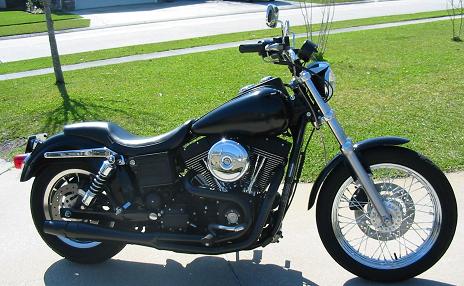
Editor's Note: The Following is a special tech piece by our great friend and fellow Bikernet contributor Anson “Knucklehead” Alexander. You may have read about his 95” upgrade on his bagger a few months back. Well, it seems some guys just aren’t happy having just one bike to tinker with and build for a national audience to critique, they want it all. Here’s the initial recording of what looks to be many tech’s by our readers. Instead of trying to decipher all the words and make them my own, I have decided to leave the article the way Anson submitted it. I think he did a fine job and encourage each of you reading this to follow suit with any tech articles you would like to submit. If anyone is interested, contact the big guy, Bandit.
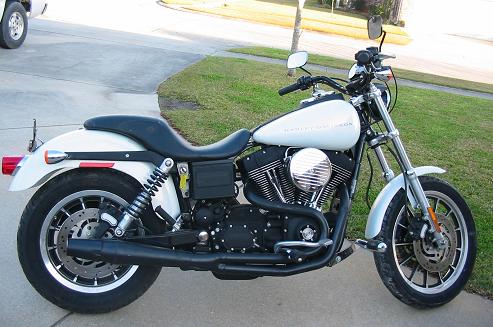
The original wrecked white 2002 FXDX. What doesn't show is that the fork trees are broken, twisted front end, questionable front wheel, broken speedo indicating 45 mph, the left front of the tank was badly dented, ruined fenders, seat and all left side trim parts were toast. The bike had been laid down at speed on it's left side. I found dirt and mud packed into the frame and electrical area.
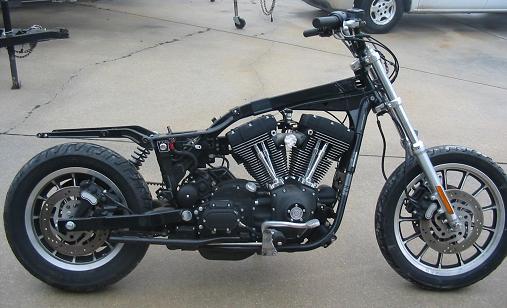
The FXDX suspension including the rear shocks was sold off. Then the bike starts getting back together. Suspension replaced with a FXDL setup. Used Thunderheader. Finally finished with bondoed tank, replacement misc parts and a $40 paint job. The engine, electronics, drivetrain and frame were all good. Original bike price $8500, parts sold off $700, parts replaced $1200, upcoming TC 95″ upgrade $500 = $9500.
I also attached a couple photos of the bike with the engine teardown. And a piston comparison.
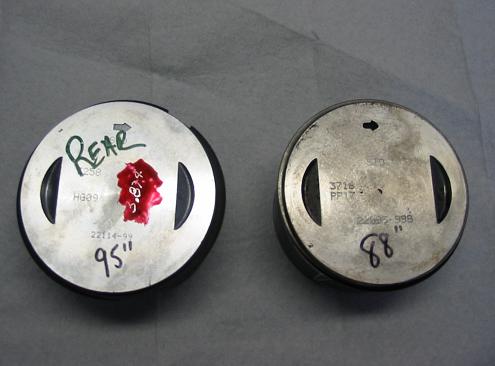
The 203 cams are installed and the heads cleaned up. After waiting on a set of mail order Crane pushrods and Cometic .030 gasket set, it turned into wrenching time.
