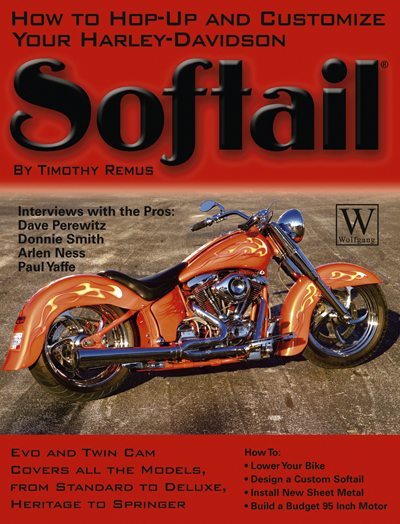
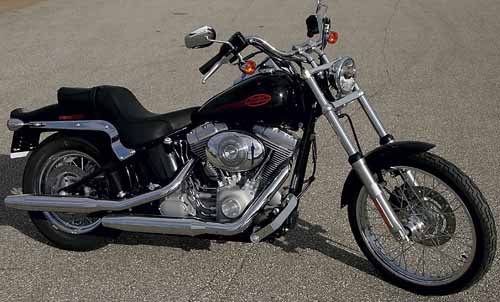
Making a Bobber out of a late model Softail seemed the ideal project for the Softail book. After all, Bobbers are popular right now and all we had to do was install a new short rear fender, throw away the front fender, install a solo seat and get rid of the factory dash (maybe). We started the mock up with a 2002 Night Train, though the Night Train would be replaced later by a Softail Standard.
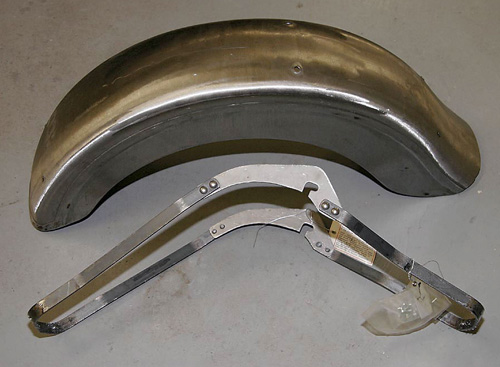
What you see here is the first planning and mock up session. And we can’t emphasize enough the importance of the mock up for any kind of customizing project. As explained, the Night Train was replaced with a Standard, but both are late-model bikes and the chassis and swingarm are the same so it really isn’t a big deal. Just follow along as we try to decide which fender best fits our “keep it simple” Bobber project.
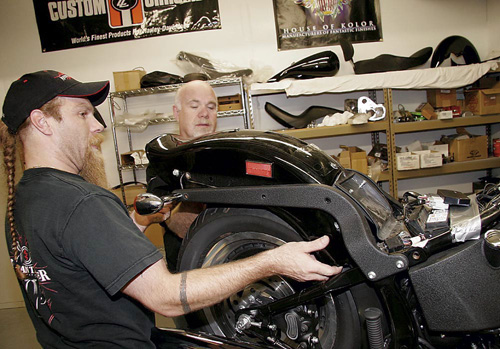
Disassembly
The disassembly is straightforward, the only real trick is to disconnect the wiring, which must be done before the fender and rails can be removed. Most late model Harleys route the rear turn signal wires into the taillight housing. This makes more sense if you take off the taillight lens and scrutinize the way the wires from the blinkers are routed up into the housing and then turn and plug into the light-base.
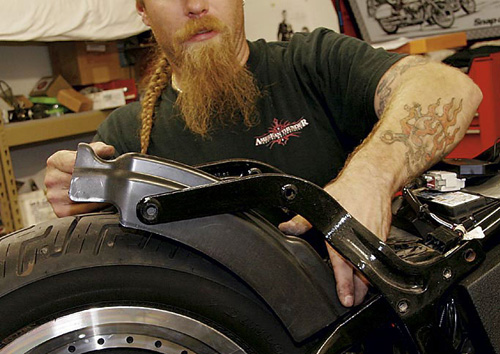
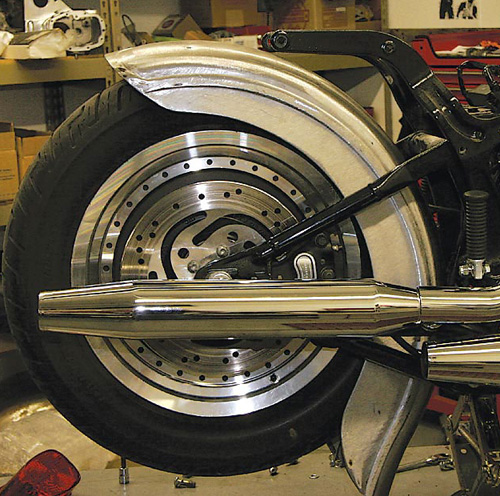
Once we had the bike apart, Neil and Ken tried three different fenders before finding one that seemed to hold promise. We tried a late model front Dresser fender, a round fender blank, and a re-pop of an early Springer fender meant for 1937 to 1948 models. I was trying for a late-Bobber/early Chopper look and the front Springer fender, stripped of its supporting brackets and turned around, seemed the best fit, both literally and aesthetically.
