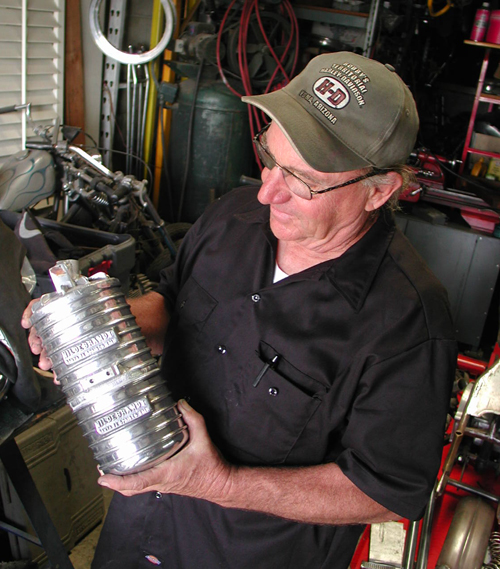
Bikernet is about to introduce you to the god of Triumph bobbers. Earl, 64, has been tinkering with bikes since he was eight, and got serious in 1966. He discovered a motorcycle niche home 30 years ago and is devoted to customizing rigid- framed Triumph twins. Once in a while, he stumbles off his yellow-brick road to work on a single, a BSA or a Sportster, but don't tell anyone.
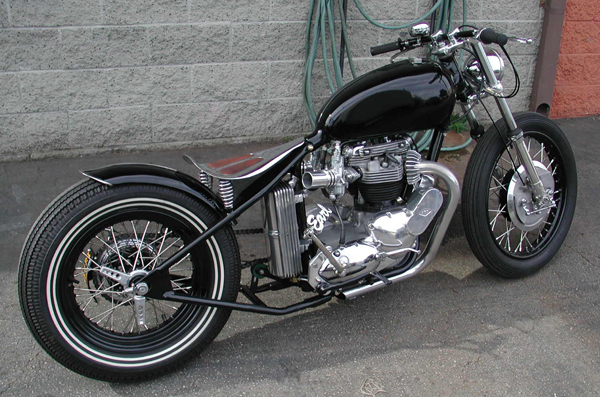
Here's an example of his devotion.
“If someone brings me stock Triumph parts or sheet metal, even the vintage stuff,” Earl said, “I trade it for stuff to build custom Triumphs with.”
He's never restored anything, but he'll weld a rigid tail on any Triumph frame and build you a one-off, hand-fabricated, rideable chunk of rebel lore. Today, Bikernet is investigating the product side of Earl's existence in the motorcycle industry. We've watched the aerospace machinists dive into the motorcycle industry with computer- driven CNC capabilities. We witnessed Jay Leno point out the scanning capabilities his crew uses to remanufacture components for his rare car and bike collection. Earl, however, resides on the dinged and dented side of the antique coin. He has a torch, a welder, a chop saw, and a drawer full of files. He likes to cut, weld, and hand- form several of his products, and so if the price hits the high-water mark, Earl earned it with his bare hands.
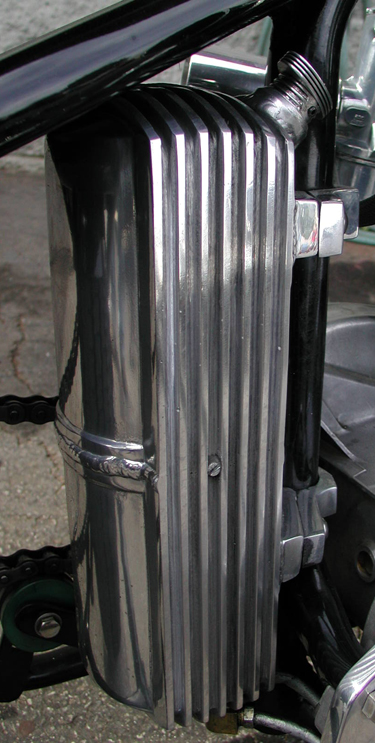
Let's get started with some of his classic products. If you have an alternate notion in mind for one of Earl's components, don't hesitate to ask for a change. He's going to make it by hand anyway. For instance, his finned Hildebrand oil tanks involve 20 hard hours of welding and hand-forming. He will install the oil outlets, cap, or drain plug wherever you want it.
“I'll plumb it to fit anything,” Earl said.
He will also make and weld in place any mounting bracket system you need. Even the oil capacity of these constantly cooling tanks (terrific heat dispersion) is flexible. They can be fabricated to carry from 2 to 3.5 quarts. Plus he can build a tank to mount vertically or horizontally.