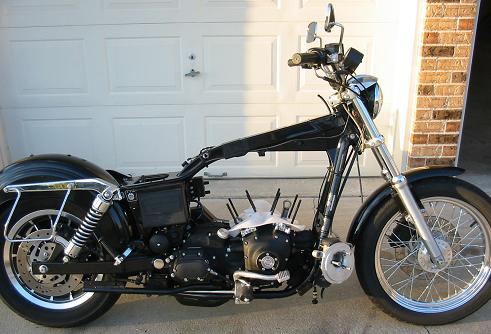
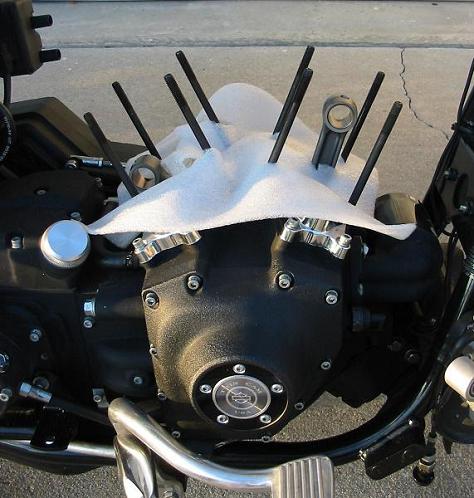
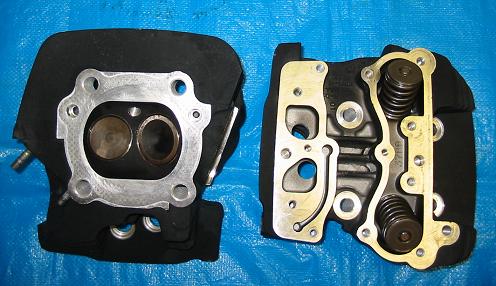
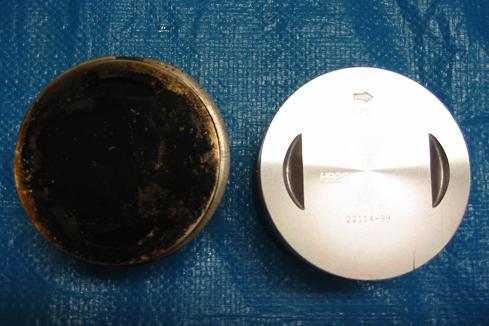
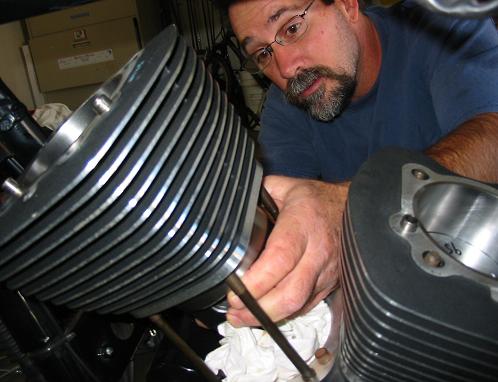
Performance for a Tight Fisted Bastard! See if you can follow along.
The engine is a 2002 Twin Cam 88. The performance upgrades initially installed were a modified CV carb and used Thunderheader. The carb modification centered around Joe Minton's advice:
“Install the 1988 XL 1200 needle P/N 27094-88.
Drill out the plug to access the idle mixture adjustment.
The main and low jet remains stock.
Adjust the idle mixture for the air filter kit installed. (I like the Ness Big Sucker kit)
The XL 1200 needle has a full taper design. The stock needle does not. The XL needle allows for better fuel mixture and throttle response.
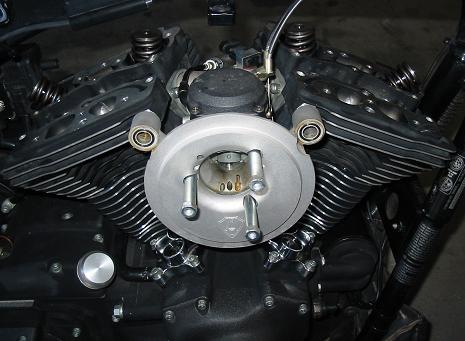
I have used these two simple modifications since my first Evo, in 1989, to cure the factory cough at low speed and improve overall carb performance.
I recently installed a set of used Screaming Eagle 203 cams along with the Torrington B-148 inner cam bearings. I rode the bike briefly and then found a SE 95-inch upgrade kit for sale.