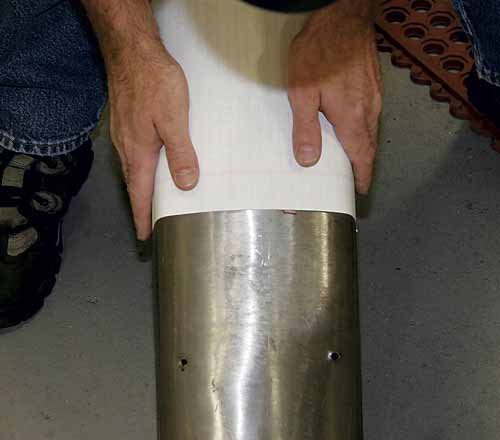
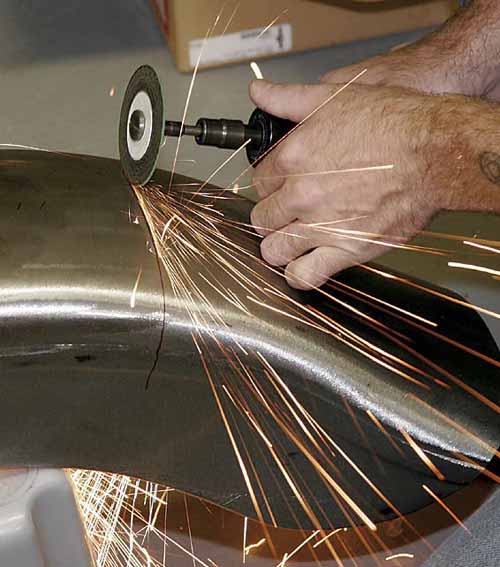
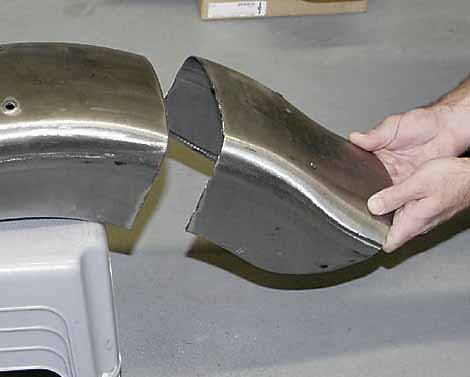
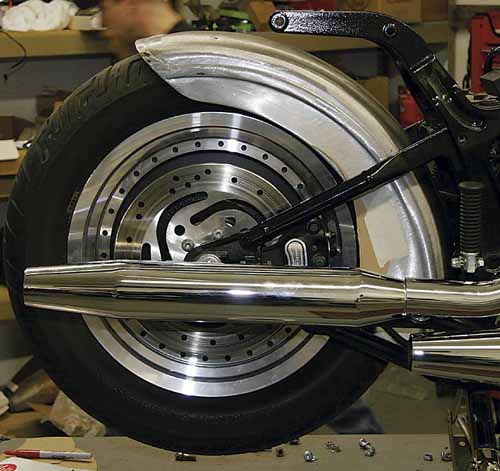
The photos tell the story of our little planning or mock-up session better than words. In the end we had to cut the bottom off the fender, then do a pie cut to ensure the fender would follow the radius of the wheel.
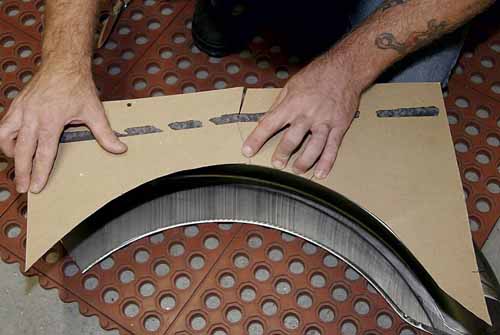

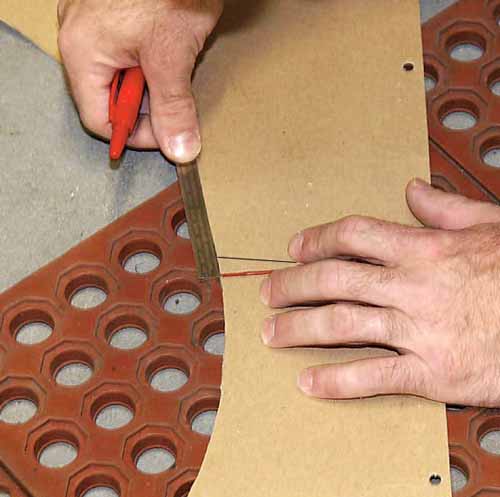
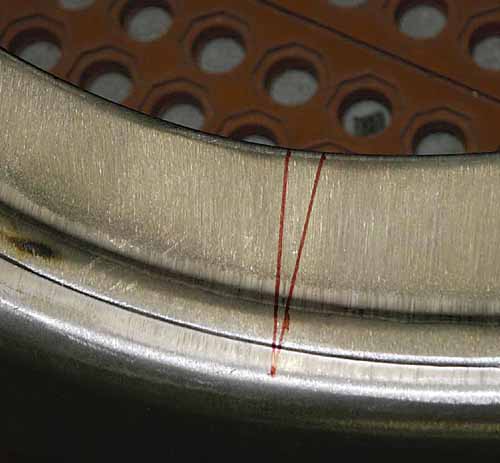
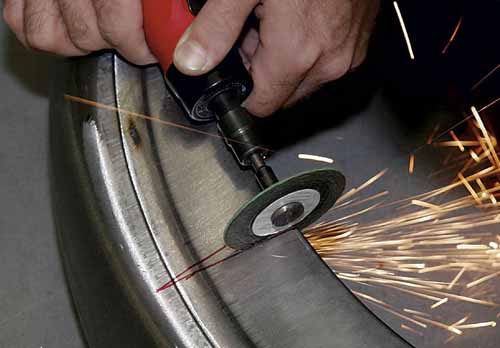
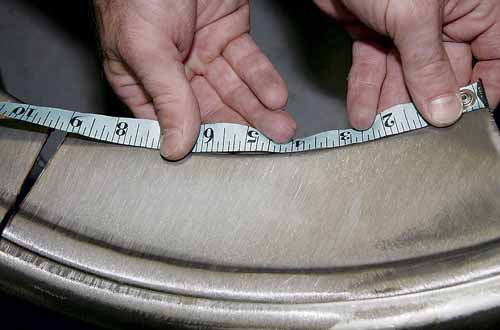
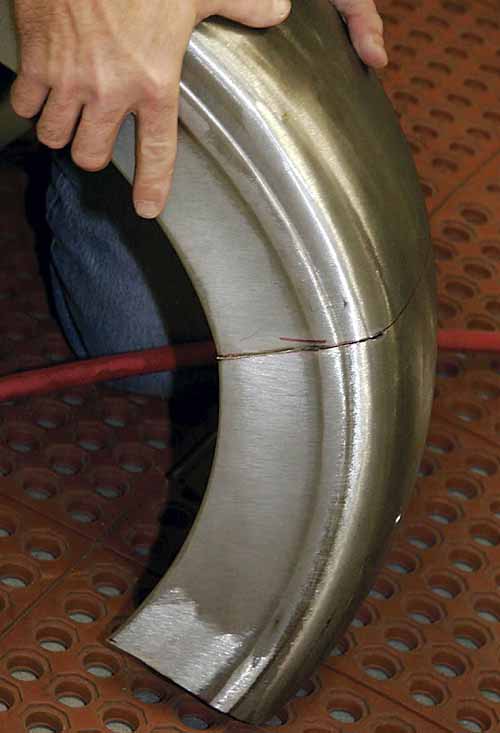
FENDER
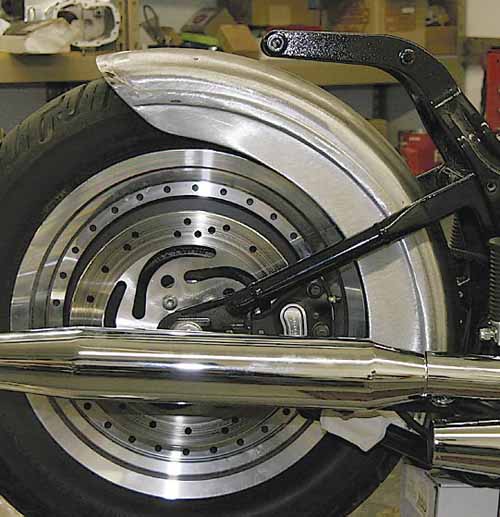
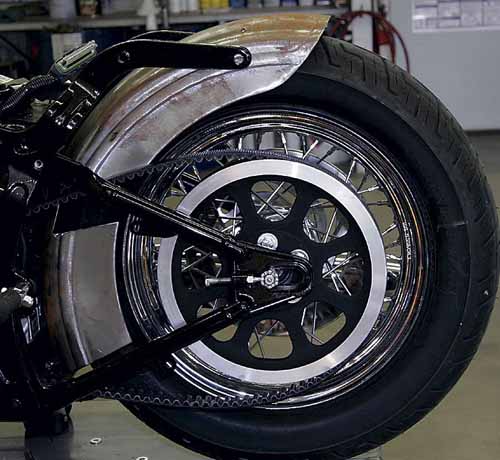
