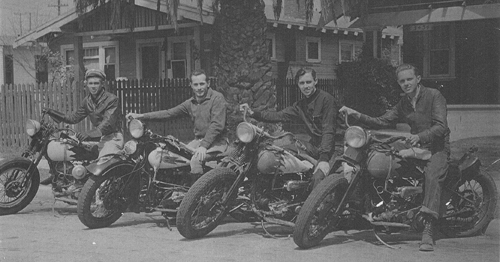
Scott Long and Darin Morris, Central Coast Cycles, Inc. of Santa Cruz, CA shared their gas tank building experience with Jeff Najar of Horsepower Marketing.
Many motorcycle builders regard the gas tank as the center piece of a custom motorcycle. It’s crucial to the style of the motorcycle by its lines and shape.
Scott Long and Darin Morris at Central Coast Cycles, Inc. build plenty of classic, custom motorcycles and have gained a reputation for custom gas tanks. The following is their approach to building a custom gas tank.
Equipment
You will need to assemble the following equipment including poster board, English wheel, sandbag, mallets, electric sheer, body dolly, post dolly, shrinker, 18 gauge sheet metal, tig welder, a good eye and strong hands, knees and forearms.
Rule of thumb
When building a tank you need to take into consideration the style of the bike, along with the location of the seat pan, triple trees and front end to ensure that the handle bars do not crash into the tank. “We measure 2 or 3 inches from the neck where the neck joins the top tube,” Scott said, “and 2 or 3 inches from the seat pan to determine the location of the tank on the backbone.”
The frame that we are using for this build is a 2-inch stretched, arched backbone, single down tube with a 30 degrees of rake. Our customer is building a tight chopper and wants the tank bottom to be “Frisco Style” or a smooth bottom tank that runs parallel to the bottom of the backbone.
Let’s get started:
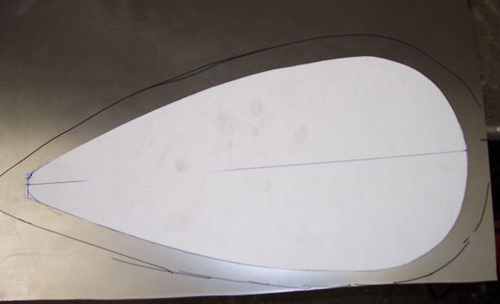
Create a design pattern and cut it out. “We’ll create a top, two sides and two bottoms,” Darin said. This is critical. The more accurate the pattern, the easier the project will be. Try to implement all your thinking, considerations, notions at this stage—they’ll save you a ton of work. Think about the bracket positions, petcock position, gas cap position. Consider the cap and the position of the tank for fuel capacity and fueling access.
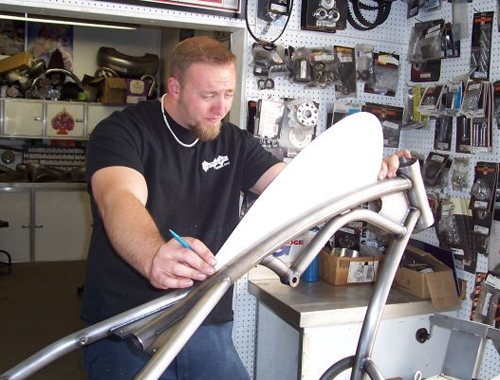
Check the pattern as to size and position on the frame. Use a sharpie to run a line on the pattern that is parallel to the bottom of the backbone.
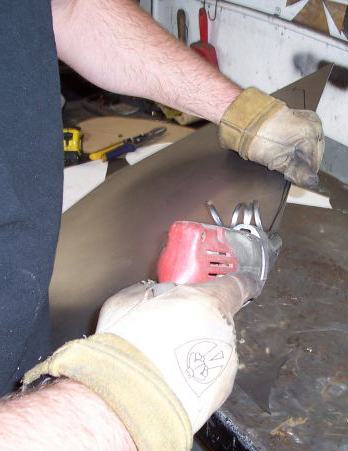
Cut the pattern out using an electric hand sheer. Create a centerline with your Sharpie on the top panel. As you shape the metal you will refer back to the centerline to ensure your shaping is uniform on both sides of the tank. You will need to measure from the centerline on both sides. “Don’t eyeball it,” Scott said, “because compound shapes can play tricks with your eyes.”