The kit included the 1550 flat top pistons, top end gaskets and heavier clutch springs. In addition I purchased a Cometic MLS .030 head gasket kit P/N C9721. This kit optimizes the fuel mixture burn in the stock Harley head chamber on the engine's combustion stroke.
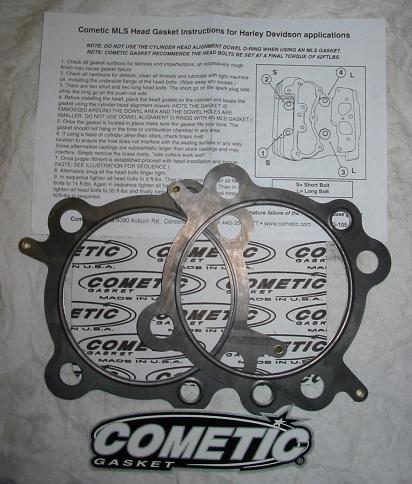
I tore the engine down and shipped the cylinders out with the pistons and SE directions to the machine shop for bore and hone.
It is important to use a shop familiar with the procedure and the use of torque plates while machining.
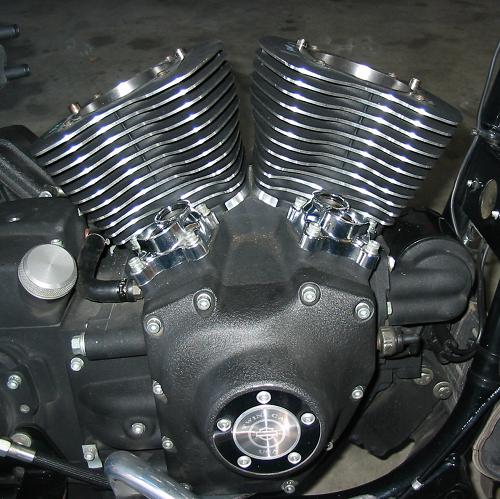
During my internet search for shops that handle this work, I found a variety of methods used for this process. I went with a shop that utilized a boring bar and honing machine coupled with a reputation for quality work. As the machining process was out of my hands I wanted the best for my project. I discussed my project with the machinist and was reassured that my project was in good hands.
While the cylinders were being machined I disassembled the heads, removed the carbon buildup, lapped the valves, installed new valve seals and reassembled.
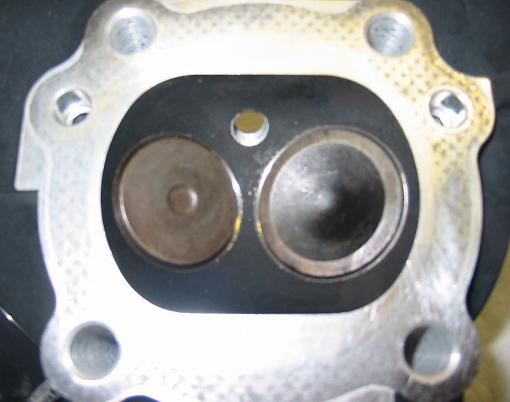
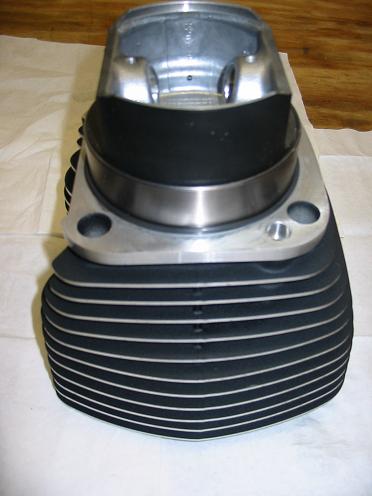
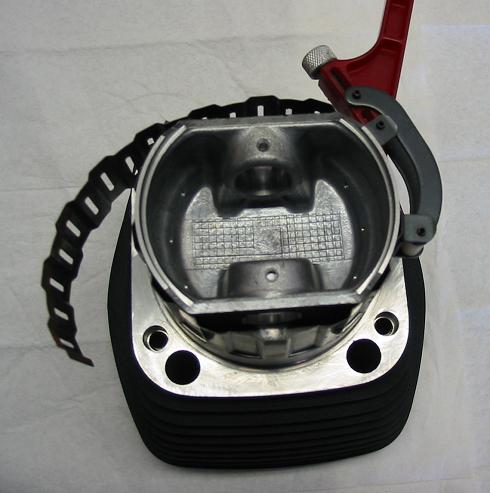
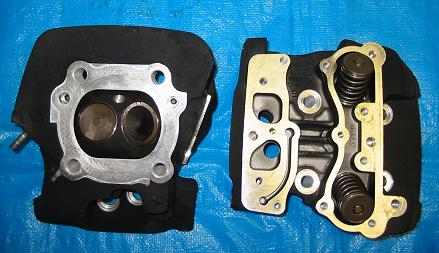
During any engine work it is recommended to disconnect the battery cables to prevent accidental engine turn-over.