Our Softail Project, last seen at American Thunder, made its way to the Dougz shop in La Crosse, Wisconsin. That is, the fender and a brand new 2005 Softail Standard, made their way to Dougz. And as the photos show, the project started up again about where it left off at American Thunder.
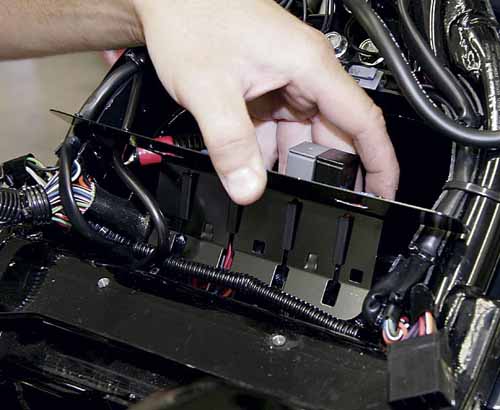
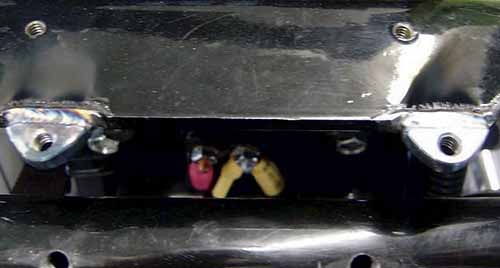
First Doug and Terry had to strip off all the stock sheet metal and then get a feel for the new fender, how would it fit and mount to the swingarm. As the swingarms themselves are all the same between the 2002 Night Train and the 2005 Standard, there were no major hiccups in the initial part of the project at Dougz.