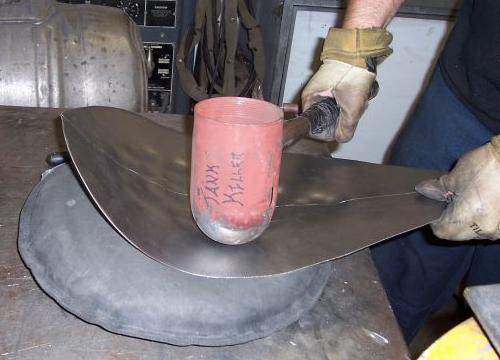
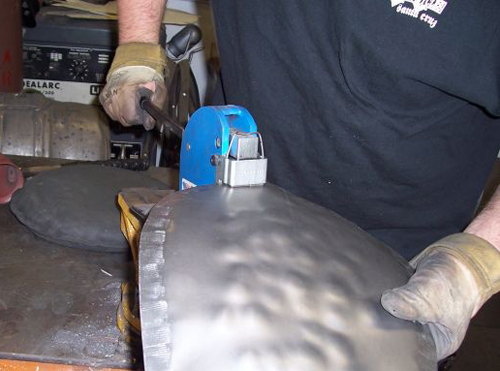
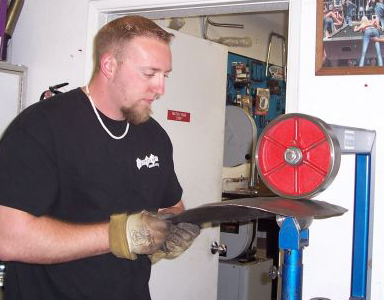
It was time to grab the sheet metal and start forming it. Lay the metal on the sandbag and use a mallet to pound it into compound shapes. Using the mallet will lengthen the metal and expedite the process. After you get your shape use the English wheel to smooth it.
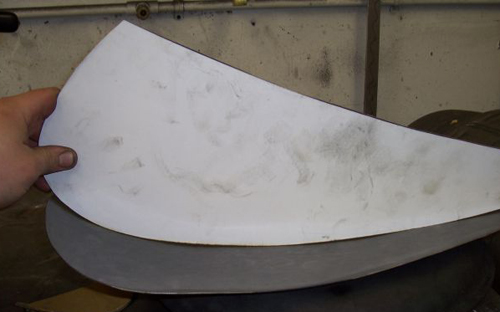
Check the shape against the pattern and make sure that the shapes are symmetrical.
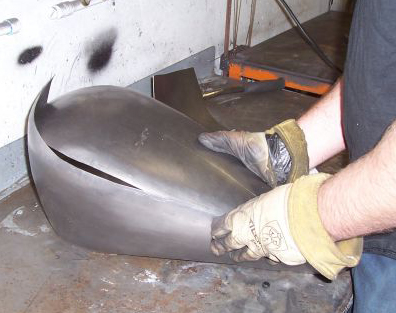
Fit together that’s one side and the top. Darin used the shrinker to remove waves and shrink it. Use your knee for precision help—I hope.
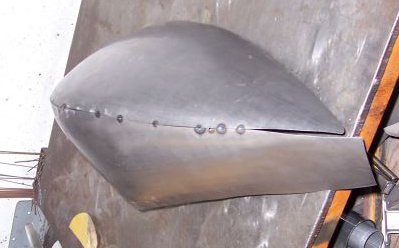
After you fit both sides together, then tack weld them into place. Make sure that you do not apply too much heat, as it will shrink and warp the metal.
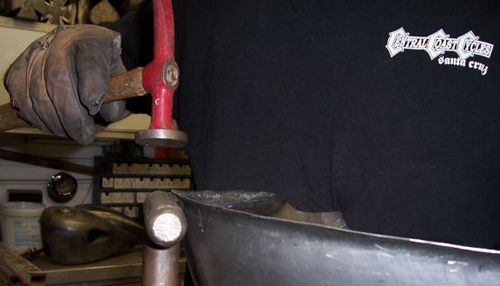
After they reached this state, they cut the tank in half and created a ridge down the center for that super-cool look. “We did it by using a hand dolly and a mallet,” Darin said. “We then tack welded it back into place and fit it on the frame to check it against the pattern. Another signature of our tanks is a concave cutout at the lower 1/3 of the tank sides, for that swept look. It accentuates the design and emphasizes the custom nature of the tank. We then welded the tank together permanently.