I filled the engine cases with clean shop rags to prevent my dropping anything into them. I cleaned the shop bench and floor before assembly as well.
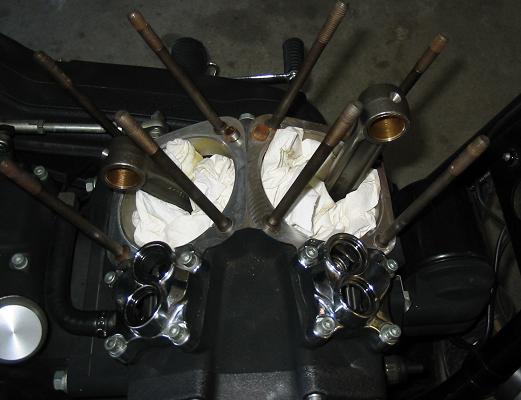
I use the “tag and bag” method during any involved mechanical work. During the dismantling process I put the various parts and hardware in plastic bags and mark what each is. I also write notes on the bags as to how many fasteners should be inside and anything else that is informative. I use a digital camera to take photos of the process showing how the parts are assembled. These extra steps take the guesswork out of the following assembly as I am not a full time mechanic doing this on a daily basis. When I visit the local dealer for replacement parts, I bring the “tag and bags” along. It allows for the parts person to see the actual parts and not have to look at the computer parts drawing attempting to figure out what I am talking about.
The build began with the washing the cylinders. I did this in the kitchen sink using dishwashing detergent. I then dried them thoroughly and wiped them with a light machine oil. The machine shop had fitted the pistons with the rings installed.
The cylinders and pistons were then marked as to “front” and “rear”.
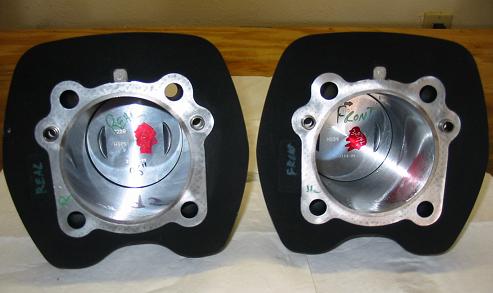
Using an inexpensive piston ring compressor tool I installed the pistons in the cylinders orientating the ring gaps according to the SE directions. The two o-rings on the primary side engine case corners were installed.
The cylinder base o-rings were also installed.

Then the cylinder with the piston was placed over the connecting rod.
The piston was tapped down until it was possible to push the piston wrist pin through the connecting rod and the wrist pin circlips installed. Care was taken to prevent the clips from falling into the engine cases and all parts were lubricated for ease of installation. I prefer this method to installing the piston on the connecting rod and then installing the cylinder over it.
After both cylinders were installed a light coat of HD motor oil was wiped on the inner walls of each cylinder. The Cometic head gaskets were put in place and the cylinder heads were installed per the Cometic directions.
