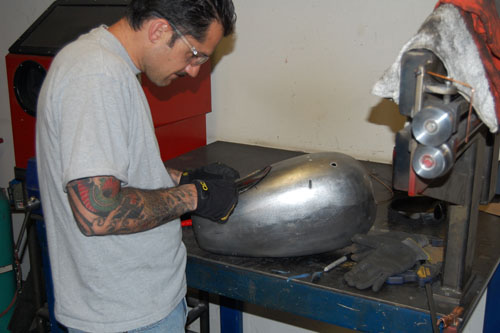
I know it’s been a while, but shit it’s the season and I’m busy as hell and would rather work on getting this beast done than write about it. Last time around we got the axle blocks cut, drag brace in, and everything welded. I’m not sure if I’ve said this before, but Ryan is a badass TIG welder. It’s fun to watch someone with that level of talent focus, and make shit happen. His typical response to whatever insane idea I come up with is, “Sure we can do that.” He's good at pretending I have something significant to do with this build, other than being an extra set of hands or a pain in the ass.
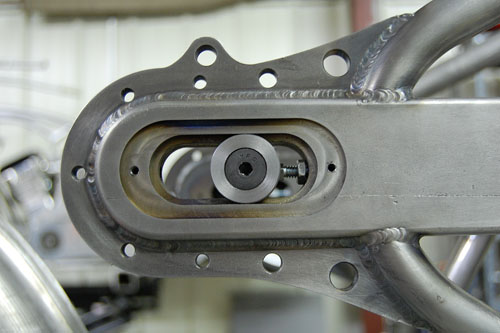
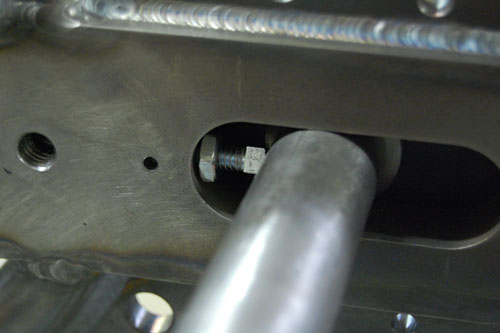
Ryan got to work on the hidden axle block covers, axle and hidden axle adjusters. They look so trick that every time I see them I think, “Shit, this bike is gonna be bad!” The frame was done, so it was time to move on to the tank. Tanks are a funny thing. They become all consuming and boring to some, and others can’t get enough of them.
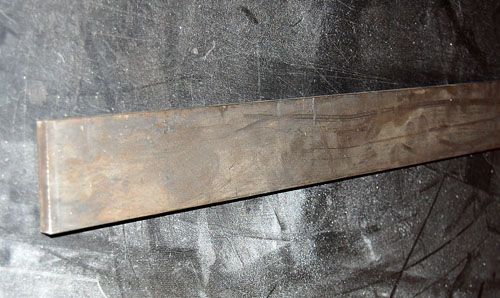
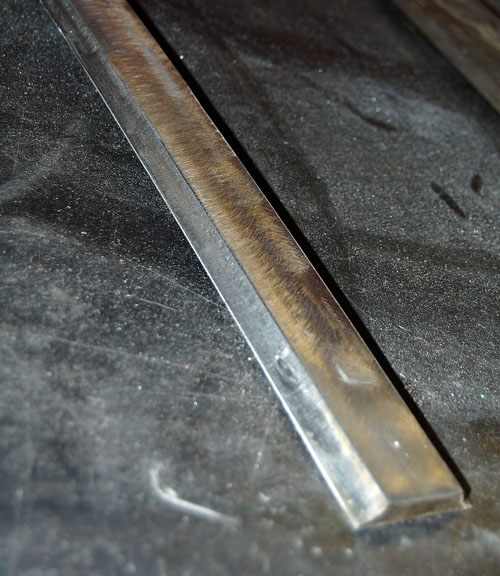
We had the bottom and the hidden tank mounts tack welded. I really wanted an accent piece on the top that matched the rear flattop fender, I ordered from Pat at Led Sled. It was going to be a ridge, and Ryan and I discussed trying to fab it out of sheet metal. Then common sense got a hold of Ryan, and he decided to cut it out of a solid bar stock on his CNC mill. The finished product was precision and better than I envisioned.
