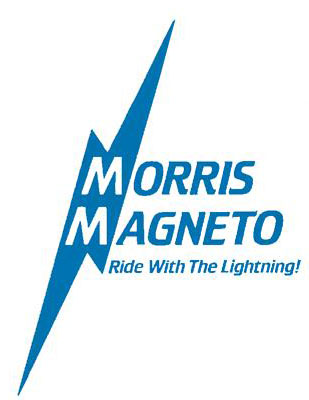
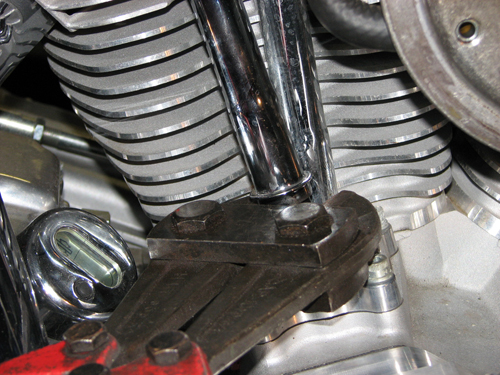
I don't know why I think this is wild, but I do. There's something so damn old school about this. In essence this allows any builder to take all the electronic bullshit off his Twin Cam, including the battery and make it a kick-start-only magneto driven motorcycle. This Morris Magneto returns the latest powerhouse to a one-wire off the alternator to the lights and your done, chopper. I think that's bitchin and I'm dying to know if Paul Yaffe has built one. He was the first Twin Cam Chopper builder.
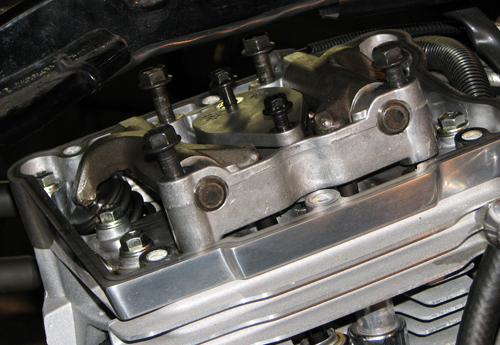
Okay, here's the installation instructions from Dave Shaw, the master of Morris Magnetos. We don't have all the photos we need, but there's more help in the S&S Gear Set Installation here on Bikernet, if you need additional info. This install also uses S&S gear drives and cams when making this modification. Click here for S&S Gear Drive Install Tech Let's get started:
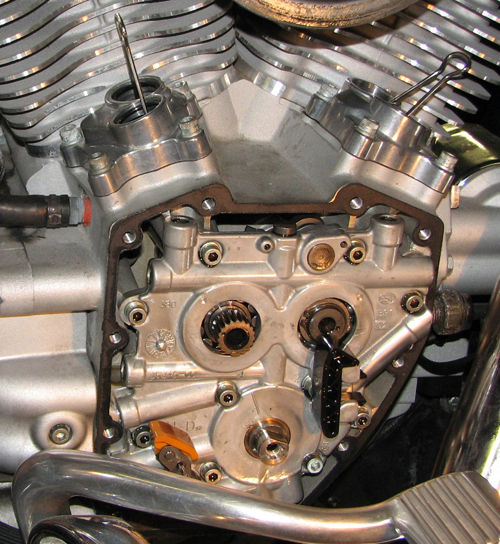