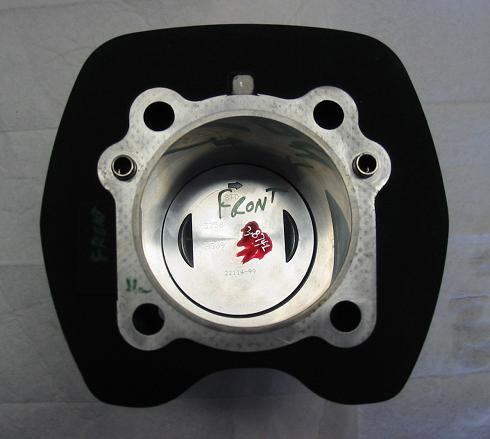
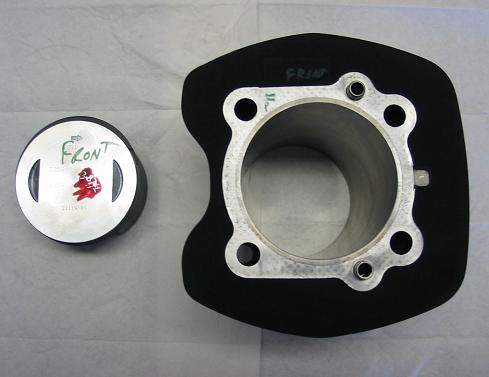
The Harley cylinder heads are marked “Front” and “Rear” to keep assembly straight. The cylinder head bolts were lubed with machine oil. The underside of the head bolt flats were also lubed. This is to minimize friction effects while torqueing the head bolts.I have two Snap-On torque wrenches: one is for ft-lbs and one for inch-lbs. These wrenches enable me to follow the recommended torquing procedure stated in the H-D manual.
In the event I can not reach a fastener with the torque wrench I am able to reference my “hand feel” to a like-torqued fastener. It may not be a 100 percent proper technique, but it is lot better than guessing the entire process. So far, in 30 years of wrenching, it hasn't let me down.
Before going on to the rocker covers I fitted the CV carb manifold while there was plenty of room to install it. I followed with installing the rocker plates. It's sometimes good to align the intack manifold before torquing the heads.
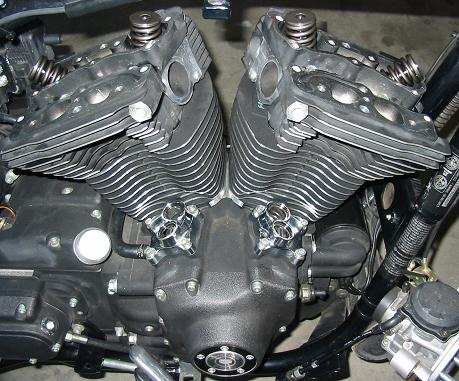
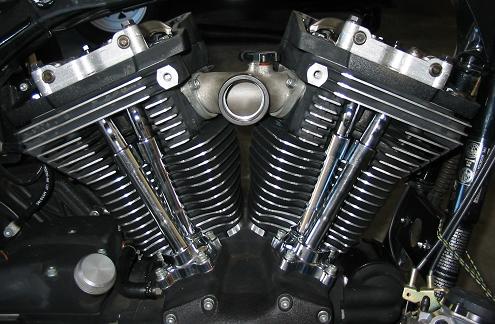
The front and rear heads have a different passageway orientation. The rocker plate gaskets must be installed covering this passageway.
The pushrods and pushrod covers with new o-rings were installed. Each pushrod takes three different o-rings. The pushrod cover must be dismantled to change one of the o-rings.
I used CRANE chrome-moly adjustable pushrods. The pushrods feature small diameter for minimal pushrod cover interference and are easily adjustable with two 3/8″ wrenches.
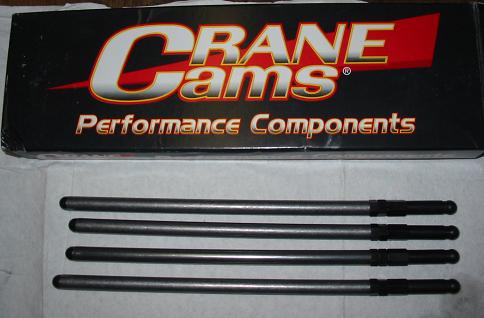
The rear cylinder required that I place the rocker plate and rocker assembly in together due to frame top tube interference. The front and rear rocker plate bolts were treated to light coat of LOCTITE BLUE and torqued down.
