN 55082
651.275.9394
Fax: 651.275.9330
24 hr. order line: 651.275.9411
http://www.wolfpub.com