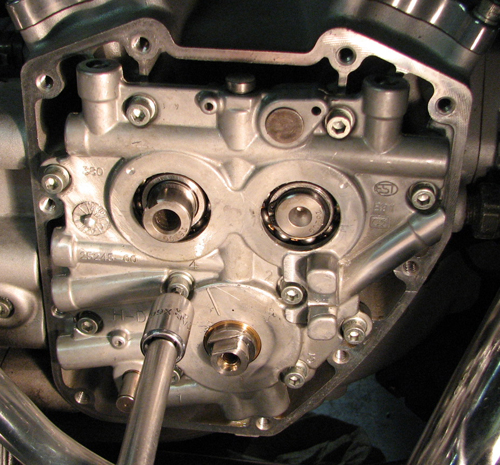
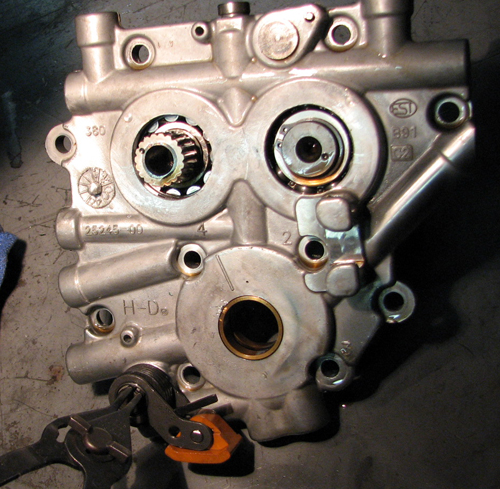
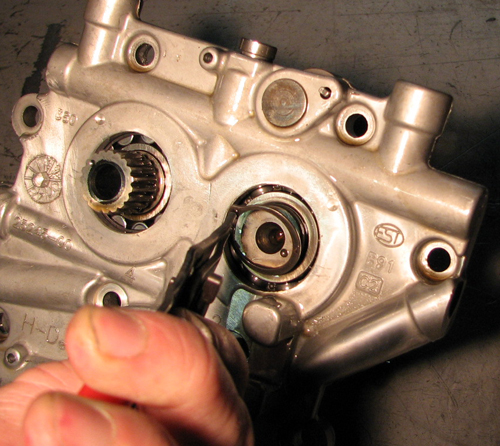
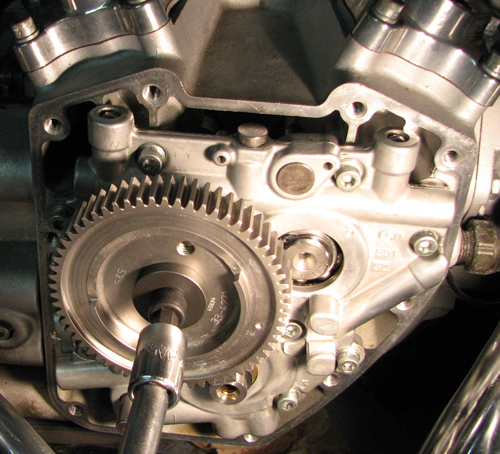
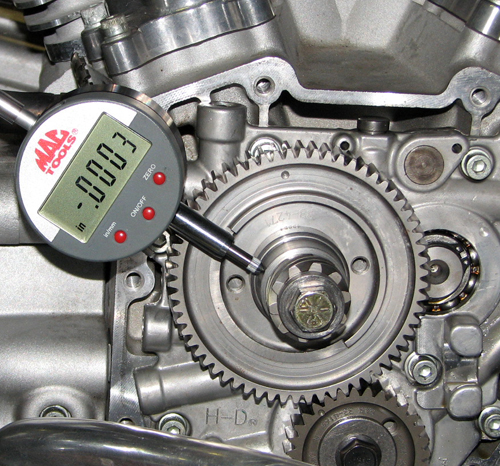
Install Twin Cam gear set per supplier’s instructions, substituting the cam gear bolt with parts supplied: magneto drive gear, spacer, and bolt. Gear should run concentric within .001” t.i.r. upon final tightening, so it will be necessary to mount a dial indicator; apply a small amount of red Loctite to the gear mating surface and bolt threads.
A light film of oil between gear and washer may help to align and seat bolt properly. Finally tighten to 45 ft/lbs.Using a 12-point 1½” socket, remove drive shaft assembly from cam cover, being careful to not loose any shim washer(s). Tighten bolt in steps, tapping on base of drive gear assembly to achieve concentricity while turning cam.
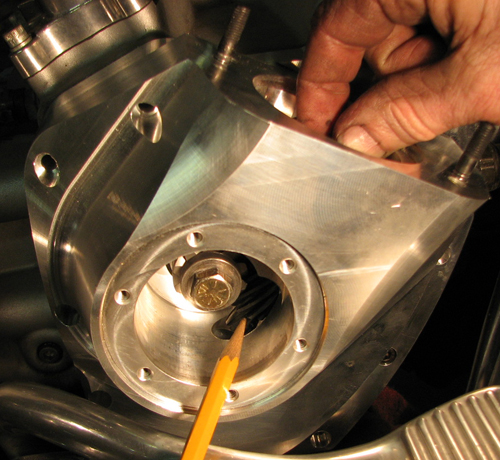

NOTE: Be sure to keep socket straight to prevent damaging drive top.