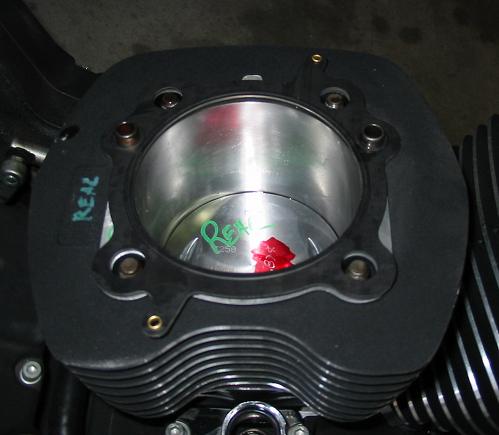
A new rocker plate o-ring and oil breather filter were installed. My 2002 TC engine has the plastic breather assembly. Later models have an aluminum assembly that allows for the changing of the umbrella valve and require additional gaskets. At this point the all bolts were checked for final torque values.
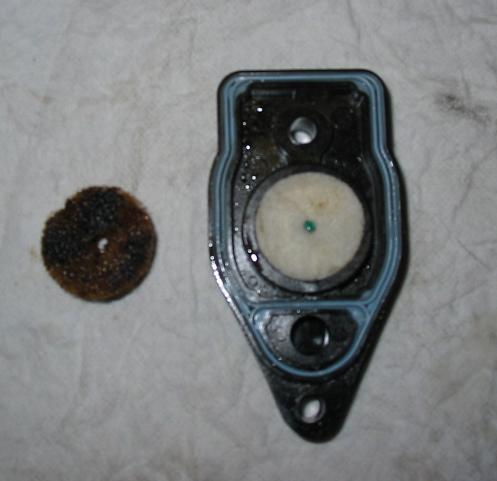
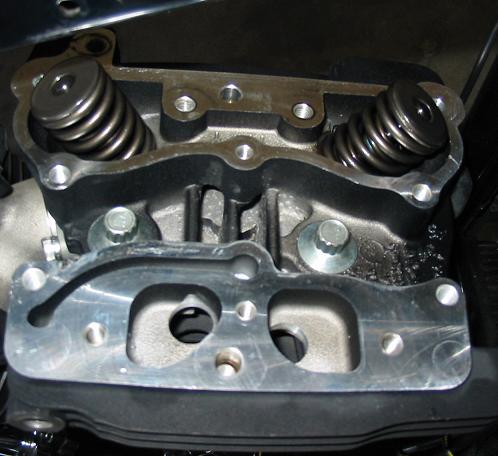
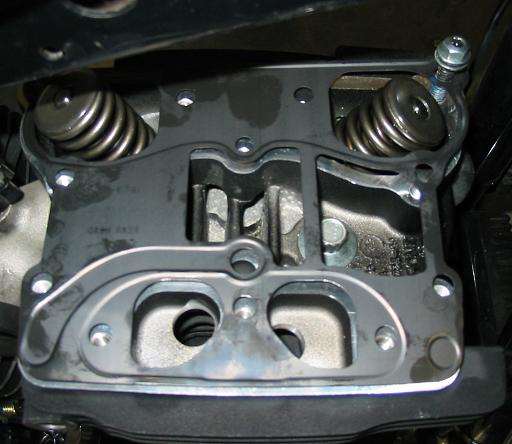
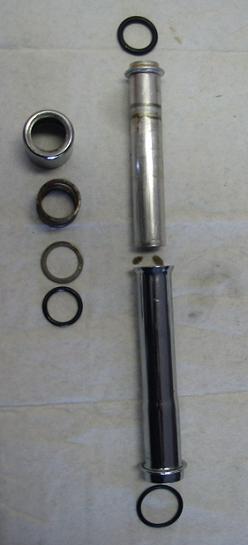
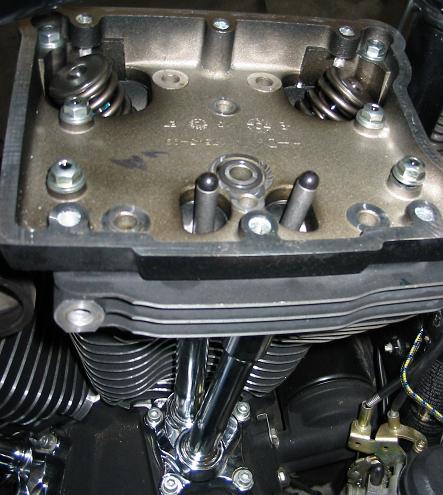
I lifted the bike with a small floor jack and shifted into third gear. Rotating the rear, I was able to see the actual rocker vs. pushrod movement allowing for accurate and easy pushrod adjustment. I allowed for 10-15 minutes lifter bleed off time between adjustments of the pushrods.