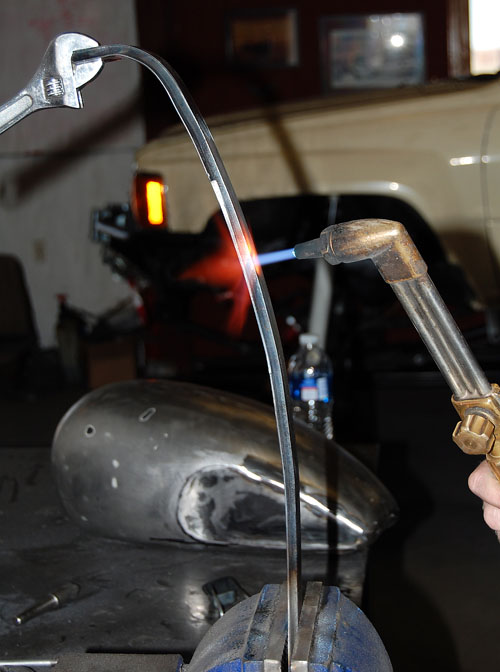
The ridge needed a gentle arc to match the contour of the tank, so how hard could that be? Turns out–very hard. We heated and hammered, bent and unbent. It sucked, but in the end the finished product was dead nuts center and will look killer and unique. Ryan did a great job welding the ridge to the tank. We celebrated the finished product with a CAO cigar, and man they are good. There’s nothing better than bullshitting in a shop and smoking a quality cigar.
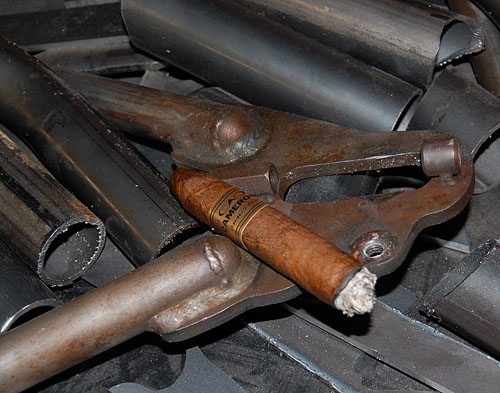
One of the design elements that comes to mind, when I think of a racy bike is the tank side panels – a rider should be able to tuck his knees in to grab a racer's position. Triumph had that nailed for decades, so we dished the sides of the tank.
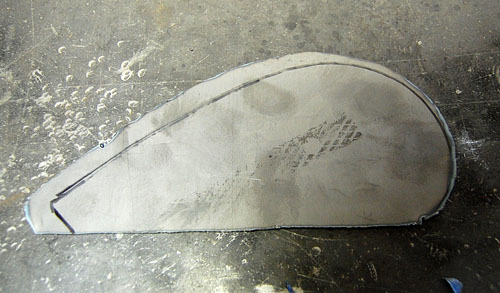
I never realized how many options there are for dishing a tank. I thought you cut ‘em, turned ‘em inside out, welded in the panels and called it good. Not so. We needed to decide how to make it look. Should there be a lip at the bottom or should it run straight off? After lots of discussion we taped it, cut through the first side with a plasma cutter and ground off the slag, so it wouldn't hinder quality welding.