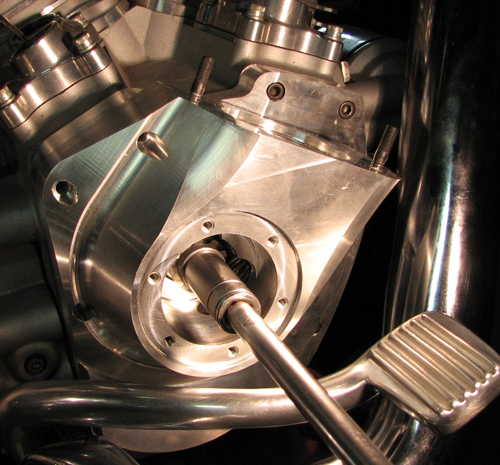
Place cover on engine, and shift cover around while looking in bolt-holes to insure that there is enough clearance between cover and cam plate. Mount cover with gasket, and hand tighten bolts provided. Now thread the drive shaft assembly back into cover, from the top (should thread in freely by hand, do not cross-thread) to about 40 ft/lbs. Gear lash must be set by shifting cover; location is proper when gears are free, and any lash is barely noticeable. Rotate cam gear to check lash in different positions. Lock down cover mounting screws securely.
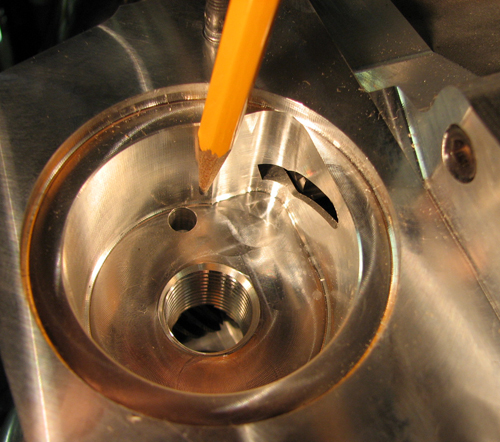
Remove drive shaft assembly.Set your engine on the correct stroke & position for installation, as follows:
a) Remove your rear spark plug only; you will be using rear cylinder for piston position only.
b) Rotate engine until you feel front cylinder compression; rear piston will be on the way up.
c) Continue turning the motor until the rear piston gets to the top. This is 45° before front cylinder TDC, a good starting point from which to set timing. We have achieved best results with a timing of 35 to 37 degrees BTC, so you will need to rotate engine about 10 degrees further; this can be done by using a degree wheel, checking piston position, or accessing the flywheel notches thru the stock pickup port (11.25 degrees per ‘tooth’).
Note: Due to whatever combination of components and modifications have been performed, you may need to change your timing spec.
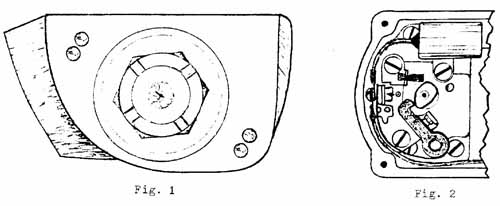
Remove magneto cap. Set magneto rotor so narrow cam lobe is located counter-clockwise from cam follower as in Picture 2, and breaker points are just opening. This is your correct front cylinder advanced timing position. On the bottom of the magneto, note position of drive lugs in relation to mounting flange.