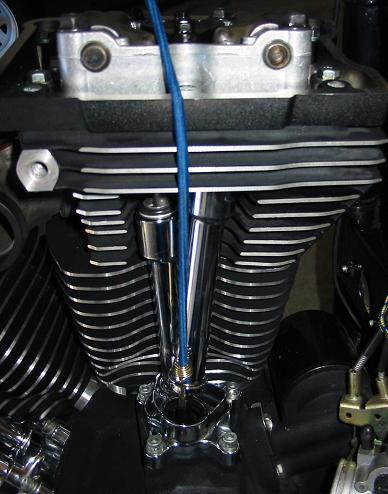
Crane recommends three turns out and then setting the lock nut.
I use a drop of LOCTITE BLUE on the pushrod threads to secure the lock nut.
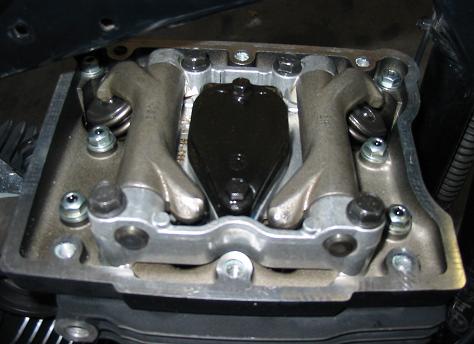
With the cylinders, pistons, pushrods and rockers in place I then reconnected the battery. I spun the engine over to check for operation and pushrod binding.
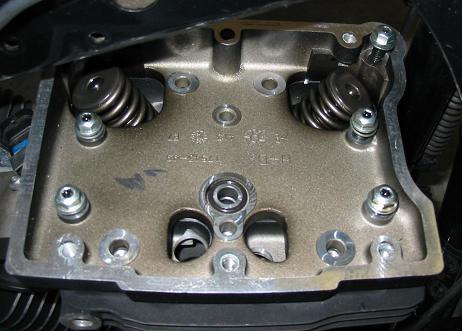
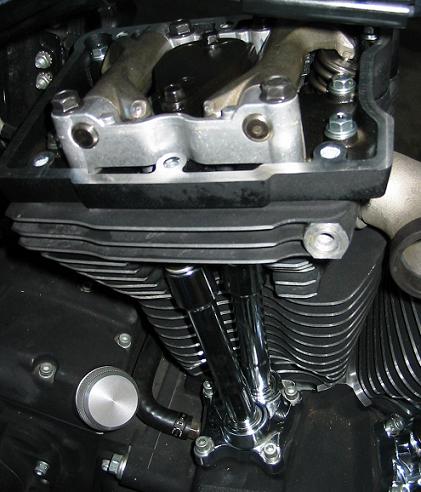
With everything looking good I proceeded to install the rocker covers, upper motor mount, CV carb, exhaust and gas tank.Afterward I spun the engine over and checked for any problem prior to installing a set of spark plugs and filling the gas tank. Then it was “FIRE UP” time.