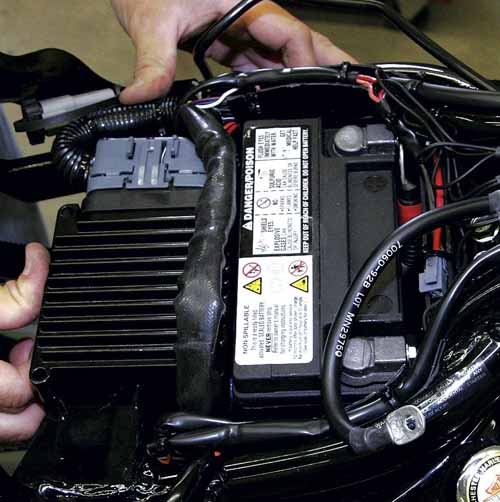
Possibly the hardest part of this whole project was deciding what to do with the ignition module. Unlike an Evo, which can be converted to a system contained entirely under the points cover, the Twin Cam engines use a large box that houses the brains for the ignition system. Normally this box resides in a concave fender insert under the seat. As our Bobber would use a fender mounted to the swingarm and placed farther back than a stock fender, there was no way to mount the module to the new fender.
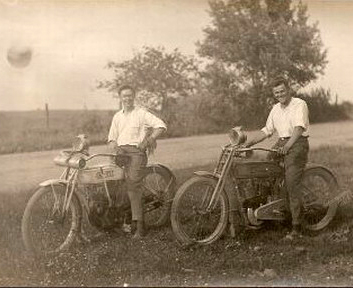

The harness going into the module looks like the main harness for the Space Shuttle, or a least the main harness for a Cadillac. There are a lot of wires, cutting them in order to splice in longer wires and thus make it easy to move the module didn’t seem like a good idea. After considering all our options Doug suggested mounting the module on the cross-bar just behind the battery as shown in the photos.
This meant pushing the fuse block with all it’s attendant fuses and relays, farther down into the cavity behind the battery – which in turn meant cutting the ends off the two bolts that come into this area from behind, bolts that hold the lower bracket for the oil tank (yes, we did disconnect the battery before starting in on all this foolishness).
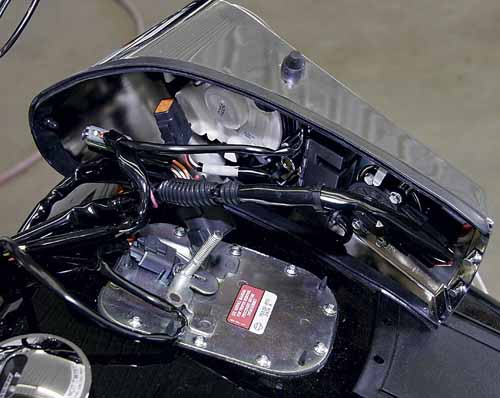
Gas Tank
Once we have a home for the module, Doug took the gas tank off, which meant disconnecting the line at the bottom of our fuel injected bike. This was done by sliding the collar on the fitting up and then pulling the line off the fitting. The cross-over tube came off too, after siphoning most of the fuel out of the tank. There’s also a vent line at the front of the tank. The speedo and ignition switch wires simply disconnect from the fuel pump base on the bottom of the dash, after the dash was unbolted and tipped up off the tank.
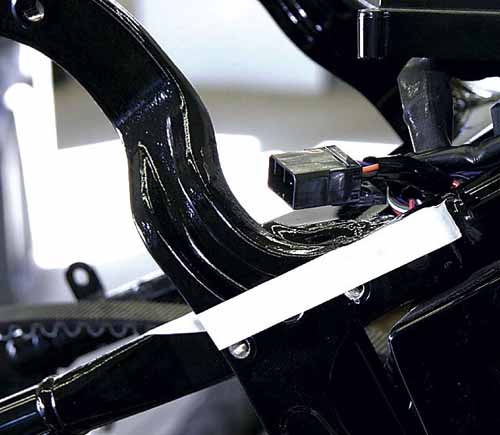
Cut, Cut, Cut
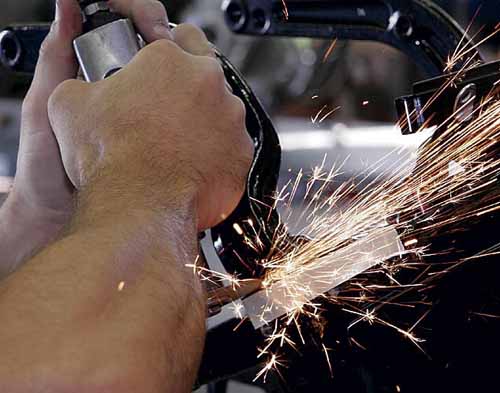
With the tank off the bike it was easy to envision the line we want the frame to have in the area of the struts. Doug marked this line with a piece of tape and went to town with a zinger. Unfortunately, the cross-bar located behind the struts is tipped up toward the back, which would foil our plan to have a straight line running from the neck all the way down the frame and onto the swingarm – like a true hardtail.
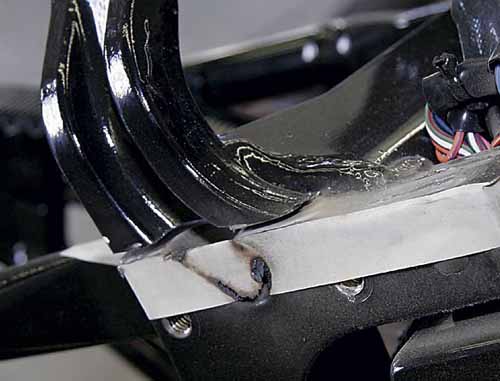
So after cutting nearly all the way through the strut, Doug cut the area inside where the strut meets the cross-bar with a plasma cutter. And after the struts were out of the way he cut this area back even further (this all makes more sense if you check out the photos).