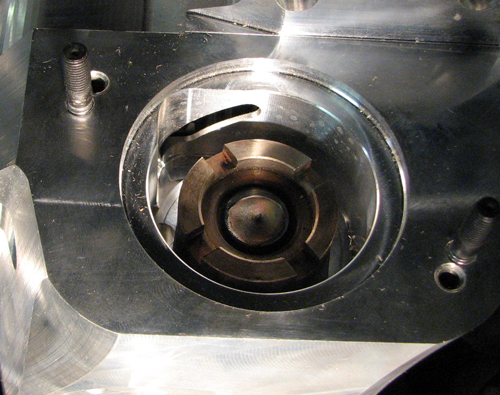
Install the drive shaft assembly so that either pair of slots on drive is in a similar position in relation to hold-down stud holes; this way, slots will line up and engage lugs when installing mag head, with both the engine and mag head in firing position. Slot position can be changed in 18 degree increments.
Note that there are two sets of holes in which you can install the studs; choose whichever pair lines up best for mounting mag head in the position you want.
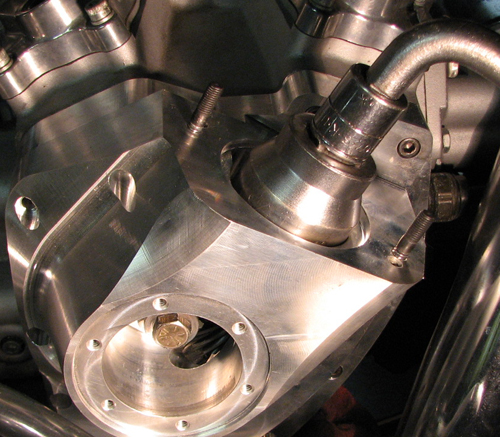
Using a drop of blue loctite, securely install studs by using two nuts jammed together. Tighten drive shaft assembly 80-100 ft/lbs with threads lightly oiled. Grease gears liberally, install side plate and gasket. Install the magneto and gasket, securing with the nuts and heavy washers provided. If you wish, you can check for 'points open' by using a good digital ohmmeter; reading will increase by about .3 ohms.
Re-install cap (make sure coil springs line up), and tighten so gasket does not compress more than 25%. Stud on side of magneto is used to “kill” magneto with a grounding toggle switch or lever (p/n KSL).
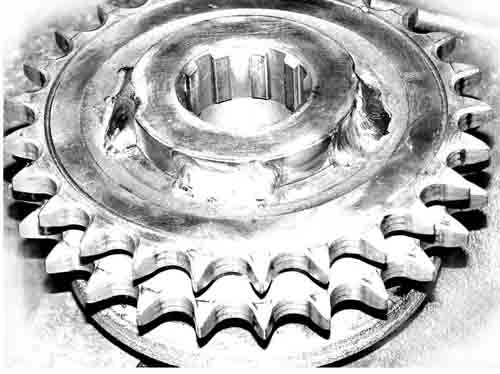
Stuff to know: This magneto was designed to start with a moderate kick. Hard kicks may actually hamper starting. Unit is also fully compatable with electric start, however, due to weak gears in the electric start system, it is recommended that you eliminate the compensating sprocket by replacing or welding.
The long-lasting OEM-type points in your magneto have been set at .015, and will require no attention for years. When replacement is necessary, use Morris p/n P5 and condensor p/n P6. Use only original type cap, gasket, points and condenser.

Initial spark plug gap .025. Due to the hot spark, plug gap may burn larger faster than before. Use of a single-fire module, Morris p/n MSF, may help prolong plug life. Use copper or stainless steel solid core (non-suppression) spark plug wires (Morris p/n MWS).
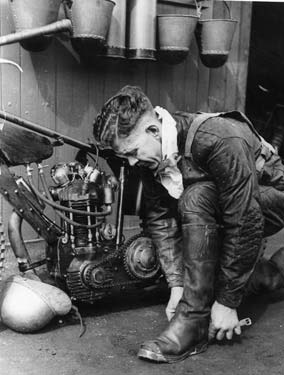
Morris Magnetos mf'd under US Patents 4191157, D375509, applicable pat's pend.
Email Info@morrismagneto.com
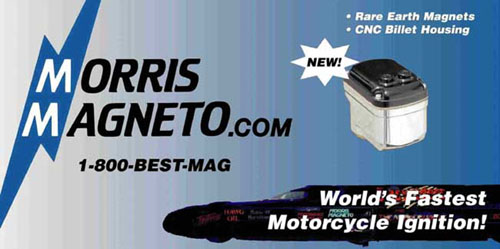