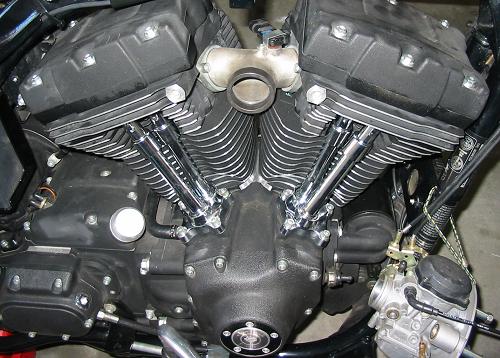
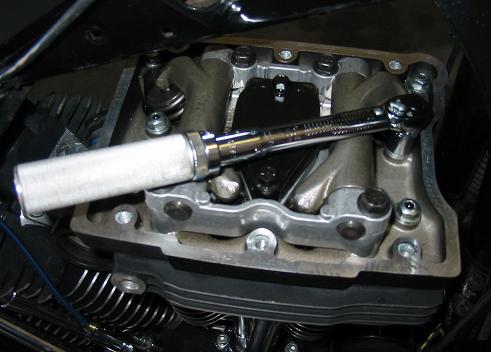
The engine caught on the second attempt after the initial pushrod clatter settled down to a nice even idle. A couple easy passes up and down the street confirmed that everything was running as it should.
The remaining tasks are to make a few passes at speeds of 60-70 mph, allowing the engine to coast down in between. This will seat the piston rings to the cylinders. After that, nothing else to do but “RIDE IT”!
Cost sheet:
$140 – Cylinder bore and hone
$115 – SE 1550 flat top piston and gasket kit
$ 75 – Crane pushrod kits
$ 45 – Cometic .030 MLS head gasketsulnone $375
Total 1550cc kit install
$100 – CV Carb mod w/ Ness kit
$125 – SE 203 used cams
$150 – Thunderheader used
$ 25 – Torrington inner cam bearingsulnone
$400 – Cam, carb and exhaustpar
Ride Safe! Ride Fast! – Happy Holidays 2006!
Anson “Knucklehead” Alexander
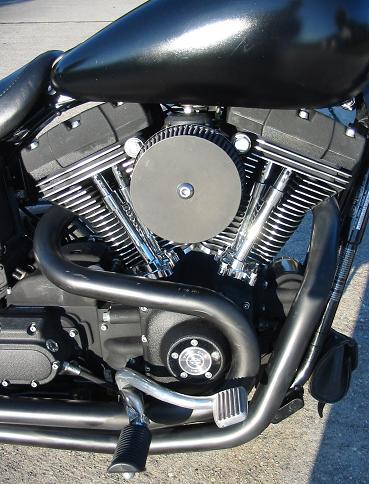
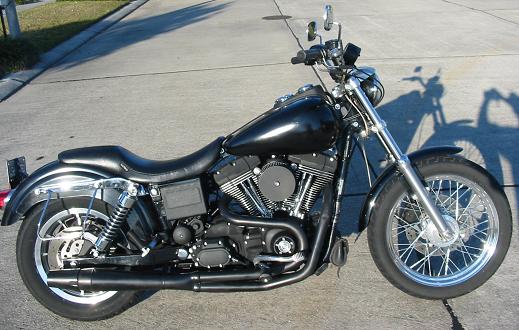
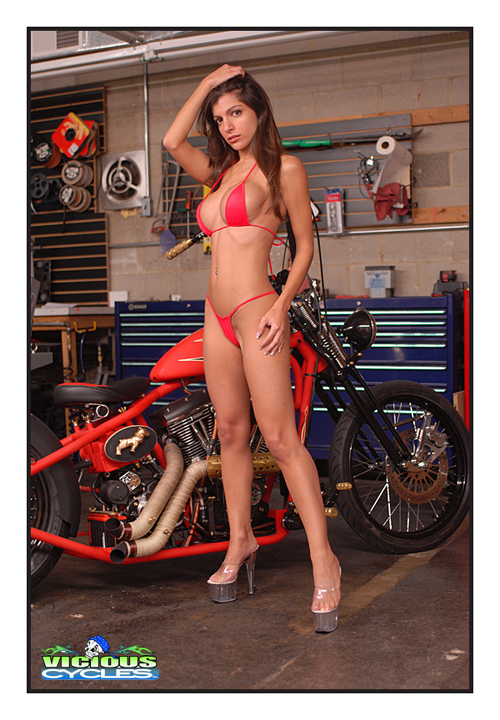