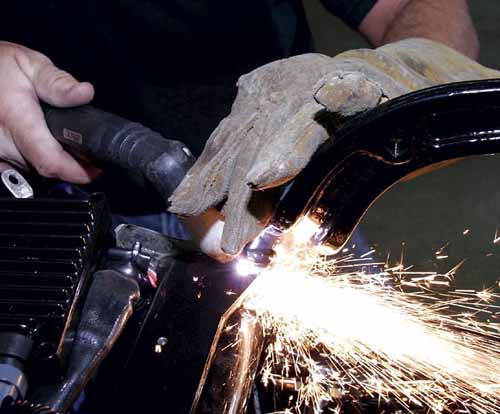
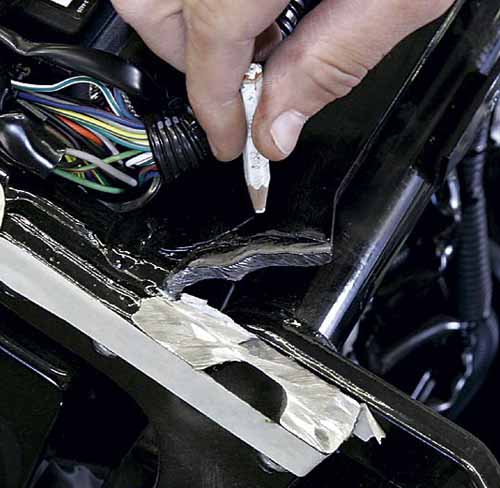
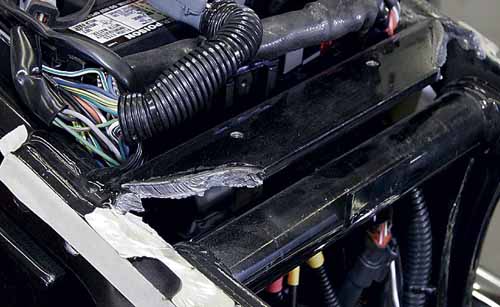
Now we did another mock-up session with the struts gone. The bike was finally starting to look like a proper Bobber. The goal here is to have a bike reminiscent of the late Bobber/early Choppers from the era before Choppers turned into long radical rides with super long forks and extreme rake angles.
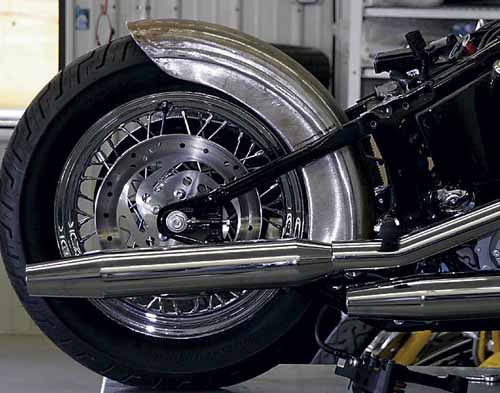
In keeping with that theme Doug fabricated simple mounting brackets for the fender, as a guy working in his own garage might have in the 1960s.
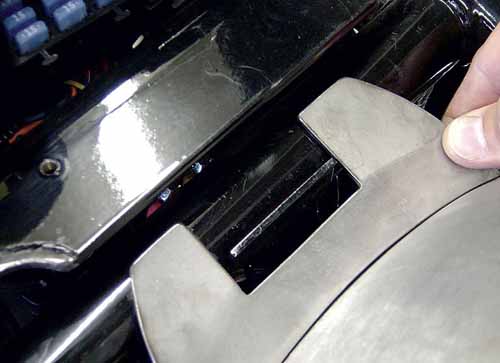
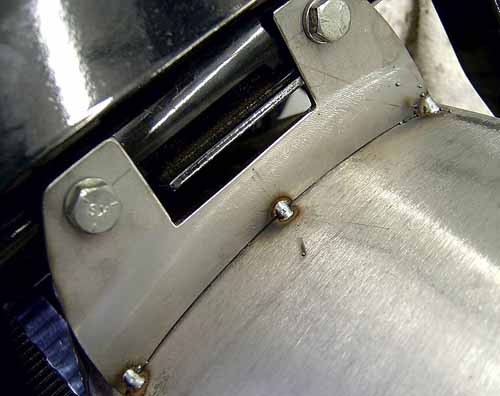
Once the fender sat correctly on the bike, held in place with two lower bolts and the rubber tubing taped up into the inside of the fender, Doug fabricated a simple bracket between the fender and the swingarm’s cross-bar. After tack welding the bracket to the fender, he drilled two holes in the bracket and then drilled and taps two matching holes in the cross-bar.