His seats are not stamped out of cheap mild steel in India and shipped by slow steamship to the Los Angeles Harbor in bulk. He hand-forms each seat out of stainless steel, builds the leather inserts out of cowhide and hand-makes a stainless liner on the bottom. That's not all. He hand polishes each seat to a glistening finish. He runs through almost 40 hours on one seat.
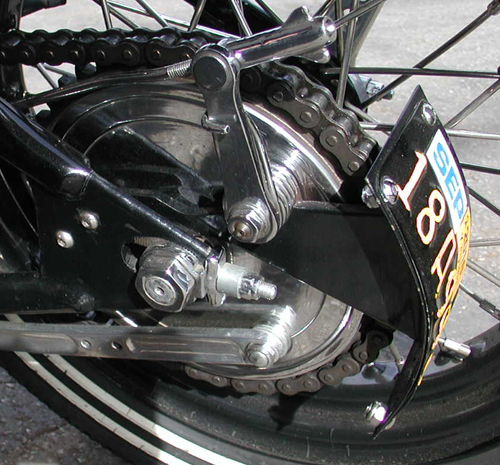
His popular license plate mounting bracket doubles as a chain guard. They are one-off, made out of stainless, to avoid plating. As the rear chain is adjusted, so does the bracket to maintain the exact position.
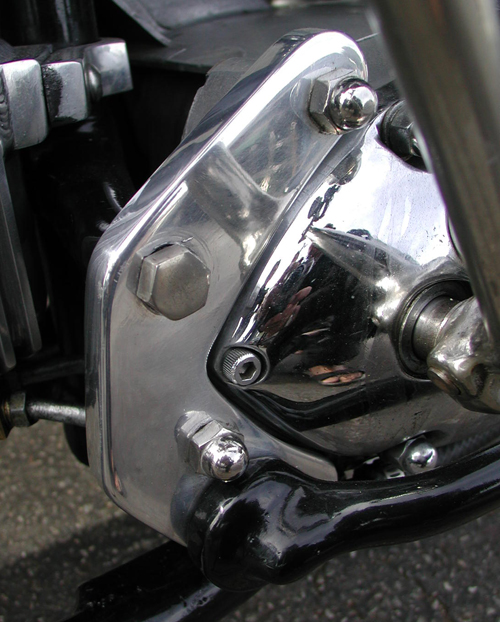
Earl is also building 5/8-inch thick polished aluminum rear motormounts for Triumphs. They are a direct replacement for damaged or worn stock units and contain the bungs for shifting or brake levers.
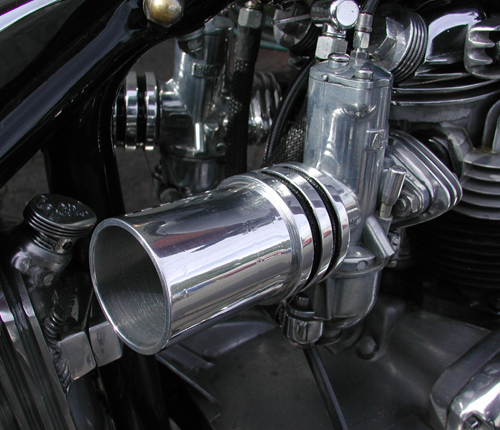
He admits that his velocity stacks are not performance tested, but a custom look for a standard Amal carb. “They're straight through and threaded for Amals,” Earl said. But he also added setscrews to prevent vibrating off. They are '50s style, and polished, thick wall 6061 tubing for a non-porous surface.
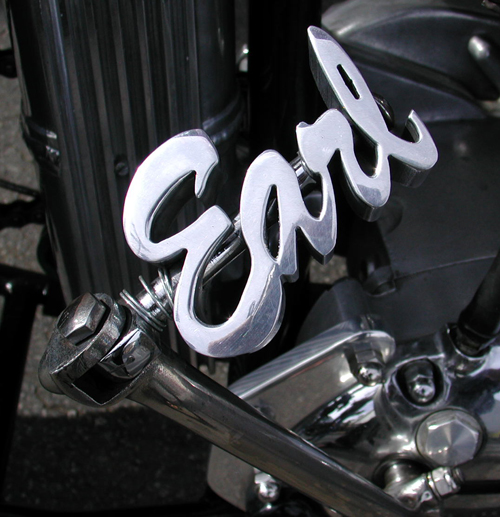
His oil tank caps, gas tank caps, and aluminum kickers are water jet cut and polished, so he's not completely against modern technology. His Earl kicker was originally made by hand, but now it's 1-inch thick aluminum and comes with a new spindle.