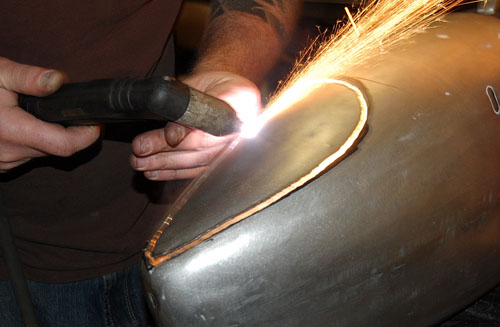
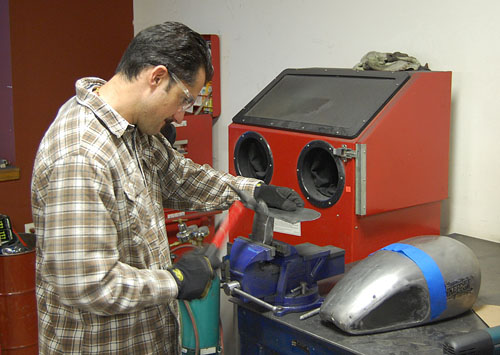

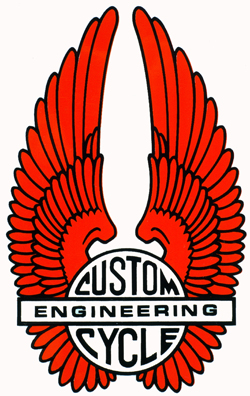
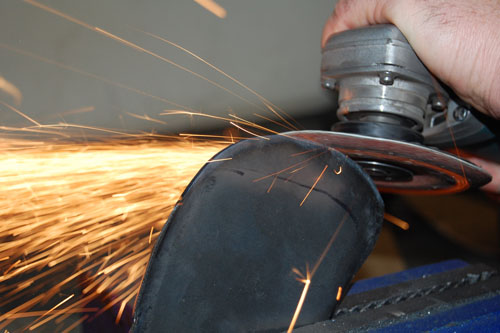
We cut 16-gauge sheet metal in a size similar to the hole and started pounding. Ryan did most of the work but gave me the opportunity to use the hammer and dolly. He taught me that the sound and feel of what you are working on is the most important way to tell if you are actually making progress. We hammered, bent, fit and ground all night until it looked just right. Then came the hard part – trying to duplicate it on the other side.
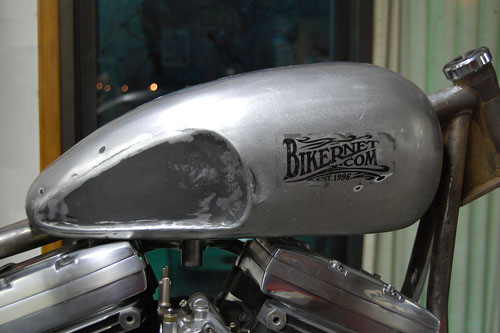
I’m very happy with the results. It looked just as I thought it would, only better. We discussed a filler cap, which Ryan is going to machine, and petcock position. He turned a bung for the petcock and then decided it was time to seal up the tank. He is very precise about his welding, so he takes his time. The first pass result was very clean and should hold up well, but he’ll incorporate a finish pass anyway.
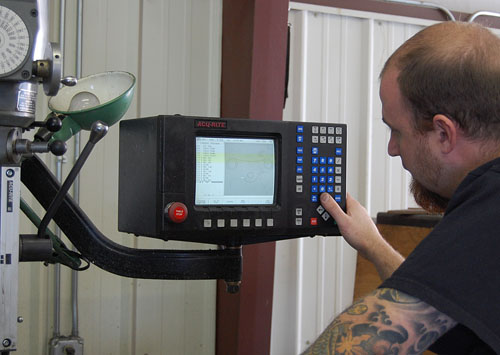
I had an idea for some triple trees. I wanted to run a super narrow, 35mm dual disc front end but hate the stock trees. I picked up a unit that had the lowers I needed. The trees looked like something made in a garage in the '70s with a sawzall, and they weighed a ton. I looked to Rick at Custom Cycle Engineering for some guidance as to what length tubes I would need. They are tapered at the top, making them a bit tricky, but hopefully we came up with the best length available.
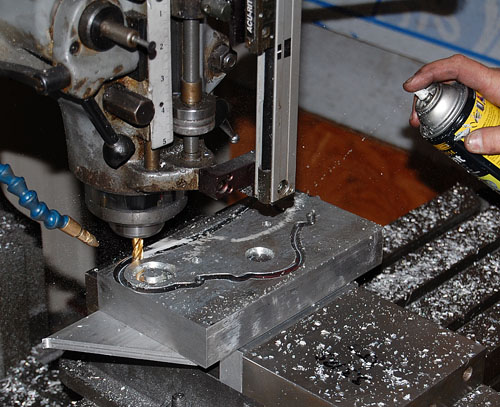
I showed Ryan some trick Buell trees I liked from Europe, and we modified the design heavily. We designed some pinch bolts into it to add that racy look. Ryan input everything into his Bridgeport CNC and, voila, they were done. Well, not quite … it took several hours, bit changes, etc. He added some killer extras to the tree design, like the bosses for the tubes extend and the holes in the trees are machined just right. The two solid plates of aluminum weighed just a few pounds, and they are totally unique. Ryan is thinking about having a few on hand and doing some custom orders if people really like these.