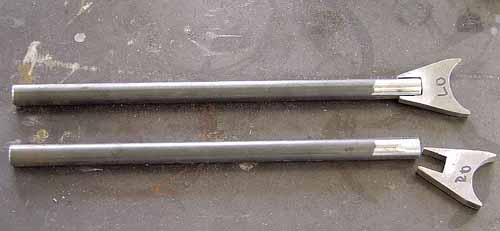
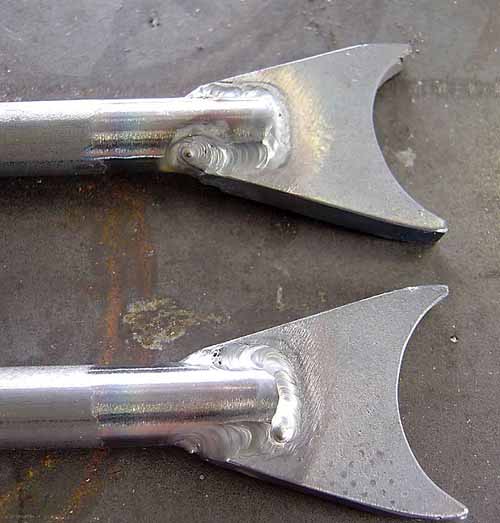
What was left were the rear support bars, made from round-stock bent just a bit and then welded to the big heavy washers on the outside of the swingarm, and two small fabricated tabs on the upper end. At the same time Doug forms a simple little concave piece of sheet metal to fit the spot where we cut the fender to clear the belt.
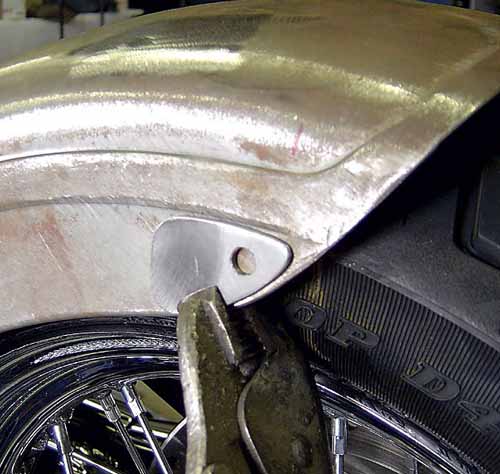
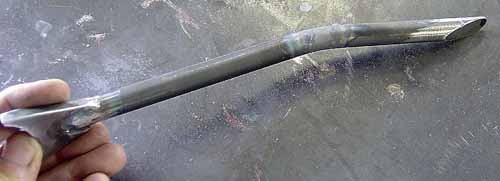
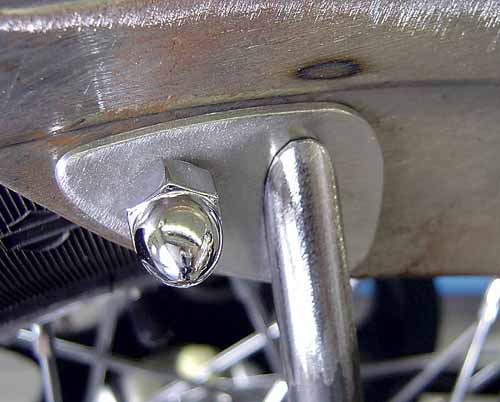
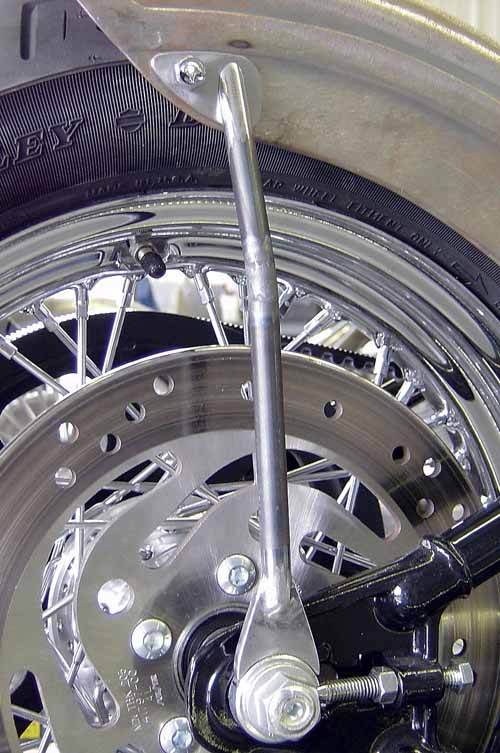
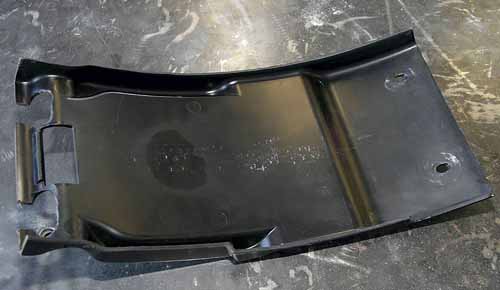
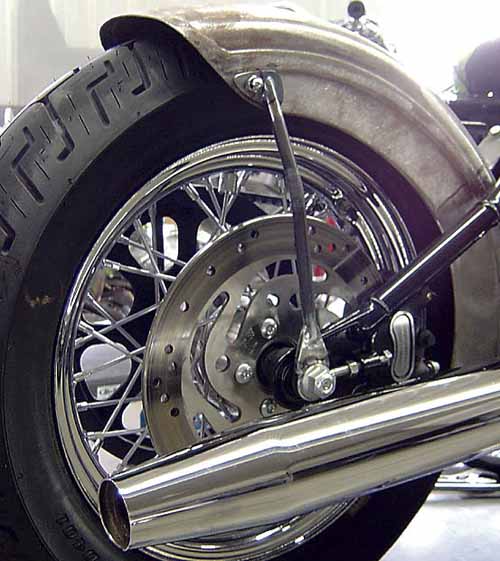
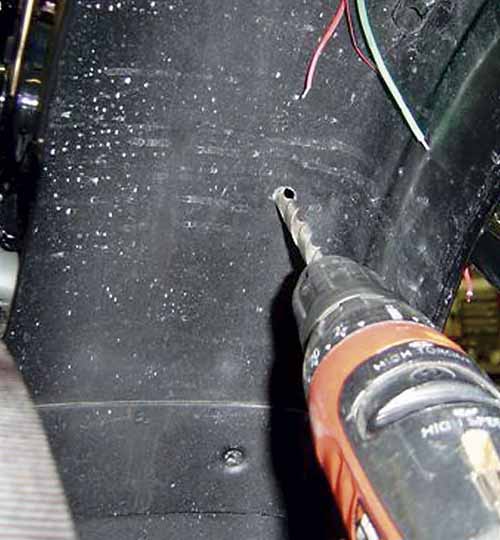

Prep and Paint
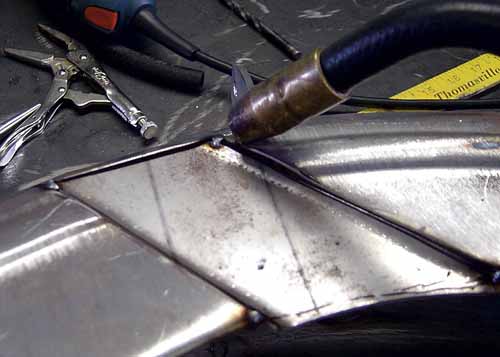
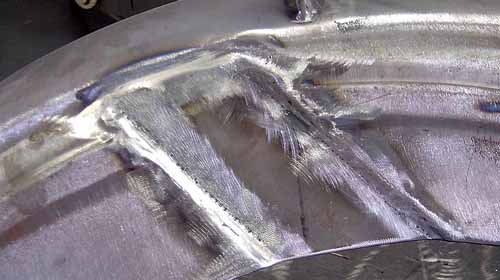
With the welder still idling in the corner, Doug filled the small holes in the fender and fills in the small kink where we did the pie-cut earlier (and hidden by the upper part of the swingarm). Metal finishing was handled with a small grinder. Next, Doug used a little filler on the roughest areas, followed by more sanding (much of it by hand) and