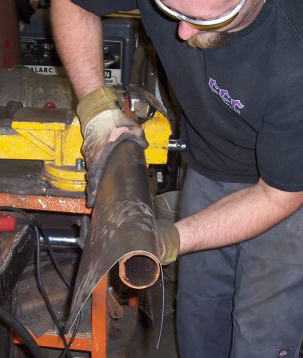
They created the tank tunnel by bending it around a pipe the same diameter tubing as the backbone. “We then cut it and used the shrinker to precisely form it,” Scott said, “then welded it back together as one piece.
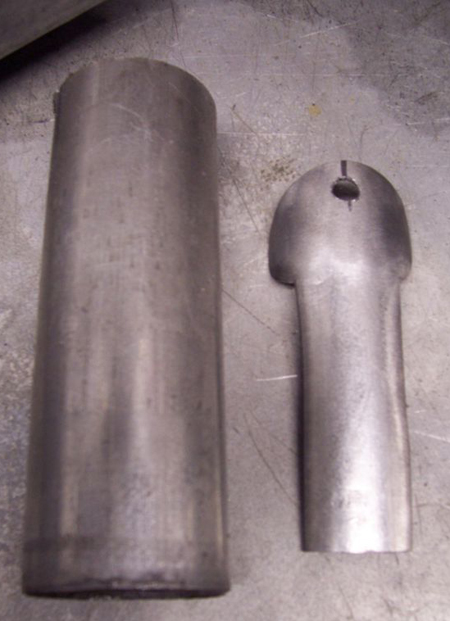
Mounting hardware was created to attach the tank to the frame. The hardware was then welded to the tank after it was tested on the frame to insure that the front end or the bars wouldn’t smack it.
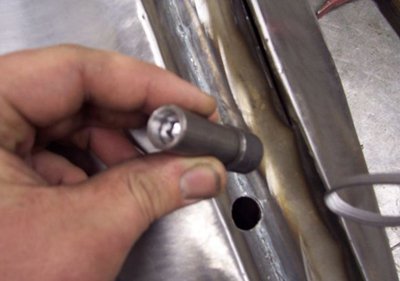
A bung was welded through the frame to insure the integrity of the frame. Then they ran a bolt through the frame and attached the tank.
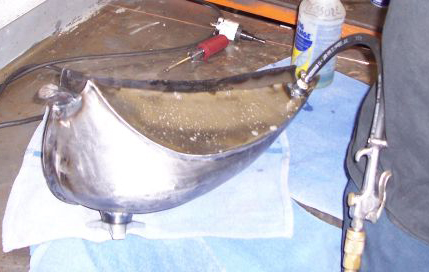
A pressure test was conducted to ensure that the tank has integrity, like man, it better not leak or break.
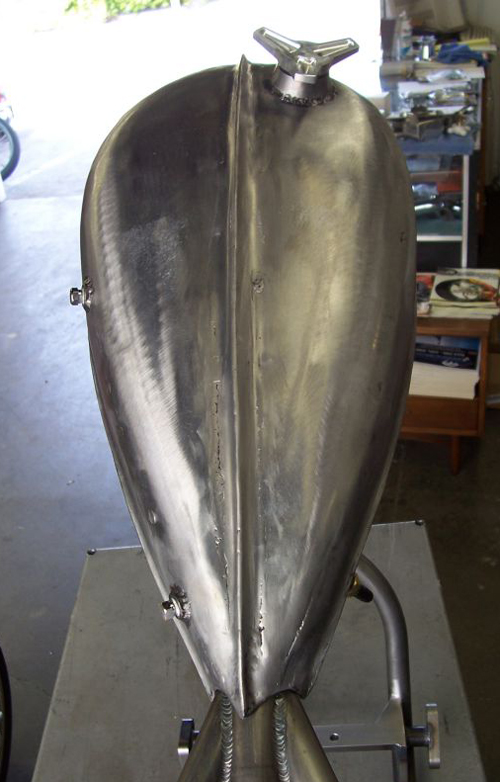
After the pressure test was completed to the builders’ satisfaction, they welded in the filler bung and petcock bung and mounted the tank on the frame. Bitchin!