“You just pull the bolt, replace the kicker,” Earl said, “and you're good to go.”
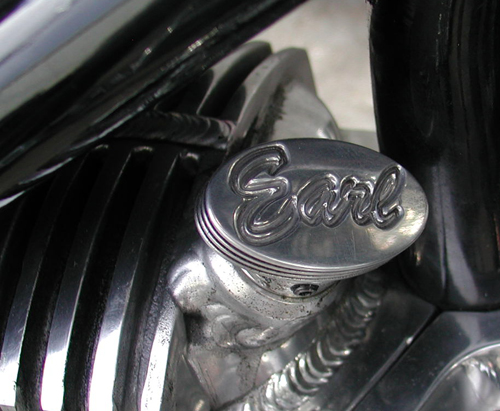
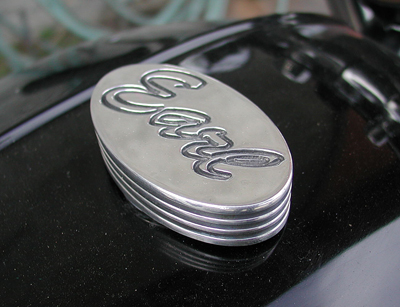
Earl also makes two exhaust systems for early Twin Triumphs. The custom TT system is made exclusively out of stainless tubing and polished.
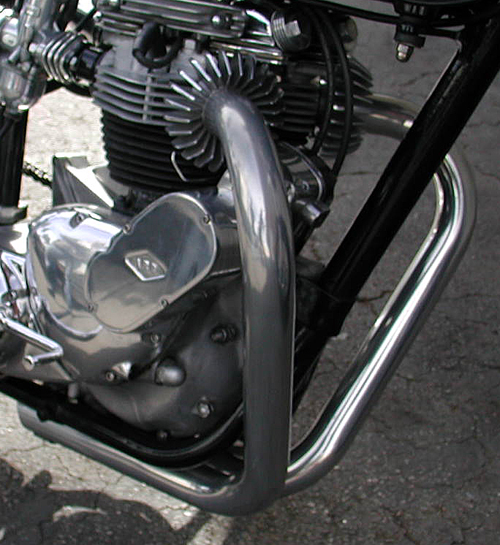
“If you drop your bike, you can repair these and re-polish,” Earl said. “They'll be just like new.”
He also makes the stock two-into-one configuration. It's the type that runs along the bottom of the frame to a single muffler. All his pipes are made from 1 ¾-inch tubing and flat cut for the classic Triumph sound.
“If you slash cut them, they don't sound right,” Earl added.
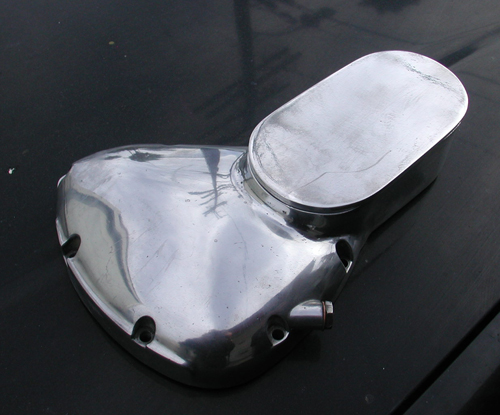
Back to strictly handmade items. Earl makes a replacement system for the classic ART mag timing cover plate. He couldn't buy one, so he made one, then another and another. He's crafted them for 650 Triumphs, 500cc models, and 650 BSAs. He uses a stock cover and installs and welds in his aluminum extension to mount a Joe Hunt or Morris Mag. The cover comes with two pulleys and a belt, but no mag. While having a Veterans' Day lunch with Earl at King's Fish in Long Beach, he told me a magneto tip, as we discussed and swapped old magneto stories. “Most mag problems are the condensers,” Earl said. “A condenser can last 15 minutes or 15 years.”
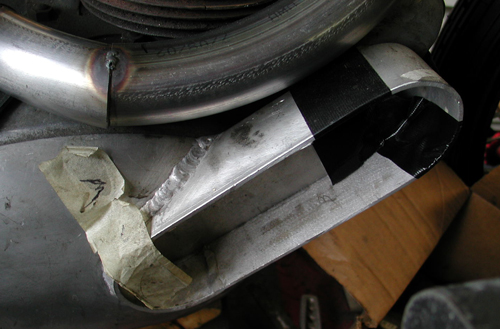
He also told me how to check mag magnets.