then multiple coats of fast-build primer. The last coat of “primer” was a guide coat, a coat of paint lighter than the rest of the primer. This way when the fender was block-sanded any remaining light paint will indicate low spots.
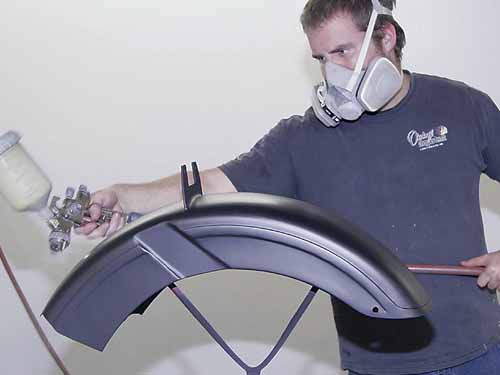
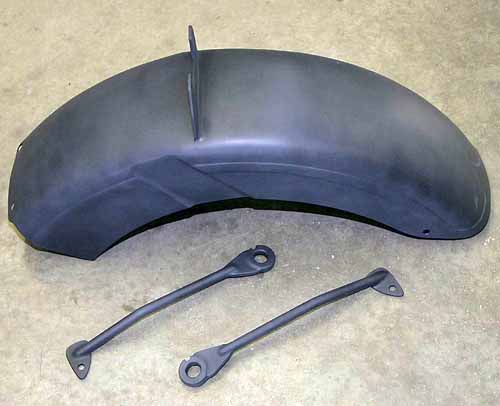
The tank was scuffed at the same time, as we simply can’t live with the very modern Harley-Davidson logo on our old Bobber. Some late-model logos are actually decals that were buried under clear-coats. In that case it was necessary to grind off the decal, seal the raw metal, prime and paint. In our case, the logos are painted on at the factory, so Doug and Brandon simply scuff, seal and paint the tank. The black used on both the fender and tank is black basecoat, BC 25, from House of Kolor.
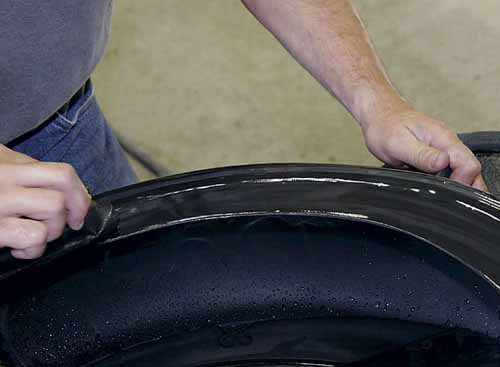
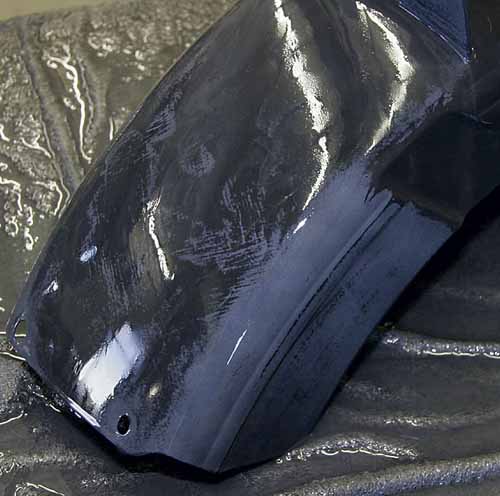
We planned at one time to hand letter the words Harley-Davidson, as that was often done, “back in the day.” In the end we used original logos, as shown. These go on in a two-step process, and require no drilling so they can be put on after the tank is painted.