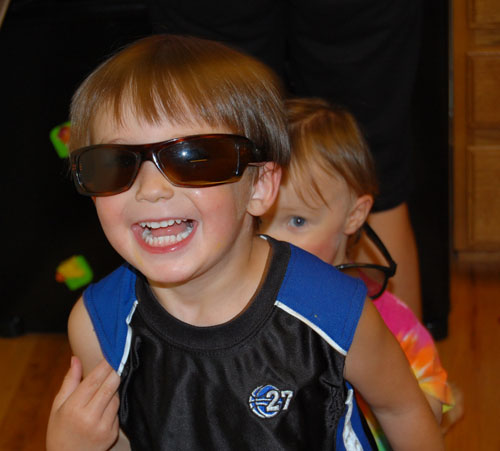
Ryan and I were graced with Tattoo John’s presence last week, and he gave his slippery nod of approval. He just got a sick new ride, a custom Roadglide that he promptly spray-bombed flat brown and black. He is taking it on a 48 state tour this summer, so watch out lower 48.
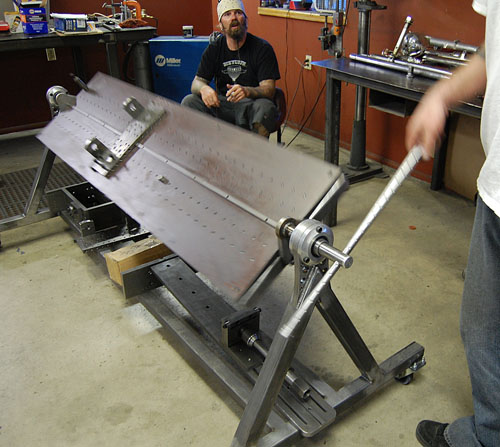
While John was on hand, Ryan pulled out his latest creation – a spinning dolly for his frame jig. It’s a piece of art, and lots of time was spent on every little detail. He still has a mini-bike brake to throw on it, but otherwise it’s good to go. He doesn’t go halfway on anything.
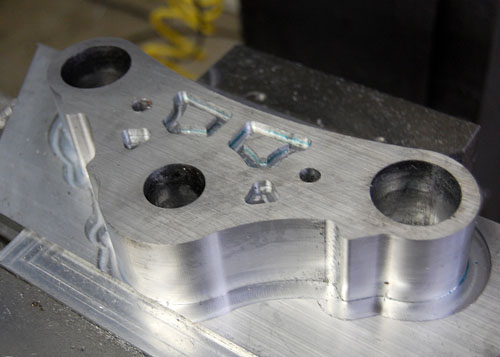
We’re getting close and will hopefully see a full mock-up by the end of June. SPS is sending me a set of billet spoke wheels and matching rotors. Then all that’s left is little stuff like the battery box, oil tank mounts, fender mounts and mid controls. All fun stuff! Remember, you can see more of Ryan’s work at www.myspace.com/rbfabrication.
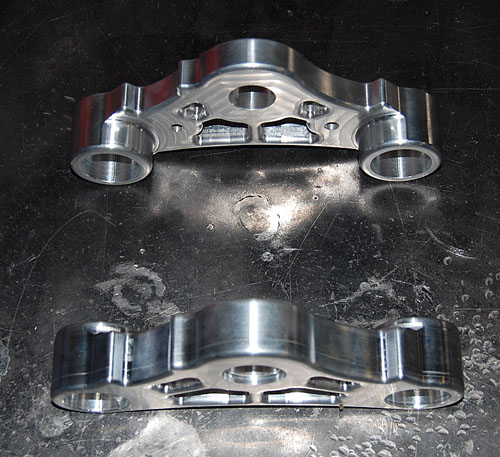
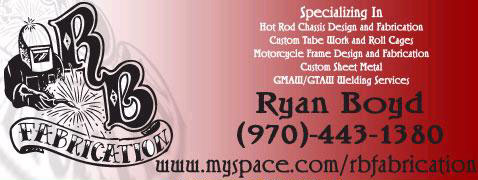