“If you take a knife and lay it across the magnet, it should stick,” Earl added. “If it sticks at all the magnet charge is good. If it doesn't the mag is toast.”
Earl also pointed out that Triumph points run the opposite direction of BSA units. “You need to flip the points plate in the mag,” he pointed out.

There you have it. Oh shit, I missed one. Earl also makes chain tensioners for weld-on Triumph hardtail frames. He won't hesitate to modify anything for any Triumph, including brake backing plates for cool running or manufacturing BSA intake runners to allow the carbs to run closer inboard to one another for a sleek look.
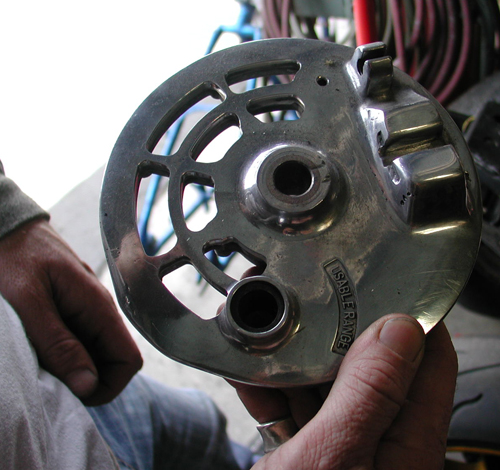
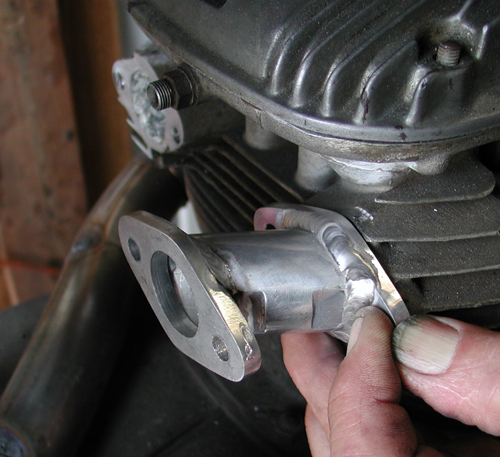
Earl's one of the cool cats in the motorcycle world, and if you fuck with him, the entire bobber nation will kick your ass. He's a neat guy and deserves a great deal of respect for his long and hand-ground career as the master manufacturer of one classic line of parts for one vintage motorcycle.

If you decide to buy one of his parts, or have your bike bobified by Earl, you'll enjoy the process, but be patient. He's a one-man band.
–Wrench
Check Earl's Web Site
Earl's Shop: (310)218-2979
See the HarborTown Bobber DVD trailer
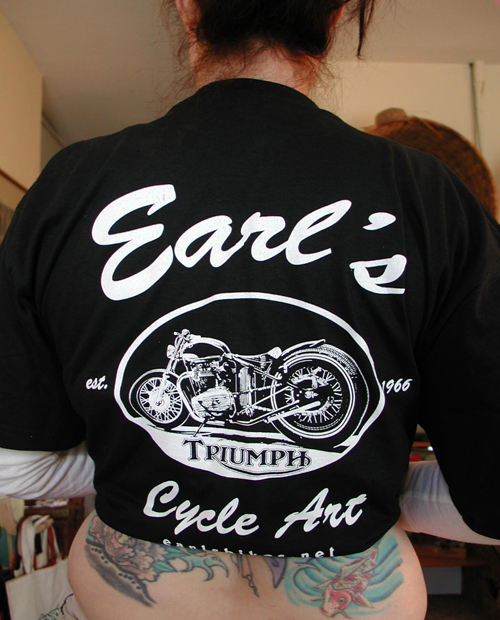
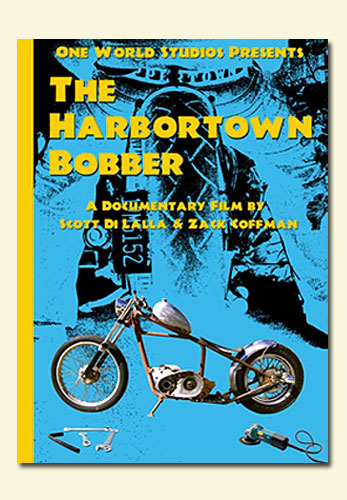