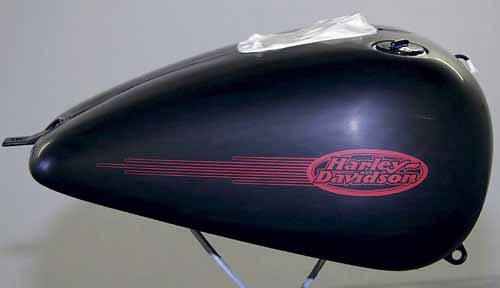
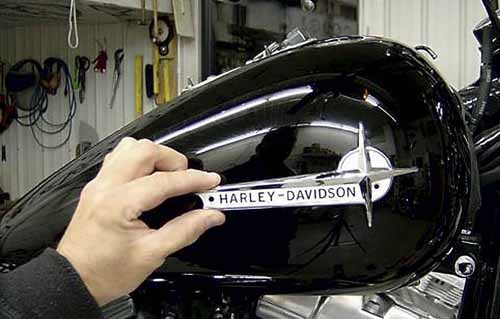
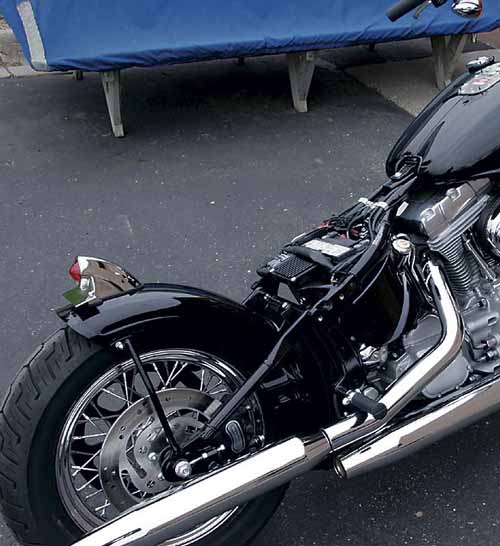
Once these logos were glued and screwed to the tank and the ignition switch is relocated with a Klock Werks bracket, the bike made another journey. Kevin Lehan is in charge at the Lemans upholstery shop where they make seats for Drag Specialties. Kevin agreed to knock out a solo seat in record time as a favor (they don’t do retail work at the shop).
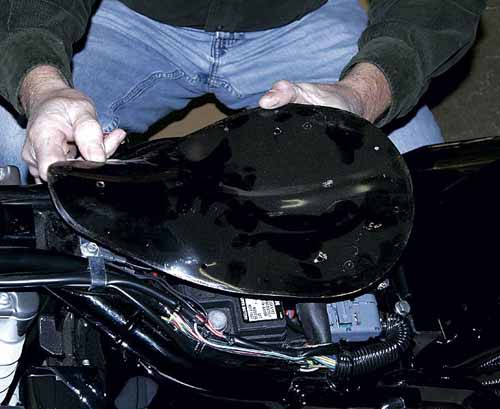
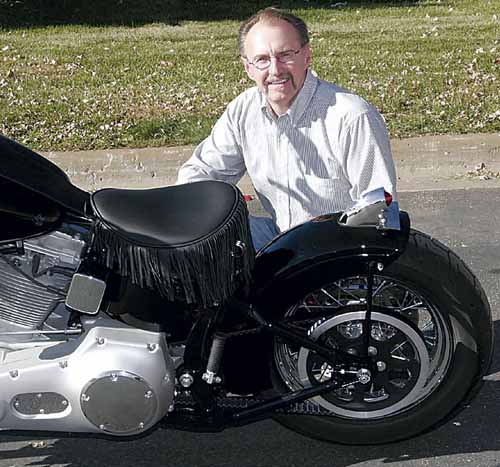
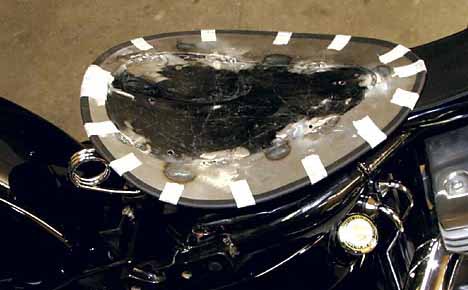
As the photos show, we started with a very small solo seat stamped out of metal. Rather than make a larger base from vacuum-formed plastic,(which might not be strong enough). Kevin and crew flattened the solo base and added metal to the edge. Kevin designed the seat with both skirting and fringe to hide the electronics hiding under the seat.
Because of the module under the seat there wasn’t room for coil springs, and we used hairpin style springs instead. All that was left was one more trip to American Thunder.
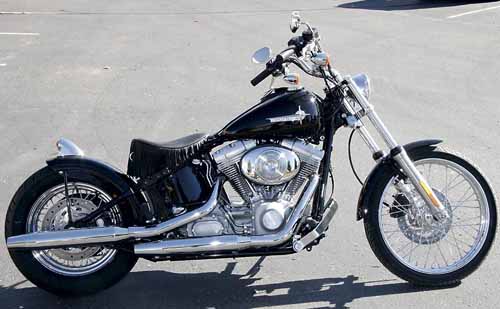
